- お役立ち記事
- Manufacturing Process of Automatic Cup Warmers and Improvement in Heating Technology
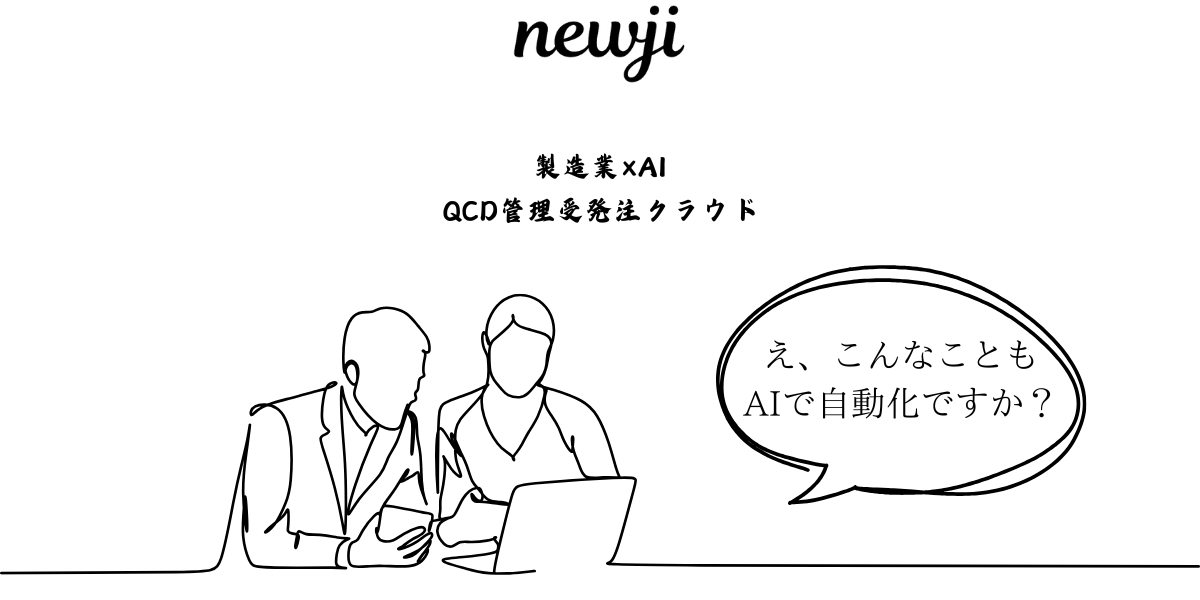
Manufacturing Process of Automatic Cup Warmers and Improvement in Heating Technology
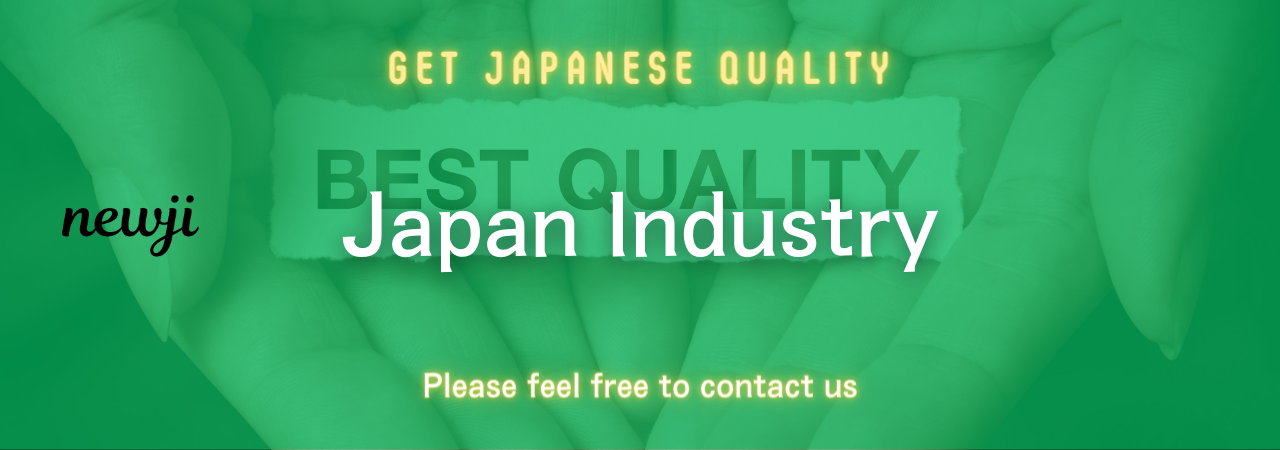
Automatic cup warmers have revolutionized how we enjoy our hot beverages, ensuring they stay at the perfect temperature for longer periods.
Knowing the step-by-step manufacturing process and understanding the constant improvements in heating technology can provide valuable insight into this everyday convenience.
This article delves into how these marvelous gadgets are made and the advancements that make them more efficient than ever before.
