- お役立ち記事
- Manufacturing Process of Anti-freeze Heaters and Durability Reinforcement
月間76,176名の
製造業ご担当者様が閲覧しています*
*2025年3月31日現在のGoogle Analyticsのデータより
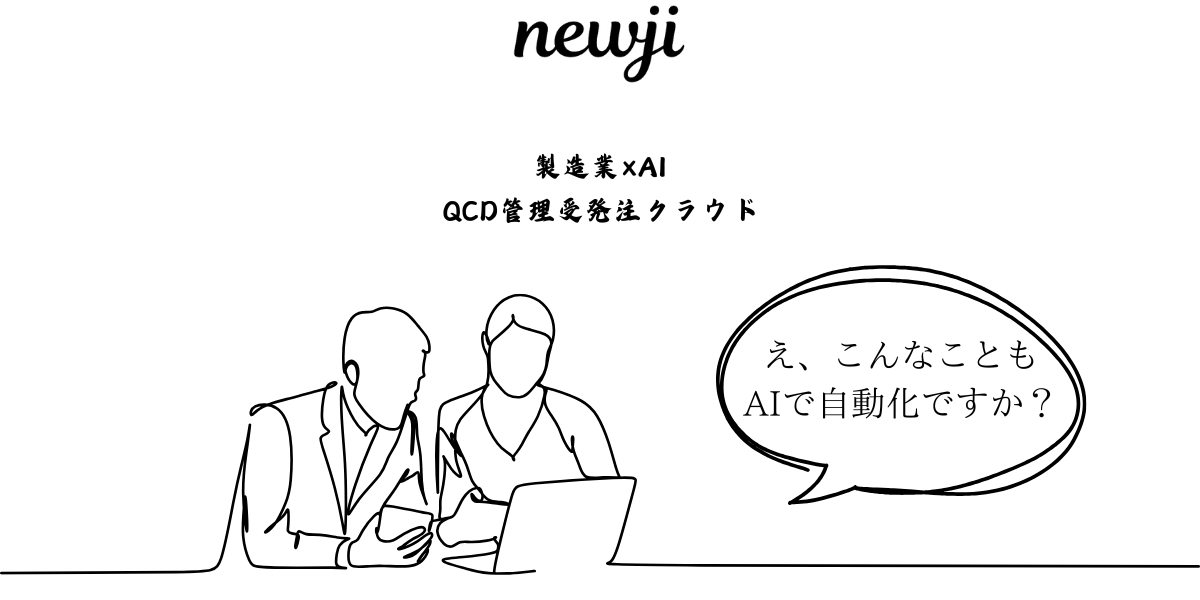
Manufacturing Process of Anti-freeze Heaters and Durability Reinforcement
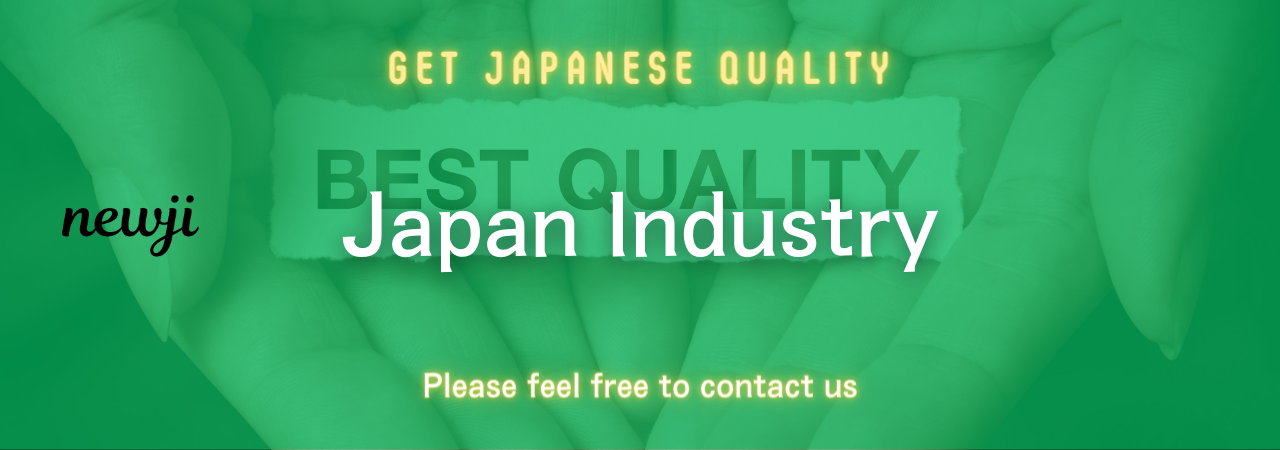
Understanding the manufacturing process and durability reinforcement of anti-freeze heaters requires us to delve into several key stages, each crucial for producing a reliable, efficient product.
These heaters play a vital role in preventing freezing in various systems, especially in colder climates.
Let’s break down the process step-by-step.
目次
Raw Material Selection
The first crucial step in manufacturing anti-freeze heaters is selecting appropriate raw materials.
High-quality materials ensure high performance and longevity.
Common materials include stainless steel, ceramic, and silicone rubber.
Stainless steel is chosen for its resistance to corrosion and its durability under extreme temperatures.
Ceramic also offers excellent thermal properties, while silicone rubber provides flexibility and resistance to harsh weather conditions.
Heating Elements
Selecting the right heating element is vital.
