- お役立ち記事
- Manufacturing Process of Acrylic Display Cases and Transparency Reinforcement
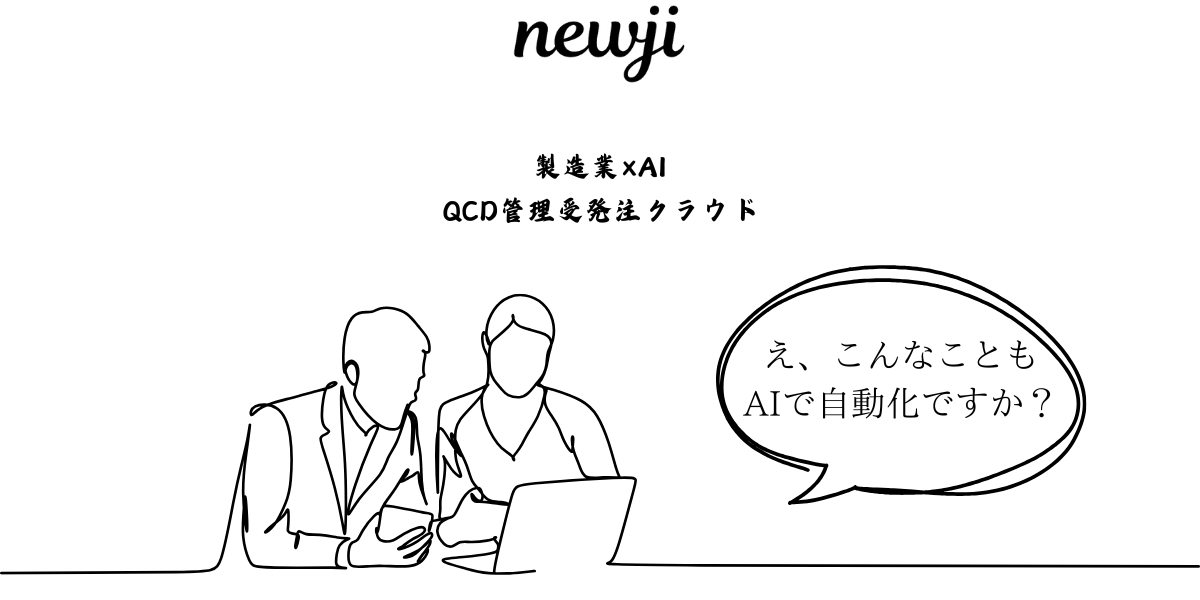
Manufacturing Process of Acrylic Display Cases and Transparency Reinforcement
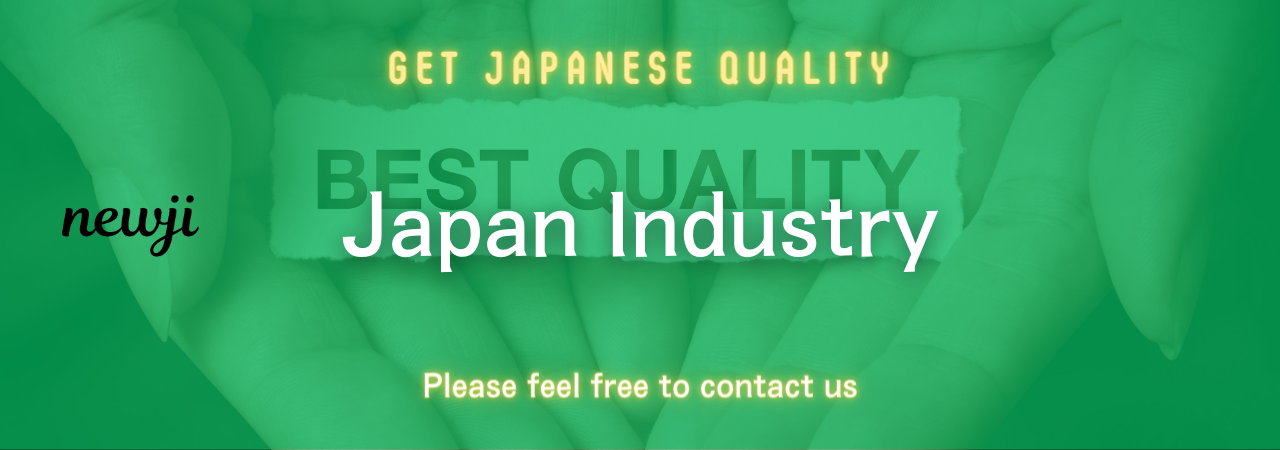
Acrylic display cases are widely used to showcase various items, from collectibles to jewelry, due to their transparency, durability, and aesthetic appeal.
Understanding the manufacturing process of these cases and the techniques used to enhance their transparency can provide a deeper appreciation for their quality.
Here, we delve into the step-by-step process of how acrylic display cases are made and some methods used to ensure they remain clear and spotless.
目次
1. Material Selection
The first step in manufacturing an acrylic display case is choosing high-quality acrylic materials.
Acrylic, also known as polymethyl methacrylate (PMMA), is preferred for its excellent optical clarity and strength.
Plexiglass vs. Acrylic
Plexiglass is a type of acrylic, but not all acrylic is plexiglass.
