- お役立ち記事
- Manufacturing Process of Automatic Foldable Helmets and Enhancement of Impact Absorption Technology
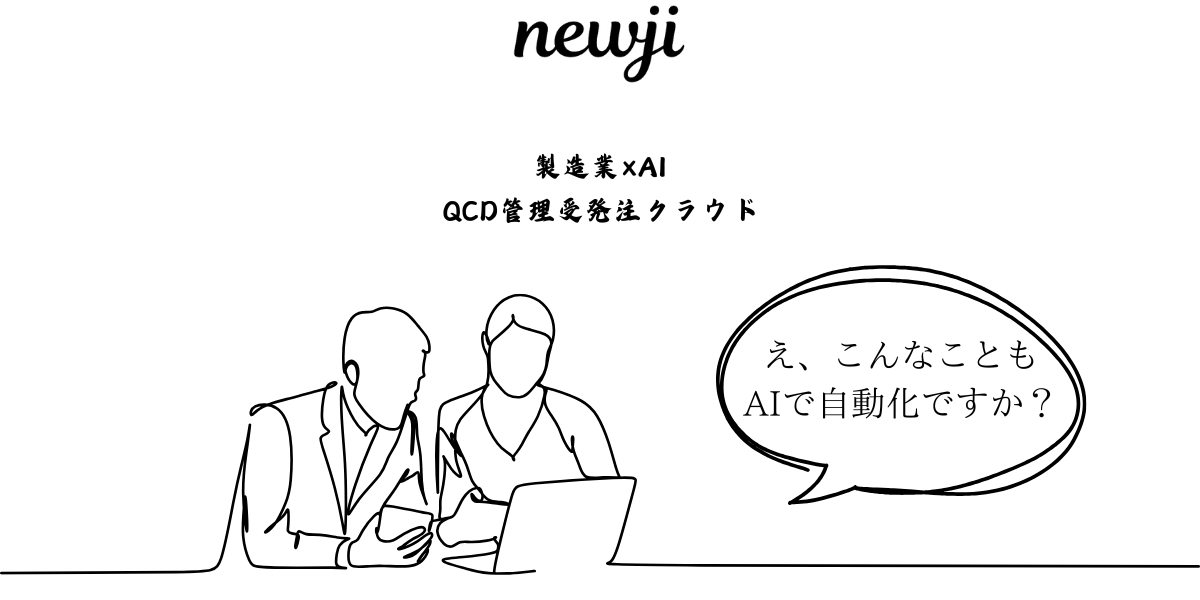
Manufacturing Process of Automatic Foldable Helmets and Enhancement of Impact Absorption Technology
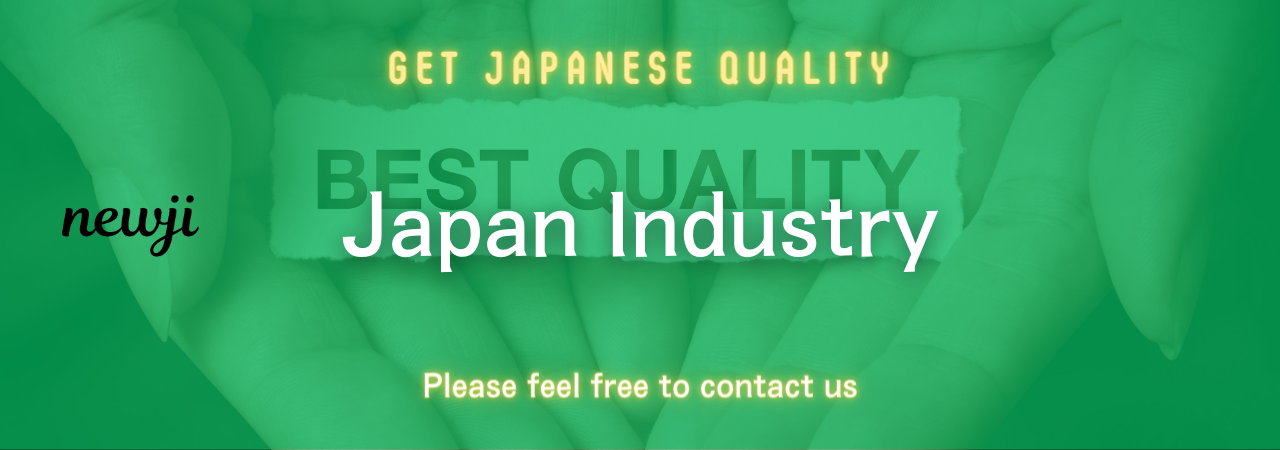
目次
The Importance of Automatic Foldable Helmets
In recent years, the demand for automatic foldable helmets has surged significantly.
This innovation addresses the concerns of convenience and safety for cyclists and motorcyclists alike.
A foldable helmet offers the practicality of easy storage and portability, while automatic mechanisms further enhance user experience by making the transformation process effortless.
Design Considerations
Compact and Efficient
Designing an automatic foldable helmet begins with prioritizing compactness and efficiency.
Engineers focus on creating a helmet that transforms easily while maintaining a sturdy construction.
Lightweight materials, such as polycarbonate or specialized polymers, are often used to ensure the helmet remains light yet resilient.
Safety Standards
Safety is paramount in helmet design.
Automatic foldable helmets must meet or exceed industry safety standards.
