- お役立ち記事
- Manufacturing Process of Automatic Pet Doors and Strengthening Detection Systems
Manufacturing Process of Automatic Pet Doors and Strengthening Detection Systems
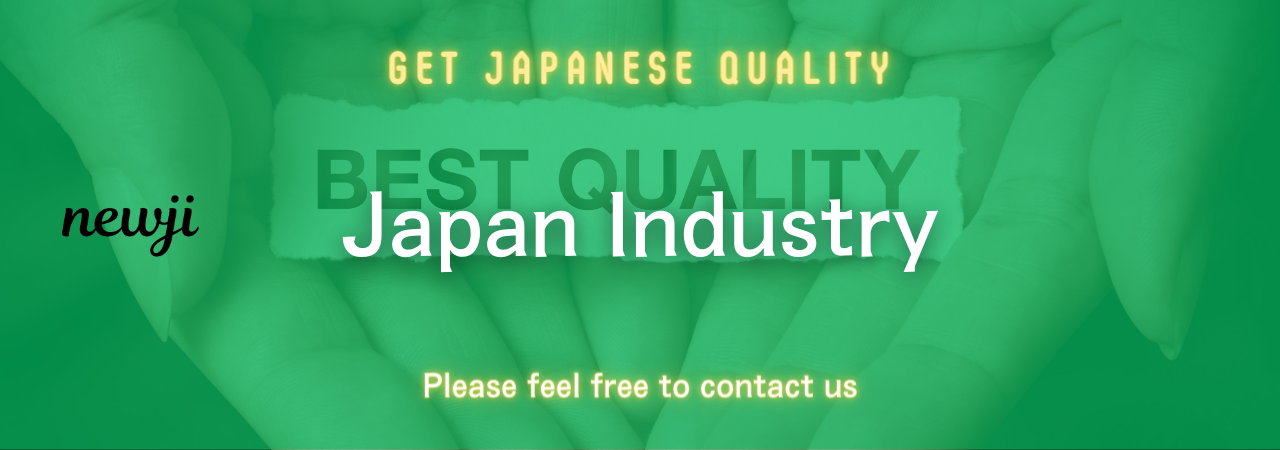
Pet doors have long been a solution for the independent pets who enjoy a mix of indoor comfort and outdoor adventure.
With advancements in technology, automatic pet doors have provided a level of convenience and security previously unattainable by manual models.
Understanding the manufacturing process of automatic pet doors and how their detection systems are strengthened can bring this marvel of pet products to light.
目次
Materials and Initial Design
Manufacturing an automatic pet door begins with selecting the right materials.
Durability and safety are paramount concerns, given that these doors must endure frequent use and resist potential threats from weather and potential intruders.
Common materials include:
– High-grade aluminum for the framework.
– Sturdy, shatterproof plastic for the flap.
– Weather-resistant seals to keep drafts and rain out.
Designers sketch out the initial designs, focusing on the door’s dimensions, security features, and aesthetics.
3D modeling software helps in visualizing the door, testing for durability and usability before the physical prototype phase begins.
Prototyping
Once the initial design is ready, manufacturers create prototypes.
These prototypes are integral to ironing out any issues before full-scale production.
Engineers and designers collaborate to evaluate the prototypes, focusing on ease of use for pets, strength, and functionality of the automatic features.
Feedback from pet behaviorists is also considered.
Pets of various sizes and temperaments are given access to the doors, ensuring the design is pet-friendly and intuitive.
Production Line Phase
After the prototyping phase, the design is refined and approved for mass production.
The first step in the production process is material preparation.
Aluminum and plastic materials are cut to specification using precision machinery.
Here’s a breakdown of the steps:
Aluminum Frame
The aluminum frames are cut using CNC (Computer Numerical Control) machines for precision.
They are then shaped and welded to form the rigid structure around the door.
Plastic Flap
The flap is often crafted from high-impact polymer.
Injection molding is used to create a uniform, sturdy piece.
This flap is then fitted into the aluminum frame.
Assembly
During the assembly phase, the various components are brought together.
Automated robotic arms assist in attaching the flap to the frame with high-strength fasteners.
