- お役立ち記事
- Manufacturing Process of Accelerator Pedals and Response Speed Enhancement
月間76,176名の
製造業ご担当者様が閲覧しています*
*2025年3月31日現在のGoogle Analyticsのデータより
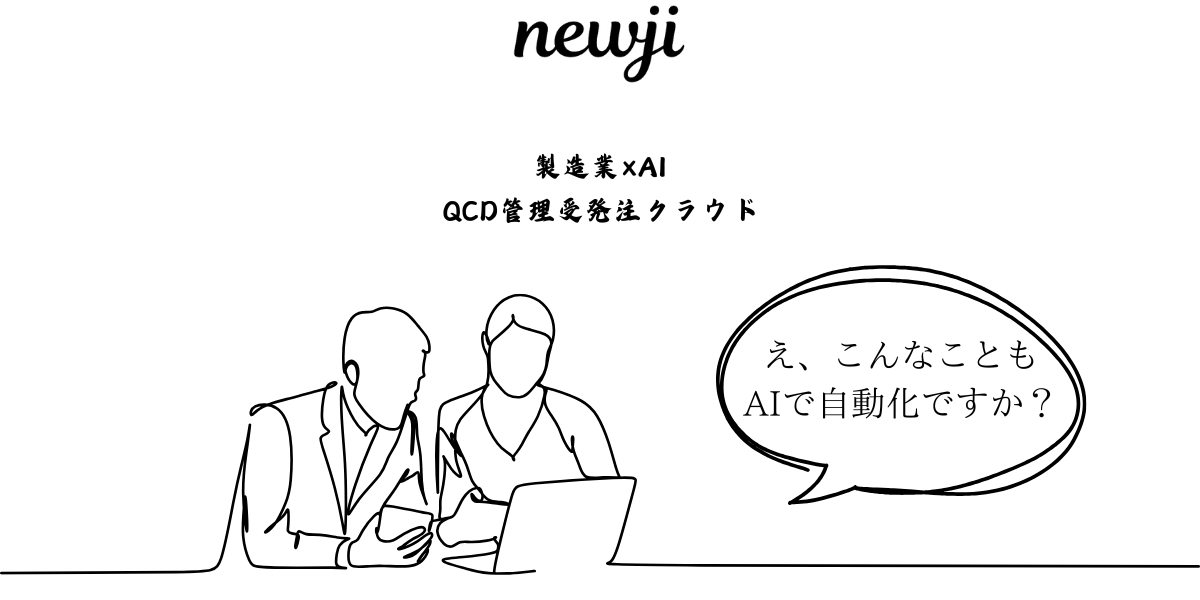
Manufacturing Process of Accelerator Pedals and Response Speed Enhancement
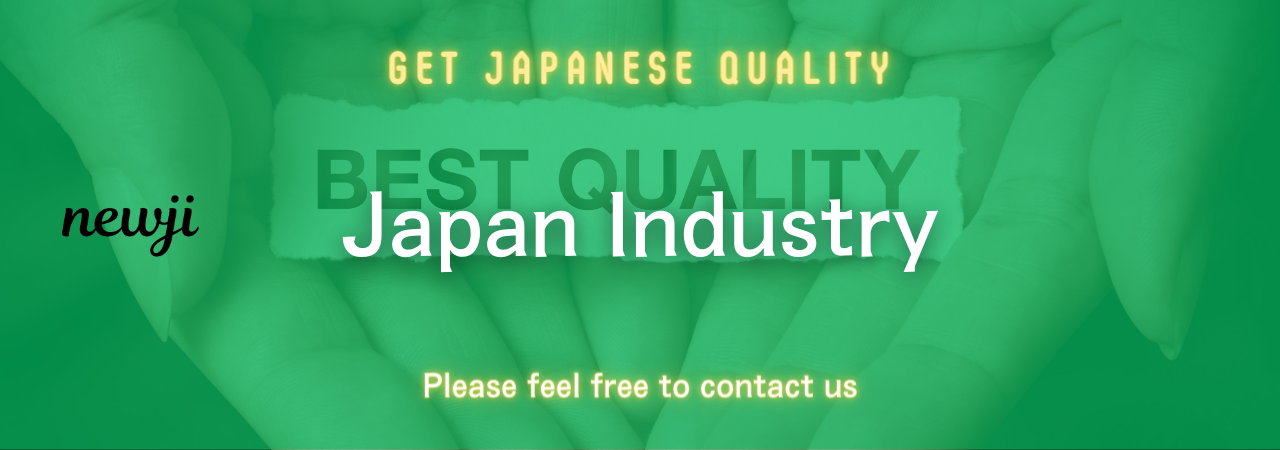
目次
Introduction to Accelerator Pedals
Accelerator pedals are crucial components of any vehicle.
They are responsible for controlling the engine’s power by managing the throttle.
When you press the pedal, it sends signals to the engine’s control unit, adjusting the amount of fuel and air mixture fed into the engine.
A well-functioning accelerator pedal ensures smoother rides and better engine performance.
Materials Used in Accelerator Pedals
The manufacturing of accelerator pedals begins with selecting the right materials.
Most modern accelerator pedals are made from a combination of metals, plastics, and electronic components.
The pedal arm is often made from high-strength steel or aluminum, which provides durability and strength.
Plastics are used for the pedal pad to ensure comfort and grip for the driver’s foot.
Electronic components, such as sensors and wiring, are used to communicate with the vehicle’s engine control unit.
Types of Plastics
Different types of plastics are used in various parts of the pedal.
For instance, polycarbonate is often used for its high impact resistance.
Thermoplastic elastomers (TPE) provide flexibility and longevity, making them ideal for the pedal’s surface.
