- お役立ち記事
- Manufacturing Process of Acrylic Tables and Impact Resistance Improvement
Manufacturing Process of Acrylic Tables and Impact Resistance Improvement
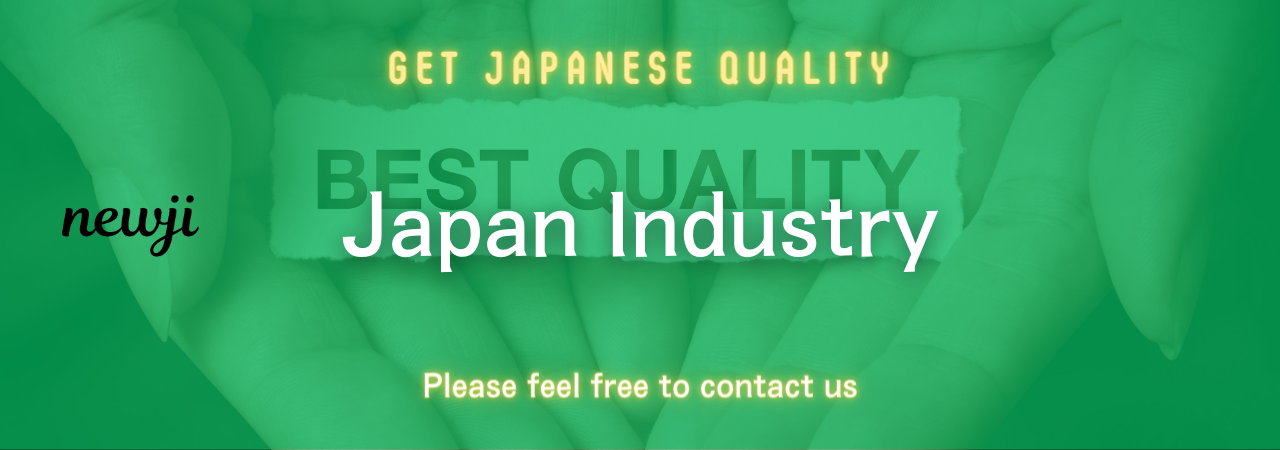
Acrylic tables have become increasingly popular for their sleek design and durability.
Understanding the manufacturing process behind these chic furnishings can offer insight into their resilience and aesthetic appeal.
Additionally, many are curious about how the impact resistance of these tables can be enhanced.
Here, we delve into the detailed stages of manufacturing acrylic tables, as well as how their impact resistance is improved.
目次
Materials and Preparation
The manufacturing process for acrylic tables begins with sourcing high-quality raw materials.
Acrylic, also known as polymethyl methacrylate (PMMA), is the primary component.
This material is appreciated for its transparency, strength, and lightweight properties.
After acquiring the raw material, it is essential to thoroughly cleanse it to eliminate any impurities that could compromise the quality.
Typically, the raw acrylic comes in pellet form.
These pellets undergo a drying process to ensure no moisture is present, as this can affect the final product’s clarity and strength.
Fabrication Techniques
One of the most common methods of fabricating acrylic tables is through casting.
During this process, the dried acrylic pellets are heated until they melt into a viscous liquid.
1. Sheet Casting
A popular method is sheet casting.
Here, the molten acrylic is poured into a mold and allowed to cool.
As it cools, it hardens into flat, transparent sheets.
These sheets are then subjected to additional processes, such as cutting and polishing, to achieve the desired shape and finish.
2. Cell Casting
Another technique is cell casting.
In this method, the melted acrylic is poured into a specially designed cell that dictates the table’s shape.
This allows for more intricate and varied designs compared to sheet casting.
Once the acrylic solidifies, it is carefully removed from the mold and prepared for further finishing operations.
Forming and Assembly
After casting, the acrylic sheets or formed pieces undergo a series of operations to create the final table.
1. Cutting
Precision cutting tools, such as laser cutters or CNC machines, are employed to trim the acrylic to the exact dimensions required.
This stage is crucial for ensuring that all parts fit perfectly during assembly.
2. Shaping
In this step, the acrylic pieces may be bent or formed using heat to achieve the desired curves and angles.
