- お役立ち記事
- Manufacturing Process of Air Inlet Filters and Air Purity Improvement
月間76,176名の
製造業ご担当者様が閲覧しています*
*2025年3月31日現在のGoogle Analyticsのデータより
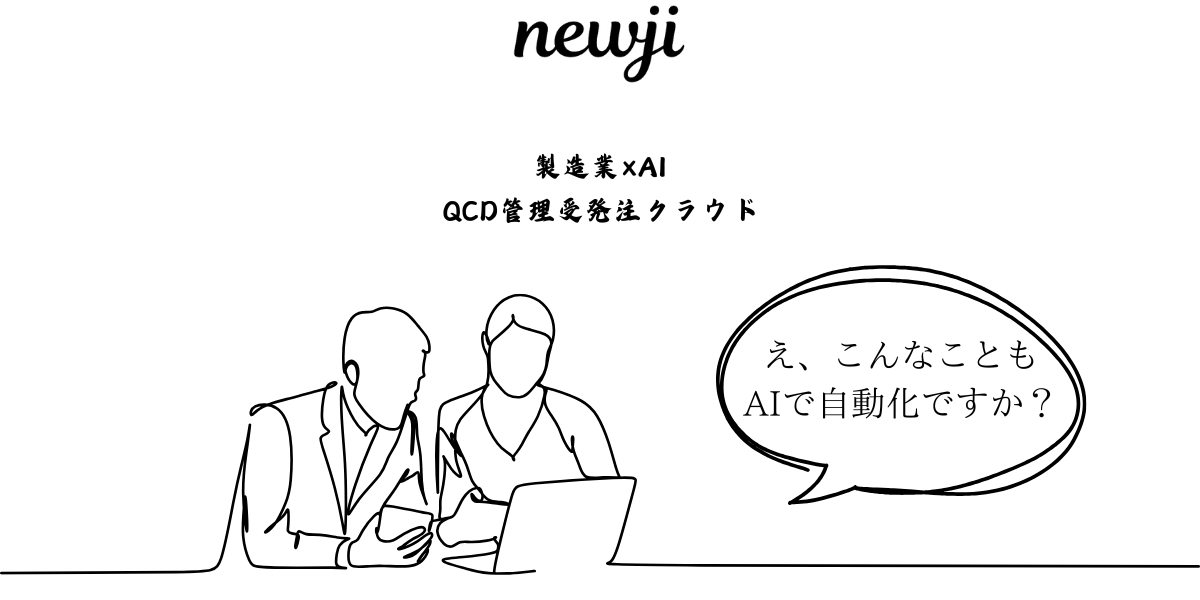
Manufacturing Process of Air Inlet Filters and Air Purity Improvement
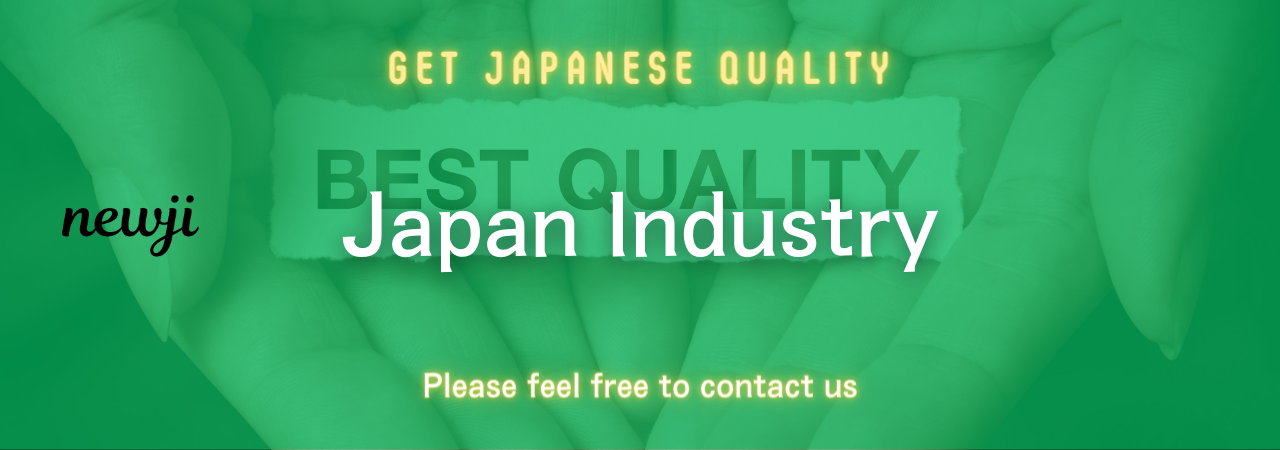
Air inlet filters play a crucial role in maintaining the purity of the air we breathe, enhancing the quality of indoor environments, and ensuring the health and safety of various industrial processes.
Understanding the manufacturing process of these filters and how they contribute to air purity can help both consumers and industry professionals make informed decisions.
目次
Introduction to Air Inlet Filters
Air inlet filters are designed to capture airborne particles, pollutants, and impurities that might otherwise enter a system or environment.
They are commonly used in HVAC systems, engines, and various industrial applications to ensure the air entering the system is clean and free from contaminants.
These filters are constructed from different materials and designed to meet specific standards based on their intended use.