Electronic Components
Modern cars increasingly rely on electronic sensors to perform numerous functions.
Hall effect sensors and potentiometers are commonly used in accelerator pedals to measure pedal position.
These sensors convert the physical movement of the pedal into an electrical signal that the engine control unit can interpret.
Manufacturing Process
The manufacturing process for accelerator pedals involves several stages, from material preparation to assembly and quality control.
Each step is crucial for ensuring that the final product is both functional and safe.
Material Preparation
The first step in the manufacturing process is material preparation.
Metals are cut and shaped using advanced machinery.
Plastics are melted and molded into the desired shapes, either by injection molding or vacuum forming.
Electronic components are either sourced from suppliers or manufactured in-house.
Machining and Forming
Once the materials are prepared, the metal parts go through machining processes.
Computer Numerical Control (CNC) machines precisely cut and shape the metal parts according to design specifications.
For plastic components, molds are created to form the pedal pad.
Both types of materials are then inspected for any defects.
Assembly
The next stage is assembly.
Metal and plastic parts are assembled together using various methods, such as welding, riveting, or using adhesives.
Electronic sensors are integrated into the pedal during this stage.
Wiring is meticulously connected to ensure reliable communication with the vehicle’s engine control unit.
Assembly often takes place on automated production lines to ensure consistency and efficiency.
Quality Control
Quality control is a critical aspect of the manufacturing process.
Each accelerator pedal undergoes rigorous testing to ensure it meets safety and performance standards.
Tests include stress tests, functionality tests, and environmental tests to simulate real-world conditions.
Any pedal that fails these tests is either reworked or discarded.
Packaging and Distribution
Once the pedals pass quality control, they are packaged and prepared for distribution.
Packaging is designed to protect the pedals during shipping and handling.
Labels with essential information, such as part numbers and manufacturing dates, are also attached.
The packaged pedals are then shipped to vehicle manufacturers, suppliers, or directly to consumers.
Technology and Response Speed Enhancement
With advancements in technology, accelerator pedals have become more sophisticated.
One key area of focus is enhancing the response speed of the pedal, which directly impacts the driving experience.
Drive-by-Wire Systems
Traditional mechanical linkages between the accelerator pedal and the engine have been replaced by drive-by-wire systems.
In these systems, electronic signals are used to control the throttle, resulting in quicker response times.
When the driver presses the accelerator, sensors send data to the engine control unit almost instantaneously, improving the vehicle’s overall performance.
Improved Sensor Technologies
The development of advanced sensor technologies has also played a significant role in enhancing response speed.
High-precision sensors, such as Hall effect sensors and magneto-resistive sensors, provide more accurate readings of pedal position.
These sensors are less susceptible to wear and tear, ensuring consistent performance over time.
Software Optimization
Software optimization is another crucial factor in improving response speed.
Engine control units are programmed with advanced algorithms that analyze data from the accelerator pedal in real-time.
These algorithms predict the driver’s intentions and adjust the engine parameters accordingly, minimizing any delays between pedal input and acceleration.
Regular software updates can further enhance performance, ensuring the system remains cutting-edge.
Future Trends
As technology continues to evolve, we can expect further innovations in accelerator pedal design and functionality.
Research is ongoing into new materials that could make pedals lighter and more durable.
Advancements in sensor technology and artificial intelligence (AI) could lead to even quicker response times and enhanced safety features.
Integration with Autonomous Vehicles
As autonomous vehicles become more prevalent, accelerator pedals will need to integrate seamlessly with self-driving systems.
This integration may involve more complex sensors and communication protocols to ensure that the autonomous vehicle can control speed and acceleration safely.
Eco-Friendly Materials
With a growing focus on sustainability, manufacturers are exploring eco-friendly materials for accelerator pedals.
Biodegradable plastics and recycled metals could reduce the environmental impact of production.
Enhanced User Experience
Future accelerator pedals may also include features designed to enhance the user experience.
For example, pedals could incorporate haptic feedback to provide drivers with tactile alerts or resistance adjustments based on driving conditions.
Conclusion
The manufacturing process of accelerator pedals is a complex and intricate endeavor that involves multiple stages and various materials.
With advancements in technology, these pedals have become more efficient, reliable, and responsive.
As the automotive industry continues to innovate, the humble accelerator pedal will undoubtedly continue to evolve, offering enhanced performance and safety for drivers worldwide.
資料ダウンロード
QCD管理受発注クラウド「newji」は、受発注部門で必要なQCD管理全てを備えた、現場特化型兼クラウド型の今世紀最高の受発注管理システムとなります。
ユーザー登録
受発注業務の効率化だけでなく、システムを導入することで、コスト削減や製品・資材のステータス可視化のほか、属人化していた受発注情報の共有化による内部不正防止や統制にも役立ちます。
NEWJI DX
製造業に特化したデジタルトランスフォーメーション(DX)の実現を目指す請負開発型のコンサルティングサービスです。AI、iPaaS、および先端の技術を駆使して、製造プロセスの効率化、業務効率化、チームワーク強化、コスト削減、品質向上を実現します。このサービスは、製造業の課題を深く理解し、それに対する最適なデジタルソリューションを提供することで、企業が持続的な成長とイノベーションを達成できるようサポートします。
製造業ニュース解説
製造業、主に購買・調達部門にお勤めの方々に向けた情報を配信しております。
新任の方やベテランの方、管理職を対象とした幅広いコンテンツをご用意しております。
お問い合わせ
コストダウンが利益に直結する術だと理解していても、なかなか前に進めることができない状況。そんな時は、newjiのコストダウン自動化機能で大きく利益貢献しよう!
(β版非公開)