- お役立ち記事
- Managing Manufacturing Costs Thoroughly with the Total Cost Model
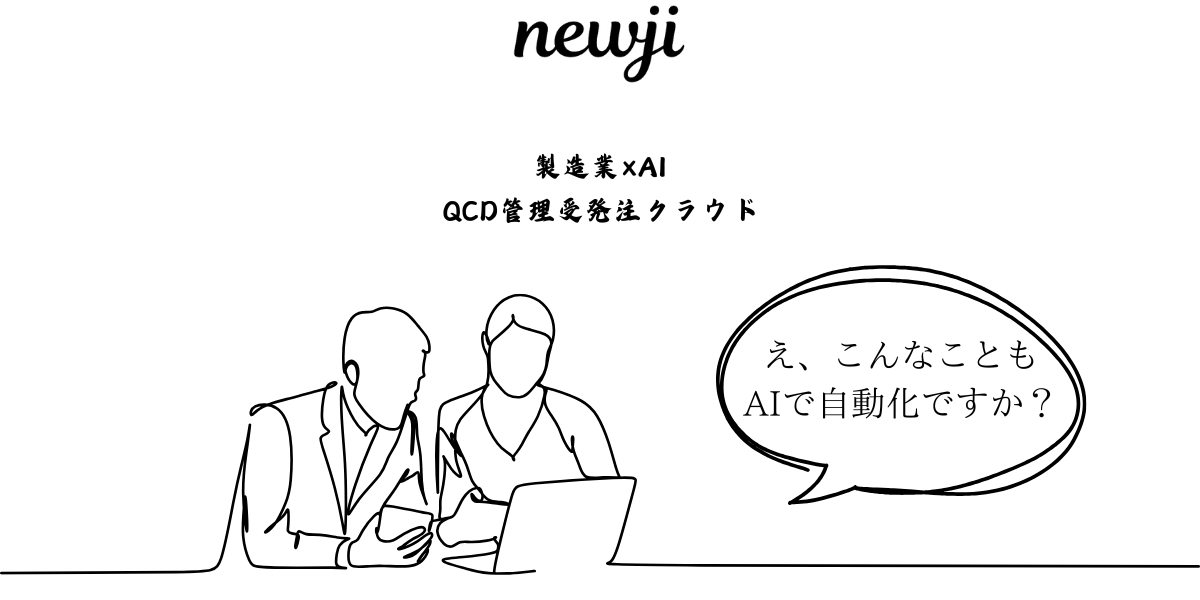
Managing Manufacturing Costs Thoroughly with the Total Cost Model
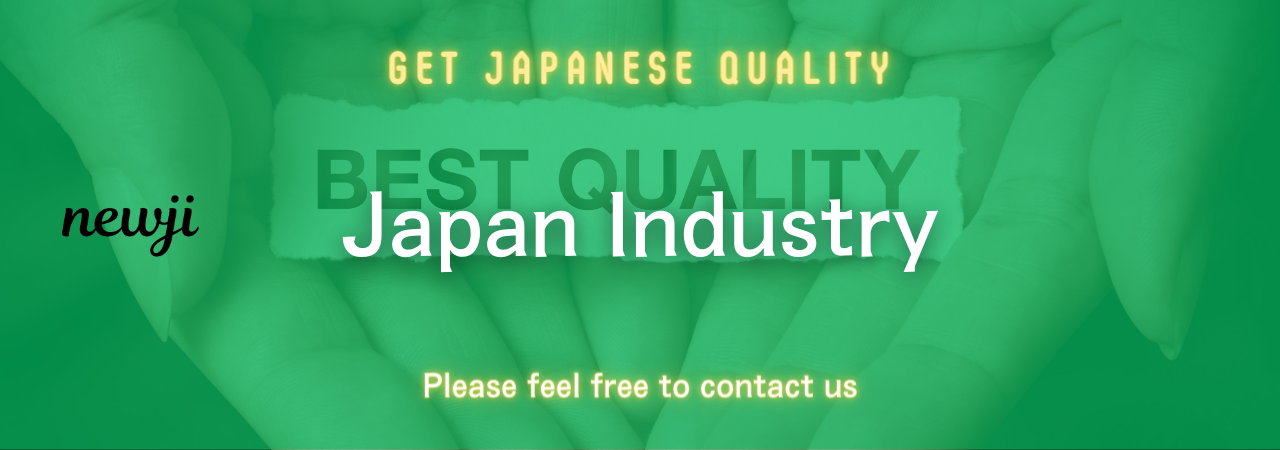
Managing manufacturing costs is a cornerstone of any successful business strategy, particularly for manufacturing companies. The total cost model is a comprehensive approach that can effectively help businesses control and reduce their manufacturing expenses. In this article, we will explore what the total cost model is and how to use it to manage manufacturing costs.
