- お役立ち記事
- Manufacturing Process of Anti-freeze Heaters and Durability Reinforcement
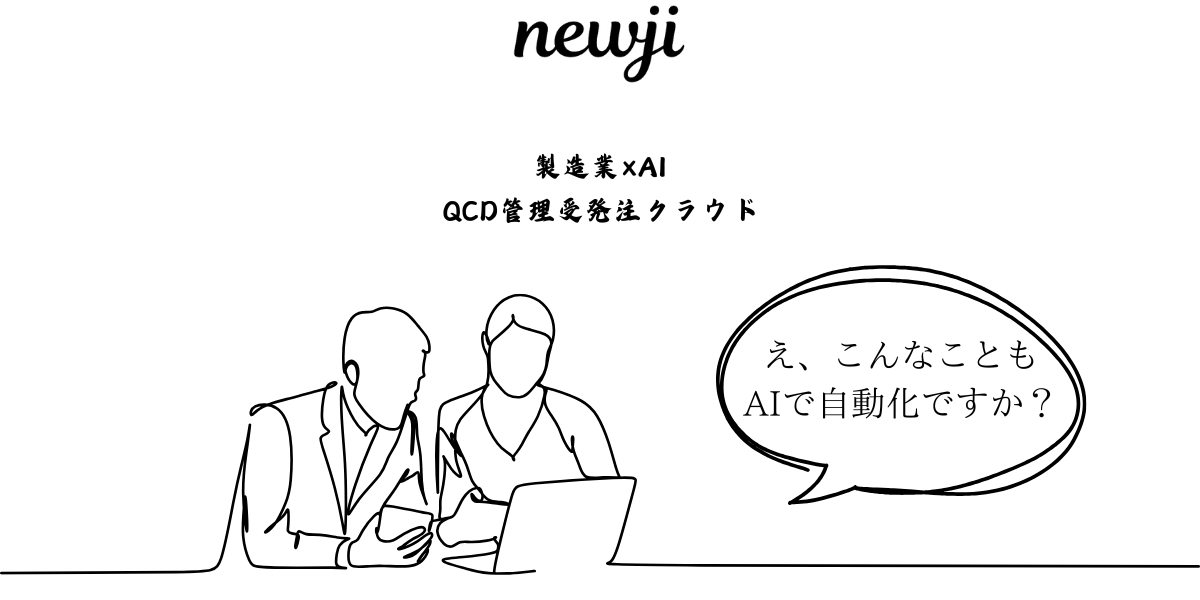
Manufacturing Process of Anti-freeze Heaters and Durability Reinforcement
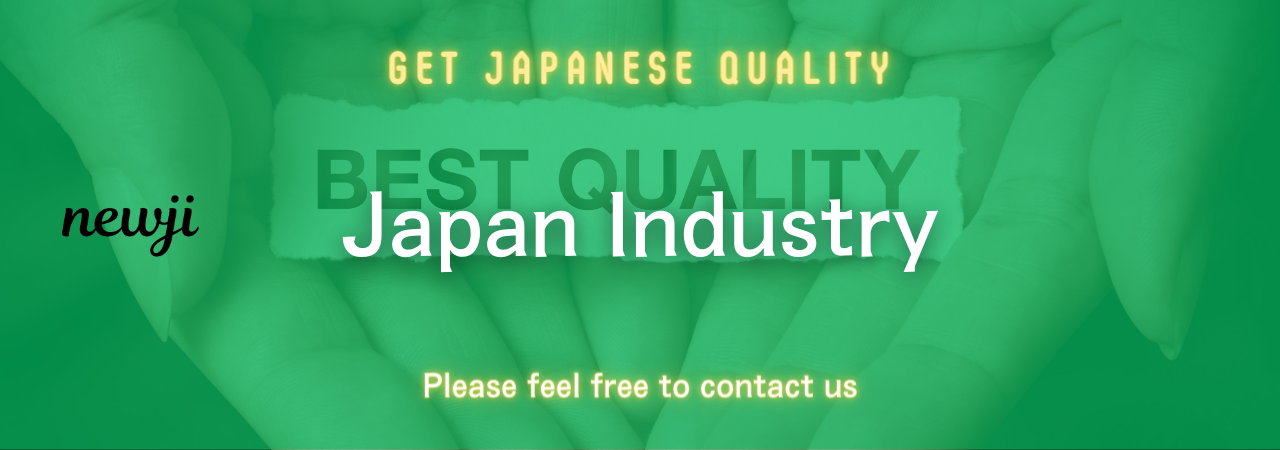
Anti-freeze heaters play a crucial role in various industries, particularly in cold climates and regions where freezing temperatures can disrupt operations and damage equipment.
Understanding how these heaters are manufactured and their durability reinforced ensures they perform effectively and have a long service life.
Let’s break down the process into a comprehensible guide.
目次
The Basics of Anti-freeze Heaters
Anti-freeze heaters are designed to prevent liquids from freezing in various systems.
They are commonly used in automotive engines, industrial pipes, and HVAC systems.
The primary function of these heaters is to maintain an optimal temperature, ensuring smooth operation even in cold conditions.
Materials Used in Anti-freeze Heaters
The materials used in manufacturing anti-freeze heaters are selected based on their thermal conductivity, durability, and resistance to corrosion.