Materials Used in Air Inlet Filters
The performance of an air inlet filter largely depends on the materials used in its construction.
Filter Media
The primary component of any filter is the filter media, which is the porous material that traps particles.
Common filter media include fiberglass, polyester, cellulose fibers, and synthetic materials.
Each type of media has its own advantages, such as high efficiency, durability, or specific functionalities like moisture resistance.
Support Structures
To provide stability and prevent the filter media from collapsing under airflow pressure, support structures made from wire mesh, plastic grids, or metal frames are used.
These structures ensure the filter maintains its shape and effectiveness over time.
Adhesives and Sealants
Adhesives and sealants are used to bond the filter media to the support structures and to seal any potential gaps where unfiltered air could bypass the media.
These materials must be resistant to environmental factors such as temperature variations and chemical exposure.
Steps in the Manufacturing Process
The production of air inlet filters involves several critical steps to ensure they meet quality and performance standards.
Design and Material Selection
The first step is designing the filter according to its intended application.
Engineers consider factors such as airflow rate, particle size, filtration efficiency, and environmental conditions.
Based on these requirements, suitable materials for the filter media, support structure, and adhesives are selected.
Cutting and Pleating
Once the materials are chosen, the filter media is cut into appropriate sizes.
For improved filtration efficiency and increased surface area, the media is often pleated.
Pleating involves folding the media in a zigzag pattern, creating more surface area to trap particles while maintaining a compact size.
Assembly and Bonding
The pleated filter media is then positioned within the support structure.
Adhesives and sealants are applied to bond the media to the frame and seal any potential bypass paths.
This step ensures the filter’s structural integrity and effectiveness.
Quality Control and Testing
Before reaching the market, air inlet filters undergo rigorous quality control and testing procedures.
These tests evaluate factors such as filtration efficiency, pressure drop, and durability under various conditions.
Only filters that meet industry standards and specifications are approved for sale.
Improving Air Purity with Air Inlet Filters
Air inlet filters significantly contribute to improving air purity in various settings.
Residential and Commercial HVAC Systems
In residential and commercial buildings, HVAC systems equipped with high-quality air inlet filters can significantly improve indoor air quality.
These filters capture dust, pollen, mold spores, and other airborne particles, reducing the risk of respiratory issues and allergies among occupants.
Industrial Applications
In industrial settings, air inlet filters are essential for protecting machinery and processes from contaminants.
For example, in manufacturing plants, filters prevent dust and debris from entering sensitive equipment, reducing the risk of malfunctions and ensuring product quality.
In cleanroom environments, air inlet filters are crucial for maintaining strict air purity standards required for sensitive processes such as electronics manufacturing and pharmaceutical production.
Automotive and Aerospace Industries
Air inlet filters are also vital in the automotive and aerospace industries, where they protect engines and other critical components from dust and debris.
This not only enhances the performance and lifespan of the equipment but also contributes to safety and reliability.
Advancements in Air Inlet Filter Technology
The field of air filtration is continually evolving, with ongoing research and development leading to new and improved filter technologies.
Nanofiber Technology
One of the significant advancements in recent years is the use of nanofiber technology in filter media.
Nanofibers, which are extremely fine fibers on the nanometer scale, offer superior filtration efficiency due to their high surface area and the ability to capture ultra-fine particles.
Electrostatic Filters
Electrostatic filters use static electricity to attract and capture particles, providing high-efficiency filtration without significantly restricting airflow.
These filters are particularly effective in capturing smaller particles that might bypass traditional filter media.
Sustainable and Recyclable Materials
With increasing attention on sustainability, manufacturers are exploring the use of eco-friendly and recyclable materials in filter production.
These materials not only reduce the environmental impact but also offer viable alternatives to traditional filter media.
Conclusion
Air inlet filters play a vital role in maintaining air purity, protecting both human health and valuable equipment.
Understanding the manufacturing process and the materials used can help consumers and industry professionals choose the right filters for their needs.
As technology advances, we can expect even more efficient and sustainable air filtration solutions to emerge, further enhancing air quality in various applications.
資料ダウンロード
QCD管理受発注クラウド「newji」は、受発注部門で必要なQCD管理全てを備えた、現場特化型兼クラウド型の今世紀最高の受発注管理システムとなります。
ユーザー登録
受発注業務の効率化だけでなく、システムを導入することで、コスト削減や製品・資材のステータス可視化のほか、属人化していた受発注情報の共有化による内部不正防止や統制にも役立ちます。
NEWJI DX
製造業に特化したデジタルトランスフォーメーション(DX)の実現を目指す請負開発型のコンサルティングサービスです。AI、iPaaS、および先端の技術を駆使して、製造プロセスの効率化、業務効率化、チームワーク強化、コスト削減、品質向上を実現します。このサービスは、製造業の課題を深く理解し、それに対する最適なデジタルソリューションを提供することで、企業が持続的な成長とイノベーションを達成できるようサポートします。
製造業ニュース解説
製造業、主に購買・調達部門にお勤めの方々に向けた情報を配信しております。
新任の方やベテランの方、管理職を対象とした幅広いコンテンツをご用意しております。
お問い合わせ
コストダウンが利益に直結する術だと理解していても、なかなか前に進めることができない状況。そんな時は、newjiのコストダウン自動化機能で大きく利益貢献しよう!
(β版非公開)