Weather-resistant seals and insulation are added to the frame to keep the elements out.
Integrating Automatic Mechanisms
Automatic pet doors distinguish themselves with their ability to open and close without manual intervention.
This feature relies on electronic components like sensors and motors.
Here’s the step-by-step process:
Sensors
Sensors are essential.
They detect when a pet approaches and trigger the door to open.
These can include motion sensors, RFID (Radio Frequency Identification), or even microchip recognition systems.
During the manufacturing process, these sensors are tested rigorously for sensitivity and reliability.
Motors
Small, yet powerful motors are installed to facilitate the opening and closing mechanism.
The motors are designed to open the flap quietly and smoothly, minimizing any noise that could startle a pet.
Power Supply
Automatic pet doors can operate on various power sources, including batteries or direct electrical connection.
During assembly, the appropriate power supply option is integrated, ensuring safety and easy maintenance.
Testing and Quality Assurance
Post-assembly, every automatic pet door undergoes comprehensive testing.
This includes functionality tests to ensure sensors and motors are responsive and reliability tests to gauge performance under extended use.
Environmental tests also take place, verifying the door’s resistance to water, wind, and varying temperatures.
Strengthening Detection Systems
To enhance security and functionality, the detection systems in automatic pet doors are continuously being refined.
There are a number of ways this can be achieved:
Advanced Motion Sensors
Advanced motion sensors can differentiate between pets, humans, and inanimate objects.
This ensures that the door only opens for the pet, enhancing security.
Microchip Recognition
This system utilizes the unique identification microchip already embedded in many pets.
Only pets with recognized microchips can trigger the door, keeping unwanted animals out.
Manufacturers install programming to read and respond to specific microchip frequencies.
Wi-Fi Connectivity
Many modern automatic pet doors come with Wi-Fi connectivity.
This allows pet owners to monitor and control the door remotely through a smartphone app.
Real-time alerts and usage logs provide additional layers of security and convenience.
Installation and Final Adjustments
The last step in the manufacturing process is educating the consumer on installation.
Clear instructions are provided, sometimes accompanied by video tutorials to ensure correct setup.
Manufacturers often include adjustable features, allowing the user to fine-tune the sensor sensitivity and motor speed after installation.
Environmental Considerations
Modern manufacturers focus on eco-friendly practices.
Recycled materials are often used, and factories adhere to environmental regulations to minimize waste.
Energy-efficient production techniques help reduce the carbon footprint associated with manufacturing.
Conclusion
The manufacturing process of automatic pet doors blends traditional materials with cutting-edge technology.
From the moment raw materials are chosen to the final quality assurance tests, each step ensures the product is durable, reliable, and user-friendly.
Additionally, ongoing improvements in detection systems cater to the needs of pet owners who seek convenience without compromising security.
With these advancements, automatic pet doors continue to evolve, providing both pets and their owners with unparalleled ease and peace of mind.
資料ダウンロード
QCD調達購買管理クラウド「newji」は、調達購買部門で必要なQCD管理全てを備えた、現場特化型兼クラウド型の今世紀最高の購買管理システムとなります。
ユーザー登録
調達購買業務の効率化だけでなく、システムを導入することで、コスト削減や製品・資材のステータス可視化のほか、属人化していた購買情報の共有化による内部不正防止や統制にも役立ちます。
NEWJI DX
製造業に特化したデジタルトランスフォーメーション(DX)の実現を目指す請負開発型のコンサルティングサービスです。AI、iPaaS、および先端の技術を駆使して、製造プロセスの効率化、業務効率化、チームワーク強化、コスト削減、品質向上を実現します。このサービスは、製造業の課題を深く理解し、それに対する最適なデジタルソリューションを提供することで、企業が持続的な成長とイノベーションを達成できるようサポートします。
オンライン講座
製造業、主に購買・調達部門にお勤めの方々に向けた情報を配信しております。
新任の方やベテランの方、管理職を対象とした幅広いコンテンツをご用意しております。
お問い合わせ
コストダウンが利益に直結する術だと理解していても、なかなか前に進めることができない状況。そんな時は、newjiのコストダウン自動化機能で大きく利益貢献しよう!
(Β版非公開)