Common materials include:
1. **Metals**: Copper and aluminum are frequently used due to their excellent thermal conductivity.
2. **Ceramics**: These materials are known for their high-temperature resistance and durability.
3. **Polymers**: Used in specific applications, polymers provide flexibility and insulation properties.
Design and Engineering
Designing anti-freeze heaters involves several critical steps to ensure efficiency and reliability.
These steps include:
1. **Thermal Analysis**: Engineers conduct thermal analysis to determine the necessary heat output and distribution required to prevent freezing.
2. **Custom Configuration**: Heaters are often custom-designed to fit specific equipment or system requirements.
3. **Safety Features**: Incorporating safety features like thermal cut-offs and temperature sensors to prevent overheating.
Manufacturing Process
The manufacturing process of anti-freeze heaters combines precision engineering with advanced manufacturing techniques.
Here’s a detailed look at the steps involved:
Step 1: Material Procurement
The first step is sourcing high-quality raw materials.
Metals, ceramics, and polymers are procured from trusted suppliers to ensure they meet industry standards and specifications.
Step 2: Component Fabrication
Once materials are procured, the next step is fabricating the individual components.
This process involves cutting, shaping, and forming the materials according to the design specifications.
For instance, metal sheets might be cut into specific shapes, while ceramics are molded and fired to achieve the desired hardness.
Step 3: Assembly
In the assembly phase, various components are meticulously put together.
This step may involve welding, soldering, or bonding different parts to create the heater element.
Attention to detail is critical here to ensure there are no gaps or misalignments that could affect performance.
Step 4: Electrical Integration
After assembly, the electrical components are integrated.
This includes installing heating elements, wiring, and control units.
Precision is vital to ensure that electrical connections are secure and capable of handling the required load.
Step 5: Testing and Quality Control
Thorough testing and quality control are essential to ensure the heaters meet performance and safety standards.
This step involves:
– **Thermal Testing**: Checking if the heater produces the expected heat output.
– **Electrical Testing**: Verifying that all electrical components function correctly.
– **Durability Testing**: Subjecting the heaters to conditions that simulate real-world usage to assess their durability.
Reinforcing Durability
Durability is a key factor in the performance of anti-freeze heaters.
Ensuring that these heaters can withstand harsh conditions and prolonged use is achieved through several reinforcement techniques.
Using High-Quality Materials
The foundation of durability is high-quality materials.
Using metals like stainless steel, which resists corrosion, and ceramics that withstand high temperatures, ensures a long service life.
Protective Coatings
Applying protective coatings to the heaters helps prevent corrosion and wear.
These coatings can significantly extend the life of the heaters, especially in harsh environments.
Advanced Welding Techniques
Advanced welding techniques contribute to the overall strength and durability of the heaters.
Techniques like TIG and MIG welding are used to ensure strong, reliable joints that can withstand high temperatures and pressures.
Regular Maintenance and Inspection
Even the most durable heaters benefit from regular maintenance and inspection.
Keeping the heaters clean, checking for any signs of wear or damage, and replacing any worn-out parts can prevent breakdowns and extend the heater’s lifespan.
Redundant Safety Features
Incorporating redundant safety features ensures that the heater operates safely even if one component fails.
This not only enhances safety but also contributes to the overall durability of the heater.
Importance of Anti-freeze Heaters
Anti-freeze heaters are indispensable in ensuring the smooth operation of various systems in cold climates.
From preventing engine block freezing in vehicles to ensuring the free flow of liquids in industrial pipelines, their role is critical.
Understanding their manufacturing process and the steps taken to reinforce durability highlights their importance and the technology behind their reliability.
Conclusion
In conclusion, the manufacturing process of anti-freeze heaters involves careful selection of materials, precise assembly, and meticulous testing.
Reinforcing their durability through high-quality materials, protective coatings, advanced welding techniques, and regular maintenance ensures they perform effectively and have a long service life.
These factors combined help anti-freeze heaters fulfill their vital role in various industries, keeping systems operational even in the harshest conditions.
資料ダウンロード
QCD調達購買管理クラウド「newji」は、調達購買部門で必要なQCD管理全てを備えた、現場特化型兼クラウド型の今世紀最高の購買管理システムとなります。
ユーザー登録
調達購買業務の効率化だけでなく、システムを導入することで、コスト削減や製品・資材のステータス可視化のほか、属人化していた購買情報の共有化による内部不正防止や統制にも役立ちます。
NEWJI DX
製造業に特化したデジタルトランスフォーメーション(DX)の実現を目指す請負開発型のコンサルティングサービスです。AI、iPaaS、および先端の技術を駆使して、製造プロセスの効率化、業務効率化、チームワーク強化、コスト削減、品質向上を実現します。このサービスは、製造業の課題を深く理解し、それに対する最適なデジタルソリューションを提供することで、企業が持続的な成長とイノベーションを達成できるようサポートします。
オンライン講座
製造業、主に購買・調達部門にお勤めの方々に向けた情報を配信しております。
新任の方やベテランの方、管理職を対象とした幅広いコンテンツをご用意しております。
お問い合わせ
コストダウンが利益に直結する術だと理解していても、なかなか前に進めることができない状況。そんな時は、newjiのコストダウン自動化機能で大きく利益貢献しよう!
(Β版非公開)