Manufacturers often choose Plexiglass for its superior clarity and resistance to yellowing over time.
2. Cutting the Acrylic Sheets
Once the material is selected, the next step is cutting the acrylic sheets into the desired shapes and sizes.
This process uses precision machinery like laser cutters or CNC (Computer Numerical Control) machines to ensure accuracy and clean edges.
Laser Cutting
Laser cutting offers a high degree of precision and can create complex shapes with smooth edges.
The intense heat from the laser melts the acrylic, producing a polished finish.
CNC Machining
CNC machines use computer-controlled tools to cut the acrylic.
This method is highly accurate and suitable for thicker acrylic sheets that laser cutters might struggle with.
3. Forming the Parts
After cutting, the acrylic pieces need to be molded into the necessary shapes.
This step can involve bending or thermoforming, depending on the design of the display case.
Bending
For simple designs, bending the acrylic sheets is often sufficient.
The sheets are heated until they become pliable, then bent into the required shapes and allowed to cool.
Thermoforming
Thermoforming involves heating the acrylic sheets and then placing them over a mold.
A vacuum is then used to shape the acrylic sheet around the mold, producing more complex shapes and contours.
4. Assembling the Case
Once the various parts are shaped, the next step is to assemble the display case.
This process involves joining the parts together using adhesives or mechanical fasteners.
Adhesive Bonding
Special adhesives designed for acrylic are used to bond the pieces together.
The adhesive is applied to the edges, and the parts are held in place until the bond sets, resulting in a seamless join.
Mechanical Fastening
In some cases, mechanical fasteners like screws or rivets are used to assemble the display case.
These are typically covered or hidden to maintain the aesthetic appeal of the case.
5. Finishing the Edges
Finishing the edges of the display case is crucial for both safety and aesthetics.
Rough edges can be sharp and detract from the overall look of the case.
Polishing
Edge polishing enhances the transparency of the acrylic and provides a smooth, glass-like finish.
This process can be done using various methods, including flame polishing, buffing, and sanding.
Flame Polishing
Flame polishing involves using a flame to melt and smooth the edges of the acrylic.
This method is quick and effective for achieving a high-gloss finish.
Buffing and Sanding
Buffing and sanding are more labor-intensive but result in a polished, smooth edge.
Gradual sanding with increasingly fine grits, followed by buffing with a special polishing compound, produces excellent results.
6. Ensuring Transparency
Maintaining the clarity of acrylic display cases is essential.
Various techniques are used during and after manufacturing to ensure the cases remain transparent and free from defects.
Anti-Static Coatings
Acrylic can attract dust due to static electricity.
Applying an anti-static coating can help repel dust and keep the surface clean.
UV Coatings
UV coatings protect the acrylic from yellowing and damage caused by UV light.
This coating helps maintain the clarity and appearance of the display case over time.
Cleaning and Maintenance
Regular cleaning with appropriate cleaners designed for acrylic is crucial.
These cleaners prevent scratches and maintain the transparency of the acrylic.
Quality Control
The final step in manufacturing acrylic display cases is ensuring they meet quality standards.
This involves inspecting the cases for defects, such as scratches, bubbles, or imperfections in the acrylic.
Visual Inspection
A thorough visual inspection is conducted to detect any visible flaws.
Minor defects can often be polished out, while more significant issues may require reworking or rejecting the part.
Dimensional Accuracy
The dimensions of the acrylic display case are carefully checked to ensure they meet the required specifications.
This ensures that the case will fit together correctly and provide the desired level of protection and display.
By understanding these steps, consumers can better appreciate the craftsmanship involved in producing these elegant and functional items.
From material selection and cutting to assembly and quality control, each stage plays a crucial role in delivering a product that meets high standards of clarity and durability.
With proper care and maintenance, these display cases can provide long-lasting transparency and functionality, highlighting the beauty of the items they showcase.
資料ダウンロード
QCD調達購買管理クラウド「newji」は、調達購買部門で必要なQCD管理全てを備えた、現場特化型兼クラウド型の今世紀最高の購買管理システムとなります。
ユーザー登録
調達購買業務の効率化だけでなく、システムを導入することで、コスト削減や製品・資材のステータス可視化のほか、属人化していた購買情報の共有化による内部不正防止や統制にも役立ちます。
NEWJI DX
製造業に特化したデジタルトランスフォーメーション(DX)の実現を目指す請負開発型のコンサルティングサービスです。AI、iPaaS、および先端の技術を駆使して、製造プロセスの効率化、業務効率化、チームワーク強化、コスト削減、品質向上を実現します。このサービスは、製造業の課題を深く理解し、それに対する最適なデジタルソリューションを提供することで、企業が持続的な成長とイノベーションを達成できるようサポートします。
オンライン講座
製造業、主に購買・調達部門にお勤めの方々に向けた情報を配信しております。
新任の方やベテランの方、管理職を対象とした幅広いコンテンツをご用意しております。
お問い合わせ
コストダウンが利益に直結する術だと理解していても、なかなか前に進めることができない状況。そんな時は、newjiのコストダウン自動化機能で大きく利益貢献しよう!
(Β版非公開)