- お役立ち記事
- Manufacturing Process of Automatic Hydroponic Systems and Improvement in Nutrient Management Systems
この記事は、当社の提供するお役立ち記事の一部です。詳しくは公式サイトをご覧ください。
Manufacturing Process of Automatic Hydroponic Systems and Improvement in Nutrient Management Systems
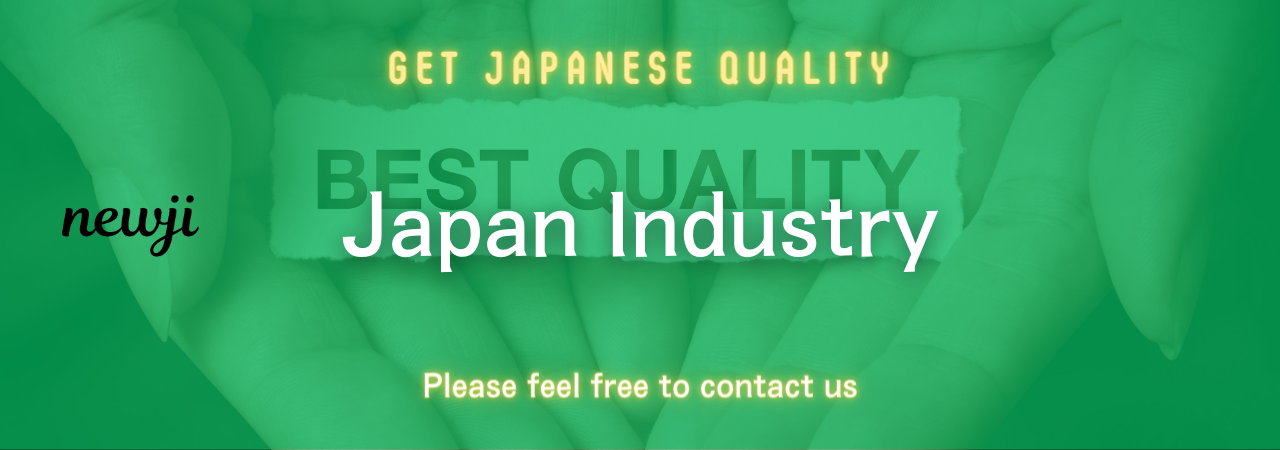
Hydroponic systems have gained incredible popularity in recent years due to their ability to cultivate plants without soil, utilizing mineral nutrient solutions in an aqueous solvent.
With the rise of automation in various industries, the development of automatic hydroponic systems has taken a significant leap forward.
This article will explore the manufacturing process of these innovative systems, as well as discuss improvements in nutrient management systems.
目次
Understanding Automatic Hydroponic Systems
Before delving into the manufacturing details, it’s essential to understand what automatic hydroponic systems are and why they are pivotal in modern agriculture.
Hydroponics is a method of growing plants using mineral nutrient solutions in water, without soil.
Automatic hydroponic systems incorporate advanced technologies such as sensors, pumps, and controllers to manage the growth environment more efficiently and reduce manual labor.
The Core Components
Any automatic hydroponic system consists of several key components:
– Water Reservoir: Holds the nutrient solution.
– Water Pump: Circulates the nutrient solution to the plants.
– Grow Trays: Where plants are placed to grow.
– Sensors: Monitor crucial parameters like pH, nutrient levels, and temperature.
– Controller: The brain of the system that automates various functions based on sensor data.
– Grow Lights: Provide the necessary light spectrum for photosynthesis.
Manufacturing Process of Automatic Hydroponic Systems
The creation of automatic hydroponic systems involves several stages, each focusing on different components and ensuring the system’s overall efficiency and reliability.
Design and Prototyping
The first step in the manufacturing process is designing the system.
Engineers and designers collaborate to create a blueprint that meets the specific requirements of the end-users.
This includes determining the size, materials, and functionalities of the system.
Prototyping follows, where a preliminary model is developed to test different aspects such as structural integrity, sensor efficiency, and overall system functionality.
Material Selection
Choosing the right materials is crucial for the durability and efficiency of the hydroponic system.
Commonly used materials include food-grade plastics for reservoirs and grow trays, stainless steel for structural parts, and high-quality electronic components for sensors and controllers.
The materials must be non-reactive to prevent contamination of the nutrient solution and ensure long-term sustainability.
Component Manufacturing
The next phase involves manufacturing each component separately.