Heated acrylic becomes pliable, allowing manufacturers to mold it into various shapes.
Once shaped, it is cooled to retain the new form.
3. Polishing
Polishing is critical to achieving the characteristic shine and transparency of acrylic tables.
The edges are smoothed using mechanical polishers, and any surface imperfections are buffed out.
Specialized polishing compounds can enhance the finish and ensure a flawless appearance.
4. Bonding
The final step involves bonding all the individual parts together.
Industrial adhesives specifically designed for acrylic are used to ensure strong and invisible joints.
Careful application and curing ensure the assembled table is sturdy and aesthetically pleasing.
Improving Impact Resistance
While acrylic is inherently durable, its impact resistance can be further enhanced through several techniques.
1. Co-Polymerization
Incorporating other polymers during the production process can significantly enhance impact resistance.
This method involves blending acrylic with other materials to create a composite that retains acrylic’s clarity but offers superior strength.
2. Annealing
Annealing is a heat treatment process that involves gradually heating the acrylic and then allowing it to cool slowly.
This relieves internal stresses within the material, making it less prone to cracking and breaking under impact.
Annealed acrylic is considerably stronger and more durable.
3. Surface Treatments
Applying specialized coatings can protect acrylic surfaces from scratches and enhance their impact resistance.
These coatings create a hard, protective layer that can absorb and dissipate energy from impacts, thereby reducing the risk of damage.
4. Laminating
Laminating involves bonding multiple layers of acrylic together.
This multilayer structure can significantly improve impact resistance, as the energy from an impact is distributed across several layers, reducing the risk of cracking.
This technique also provides added flexibility in design.
Quality Control and Testing
Quality control is paramount in the manufacturing process to ensure the final product meets high standards.
Each acrylic table undergoes stringent testing to evaluate its strength, durability, and overall quality.
1. Visual Inspection
Inspectors examine the tables for any visible defects, such as bubbles, scratches, or uneven surfaces.
This step ensures that only flawless pieces move on to the next stage.
2. Impact Testing
Impact testing is conducted to assess the table’s ability to withstand forces.
Specialized equipment applies controlled impacts to the acrylic to determine its resistance.
Tables that pass this test are deemed suitable for use.
3. Load Testing
Load testing involves placing weights on the table to ensure it can support the specified load without deforming or breaking.
This test guarantees that the table will be functional and safe for everyday use.
Final Thoughts
The manufacturing process of acrylic tables is a complex and meticulous journey.
From selecting high-quality materials to applying innovative techniques for improving impact resistance, each stage is crucial in producing a durable, stylish end product.
Understanding these steps not only provides insight into the craftsmanship involved but also highlights the ingenuity in enhancing the performance of acrylic tables.
By employing advanced methods such as co-polymerization, annealing, surface treatments, and laminating, manufacturers can ensure that the acrylic tables not only look great but also stand up to everyday use with remarkable resilience.
資料ダウンロード
QCD調達購買管理クラウド「newji」は、調達購買部門で必要なQCD管理全てを備えた、現場特化型兼クラウド型の今世紀最高の購買管理システムとなります。
ユーザー登録
調達購買業務の効率化だけでなく、システムを導入することで、コスト削減や製品・資材のステータス可視化のほか、属人化していた購買情報の共有化による内部不正防止や統制にも役立ちます。
NEWJI DX
製造業に特化したデジタルトランスフォーメーション(DX)の実現を目指す請負開発型のコンサルティングサービスです。AI、iPaaS、および先端の技術を駆使して、製造プロセスの効率化、業務効率化、チームワーク強化、コスト削減、品質向上を実現します。このサービスは、製造業の課題を深く理解し、それに対する最適なデジタルソリューションを提供することで、企業が持続的な成長とイノベーションを達成できるようサポートします。
オンライン講座
製造業、主に購買・調達部門にお勤めの方々に向けた情報を配信しております。
新任の方やベテランの方、管理職を対象とした幅広いコンテンツをご用意しております。
お問い合わせ
コストダウンが利益に直結する術だと理解していても、なかなか前に進めることができない状況。そんな時は、newjiのコストダウン自動化機能で大きく利益貢献しよう!
(Β版非公開)