目次
Understanding the Total Cost Model
What is the Total Cost Model?
The total cost model is a method that businesses use to calculate all expenses involved in the manufacturing process. This model takes into account direct costs, like raw materials and labor, as well as indirect costs, such as overhead, utilities, and maintenance. By identifying and analyzing all these expenses, companies can gain a more accurate picture of their total production costs.
Why is the Total Cost Model Important?
Understanding the total cost is crucial for various reasons. First, it helps in setting the right price for products. If a company underestimates its total costs, it may end up pricing its products too low, resulting in losses.
Conversely, overestimating costs can make products too expensive, reducing competitiveness.
Second, the total cost model aids in budget planning and cost control. It allows businesses to identify areas where they can cut costs or improve efficiency.
Finally, it helps in decision-making processes, such as whether to make or buy a component, invest in new machinery, or move production to a different location.
Key Elements of the Total Cost Model
Direct Costs
Direct costs are expenses that can be directly traced to the production of a specific product. The two primary direct costs are materials and labor.
Raw Materials: These are the essential components that go into creating a product. For example, steel for making cars, fabric for clothes, or grains for cereals.
Tracking the cost of raw materials is vital because fluctuations in material prices can significantly affect total manufacturing costs.
Direct Labor: This includes wages paid to workers who are directly involved in the production process. Efficient labor management and productivity improvements can considerably reduce direct labor costs.
Indirect Costs
Indirect costs, also known as overhead costs, are expenses that cannot be directly traced to a specific product but are necessary for the manufacturing process.
These costs include:
Utilities: Bills for electricity, water, and gas are part of manufacturing overhead. Reducing energy consumption can lead to significant cost savings.
Maintenance: Maintenance costs for machinery and equipment are another crucial element. Regular maintenance helps prevent unexpected breakdowns, which can be costly.
Depreciation: The decrease in value of manufacturing equipment over time also counts as an indirect cost. Proper accounting for depreciation helps in the accurate assessment of total costs.
How to Implement the Total Cost Model
Data Collection and Analysis
The first step in implementing the total cost model is to collect all relevant data. This includes records of raw material purchases, labor costs, utility bills, maintenance expenses, and depreciation schedules. Advanced software tools can aid in automating this data collection process.
Once the data is collected, it needs to be analyzed to identify trends and patterns. For example, you might find that certain materials are consistently more expensive or that utility costs spike during particular times of the year. Identifying these trends allows for more informed decision-making.
Cost Allocation
After gathering and analyzing data, the next step is to allocate costs appropriately. Direct costs are straightforward to allocate since they are easily traceable to specific products. For indirect costs, different allocation methods can be used, such as activity-based costing (ABC) or using allocation bases like machine hours or labor hours.
Activity-based costing (ABC) is particularly effective because it allocates overhead costs based on the actual activities that generate these costs. This method provides a more accurate representation of the true cost of manufacturing a product.
Regular Monitoring and Reporting
Implementing the total cost model is not a one-time activity. Regular monitoring and reporting are essential to ensure that the cost management strategies remain effective over time. Monthly or quarterly reports should be generated to track costs, identify variances from the budget, and make necessary adjustments.
