- お役立ち記事
- Manufacturing Process of Acrylic Desk Organizers and Storage Capacity Improvement
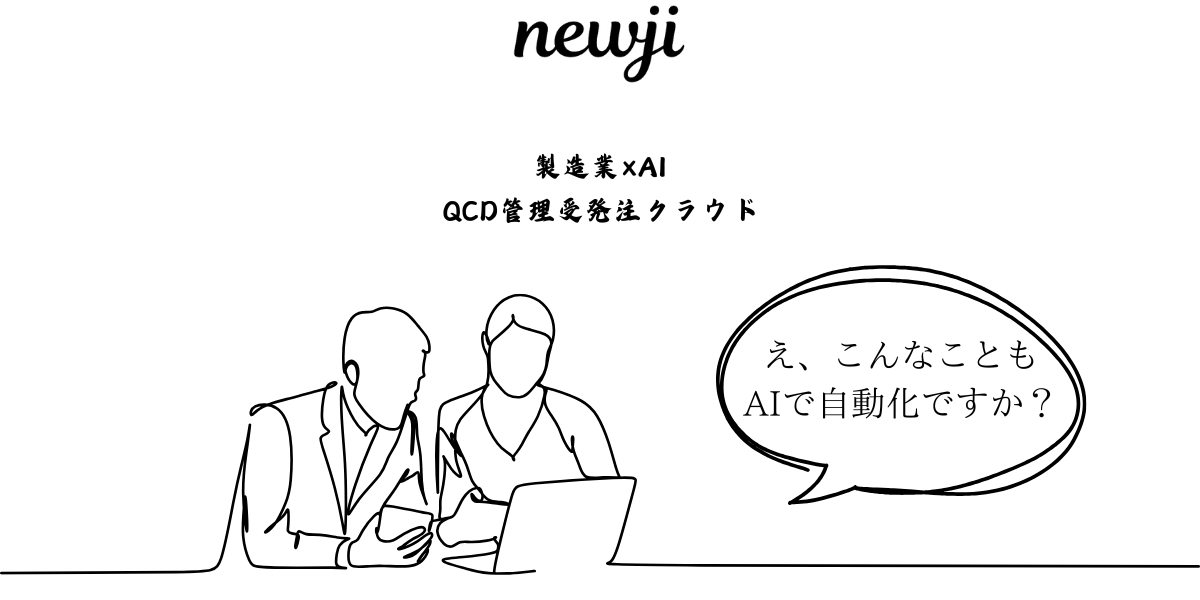
Manufacturing Process of Acrylic Desk Organizers and Storage Capacity Improvement
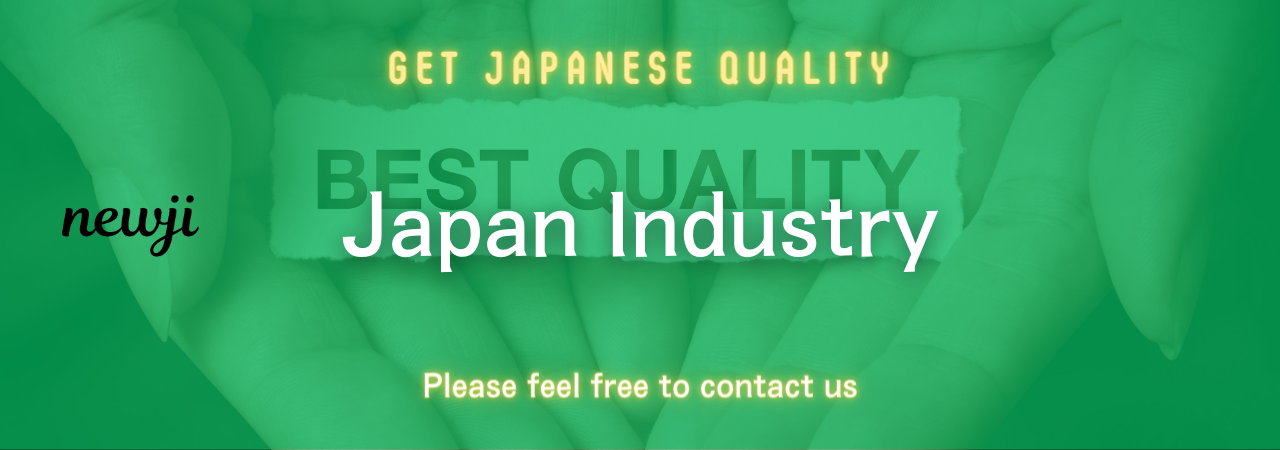
Acrylic desk organizers are frequently chosen for their aesthetic appeal, durability, and functionality.
These products can enhance the tidiness and efficiency of any workspace.
Let’s delve into the steps involved in their manufacturing process and explore ways to improve their storage capacity.
目次
Introduction to Acrylic Desk Organizers
Acrylic desk organizers are popular for their transparency, sturdiness, and ease of maintenance.
