- お役立ち記事
- Manufacturing and Talent Development: The Ironman Dojo
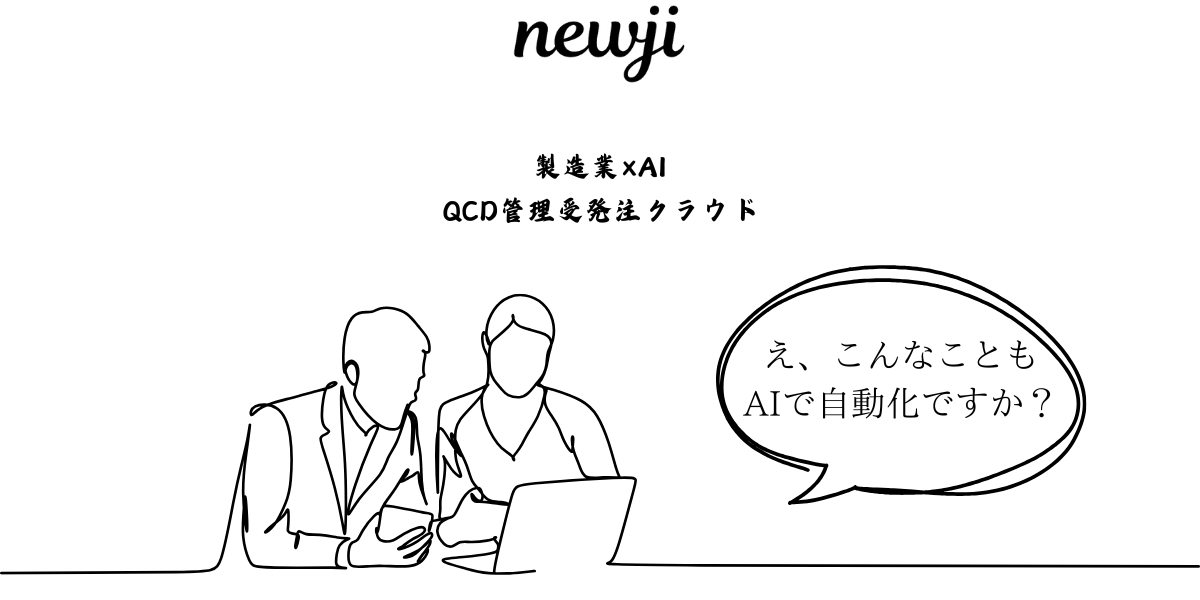
Manufacturing and Talent Development: The Ironman Dojo
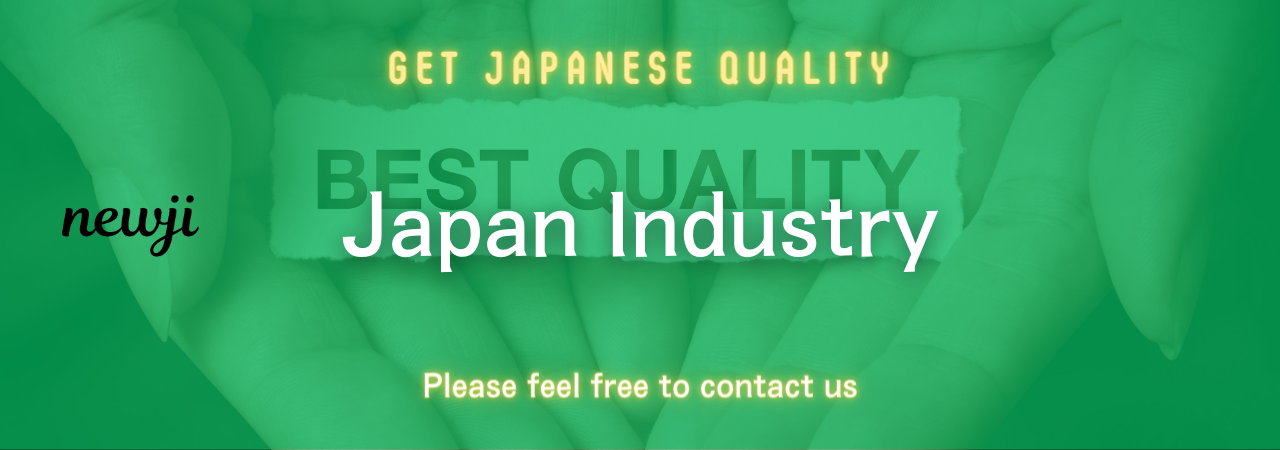
目次
Introduction to the Ironman Dojo
The world of manufacturing is constantly evolving and innovating.
For companies to stay competitive, there’s a growing need for talent development programs.
One such initiative is the Ironman Dojo.
But what is it, and how does it help in enhancing skills?
In this article, we’ll dive into the concept of the Ironman Dojo and its significance in the manufacturing sector.
What is the Ironman Dojo?
The Ironman Dojo is a specialized training program designed for individuals in the manufacturing industry.
It’s like a boot camp focused on developing specific skills required in this sector.
The term “dojo” comes from Japanese martial arts, meaning a place of learning or training.
In this context, it symbolizes an environment where manufacturers train to become experts in their field.
By participating in the Ironman Dojo, trainees undergo rigorous instruction and hands-on experience.
This ensures that they are well-prepared for real-world manufacturing challenges.
Why is Talent Development Important in Manufacturing?
The manufacturing industry is highly dynamic.
Technology is advancing at a rapid pace, and new methodologies are always emerging.