目次
Design and Concept Phase
Before production begins, the design and engineering teams work closely to conceptualize the automatic cup warmer.
They consider various factors such as size, shape, power consumption, and heating efficiency.
The design must be both visually appealing and practical.
Sketches and 3D models are created to fine-tune the aesthetics and functionality of the product.
Material Selection
Choosing the right materials is crucial for manufacturing a durable and efficient automatic cup warmer.
High-quality plastics and metals are typically selected for their heat resistance and durability.
Silicone or rubber components may be added for better grip and insulation.
Prototyping
Once the design is finalized, a prototype is created.
This prototype is rigorously tested for performance, safety, and durability.
It helps the engineers identify potential problems and make necessary adjustments before mass production.
Performance tests ensure that the warmer can maintain a consistent temperature without overheating or posing any safety risks.
Heating Mechanism
Electrical Coils and Conductors
One of the core components of an automatic cup warmer is its heating mechanism.
Most commonly, electrical coils or conductive materials are used to generate heat.
These are made of materials like nichrome, a nickel-chromium alloy known for its ability to withstand high temperatures.
Temperature Control
Maintaining a consistent temperature is vital for an automatic cup warmer.
Advanced models come with built-in temperature sensors and control units.
These components monitor the temperature and adjust the power output to avoid overheating.
Thermostats or microcontrollers are commonly used for this purpose.
Manufacturing Process
Injection Molding
The body and casing of the automatic cup warmer are generally made using an injection molding process.
This technique involves injecting molten plastic or metal into a mold to form the desired shape.
After cooling and solidifying, the molded parts are removed and cleaned.
Assembly
Once the individual components are prepared, they are carefully assembled.
The heating coils, temperature sensors, and electrical circuits are placed inside the casing.
Wires are soldered to connect various components, ensuring that the device functions correctly.
Quality checks are performed at different stages to ensure everything is in perfect working order.
Quality Assurance
Quality assurance is a critical step in the manufacturing process.
Every unit undergoes rigorous testing to ensure it meets safety standards and performs as expected.
Any defects are identified and rectified to maintain high product standards.
Advancements in Heating Technology
Energy Efficiency
One of the significant improvements in automatic cup warmers is energy efficiency.
Newer models consume less power while providing the same level of heating.
This enhancement is achieved by using advanced materials and better design principles.
Energy-efficient models are not only cost-effective but also environmentally friendly.
Smart Features
Modern automatic cup warmers come equipped with smart features that make them more user-friendly.
Bluetooth connectivity, mobile apps, and voice control are some of the innovations that have been integrated.
These features allow users to control the warmer remotely, set specific temperatures, and even receive notifications.
Safety Enhancements
Safety is always a priority when it comes to electrical appliances.
Newer cup warmers have built-in safety mechanisms such as auto shut-off, tip-over protection, and child safety locks.
These enhancements minimize the risk of accidents and provide peace of mind to users.
Future Trends
Eco-Friendly Materials
As sustainability becomes increasingly important, manufacturers are exploring the use of eco-friendly materials.
Biodegradable plastics and recycled metals are being considered for future models.
These materials reduce the environmental impact and appeal to eco-conscious consumers.
AI Integration
Artificial intelligence is gradually making its way into everyday gadgets, including automatic cup warmers.
Future models may use AI to learn user preferences and adjust the temperature accordingly.
This personalized heating experience ensures that your beverage is always at the perfect temperature.
Understanding the manufacturing process and continuous improvements in technology gives us a newfound appreciation for the automatic cup warmer.
These advancements not only make our lives more convenient but also contribute to a more sustainable and efficient future.
資料ダウンロード
QCD調達購買管理クラウド「newji」は、調達購買部門で必要なQCD管理全てを備えた、現場特化型兼クラウド型の今世紀最高の購買管理システムとなります。
ユーザー登録
調達購買業務の効率化だけでなく、システムを導入することで、コスト削減や製品・資材のステータス可視化のほか、属人化していた購買情報の共有化による内部不正防止や統制にも役立ちます。
NEWJI DX
製造業に特化したデジタルトランスフォーメーション(DX)の実現を目指す請負開発型のコンサルティングサービスです。AI、iPaaS、および先端の技術を駆使して、製造プロセスの効率化、業務効率化、チームワーク強化、コスト削減、品質向上を実現します。このサービスは、製造業の課題を深く理解し、それに対する最適なデジタルソリューションを提供することで、企業が持続的な成長とイノベーションを達成できるようサポートします。
オンライン講座
製造業、主に購買・調達部門にお勤めの方々に向けた情報を配信しております。
新任の方やベテランの方、管理職を対象とした幅広いコンテンツをご用意しております。
お問い合わせ
コストダウンが利益に直結する術だと理解していても、なかなか前に進めることができない状況。そんな時は、newjiのコストダウン自動化機能で大きく利益貢献しよう!
(Β版非公開)