- お役立ち記事
- Manufacturing Process of Acrylic Speaker Covers and Acoustic Performance Improvement
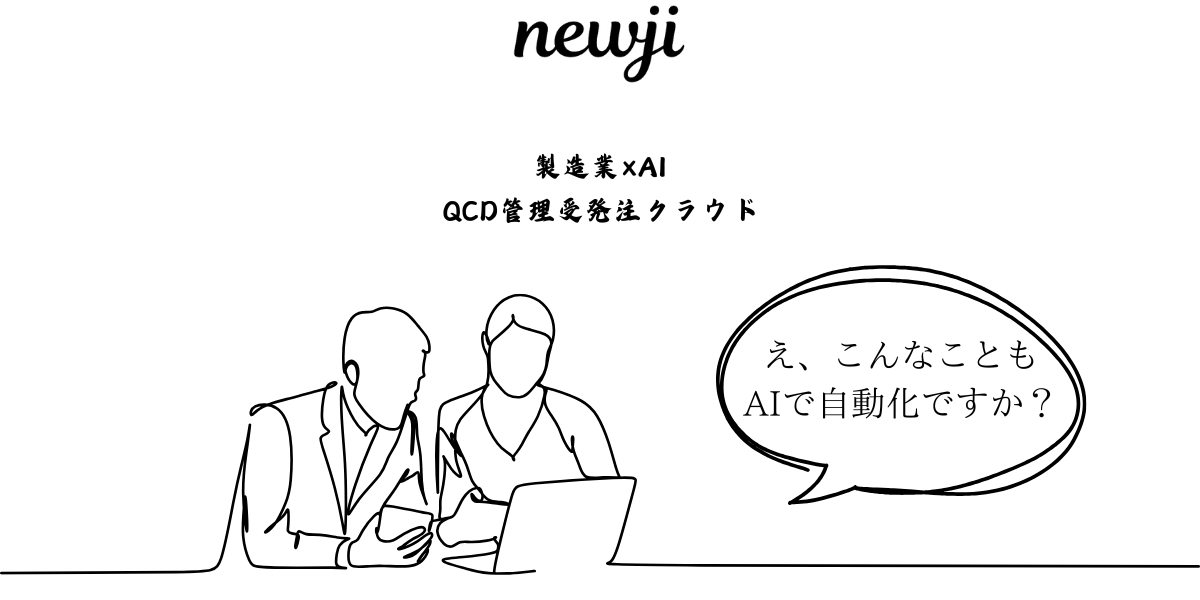
Manufacturing Process of Acrylic Speaker Covers and Acoustic Performance Improvement
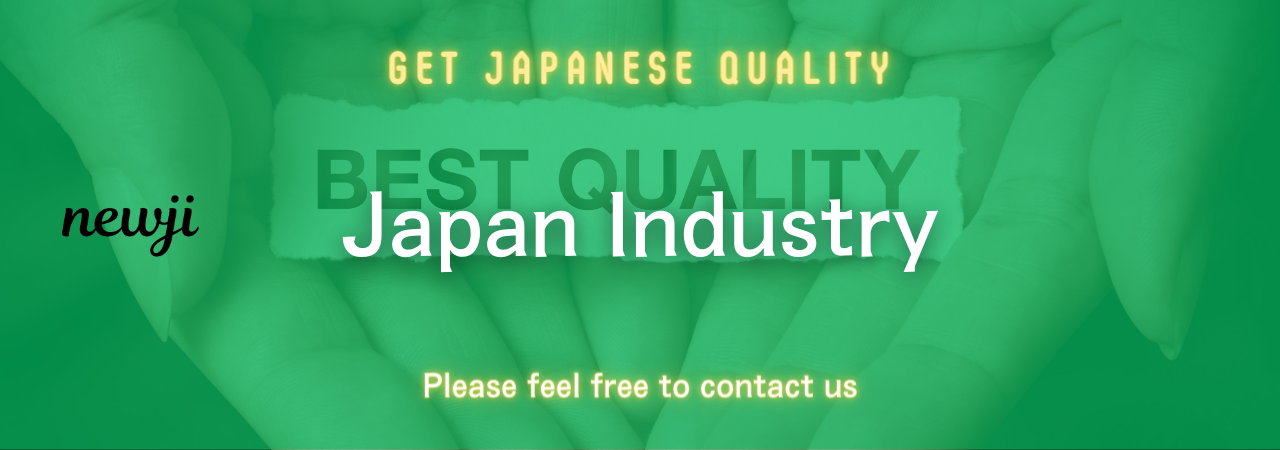
Acrylic speaker covers are increasingly popular due to their aesthetic appeal and acoustic benefits.
These covers protect the sensitive components of the speaker while also enhancing its sound quality.