Nickel-chromium (NiCr) is often used due to its excellent electrical conductivity and heat resistance.
Mica, fiberglass, and ceramic cores are added to provide insulation and support for the heating elements.
These cores help to distribute heat evenly without compromising safety.
Design and Prototyping
Once materials are selected, the design phase begins.
Engineers and designers work together to create a blueprint that meets performance criteria and safety standards.
They use Computer-Aided Design (CAD) software to model the heater and simulate its performance under different conditions.
Prototyping follows, wherein a sample heater is produced based on the design blueprint.
This prototype undergoes rigorous testing to ensure it meets all specifications.
Adjustments may be made based on test results before proceeding to mass production.
Manufacturing Process
The manufacturing process encompasses several steps:
Cutting and Shaping
Initially, raw materials are cut and shaped according to the design specifications.
Precision cutting tools ensure that each component is accurate to size, which is critical for proper assembly.
Assembly
During the assembly phase, heating elements and insulation materials are inserted into the heater casing.
Automation often aids in assembling components with high precision.
Skilled technicians oversee the process to ensure quality control.
Welding and Bonding
Next, components are welded or bonded to form a solid structure.
Welding techniques used include TIG (Tungsten Inert Gas) welding, known for creating strong, clean welds.
Bonding agents are chosen for their durability and resistance to thermal stress.
Coating and Protection
Anti-freeze heaters are exposed to harsh conditions, so applying protective coatings are essential.
A corrosion-resistant coating is typically applied to the external surfaces.
This coating can be a combination of chemicals that prevent rust and decay, ensuring a longer lifespan for the heater.
Insulation and Encapsulation
To further protect the internal components, the heater is insulated with materials like silicone rubber.
Encapsulation helps in sealing the elements and prevents any moisture ingress, which could potentially cause short circuits or other failures.
This step is crucial for ensuring the heater’s reliability and effectiveness.
Durability Reinforcement
Enhancing the durability of anti-freeze heaters involves several techniques and technologies:
Materials Treatment
Materials may undergo various treatments to enhance their strength and thermal resistance.
Heat treatments, like annealing, improve the metal’s toughness and resistance to extreme temperatures.
Coating with anti-corrosive substances extends the lifespan of the metal components.
Structural Enhancements
Reinforcing the heater structure involves adding support elements that can withstand physical stresses.
Using a double-layered design or reinforcing certain areas with stronger materials can prevent deformation.
Such structural enhancements are vital for heaters that are used in harsh environments.
Failure Testing
Durability testing plays a significant role in ensuring product reliability.
Heaters are subjected to various stress tests, including thermal cycling, which involves repeatedly heating and cooling the device.
This process helps identify potential failure points and ensures the heater can endure continuous use under extreme conditions.
Quality Control and Testing
Quality control is a multi-step process applied throughout manufacturing to ensure each heater meets safety and performance standards.
Initial Inspections
Components are inspected for defects before assembly.
Any defective parts are discarded to prevent compromising the final product’s quality.
In-Process Testing
During assembly, various in-process tests, such as electrical resistance tests and insulation resistance tests, are conducted to ensure each part meets required specifications.
Final Testing
The final product undergoes rigorous testing, including high-voltage tests and operational testing at low temperatures.
These tests ensure the heater operates correctly and safely before it is packaged and shipped.
Environmental Considerations
Manufacturers must consider environmental impacts during production.
Using eco-friendly materials and processes can reduce the environmental footprint.
Recycling waste products and minimizing energy consumption are part of sustainable manufacturing practices.
Compliance with Regulations
Adhering to environmental regulations ensures that manufacturing practices do not harm the environment.
Following guidelines from regulatory bodies helps maintain industry standards and promotes sustainable development.
Conclusion
The manufacturing process of anti-freeze heaters is intricate, requiring careful selection of materials, precise design, and rigorous testing.
By focusing on durability reinforcement through material treatment, structural enhancements, and thorough testing, manufacturers ensure a reliable, high-performing product.
The combined efforts in each step not only enhance the heater’s efficiency but also extend its operational life, making it a valuable asset in cold weather conditions.
資料ダウンロード
QCD管理受発注クラウド「newji」は、受発注部門で必要なQCD管理全てを備えた、現場特化型兼クラウド型の今世紀最高の受発注管理システムとなります。
ユーザー登録
受発注業務の効率化だけでなく、システムを導入することで、コスト削減や製品・資材のステータス可視化のほか、属人化していた受発注情報の共有化による内部不正防止や統制にも役立ちます。
NEWJI DX
製造業に特化したデジタルトランスフォーメーション(DX)の実現を目指す請負開発型のコンサルティングサービスです。AI、iPaaS、および先端の技術を駆使して、製造プロセスの効率化、業務効率化、チームワーク強化、コスト削減、品質向上を実現します。このサービスは、製造業の課題を深く理解し、それに対する最適なデジタルソリューションを提供することで、企業が持続的な成長とイノベーションを達成できるようサポートします。
製造業ニュース解説
製造業、主に購買・調達部門にお勤めの方々に向けた情報を配信しております。
新任の方やベテランの方、管理職を対象とした幅広いコンテンツをご用意しております。
お問い合わせ
コストダウンが利益に直結する術だと理解していても、なかなか前に進めることができない状況。そんな時は、newjiのコストダウン自動化機能で大きく利益貢献しよう!
(β版非公開)