- お役立ち記事
- Manufacturing Process of Automatic Pet Feeders and Portion Control Technology
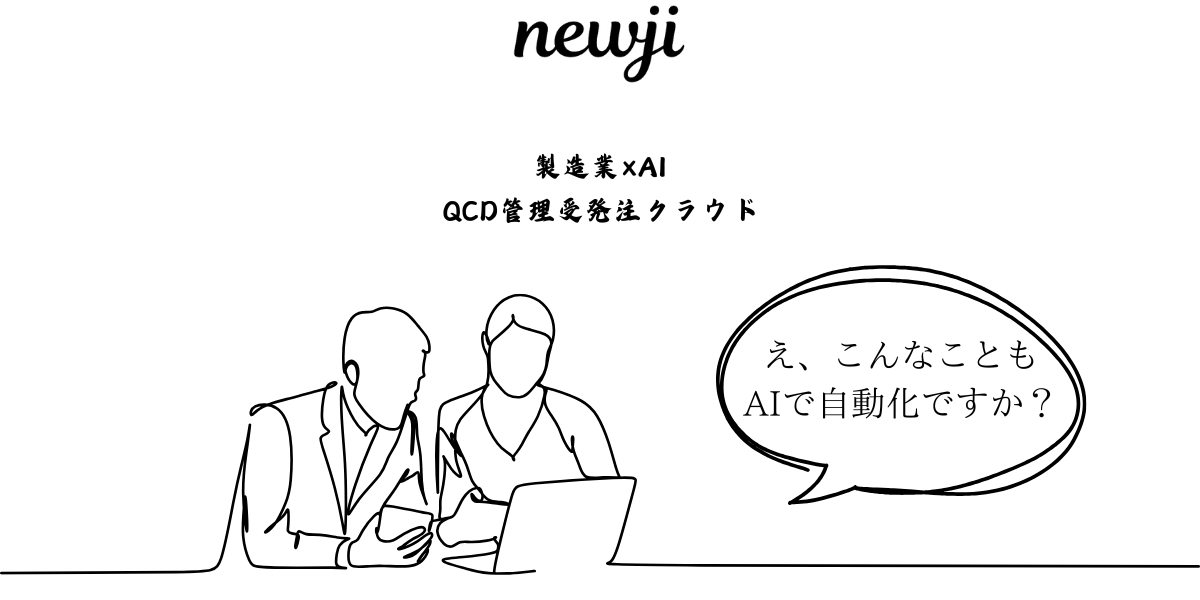
Manufacturing Process of Automatic Pet Feeders and Portion Control Technology
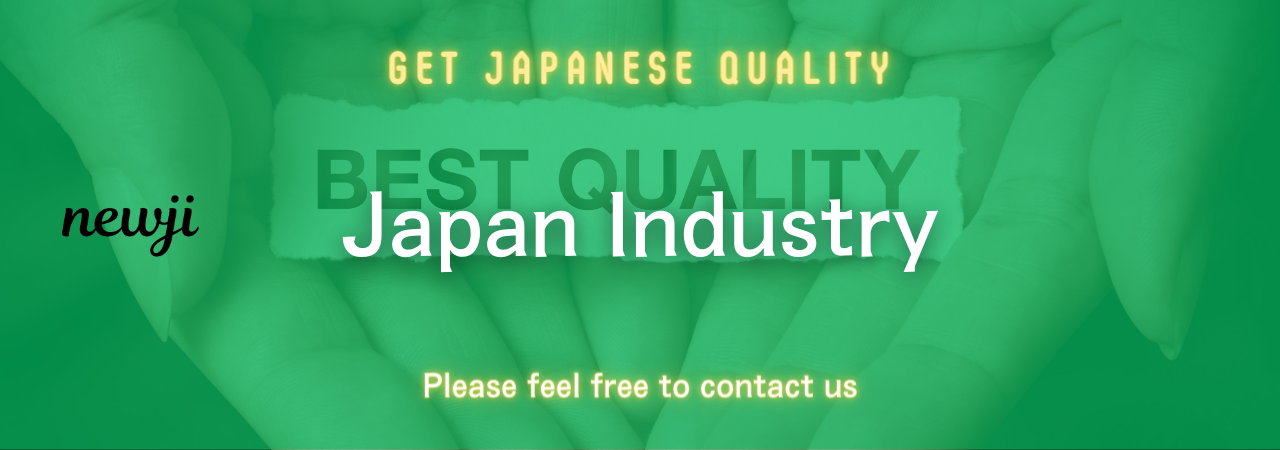
The increasing number of pet owners who seek convenience and health management for their furry friends has driven the rise in popularity of automatic pet feeders.