In this article, we’ll delve into the manufacturing process of acrylic speaker covers and how they improve acoustic performance.
目次
Understanding Acrylic Material
Acrylic, also known as polymethyl methacrylate (PMMA), is a transparent thermoplastic often used as a lightweight or shatter-resistant alternative to glass.
It is chosen for speaker covers due to its clarity, strength, and versatility.
Acrylic is durable and can be easily shaped, making it an excellent choice for custom speaker designs.
Advantages of Acrylic
There are several reasons why acrylic is preferred for speaker covers.
First, its transparency allows users to see the speaker components, which can be appealing in modern and high-tech designs.
Second, acrylic has excellent acoustic properties, helping to minimize sound distortion.
Finally, it is resistant to UV light and weathering, making it suitable for both indoor and outdoor speakers.
Manufacturing Process of Acrylic Speaker Covers
The creation of acrylic speaker covers involves several precise steps.
Understanding these steps is crucial for ensuring high-quality end-products.
Material Selection and Preparation
The manufacturing process begins with selecting the right type of acrylic.
Not all acrylic sheets are the same; they come in varying thicknesses, colors, and grades.
For speaker covers, high-grade acrylic is preferred for its acoustic properties and durability.
Once selected, the acrylic sheets are cleaned to remove any dust or impurities. This ensures a flawless final product.
Cutting and Shaping
The next step is cutting and shaping the acrylic sheets into the desired form.
This is usually done using laser cutting technology, which provides precision and clean edges.
For complex designs, CNC (Computer Numerical Control) machining may be used.
This ensures that all cuts are precise, which is essential for both the aesthetic and functional aspects of the speaker cover.
Heat Forming
Heat forming is a crucial step in manufacturing acrylic speaker covers.
The cut acrylic sheets are heated until they become pliable.
Once they reach the right temperature, they are placed into molds to achieve the desired shape.
The forming process must be carefully controlled to avoid imperfections like bubbles or warping.
After forming, the acrylic is cooled to set its shape.
Polishing and Finishing
Once the acrylic speaker covers are formed, they undergo polishing and finishing to ensure a smooth, clear surface.
This often involves multiple stages of sanding and buffing.
The final product should be free from any scratches or defects.
Improving Acoustic Performance
Acrylic speaker covers aren’t just for show; they significantly impact the speaker’s acoustic performance.
Here’s how:
Minimized Distortion
Acrylic has excellent acoustic properties, including the ability to minimize distortion.
When sound waves pass through a well-designed acrylic cover, they do so with minimal interference.
This leads to clearer sound quality.
Improved Bass Response
The rigidity of acrylic materials helps in improving bass response.
Unlike some materials that may flex or distort under low-frequency sounds, acrylic remains stable.
This stability ensures that the bass sounds are accurately reproduced, enhancing overall audio performance.
Enhanced Durability
Durability plays a significant role in maintaining good acoustic performance over time.
Acrylic’s resistance to wear and tear means that the speaker cover remains in good condition for longer.
This consistency helps in maintaining high sound quality.
Conclusion
The manufacturing process of acrylic speaker covers involves several meticulous steps, from material selection to finishing touches.
Each stage is crucial in ensuring the final product is both aesthetically pleasing and acoustically beneficial.
By choosing acrylic for speaker covers, manufacturers and consumers alike can enjoy enhanced durability, improved sound quality, and a modern, transparent design.
Understanding this process helps appreciate the sophistication and effort that goes into producing high-quality audio equipment.
資料ダウンロード
QCD調達購買管理クラウド「newji」は、調達購買部門で必要なQCD管理全てを備えた、現場特化型兼クラウド型の今世紀最高の購買管理システムとなります。
ユーザー登録
調達購買業務の効率化だけでなく、システムを導入することで、コスト削減や製品・資材のステータス可視化のほか、属人化していた購買情報の共有化による内部不正防止や統制にも役立ちます。
NEWJI DX
製造業に特化したデジタルトランスフォーメーション(DX)の実現を目指す請負開発型のコンサルティングサービスです。AI、iPaaS、および先端の技術を駆使して、製造プロセスの効率化、業務効率化、チームワーク強化、コスト削減、品質向上を実現します。このサービスは、製造業の課題を深く理解し、それに対する最適なデジタルソリューションを提供することで、企業が持続的な成長とイノベーションを達成できるようサポートします。
オンライン講座
製造業、主に購買・調達部門にお勤めの方々に向けた情報を配信しております。
新任の方やベテランの方、管理職を対象とした幅広いコンテンツをご用意しております。
お問い合わせ
コストダウンが利益に直結する術だと理解していても、なかなか前に進めることができない状況。そんな時は、newjiのコストダウン自動化機能で大きく利益貢献しよう!
(Β版非公開)