- お役立ち記事
- Manufacturing Process of Air Mixing Valves and Combustion Control Improvement
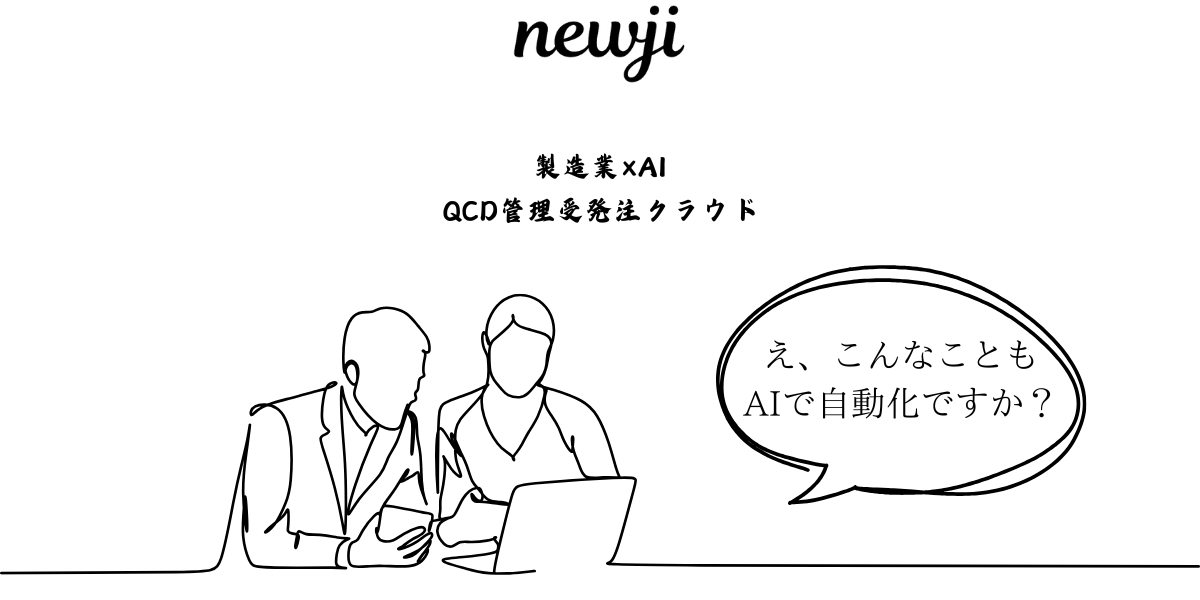
Manufacturing Process of Air Mixing Valves and Combustion Control Improvement
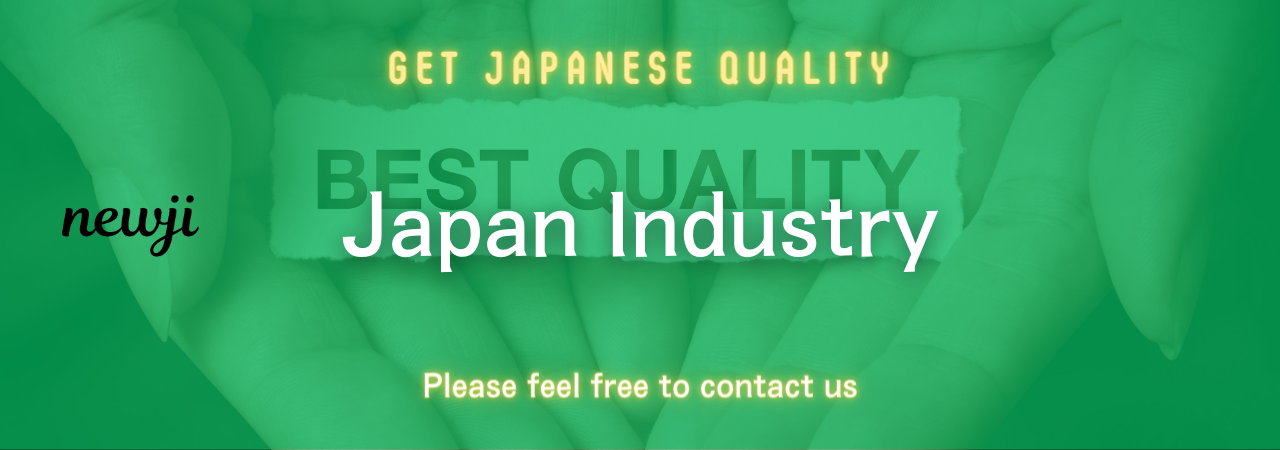
目次
Introduction
Air mixing valves play a crucial role in many industrial applications.
These valves regulate the mixture of air and fuel to optimize combustion processes.
Understanding their manufacturing process is essential for ensuring efficiency and effectiveness in various systems.