Strategies to Reduce Manufacturing Costs
Improving Operational Efficiency
One of the most effective ways to reduce manufacturing costs is by improving operational efficiency. This can be achieved through various means, such as lean manufacturing techniques that focus on eliminating waste and optimizing processes. Automation of repetitive tasks can also contribute to increased efficiency and reduced labor costs.
Negotiating with Suppliers
Raw material costs can be a significant portion of total manufacturing expenses. Negotiating better terms with suppliers, bulk purchasing, or establishing long-term contracts can help in securing lower prices for raw materials. Building strong relationships with suppliers can also lead to more favorable payment terms and conditions.
Energy Management
Energy consumption is a considerable cost for manufacturing companies. Implementing energy-efficient practices and technologies can lead to substantial savings. Conducting energy audits to identify areas where consumption can be reduced, using energy-efficient machinery, and harnessing renewable energy sources are all viable strategies.
Regular Maintenance
Ensuring that machinery and equipment are well-maintained helps in reducing unexpected breakdowns and costly repairs. Additionally, regular maintenance can extend the life of equipment, reducing the need for frequent replacements. Preventive maintenance schedules should be established and followed diligently.
The Benefits of Using the Total Cost Model
Enhanced Cost Visibility
The total cost model provides enhanced visibility into all the costs associated with manufacturing. This comprehensive understanding allows businesses to identify inefficiencies and areas where costs can be reduced. Better cost visibility also improves transparency, helping stakeholders make more informed decisions.
Improved Profit Margins
By managing and reducing costs effectively using the total cost model, businesses can improve their profit margins. Lower manufacturing costs mean that companies can either increase their profit margins or offer competitive pricing to attract more customers, thereby driving sales and revenue growth.
Informed Decision-Making
The detailed insights provided by the total cost model support more informed decision-making. Whether it’s deciding on pricing strategies, investing in new technology, or optimizing the supply chain, having a clear understanding of all manufacturing costs allows for better strategic planning and execution.
Competitive Advantage
Companies that effectively manage their manufacturing costs gain a competitive advantage in the market. They can offer products at more competitive prices, invest in quality improvements, and respond more flexibly to market changes. This competitive edge helps businesses sustain growth and profitability in the long run.
In conclusion, the total cost model is a powerful tool for managing manufacturing costs. By understanding and analyzing all the expenses associated with production, businesses can take proactive steps to reduce costs and improve efficiency. Implementing the total cost model requires careful data collection, analysis, cost allocation, and regular monitoring. However, the benefits it offers in terms of enhanced cost visibility, improved profit margins, informed decision-making, and competitive advantage make it well worth the effort.
資料ダウンロード
QCD調達購買管理クラウド「newji」は、調達購買部門で必要なQCD管理全てを備えた、現場特化型兼クラウド型の今世紀最高の購買管理システムとなります。
ユーザー登録
調達購買業務の効率化だけでなく、システムを導入することで、コスト削減や製品・資材のステータス可視化のほか、属人化していた購買情報の共有化による内部不正防止や統制にも役立ちます。
NEWJI DX
製造業に特化したデジタルトランスフォーメーション(DX)の実現を目指す請負開発型のコンサルティングサービスです。AI、iPaaS、および先端の技術を駆使して、製造プロセスの効率化、業務効率化、チームワーク強化、コスト削減、品質向上を実現します。このサービスは、製造業の課題を深く理解し、それに対する最適なデジタルソリューションを提供することで、企業が持続的な成長とイノベーションを達成できるようサポートします。
オンライン講座
製造業、主に購買・調達部門にお勤めの方々に向けた情報を配信しております。
新任の方やベテランの方、管理職を対象とした幅広いコンテンツをご用意しております。
お問い合わせ
コストダウンが利益に直結する術だと理解していても、なかなか前に進めることができない状況。そんな時は、newjiのコストダウン自動化機能で大きく利益貢献しよう!
(Β版非公開)