Water reservoirs and grow trays are often made through plastic molding techniques.
Water pumps and other mechanical parts go through precision machining processes.
Electronic components such as sensors and controllers are assembled in clean rooms to maintain their sensitivity and accuracy.
System Assembly
Once the components are ready, the system assembly begins.
Skilled technicians and engineers piece together each part, ensuring proper alignment and integration.
The water reservoir is connected to the pump, which is then linked to the grow trays.
Sensors are installed at strategic points to monitor essential parameters, and the controller is connected to manage and automate the system efficiently.
Quality Testing
Quality testing is a critical stage in the manufacturing process.
The entire system is put through various tests to ensure it meets the required standards.
This includes testing the water flow, checking the sensor accuracy, and ensuring the controller responds appropriately to different inputs.
Any defects identified during this phase are addressed before the system moves to the next stage.
Improvements in Nutrient Management Systems
Effective nutrient management is paramount for the success of hydroponic farming.
With advancements in technology, numerous improvements have been made in nutrient management systems to enhance plant growth and productivity.
Advanced Sensor Technologies
Modern automatic hydroponic systems are equipped with sophisticated sensors that can accurately measure nutrient concentrations, pH levels, and other critical parameters in real-time.
These sensors provide continuous feedback to the controller, allowing for precise adjustments to the nutrient solution.
This real-time monitoring ensures plants receive the optimal nutrients needed for healthy growth.
Automated Nutrient Dosing
Automation has significantly revolutionized nutrient dosing in hydroponic systems.
Automatic dosing pumps are programmed to add the exact amount of nutrients required based on sensor data.
This not only reduces the risk of human error but also ensures consistent nutrient delivery.
Automated dosing systems can also adapt to the changing needs of plants at different growth stages, ensuring they receive the right nutrients at the right time.
Integration with IoT
The Internet of Things (IoT) has transformed many industries, and hydroponics is no exception.
By integrating IoT technologies, hydroponic systems can be remotely monitored and controlled using smartphones or computers.
This allows farmers to keep an eye on their crops and make necessary adjustments from anywhere in the world.
IoT integration also facilitates data collection and analysis, providing valuable insights into plant health and nutrient requirements.
Nutrient Recycling Systems
Efficient nutrient use is another area that has seen significant improvement.
Advanced hydroponic systems now feature nutrient recycling capabilities, where excess nutrient solution is collected, filtered, and reused.
This not only reduces waste but also ensures a continuous supply of nutrients to the plants.
Nutrient recycling systems are designed to remove any impurities, ensuring that recycled nutrients are as effective as fresh solutions.
Conclusion
The manufacturing process of automatic hydroponic systems is a meticulous and multifaceted endeavor, involving keen attention to design, material selection, component manufacturing, assembly, and quality testing.
These systems, bolstered by advancements in sensor technology, automated nutrient dosing, IoT integration, and nutrient recycling, represent the future of agriculture.
By embracing these technologies, farmers can achieve higher yields, reduce resource use, and manage crops more efficiently, ultimately contributing to sustainable and innovative agricultural practices.
資料ダウンロード
QCD調達購買管理クラウド「newji」は、調達購買部門で必要なQCD管理全てを備えた、現場特化型兼クラウド型の今世紀最高の購買管理システムとなります。
ユーザー登録
調達購買業務の効率化だけでなく、システムを導入することで、コスト削減や製品・資材のステータス可視化のほか、属人化していた購買情報の共有化による内部不正防止や統制にも役立ちます。
NEWJI DX
製造業に特化したデジタルトランスフォーメーション(DX)の実現を目指す請負開発型のコンサルティングサービスです。AI、iPaaS、および先端の技術を駆使して、製造プロセスの効率化、業務効率化、チームワーク強化、コスト削減、品質向上を実現します。このサービスは、製造業の課題を深く理解し、それに対する最適なデジタルソリューションを提供することで、企業が持続的な成長とイノベーションを達成できるようサポートします。
オンライン講座
製造業、主に購買・調達部門にお勤めの方々に向けた情報を配信しております。
新任の方やベテランの方、管理職を対象とした幅広いコンテンツをご用意しております。
お問い合わせ
コストダウンが利益に直結する術だと理解していても、なかなか前に進めることができない状況。そんな時は、newjiのコストダウン自動化機能で大きく利益貢献しよう!
(Β版非公開)