- お役立ち記事
- Manufacturing Process of Automatic Battery Chargers and Improvement in Charging Efficiency
月間76,176名の
製造業ご担当者様が閲覧しています*
*2025年3月31日現在のGoogle Analyticsのデータより
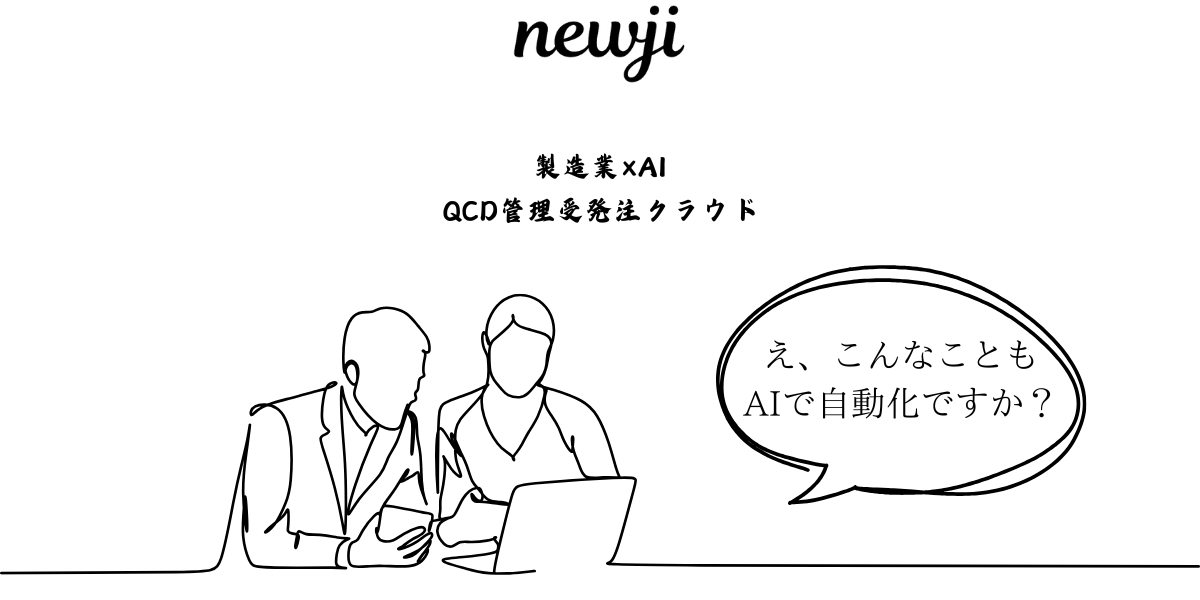
Manufacturing Process of Automatic Battery Chargers and Improvement in Charging Efficiency
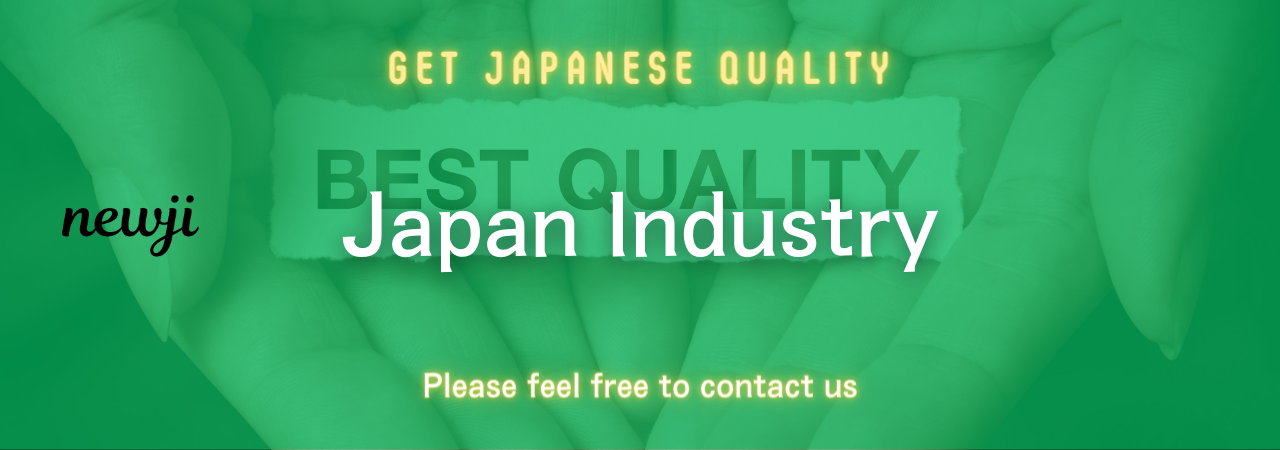
Automatic battery chargers are an essential component in various industries, ensuring efficient and reliable power supply for numerous electronic devices and machinery. The manufacturing process of these chargers is a complex journey involving intricate designs, precision engineering, and advanced technologies. Improving charging efficiency is a critical aspect that manufacturers continuously strive towards. This article delves into the manufacturing process of automatic battery chargers and explores ways to enhance their charging efficiency.
目次
Design and Planning
The manufacturing process begins with the design and planning phase. Engineers and designers collaborate to conceptualize a charger that meets specific requirements and standards. This phase involves creating detailed schematics and blueprints that outline the physical and electronic components of the charger.
During this stage, significant attention is given to the charger’s power capacity, input voltage range, output specifications, safety features, and environmental impact. Designers also determine the charger’s size, weight, and overall aesthetics.
Component Selection
Once the design is finalized, the next step is selecting the appropriate components. High-quality semiconductors, transformers, capacitors, resistors, and microcontrollers are chosen based on the design specifications.
