- お役立ち記事
- Manufacturing method of high-precision zinc alloy and its use case in the precision equipment market
月間77,185名の
製造業ご担当者様が閲覧しています*
*2025年2月28日現在のGoogle Analyticsのデータより
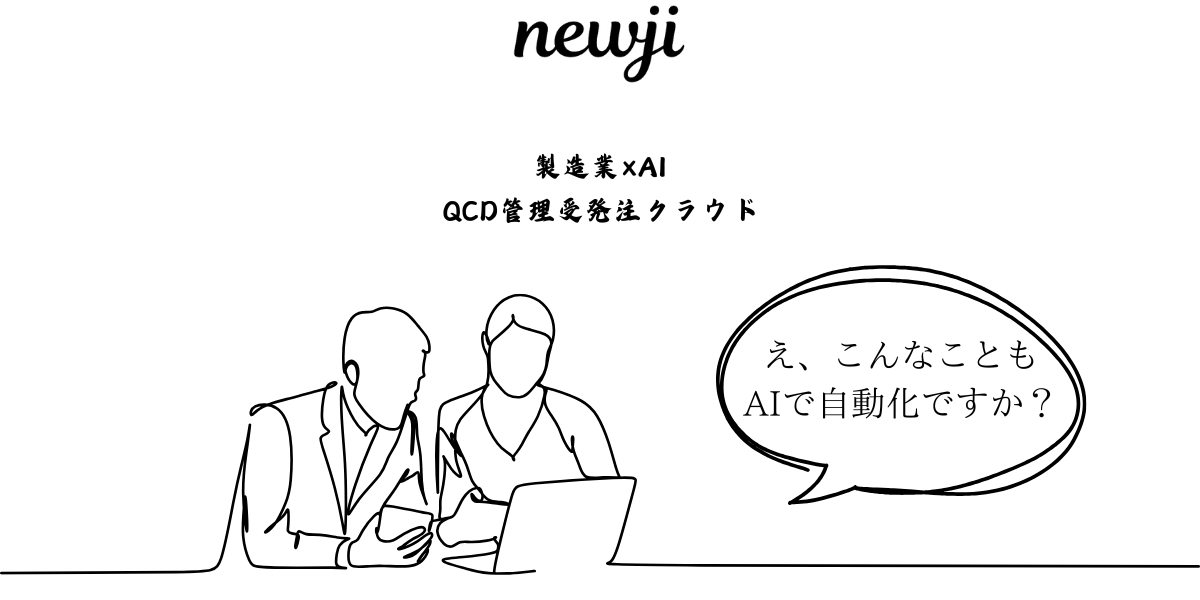
Manufacturing method of high-precision zinc alloy and its use case in the precision equipment market
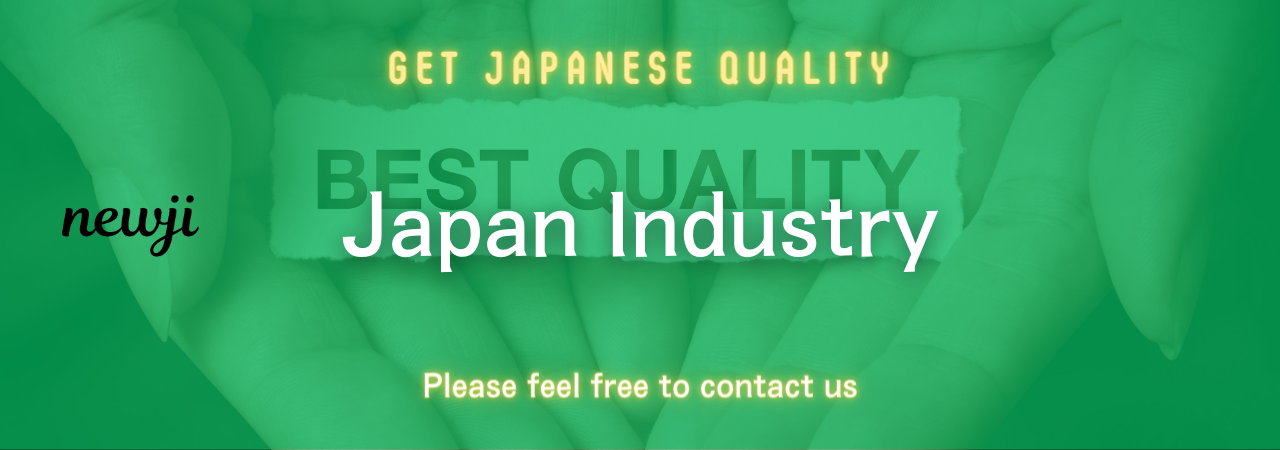
目次
Introduction to Zinc Alloy
Zinc alloy has been a vital material in the manufacturing industry due to its excellent mechanical properties and versatility.
It is a combination of zinc and other metals, typically aluminum, magnesium, and copper, crafted into an alloy that exhibits improved strength, corrosion resistance, and thermal conductivity.
