- お役立ち記事
- Manufacturing Process of Acrylic Pendants and Design Precision Improvement
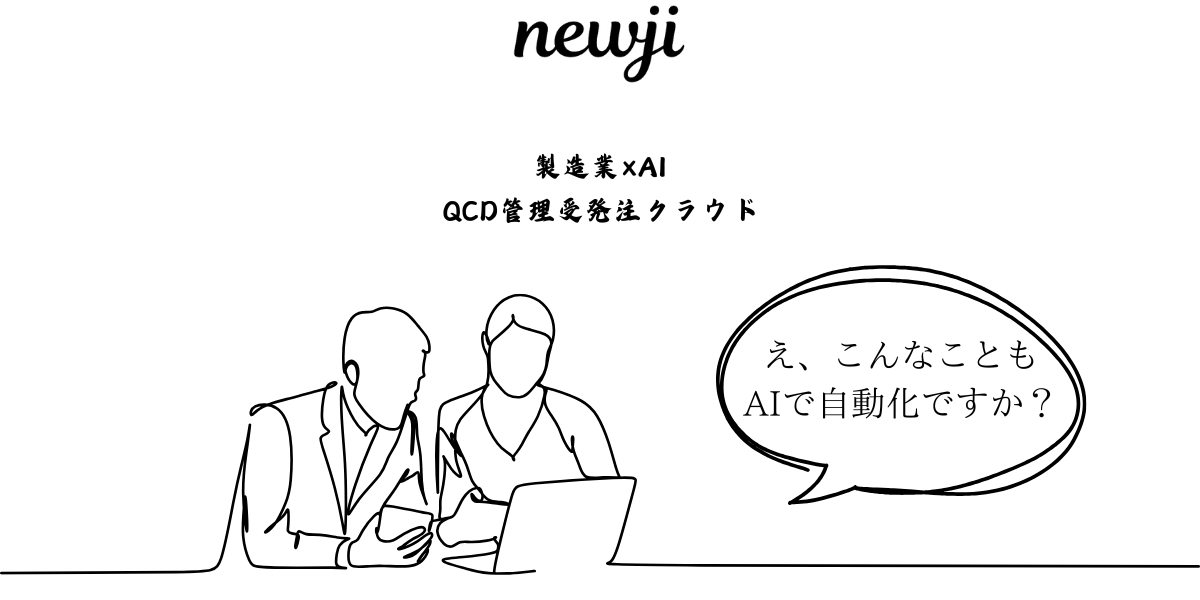
Manufacturing Process of Acrylic Pendants and Design Precision Improvement
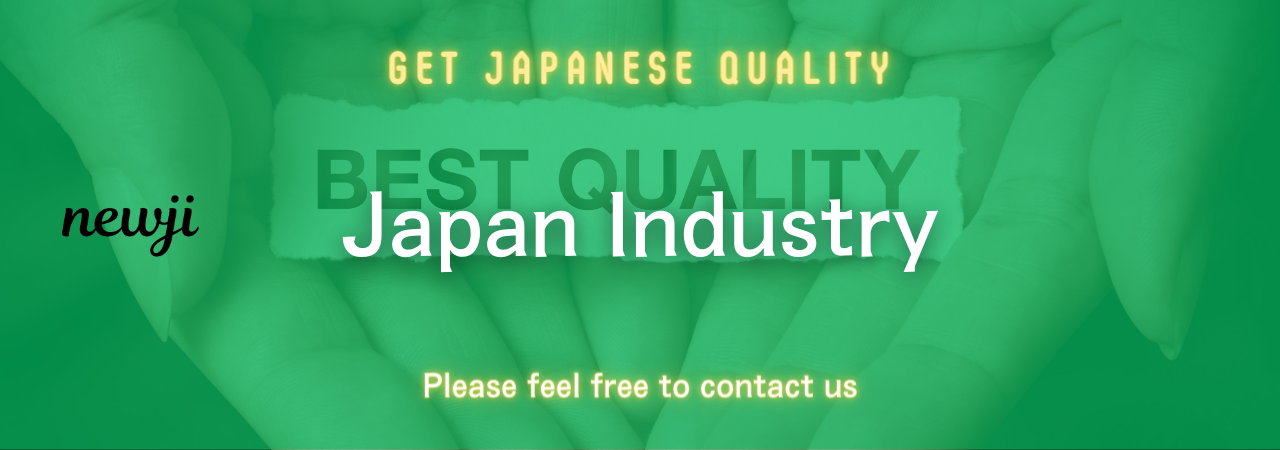
Acrylic pendants have become a popular choice for accessories, thanks to their durability and versatility.
These pendants can be made in various shapes, sizes, and colors, making them a favorite among jewelry enthusiasts.
To understand how these charming pendants are made and how their design precision is improved, let’s explore the manufacturing process and innovative techniques used in their creation.
目次
The Basics of Acrylic Material
Acrylic, also known as polymethyl methacrylate (PMMA), is a transparent thermoplastic often used as a lightweight and shatter-resistant alternative to glass.
Acrylic sheets are available in various thicknesses and are easy to cut, shape, and mold, making them ideal for crafting pendants.
The material’s clarity and weather resistance contribute to its widespread use in both functional and decorative items.
Step-by-Step Process of Making Acrylic Pendants
1. Designing the Pendant
The first step in creating an acrylic pendant is designing it.