They are perfect for keeping office supplies, stationery, and other small items organized.
The manufacturing process combines advanced technology and precise craftsmanship to produce high-quality organizers.
The Manufacturing Process
Creating acrylic desk organizers involves several key steps:
1. Material Selection
The first step is choosing high-quality acrylic sheets.
Acrylic is a type of plastic known for its clarity, strength, and lightweight properties.
Manufacturers opt for acrylic sheets with the right thickness and transparency for the desired product.
2. Cutting the Sheets
Once the acrylic sheets are selected, they are cut into the required shapes and sizes using laser cutting machines.
Laser cutting ensures clean, precise edges and allows for intricate designs.
This step is crucial for the overall look and functionality of the desk organizer.
3. Shaping and Bending
Next, the cut acrylic pieces are shaped and bent into the desired forms.
Acrylic becomes pliable when heated, allowing manufacturers to mold it into various configurations.
Specialized heating techniques help in achieving the exact bends needed for specific designs.
4. Assembling the Parts
After shaping, the different parts are assembled together.
This can involve techniques like solvent welding, where a chemical solvent is used to bond the pieces.
This process ensures strong, seamless joints.
In some cases, screws or other fasteners are used to reinforce the structure.
5. Polishing and Finishing
The assembled organizers are then polished to remove any rough edges and achieve a smooth, glossy finish.
Polishing machines and hand-polishing methods are employed to enhance the acrylic’s clarity and shine.
A high-quality finish not only improves aesthetics but also ensures durability.
6. Quality Inspection
The final step is quality inspection.
Each acrylic desk organizer is thoroughly checked for defects, stability, and overall appearance.
This ensures that only products meeting the highest standards reach the market.
Improving Storage Capacity
Enhancing the storage capacity of acrylic desk organizers can make them even more practical for users.
Here are some strategies:
1. Modular Design
Designing organizers with modular components can greatly increase storage capacity.
Users can add or remove sections based on their needs.
This flexibility allows for better customization and maximization of available space.
2. Multi-Level Compartments
Incorporating multi-level compartments within the organizer can help in maximizing vertical space.
Different tiers can be used for storing various items without cluttering the desktop.
This approach not only increases capacity but also improves accessibility.
3. Sliding Drawers
Adding sliding drawers to the organizer can provide hidden storage space for smaller items.
Drawers help in keeping supplies neatly tucked away, yet easily accessible when needed.
This can contribute to a cleaner and more organized work surface.
4. Adjustable Dividers
Incorporate adjustable dividers within the compartments.
This allows users to modify the spaces according to the sizes of their items.
Adjustable dividers enhance the versatility of the organizer, making it suitable for a wider range of supplies.
5. Utilizing Corner Spaces
Designing organizers to fit into corners can make efficient use of often-overlooked desk areas.
Corner organizers can save space and provide additional storage without encroaching on the main work area.
6. Stackable Units
Creating stackable units enables users to expand their storage vertically.
Stackable organizers can be especially useful in smaller workspaces where desktop space is limited.
This design can help in keeping the desk neat while providing ample storage options.
Conclusion
The manufacturing process of acrylic desk organizers is a meticulous blend of technology and craftsmanship.
Each step, from material selection to quality inspection, ensures the production of high-quality, durable organizers.
Enhancing storage capacity with strategies such as modular design, multi-level compartments, sliding drawers, adjustable dividers, corner utilization, and stackable units can make these organizers even more functional.
By understanding both the production process and the potential for improved storage, users can better appreciate the value and versatility of acrylic desk organizers.
資料ダウンロード
QCD調達購買管理クラウド「newji」は、調達購買部門で必要なQCD管理全てを備えた、現場特化型兼クラウド型の今世紀最高の購買管理システムとなります。
ユーザー登録
調達購買業務の効率化だけでなく、システムを導入することで、コスト削減や製品・資材のステータス可視化のほか、属人化していた購買情報の共有化による内部不正防止や統制にも役立ちます。
NEWJI DX
製造業に特化したデジタルトランスフォーメーション(DX)の実現を目指す請負開発型のコンサルティングサービスです。AI、iPaaS、および先端の技術を駆使して、製造プロセスの効率化、業務効率化、チームワーク強化、コスト削減、品質向上を実現します。このサービスは、製造業の課題を深く理解し、それに対する最適なデジタルソリューションを提供することで、企業が持続的な成長とイノベーションを達成できるようサポートします。
オンライン講座
製造業、主に購買・調達部門にお勤めの方々に向けた情報を配信しております。
新任の方やベテランの方、管理職を対象とした幅広いコンテンツをご用意しております。
お問い合わせ
コストダウンが利益に直結する術だと理解していても、なかなか前に進めることができない状況。そんな時は、newjiのコストダウン自動化機能で大きく利益貢献しよう!
(Β版非公開)