Suppliers are carefully vetted to ensure that components meet the necessary quality and performance standards. It’s essential to select components that can handle high temperatures, resist wear and tear, and offer reliable performance over extended periods.
Prototyping
With the components in place, the next phase is prototyping. This involves creating a working model of the charger to test its design and functionality. Engineers assemble the prototype, integrating all the selected components and adhering to the design specifications.
The prototype is subjected to rigorous testing, including electrical, thermal, and mechanical assessments. These tests identify potential flaws and ensure that the charger meets safety and performance standards. Any issues discovered during this phase are addressed, and necessary modifications are made to the design.
Testing and Validation
The testing and validation phase is crucial in the manufacturing process. The prototype undergoes extensive testing to validate its performance, efficiency, and safety features. Tests include load testing, where the charger is evaluated under various electrical loads, and environmental testing, which assesses performance under different temperature and humidity conditions.
Safety tests also play a significant role. The charger is tested for short circuits, overvoltage, and overheating to ensure it incorporates effective protective measures. Once the charger passes all tests, it is deemed ready for mass production.
Mass Production
Mass production begins with the fabrication of printed circuit boards (PCBs). The PCBs are essential for housing the electronic components and establishing electrical connections. Automated machines precisely place and solder components onto the PCBs, ensuring consistency and accuracy.
Next, the assembled PCBs undergo quality control checks to detect any defects. Once cleared, the PCBs are integrated into the charger’s housing. The housing is typically made of durable materials like plastic or metal, offering protection and durability.
Assembly and Integration
Assembly involves combining all the individual components, such as the transformer, capacitors, and microcontrollers, into a unified charger. This step requires precision and attention to detail to ensure that every component is correctly aligned and connected.
During integration, software is uploaded to the charger’s microcontroller. This software manages the charging process, ensuring efficient power delivery and safety mechanisms. The integrated charger undergoes final testing to verify its functionality and performance.
Quality Control and Inspection
Quality control is an ongoing process throughout manufacturing. Even in the final stages, chargers are subjected to thorough inspections and tests. Visual inspections check for physical defects, while electrical tests ensure that the charger operates within specified parameters.
Quality control teams also conduct random sampling tests, where a batch of chargers is selected and tested to ensure consistency in quality and performance. Any defects or issues identified are addressed immediately, and corrective measures are implemented.
Packaging and Shipping
Once the chargers pass all quality checks, they are ready for packaging. Packaging involves securely placing the chargers in protective boxes, often with manuals and accessories. The packaging is designed to prevent damage during transit and ensure the charger arrives in perfect condition.
The packaged chargers are then shipped to distributors, retailers, or directly to customers. Throughout shipping, logistics teams monitor the process to ensure timely and safe delivery.
Improving Charging Efficiency
Charging efficiency is a critical aspect of automatic battery chargers. Manufacturers continually seek ways to enhance efficiency to reduce energy consumption and extend battery life. Here are some methods employed:
Advanced Algorithms
Implementing advanced charging algorithms is one way to improve efficiency. These algorithms precisely control the charging process, adjusting the current and voltage to optimize battery health and charging speed. Smart algorithms reduce overcharging and overheating risks, enhancing overall efficiency.
High-Quality Components
Using high-quality components, such as low-resistance connectors and efficient transformers, reduces energy loss during the charging process. Quality components ensure better performance and longevity, contributing to higher efficiency.
Thermal Management
Effective thermal management is vital for maintaining efficiency. Advanced chargers incorporate heat sinks, cooling fans, and thermal sensors to manage temperatures. Keeping components cool reduces energy loss and enhances charger performance.
Wireless Charging Technology
Innovations in wireless charging technology have led to significant efficiency improvements. Resonant inductive coupling and other techniques minimize energy loss during wireless power transfer, making the process more efficient and convenient.
Firmware Updates
Regular firmware updates ensure that chargers continue to operate at peak efficiency. Manufacturers provide updates to enhance performance, add new features, and address any discovered issues. Maintaining up-to-date firmware optimizes the charging process and efficiency.
In conclusion, the manufacturing process of automatic battery chargers is a meticulous and complex procedure, involving multiple stages from design to quality control. Improving charging efficiency remains a focal point for manufacturers, driven by advancements in technology and innovative approaches. Through continuous efforts and dedication, the future of automatic battery chargers looks promising, offering enhanced performance and reliability to consumers worldwide.
資料ダウンロード
QCD管理受発注クラウド「newji」は、受発注部門で必要なQCD管理全てを備えた、現場特化型兼クラウド型の今世紀最高の受発注管理システムとなります。
ユーザー登録
受発注業務の効率化だけでなく、システムを導入することで、コスト削減や製品・資材のステータス可視化のほか、属人化していた受発注情報の共有化による内部不正防止や統制にも役立ちます。
NEWJI DX
製造業に特化したデジタルトランスフォーメーション(DX)の実現を目指す請負開発型のコンサルティングサービスです。AI、iPaaS、および先端の技術を駆使して、製造プロセスの効率化、業務効率化、チームワーク強化、コスト削減、品質向上を実現します。このサービスは、製造業の課題を深く理解し、それに対する最適なデジタルソリューションを提供することで、企業が持続的な成長とイノベーションを達成できるようサポートします。
製造業ニュース解説
製造業、主に購買・調達部門にお勤めの方々に向けた情報を配信しております。
新任の方やベテランの方、管理職を対象とした幅広いコンテンツをご用意しております。
お問い合わせ
コストダウンが利益に直結する術だと理解していても、なかなか前に進めることができない状況。そんな時は、newjiのコストダウン自動化機能で大きく利益貢献しよう!
(β版非公開)