- お役立ち記事
- Manufacturing Methods for Simultaneous Inventory Reduction and Lead Time Shortening/ Productivity Improvement
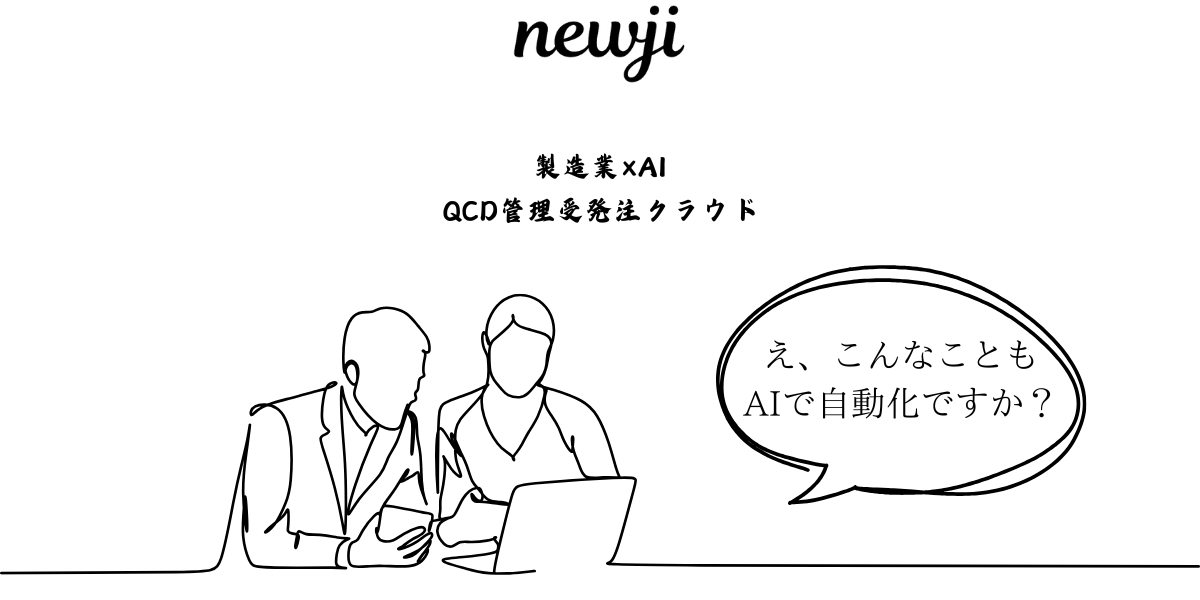
Manufacturing Methods for Simultaneous Inventory Reduction and Lead Time Shortening/ Productivity Improvement
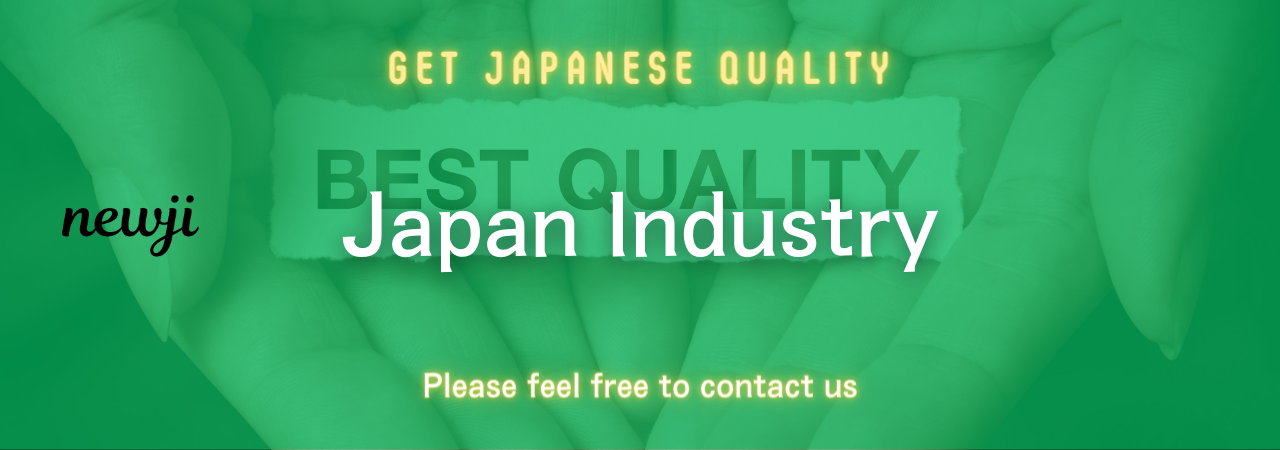
Reducing inventory while also shortening lead times and boosting productivity can seem like an impossible juggling act for manufacturers.
But with the right strategies, it’s entirely achievable.
Incorporating efficient manufacturing methods can streamline operations, resulting in a finely tuned, well-oiled machine.
目次
Lean Manufacturing
Lean manufacturing is about removing waste from the production process.
It focuses on value-added activities and eliminates anything that doesn’t contribute to the customer’s needs.
There are several principles within lean manufacturing, such as:
Just-In-Time (JIT) Production
JIT production is a key element of lean manufacturing.
It means producing goods only when they are needed and in the quantity required.