To keep up, businesses need a workforce that’s not only competent but also adaptable.
Talent development programs like the Ironman Dojo play a crucial role in this regard.
Here’s why talent development is essential:
1. Keeping up with Technological Advancements
The incorporation of high-tech machines and software in manufacturing has become common.
Workers need to understand how to operate these technologies efficiently.
Training programs ensure that employees are updated on the latest tech trends and how to use them effectively.
2. Enhancing Productivity
Skilled employees contribute significantly to the overall productivity of a company.
When workers are well-trained, they can produce higher quality work at faster rates.
This leads to increased output and better product quality, giving businesses a competitive edge.
3. Reducing Errors and Downtime
Errors in manufacturing can be costly.
They can lead to waste, defective products, and even safety hazards.
Through rigorous training, employees learn to minimize mistakes, which reduces downtime and improves overall efficiency.
The Structure of the Ironman Dojo
The Ironman Dojo is structured to provide comprehensive training in various aspects of manufacturing.
Here’s a breakdown of its key components:
1. Theoretical Learning
Participants start with classroom-style learning, where they gain a solid understanding of manufacturing principles.
This includes topics like lean manufacturing, Six Sigma, and foundational industry standards.
Theoretical learning ensures that trainees have the necessary background before they move on to practical applications.
2. Hands-On Training
One of the most important parts of the Ironman Dojo is hands-on training.
Participants work on actual machines and equipment used in manufacturing.
They learn to maintain, operate, and troubleshoot these machines under supervision.
This practical approach allows them to gain real-world experience and confidence in their abilities.
3. Problem-Solving Workshops
Problem-solving is a critical skill in manufacturing.
The Ironman Dojo includes workshops focused on tackling common manufacturing challenges.
During these sessions, participants work in teams to find solutions to hypothetical and real-world problems.
This collaborative environment enhances their critical thinking and teamwork skills.
4. Continuous Assessment
To ensure that trainees are progressing, the Ironman Dojo incorporates continuous assessment.
Participants are evaluated on their practical skills, theoretical knowledge, and problem-solving abilities.
This continuous feedback helps them identify areas of improvement and track their development over time.
5. Certification
Upon completion of the program, participants receive certification.
This certification serves as a testament to their skills and knowledge in the manufacturing field.
It can be a valuable addition to their professional portfolio and can enhance their career prospects.
The Benefits of the Ironman Dojo for Companies
Investing in the Ironman Dojo offers several benefits for companies in the manufacturing sector.
1. Improved Workforce Competency
With a well-trained workforce, companies can achieve higher levels of competency and efficiency.
Employees are better equipped to handle their tasks and contribute positively to the company’s goals.
2. Enhanced Innovation
Training programs encourage employees to think creatively and innovatively.
With new skills and knowledge, they can come up with fresh ideas that can drive the company forward.
3. Increased Employee Retention
When companies invest in their employees’ development, it fosters a sense of loyalty and commitment.
Employees are more likely to stay with a company that offers them growth opportunities and values their professional development.
4. Competitive Advantage
A skilled workforce gives companies a significant advantage over competitors.
They can produce high-quality products more efficiently, which can lead to better customer satisfaction and market positioning.
The Future of Talent Development in Manufacturing
As the manufacturing industry continues to advance, the need for specialized training programs like the Ironman Dojo will only grow.
Future talent development initiatives will likely incorporate more advanced technologies, such as virtual reality (VR) and augmented reality (AR), for training purposes.
These technologies can provide immersive learning experiences that further enhance skills and knowledge.
Moreover, the focus will also shift towards continuous learning and development.
As the industry evolves, so will the skills required, making lifelong learning an essential aspect of the manufacturing workforce.
Conclusion
The Ironman Dojo is a vital program in the realm of manufacturing talent development.
It equips individuals with the skills and knowledge needed to excel in a rapidly changing industry.
By investing in such training programs, companies can ensure they have a competent, innovative, and loyal workforce.
As we look to the future, the significance of continuous learning and development cannot be overstated.
Programs like the Ironman Dojo will play a central role in shaping the manufacturing workforce of tomorrow.
Whether you’re a business leader or a budding professional, understanding and participating in these programs can pave the way for sustained success in the manufacturing sector.
資料ダウンロード
QCD調達購買管理クラウド「newji」は、調達購買部門で必要なQCD管理全てを備えた、現場特化型兼クラウド型の今世紀最高の購買管理システムとなります。
ユーザー登録
調達購買業務の効率化だけでなく、システムを導入することで、コスト削減や製品・資材のステータス可視化のほか、属人化していた購買情報の共有化による内部不正防止や統制にも役立ちます。
NEWJI DX
製造業に特化したデジタルトランスフォーメーション(DX)の実現を目指す請負開発型のコンサルティングサービスです。AI、iPaaS、および先端の技術を駆使して、製造プロセスの効率化、業務効率化、チームワーク強化、コスト削減、品質向上を実現します。このサービスは、製造業の課題を深く理解し、それに対する最適なデジタルソリューションを提供することで、企業が持続的な成長とイノベーションを達成できるようサポートします。
オンライン講座
製造業、主に購買・調達部門にお勤めの方々に向けた情報を配信しております。
新任の方やベテランの方、管理職を対象とした幅広いコンテンツをご用意しております。
お問い合わせ
コストダウンが利益に直結する術だと理解していても、なかなか前に進めることができない状況。そんな時は、newjiのコストダウン自動化機能で大きく利益貢献しよう!
(Β版非公開)