Equally important is improving combustion control, which enhances energy efficiency and reduces emissions.
Materials Used in Manufacturing Air Mixing Valves
The manufacturing of air mixing valves begins with selecting the right materials.
These valves must withstand high temperatures and pressures.
Common materials include stainless steel, brass, and alloys.
Stainless steel is preferred for its resistance to corrosion and high-temperature stability.
Brass is often used because of its excellent machinability and strength.
Specialized alloys are chosen for specific applications where unique properties are required.
Design and Engineering
Once the materials are selected, the design phase begins.
Engineers use CAD (Computer-Aided Design) software to create detailed blueprints of the valve.
These designs must account for all operational parameters, including pressure, temperature, and flow rate.
The goal is to ensure optimal air and fuel mixing while minimizing pressure drops and resistance.
Prototyping and Testing
Prototyping is the next step after finalizing the design.
A prototype is a working model of the valve, usually created through 3D printing or machining.
Testing is critical to verify the performance of the prototype.
Engineers conduct various tests, such as flow testing and pressure testing, to ensure that the valve meets all specifications.
This phase often involves multiple iterations of the prototype to refine the design.
Manufacturing Process
Machining
Machining is a crucial part of the manufacturing process.
Using CNC (Computer Numerical Control) machines, the valve parts are precisely cut and shaped.
This ensures that each component meets the exact design specifications.
Common machining processes include turning, milling, drilling, and grinding.
Assembly
After machining, the individual parts are assembled.
Assembly involves fitting together the machined components, such as the valve body, stem, and seals.
Precision is essential during this stage to ensure that the valve operates correctly.
Any misalignment can affect the valve’s performance and longevity.
Quality Control
Quality control is a vital aspect of manufacturing air mixing valves.
Inspection teams check each valve for defects and compliance with industry standards.
Common inspection methods include visual examination, dimensional checks, and pressure testing.
Only after passing rigorous quality checks is the valve approved for use.
Improving Combustion Control
Effective combustion control is critical for maximizing the performance of air mixing valves.
Improving this process involves several key factors.
Optimizing Air-Fuel Ratio
One of the most important aspects of combustion control is the air-fuel ratio.
An optimal air-fuel ratio ensures efficient combustion and minimizes emissions.
Advanced sensors and control systems are used to constantly monitor and adjust this ratio.
Advanced Control Systems
Modern control systems use sophisticated algorithms to optimize combustion.
These systems can quickly respond to changes in operating conditions.
They help maintain a stable and efficient combustion process.
Advanced control systems also include features like real-time monitoring and diagnostics.
Regular Maintenance
Regular maintenance is essential for keeping air mixing valves and combustion systems in top condition.
Maintenance routines include cleaning, inspection, and calibration.
Regular checks help identify potential issues before they become major problems.
Consistent maintenance ensures long-term reliability and performance.
Environmental Benefits
Improving the manufacturing process of air mixing valves and enhancing combustion control has significant environmental benefits.
Efficient combustion reduces fuel consumption, leading to lower greenhouse gas emissions.
High-quality air mixing valves also minimize pollutants released into the atmosphere.
These improvements contribute to a cleaner and more sustainable environment.
Conclusion
The manufacturing process of air mixing valves involves careful material selection, precise engineering, and rigorous quality control.
Implementing advanced control systems and regular maintenance can significantly improve combustion control.
These efforts result in enhanced efficiency, reliability, and environmental sustainability.
Understanding and optimizing these processes is essential for various industries to achieve their performance and sustainability goals.
資料ダウンロード
QCD調達購買管理クラウド「newji」は、調達購買部門で必要なQCD管理全てを備えた、現場特化型兼クラウド型の今世紀最高の購買管理システムとなります。
ユーザー登録
調達購買業務の効率化だけでなく、システムを導入することで、コスト削減や製品・資材のステータス可視化のほか、属人化していた購買情報の共有化による内部不正防止や統制にも役立ちます。
NEWJI DX
製造業に特化したデジタルトランスフォーメーション(DX)の実現を目指す請負開発型のコンサルティングサービスです。AI、iPaaS、および先端の技術を駆使して、製造プロセスの効率化、業務効率化、チームワーク強化、コスト削減、品質向上を実現します。このサービスは、製造業の課題を深く理解し、それに対する最適なデジタルソリューションを提供することで、企業が持続的な成長とイノベーションを達成できるようサポートします。
オンライン講座
製造業、主に購買・調達部門にお勤めの方々に向けた情報を配信しております。
新任の方やベテランの方、管理職を対象とした幅広いコンテンツをご用意しております。
お問い合わせ
コストダウンが利益に直結する術だと理解していても、なかなか前に進めることができない状況。そんな時は、newjiのコストダウン自動化機能で大きく利益貢献しよう!
(Β版非公開)