- お役立ち記事
- Manufacturing Process of Acrylic Door Plates and Finish Precision Improvement
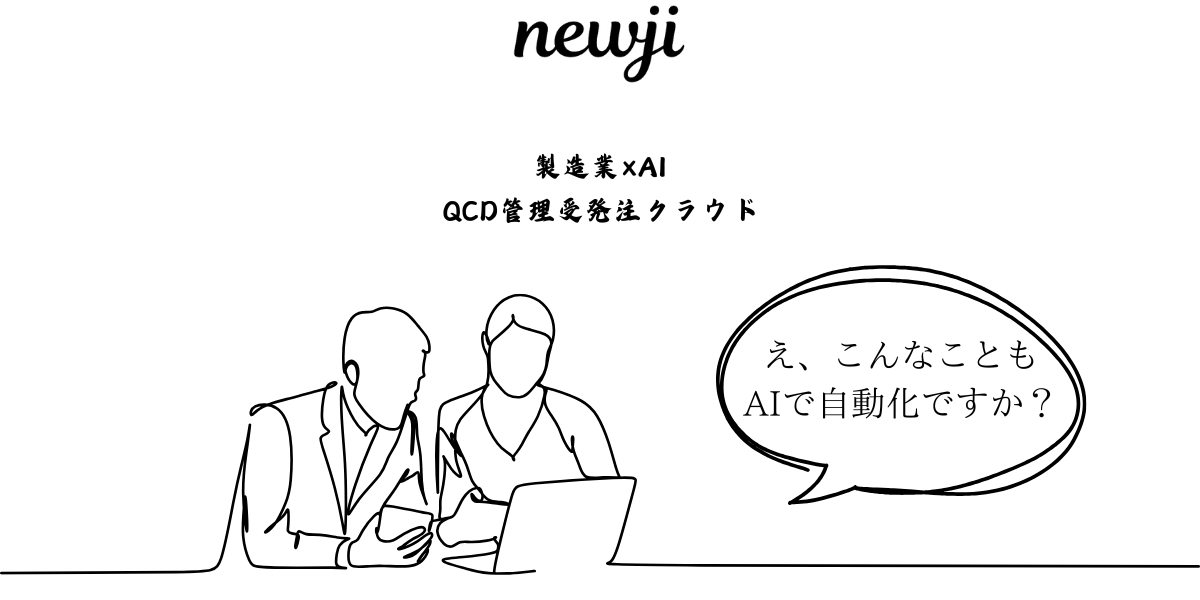
Manufacturing Process of Acrylic Door Plates and Finish Precision Improvement
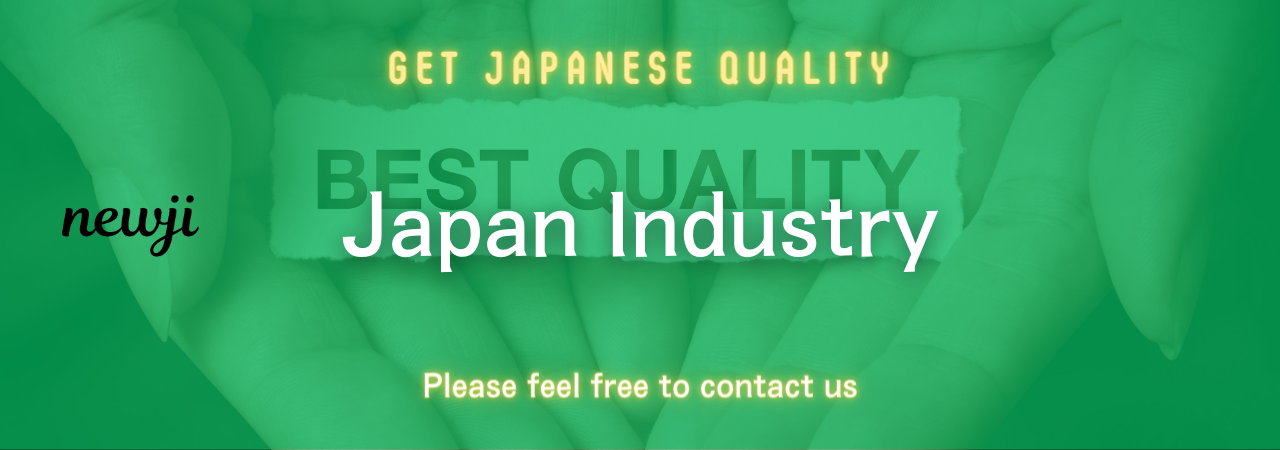
Acrylic door plates are becoming increasingly popular due to their durability, aesthetic appeal, and versatility.
Understanding the manufacturing process of these plates and the methods used to improve finish precision is essential for anyone involved in their production or use.
This article will take a closer look at the different stages involved in creating acrylic door plates and the techniques used to enhance their final appearance.
目次
Raw Material Selection
The first step in manufacturing acrylic door plates is selecting the right raw materials.
Acrylic is a synthetic polymer known for its clarity, strength, and lightweight properties.
Manufacturers choose high-quality acrylic sheets, usually cast or extruded, depending on the desired attributes of the final product.
Cast acrylic is preferred for premium applications due to its superior optical clarity and resistance to solvents.
Extruded acrylic is often chosen for more cost-sensitive projects as it is easier to thermoform and typically less expensive.
Cutting and Shaping
Once the raw materials are selected, the acrylic sheets undergo the cutting and shaping process.