The design process can involve manual sketching or computer-aided design (CAD) software.
CAD software allows designers to create precise digital models of the pendant, ensuring all aspects of the design are accurate and to scale.
The design can include various elements like shapes, patterns, text, and even 3D features.
2. Cutting the Acrylic
Once the design is finalized, the next step is to cut the acrylic sheet.
There are several methods to cut acrylic, but laser cutting is the most precise and efficient.
Laser cutting machines use a high-powered laser beam to cut through the acrylic sheet according to the digital design.
This method produces clean, smooth edges and allows for intricate designs that would be difficult to achieve with traditional cutting tools.
3. Shaping and Polishing
After the acrylic sheet is cut into the desired shape, the edges may need additional shaping and polishing.
This step ensures that the pendant has a smooth finish and no rough edges.
Various tools like sanders, files, and polishing compounds are used to achieve the desired smoothness and clarity.
For pendants requiring three-dimensional details, additional machining and polishing may be necessary.
4. Drilling Holes
Many acrylic pendants require holes for attaching chains, cords, or other mounting hardware.
These holes are often drilled using precision drills to ensure they are perfectly placed and sized.
Exact drilling is crucial for the pendant’s final appearance and functionality, as even minor misplacements can affect how the pendant hangs and moves.
5. Adding Color and Finishes
Acrylic pendants can be clear, tinted, or fully colored depending on the design requirements.
Colored acrylic sheets are available, but sometimes additional coloring or painting may be necessary.
Special techniques like screen printing, UV printing, or hand painting are used to apply intricate designs, patterns, or logos to the acrylic surface.
Finishes like gloss, matte, or frosted can also be applied to enhance the pendant’s appearance.
Improving Design Precision in Acrylic Pendants
1. Advanced CAD Software
Modern CAD software has significantly improved the precision of acrylic pendant designs.
These tools allow designers to visualize, modify, and perfect their designs down to the smallest detail.
They can test different design variations and materials without physically creating multiple prototypes.
This reduces waste and speeds up the design process, ensuring a higher level of accuracy in the final product.
2. High-Quality Laser Cutting
The precision of laser cutting cannot be overstated.
High-quality laser cutting machines equipped with advanced technology ensure that the designs are cut with exceptional accuracy.
These machines can handle complex patterns and fine details consistently, which manual cutting methods cannot achieve.
The clean cuts and smooth edges achieved by laser cutting enhance the pendant’s overall quality.
3. Quality Control and Inspection
Implementing stringent quality control measures throughout the manufacturing process ensures that each acrylic pendant meets high standards of precision and finish.
Quality control involves inspecting the cut pieces, checking the dimensions, and ensuring the surface is free of scratches or defects.
Automated inspection systems using cameras and sensors can quickly identify and rectify any inconsistencies, maintaining a uniform quality in the final products.
4. Use of CNC Machining
For more complex and detailed designs, CNC (Computer Numerical Control) machining offers enhanced precision.
CNC machines can execute detailed engraving, drilling, and shaping with high accuracy.
These machines follow the digital design created in CAD software, ensuring that each pendant matches the specified design precisely.
Using CNC technology minimizes human error and improves the overall precision and consistency of the pendants.
5. Advanced Finishing Techniques
Improving finishing techniques also contributes to the design precision of acrylic pendants.
Automated polishing machines ensure a consistent and high-quality finish on each piece.
In addition, advanced coating techniques like UV coating protect the pendant’s surface and enhance its appearance.
Even the application of colors and patterns has been refined with newer technologies like digital printing, which allows for high-resolution designs to be applied accurately.
Conclusion
Acrylic pendants’ manufacturing process is a blend of art and technology.
From the initial design to the final touches, each step requires precision and meticulous attention to detail.
The use of advanced technology like CAD software, laser cutting, and CNC machining has significantly improved the accuracy and quality of these pendants.
With continual advancements in materials and techniques, we can expect acrylic pendants to become even more intricate and beautifully crafted.
Whether for personal use or as a commercial product, these pendants showcase the perfect combination of creativity and precision engineering.
資料ダウンロード
QCD調達購買管理クラウド「newji」は、調達購買部門で必要なQCD管理全てを備えた、現場特化型兼クラウド型の今世紀最高の購買管理システムとなります。
ユーザー登録
調達購買業務の効率化だけでなく、システムを導入することで、コスト削減や製品・資材のステータス可視化のほか、属人化していた購買情報の共有化による内部不正防止や統制にも役立ちます。
NEWJI DX
製造業に特化したデジタルトランスフォーメーション(DX)の実現を目指す請負開発型のコンサルティングサービスです。AI、iPaaS、および先端の技術を駆使して、製造プロセスの効率化、業務効率化、チームワーク強化、コスト削減、品質向上を実現します。このサービスは、製造業の課題を深く理解し、それに対する最適なデジタルソリューションを提供することで、企業が持続的な成長とイノベーションを達成できるようサポートします。
オンライン講座
製造業、主に購買・調達部門にお勤めの方々に向けた情報を配信しております。
新任の方やベテランの方、管理職を対象とした幅広いコンテンツをご用意しております。
お問い合わせ
コストダウンが利益に直結する術だと理解していても、なかなか前に進めることができない状況。そんな時は、newjiのコストダウン自動化機能で大きく利益貢献しよう!
(Β版非公開)