The precision equipment market, in particular, relies on high-precision zinc alloys to ensure accurate, reliable products.
This article delves into the manufacturing method of high-precision zinc alloy and explores its use cases in the precision equipment market.
Manufacturing Method of High-Precision Zinc Alloy
Selection of Raw Materials
The journey begins with the careful selection of raw materials.
Pure zinc is the primary raw material for creating zinc alloy, selected for its superior inherent properties.
Metals like aluminum, copper, and magnesium are chosen based on the specific properties desired in the final product, such as increased strength or better corrosion resistance.
Melting Process
Once the raw materials are selected, they enter the melting stage.
The metals are heated to extremely high temperatures in a furnace to achieve full liquefaction.
This process ensures that all constituents mix evenly, contributing to a homogeneous final product.
Alloying
During the alloying phase, precise amounts of alloying metals are introduced into the molten zinc.
The process requires stringent control and supervision to maintain the correct proportions of each metal to achieve the desired final properties.
Cutting-edge technology is frequently used to monitor the composition and maintain consistent quality.
Refinement and Degassing
Refinement is crucial to creating a high-precision zinc alloy.
This process involves the removal of impurities that can affect the performance and durability of the alloy.
Degassing is also undertaken to remove gases that may be trapped during melting, which can lead to corrosion and structural defects.
Cooling and Casting
After refinement, the molten alloy is cooled at a controlled rate to prevent the formation of unwanted crystalline structures.
It is then cast into molds.
The shapes and sizes of the molds vary according to the intended use of the final product, and special molds are sometimes used to achieve specific dimensions and tolerances.
Heat Treatment
Heat treatment is an optional, but often critical, step in the production of zinc alloys.
The material is reheated and then gradually cooled to enhance the mechanical properties of the alloy, such as toughness and elasticity.
Different heat treatment processes help tailor the properties of the alloy based on the intended application.
Use Cases of High-Precision Zinc Alloy in the Precision Equipment Market
Automotive Industry
High-precision zinc alloys have found widespread use in the automotive industry due to their strength and lightweight nature.
They are commonly used in manufacturing fuel systems, braking components, and chassis parts, where precision and reliability are of utmost importance.
Electronic Devices
The electronics industry takes advantage of zinc alloys for the manufacturing of components that require high conductivity and corrosion resistance.
They are eminently suitable for making connectors, brackets, and heat sinks, which are vital for maintaining the integrity of electronic devices.
Medical Equipment
In the medical sector, zinc alloys are employed in creating complex, high-precision components for medical devices.
Their use ensures not only the durability of devices but also safety and reliability.
Examples include parts for surgical instruments and imaging equipment, where precision and safety are critical.
Telecommunications
Components made of zinc alloys are crucial in the telecommunications industry as well.
They are used in the production of connectors and housings for communications devices, offering both protection and superior performance.
The demand for robust and reliable materials in this sector is consistently met by high-precision zinc alloys.
Aerospace and Defense
The aerospace and defense sectors demand materials that can withstand extreme conditions while maintaining integrity.
Zinc alloys are chosen for components such as gears, bearings, and structural parts in aircraft and defense systems, owing to their ability to endure rigorous conditions and maintain high reliability.
Conclusion
High-precision zinc alloys are indispensable in the precision equipment market due to their unique combination of properties.
Their robust nature, coupled with versatility, makes them suitable for a wide range of applications across various industries, including automotive, electronics, medical, telecommunications, and aerospace.
Through a meticulous manufacturing process involving selection, melting, alloying, refinement, and heat treatment, high-precision zinc alloys are crafted to meet rigorous standards and specific industry requirements.
As technological advancements continue, we can anticipate further innovations in zinc alloy compositions and manufacturing processes, expanding their applications and cementing their importance in the precision equipment market.
資料ダウンロード
QCD管理受発注クラウド「newji」は、受発注部門で必要なQCD管理全てを備えた、現場特化型兼クラウド型の今世紀最高の受発注管理システムとなります。
ユーザー登録
受発注業務の効率化だけでなく、システムを導入することで、コスト削減や製品・資材のステータス可視化のほか、属人化していた受発注情報の共有化による内部不正防止や統制にも役立ちます。
NEWJI DX
製造業に特化したデジタルトランスフォーメーション(DX)の実現を目指す請負開発型のコンサルティングサービスです。AI、iPaaS、および先端の技術を駆使して、製造プロセスの効率化、業務効率化、チームワーク強化、コスト削減、品質向上を実現します。このサービスは、製造業の課題を深く理解し、それに対する最適なデジタルソリューションを提供することで、企業が持続的な成長とイノベーションを達成できるようサポートします。
製造業ニュース解説
製造業、主に購買・調達部門にお勤めの方々に向けた情報を配信しております。
新任の方やベテランの方、管理職を対象とした幅広いコンテンツをご用意しております。
お問い合わせ
コストダウンが利益に直結する術だと理解していても、なかなか前に進めることができない状況。そんな時は、newjiのコストダウン自動化機能で大きく利益貢献しよう!
(β版非公開)