This method drastically reduces inventory levels as you’re not storing large amounts of stock.
It allows companies to quickly respond to customer demands and changes in the market.
5S Methodology
Derived from five Japanese terms beginning with ‘S’, this methodology aims to organize the workspace and keep it tidy.
The steps include:
– Seiri (Sort): Remove unnecessary items from the workspace.
– Seiton (Set in order): Arrange essential items so they are easily accessible.
– Seiso (Shine): Clean the workspace regularly.
– Seiketsu (Standardize): Establish standards for the first three steps.
– Shitsuke (Sustain): Maintain and review standards consistently.
Adopting 5S enhances productivity by reducing time lost searching for tools and components, leading to faster production times.
Quick Changeover Techniques
Adopting quick changeover techniques can significantly reduce downtime between production runs.
The single minute exchange of die (SMED) is a methodology tailored for quick changeovers.
Components of SMED
– Internal Activities: These are activities that can only be performed when the machine is stopped, such as changing tools or dies.
– External Activities: Tasks that can be done while the machine is still running, such as preparing tools and materials.
The idea is to convert as many internal activities to external ones as possible, so the machine spends minimal time idle during changeovers.
Implementation Steps
1. **Observe the Current Changeover Process**: Identify steps and classify them as internal or external.
2. **Convert Internal to External**: Wherever possible, move internal activities to the external category.
3. **Streamline and Standardize**: Simplify and standardize both internal and external activities to save time.
4. **Continuous Improvement**: Regularly review and refine the process for further efficiency gains.
Cellular Manufacturing
Cellular manufacturing involves arranging workstations in a sequence that supports a smooth flow of materials and components through the production process.
It is the opposite of a traditional batch-and-queue system.
Advantages
– **Reduced Lead Time**: By moving materials more efficiently and evenly, lead times are shortened.
– **Lower Inventory Levels**: Work-in-progress inventory is minimized because parts move through the system more quickly.
– **Enhanced Flexibility**: Quickly adaptable to changes in product design or demand.
– **Improved Morale**: Enhanced job satisfaction due to varied work and reduced monotony.
Technology Integration
The use of technology can play a crucial role in inventory reduction and lead time shortening.
Enterprise Resource Planning (ERP) Systems
ERP systems integrate various functions of a business into one comprehensive system.
By doing so, they provide real-time information, enhancing decision-making processes related to inventory and production planning.
Automated Inventory Tracking
Using RFID tags or barcode systems can improve inventory accuracy.
These systems provide real-time tracking, which helps in maintaining optimal inventory levels and reduces the likelihood of stockouts or overstock.
Advanced Manufacturing Techniques
Additive manufacturing (3D printing) and CNC machining can be used for just-in-time production.
These technologies allow for rapid prototyping and production without the need for extensive inventory.
Training and Employee Involvement
Investing in training and encouraging employee involvement is a strategy often overlooked but essential.
Skills Development
Providing regular training on the latest manufacturing techniques and tools empowers employees to work more efficiently.
Skilled employees are better equipped to troubleshoot problems that could otherwise hinder productivity.
Employee Involvement Programs
Programs like Kaizen circles involve employees in continuous improvement efforts.
Who better to suggest process improvements than those working directly on the production line?
Involving employees fosters a sense of ownership and commitment, leading to more innovative solutions and enhancements in productivity.
Continuous Improvement Culture
A culture of continuous improvement is vital for long-term success.
Regular Audits
Conduct regular audits to identify inefficiencies in the manufacturing process.
What may seem like a minor issue can add up to significant time and cost savings when resolved.
Open Communication
Foster a culture of open communication where all employees can share their insights and suggestions.
A collective approach often yields the best solutions for reducing inventory and improving lead times.
By integrating these methodologies and fostering a culture of continuous improvement, manufacturers can achieve reduced inventory levels, shorter lead times, and higher productivity.
While it may require an initial investment of time and resources, the long-term gains far outweigh the efforts, setting the stage for a more efficient and competitive operation.
資料ダウンロード
QCD調達購買管理クラウド「newji」は、調達購買部門で必要なQCD管理全てを備えた、現場特化型兼クラウド型の今世紀最高の購買管理システムとなります。
ユーザー登録
調達購買業務の効率化だけでなく、システムを導入することで、コスト削減や製品・資材のステータス可視化のほか、属人化していた購買情報の共有化による内部不正防止や統制にも役立ちます。
NEWJI DX
製造業に特化したデジタルトランスフォーメーション(DX)の実現を目指す請負開発型のコンサルティングサービスです。AI、iPaaS、および先端の技術を駆使して、製造プロセスの効率化、業務効率化、チームワーク強化、コスト削減、品質向上を実現します。このサービスは、製造業の課題を深く理解し、それに対する最適なデジタルソリューションを提供することで、企業が持続的な成長とイノベーションを達成できるようサポートします。
オンライン講座
製造業、主に購買・調達部門にお勤めの方々に向けた情報を配信しております。
新任の方やベテランの方、管理職を対象とした幅広いコンテンツをご用意しております。
お問い合わせ
コストダウンが利益に直結する術だと理解していても、なかなか前に進めることができない状況。そんな時は、newjiのコストダウン自動化機能で大きく利益貢献しよう!
(Β版非公開)