Computer numerical control (CNC) machines are typically used for this purpose due to their precision and efficiency.
CNC machines can cut intricate shapes and designs with high accuracy, ensuring that each door plate is consistent in size and shape.
During this process, the acrylic sheets are securely clamped to the machine bed to prevent any movement that could lead to inaccuracies.
The cutting tools used are designed to minimize chipping and cracking, which are common issues when working with acrylic.
Polishing and Edge Finishing
After the acrylic sheets have been cut to the desired shape, the edges must be polished and finished.
This step is crucial for improving the overall appearance and safety of the door plates.
There are several methods used for polishing acrylic, including flame polishing, buffing, and diamond polishing.
Flame Polishing
Flame polishing involves passing a flame over the edges of the acrylic to melt and smooth them.
This method is quick and effective for achieving a glossy finish.
However, it requires skill to avoid overheating the acrylic, which can cause bubbling or warping.
Buffing
Buffing uses abrasive compounds and polishing wheels to smooth the edges.
This method is slower than flame polishing but provides excellent control over the finish quality.
Buffing is particularly useful for removing fine scratches and achieving a high-gloss finish.
Diamond Polishing
Diamond polishing uses diamond-tipped tools to grind and polish the edges of the acrylic.
This method is highly effective for achieving a precise and smooth finish.
It is often used for high-end applications where the highest level of clarity and smoothness is required.
Surface Treatment
The next step in the manufacturing process is the surface treatment of the acrylic door plates.
This step enhances the appearance and durability of the plates.
Common surface treatments include UV printing, screen printing, and laser engraving.
UV Printing
UV printing involves using ultraviolet light to cure ink directly onto the acrylic surface.
This method produces vibrant, long-lasting colors and can print detailed designs.
UV printing is ideal for custom door plates as it allows for personalized text and graphics.
Screen Printing
Screen printing uses a mesh screen to apply ink to the acrylic surface.
Each color requires a separate screen, making this method more suited for simple designs with fewer colors.
However, screen printing ink is highly durable and resistant to fading and wear.
Laser Engraving
Laser engraving uses a laser beam to etch designs into the acrylic surface.
This method provides high precision and can create intricate patterns and text.
Laser engraving is commonly used for adding logos, names, or other detailed elements to the door plates.
Assembly and Mounting
Once the surface treatment is complete, the acrylic door plates are ready for assembly and mounting.
This step involves attaching any additional components, such as mounting brackets, adhesive backing, or hardware for installation.
The assembly process varies depending on the specific design and intended use of the door plates.
For door plates with mounting brackets, the brackets are securely attached to the back of the acrylic plate using screws or adhesive.
For adhesive-backed plates, a strong, double-sided adhesive is applied to ensure a firm hold.
Ensuring proper alignment and securely attaching these components is crucial for the final product.
Quality Control
Quality control is a vital aspect of the manufacturing process for acrylic door plates.
Each plate undergoes a thorough inspection to ensure it meets the required standards for size, shape, finish, and durability.
Any plates that do not meet these standards are discarded or reworked to ensure only the best products are delivered to customers.
Inspectors check for any defects such as scratches, bubbles, or improper surface treatments.
Measurements are taken to ensure the plates match the specified dimensions.
This step ensures that the final product is of high quality and meets the customer’s expectations.
Packaging and Shipping
The final step in the manufacturing process is packaging and shipping the acrylic door plates.
Proper packaging is essential to protect the plates from damage during transportation.
Plates are typically wrapped in protective materials, such as bubble wrap or foam, to prevent scratches and breakage.
The plates are then placed in sturdy boxes or crates for shipping.
Proper labeling and documentation are prepared to ensure the plates reach their destination in perfect condition.
Manufacturers often work with reliable shipping partners to guarantee timely and safe delivery to their customers.
In conclusion, the manufacturing process for acrylic door plates involves several meticulous steps, from selecting high-quality raw materials to ensuring precise finishing and surface treatment.
Each step is designed to improve the final product’s appearance, precision, and durability.
Understanding these processes is essential for maximizing the quality and value of acrylic door plates in various applications.
資料ダウンロード
QCD調達購買管理クラウド「newji」は、調達購買部門で必要なQCD管理全てを備えた、現場特化型兼クラウド型の今世紀最高の購買管理システムとなります。
ユーザー登録
調達購買業務の効率化だけでなく、システムを導入することで、コスト削減や製品・資材のステータス可視化のほか、属人化していた購買情報の共有化による内部不正防止や統制にも役立ちます。
NEWJI DX
製造業に特化したデジタルトランスフォーメーション(DX)の実現を目指す請負開発型のコンサルティングサービスです。AI、iPaaS、および先端の技術を駆使して、製造プロセスの効率化、業務効率化、チームワーク強化、コスト削減、品質向上を実現します。このサービスは、製造業の課題を深く理解し、それに対する最適なデジタルソリューションを提供することで、企業が持続的な成長とイノベーションを達成できるようサポートします。
オンライン講座
製造業、主に購買・調達部門にお勤めの方々に向けた情報を配信しております。
新任の方やベテランの方、管理職を対象とした幅広いコンテンツをご用意しております。
お問い合わせ
コストダウンが利益に直結する術だと理解していても、なかなか前に進めることができない状況。そんな時は、newjiのコストダウン自動化機能で大きく利益貢献しよう!
(Β版非公開)