This includes rigorous testing for impact resistance, puncture resistance, and stability.
Manufacturers often employ advanced technology and materials to enhance the protective qualities of these helmets.
The Manufacturing Process
The creation of automatic foldable helmets involves several intricate steps.
Material Selection
The first step in the manufacturing process is choosing the right materials.
High-quality foam for impact absorption and durable outer shells made from specialized plastics or carbon fiber composites are commonly selected.
These materials must balance weight and strength to ensure both comfort and protection.
Shell Manufacturing
Once materials are selected, the outer shell of the helmet is crafted.
Typically, the process involves injection molding, where molten material is poured into a mold to create the helmet shape.
This method allows for precision and consistency in production.
Interior Construction
The interior of the helmet is equally critical.
High-density foam or similar materials are cut and shaped to fit snugly inside the outer shell.
This foam layer is crucial for absorbing impact energy and cushioning the wearer’s head.
Automatic Mechanism Integration
The defining feature of these helmets is their automatic-folding capability.
To achieve this, specialized mechanisms are integrated during the assembly process.
These mechanisms usually involve a combination of springs, hinges, and locking systems that allow the helmet to fold and unfold smoothly.
Engineers pay close attention to ensure these mechanisms do not compromise the helmet’s structural integrity.
Assembly and Quality Control
After the separate components are ready, the assembly process begins.
Each helmet undergoes a meticulous assembly process where all parts are securely fitted together.
To certify their quality, helmets are subjected to multiple inspections and tests.
This includes impact testing, durability testing, and functionality testing to ensure the folding mechanism operates correctly.
Enhancing Impact Absorption Technology
One of the critical aspects of helmet design is its ability to absorb impact and protect the wearer in case of an accident.
Recent advancements in technology have paved the way for significant improvements in this field.
Multi-Density Foam
Traditional helmets often use a single type of foam for impact absorption.
However, modern automatic foldable helmets incorporate multi-density foam.
This involves layers of foam with varying densities that work together to dissipate impact energy more effectively.
As a result, the helmet provides superior protection against different levels of force.
Fluid Technologies
Another innovative technology is the incorporation of fluid-filled bladders within the helmet.
These bladders act as shock absorbers, further dissipating impact energy.
The fluid moves within the bladders, effectively neutralizing the force before it reaches the wearer’s head.
Smart Helmets
The integration of smart technologies is revolutionizing helmet design.
Some automatic foldable helmets now come equipped with sensors that can detect impacts and provide real-time data to users.
These sensors can even send alerts to emergency services in the event of a significant impact.
This technology enhances safety and offers an added layer of protection.
Custom Fit Technology
Creating a custom fit is essential for maximizing the protective qualities of a helmet.
Advanced manufacturing techniques now allow for personalized fit adjustments.
These can include adjustable padding, flexible shells, and even 3D-printed components tailored to the wearer’s head shape.
Environmental Impact
As with any product, the environmental impact of manufacturing automatic foldable helmets is an important consideration.
Many manufacturers are striving to make the process more sustainable.
Eco-Friendly Materials
Manufacturers are increasingly turning to eco-friendly materials.
Biodegradable plastics and recyclable components are being used to create safer, more sustainable helmets.
This initiative reduces waste and minimizes the environmental footprint.
Energy Efficiency
Energy-efficient manufacturing processes are also being adopted.
From energy-saving machinery to streamlined production methods, every effort is made to reduce the energy consumption involved in manufacturing these helmets.
The Future of Automatic Foldable Helmets
The future of automatic foldable helmets looks promising.
As technology continues to advance, we can expect further enhancements in safety, convenience, and sustainability.
Innovations in materials and manufacturing processes will likely lead to even lighter, stronger, and more efficient helmets.
Additionally, the growing interest in smart technology integration will offer new ways to protect and inform helmet users.
In conclusion, automatic foldable helmets represent a significant step forward in personal safety gear.
They combine the practicality of easy transport with advanced impact absorption technology, all while adhering to rigorous safety standards.
As manufacturers continue to innovate, we can look forward to even more sophisticated and effective designs in the near future.
資料ダウンロード
QCD調達購買管理クラウド「newji」は、調達購買部門で必要なQCD管理全てを備えた、現場特化型兼クラウド型の今世紀最高の購買管理システムとなります。
ユーザー登録
調達購買業務の効率化だけでなく、システムを導入することで、コスト削減や製品・資材のステータス可視化のほか、属人化していた購買情報の共有化による内部不正防止や統制にも役立ちます。
NEWJI DX
製造業に特化したデジタルトランスフォーメーション(DX)の実現を目指す請負開発型のコンサルティングサービスです。AI、iPaaS、および先端の技術を駆使して、製造プロセスの効率化、業務効率化、チームワーク強化、コスト削減、品質向上を実現します。このサービスは、製造業の課題を深く理解し、それに対する最適なデジタルソリューションを提供することで、企業が持続的な成長とイノベーションを達成できるようサポートします。
オンライン講座
製造業、主に購買・調達部門にお勤めの方々に向けた情報を配信しております。
新任の方やベテランの方、管理職を対象とした幅広いコンテンツをご用意しております。
お問い合わせ
コストダウンが利益に直結する術だと理解していても、なかなか前に進めることができない状況。そんな時は、newjiのコストダウン自動化機能で大きく利益貢献しよう!
(Β版非公開)