These devices serve as an efficient and reliable solution for feeding pets on a regular schedule, ensuring they get the right portions of food.
The manufacturing process of automatic pet feeders is intricate and involves several stages, from design and prototyping to final production and quality control.
目次
Understanding the Design Phase
The journey of an automatic pet feeder begins in the design phase.
Engineers and product designers collaborate to create a functional and aesthetically pleasing product.
Customer needs, pet sizes, food types, and feeding schedules are all considered during this phase.
Design Specifications
Every successful product starts with clear and detailed design specifications.
This document outlines the key requirements and features of the automatic pet feeder.
Specifications might include the type of power source (batteries or plug-in), the volume of the food container, and the material used for construction, ensuring durability and safety for pets.
Prototyping
Once the design specifications are in place, the next step involves creating prototypes.
Several prototype versions might be produced to test different functionalities and materials.
Engineers run multiple tests to evaluate the prototypes’ performance, making adjustments as needed.
Material Selection and Sourcing
Choosing the right materials is a critical step in the manufacturing process.
Materials must be pet-safe, non-toxic, and durable to withstand daily use.
Plastic Components
Most automatic pet feeders are made from high-quality, food-grade plastics.
This material is chosen for its durability and ease of cleaning.
Manufacturers source the plastic from reliable suppliers to ensure consistency and quality.
Electronic Components
The technological aspect of automatic pet feeders involves various electronic components.
Sensors, microcontrollers, and display screens are sourced and tested for quality assurance.
These components ensure the accuracy of portion control and schedule adherence.
Manufacturing and Assembly
With the design and materials ready, the manufacturing process can commence.
This phase involves several steps, including molding, assembly, and quality control.
Molding the Plastic Parts
Plastic components are created through injection molding.
Molten plastic is injected into molds, which are then cooled and ejected as solid parts.
This method allows for mass production of uniform pieces, maintaining consistency across all units.
Assembling the Feeder
Assembly is the phase where all parts come together to form the final product.
Plastic components, electronic parts, and any other necessary features are assembled in a precise order.
Automated assembly lines are often used to increase efficiency and reduce human error.
Incorporating Portion Control Technology
One of the key features of an automatic pet feeder is its ability to control food portions accurately.
Portion control technology involves sensors and software that regulate the amount of food dispensed.
Programming the Software
Software engineers play a significant role in embedding the portion control technology.
They develop algorithms that determine the right amount of food based on the pet’s needs.
The software is tested thoroughly to ensure it performs accurately under various conditions.
Installing Sensors
Sensors are integral to ensuring accurate food measurement.
These include weight sensors that measure the amount of food dispensed and motion sensors that detect the presence of the pet.
Proper installation and calibration of these sensors are crucial for the feeder’s functionality.
Quality Control and Testing
Before an automatic pet feeder reaches the market, it undergoes rigorous quality control and testing procedures.
These steps ensure that each unit is reliable, safe, and performs as expected.
Functionality Tests
Every unit is tested for its basic functionality; this includes evaluating the accuracy of food portions, the reliability of the feeding schedule, and the responsiveness of the sensors.
Units that fail these tests are sent back for reevaluation and troubleshooting.
Durability Testing
To ensure the feeders can withstand daily use, durability testing is performed.
This includes testing the impact resistance of plastic parts and the long-term functionality of electronic components.
Durability tests help identify potential weaknesses in the product’s design or construction.
Packaging and Distribution
Once the feeders pass quality control, they are packaged and prepared for distribution.
Manufacturers design the packaging to protect the feeders during transit and provide information about the product.
Eco-Friendly Packaging
Many manufacturers are leaning towards eco-friendly packaging materials.
Recyclable and biodegradable options are chosen to reduce environmental impact.
Eco-friendly packaging also appeals to environmentally conscious consumers.
Global Distribution
With packaging completed, the automatic pet feeders are ready for global distribution.
Manufacturers work with logistics partners to ensure timely delivery to retailers and customers around the world.
Proper distribution channels are essential for meeting market demand efficiently.
The manufacturing process of automatic pet feeders combines modern engineering, precise material selection, advanced technology, and stringent quality control.
By following these steps, manufacturers can deliver a reliable product that meets pet owners’ needs and promotes the health and well-being of pets.
As the technology advances, automatic pet feeders will continue to evolve, offering even more sophisticated features and improved convenience for pet lovers worldwide.
資料ダウンロード
QCD調達購買管理クラウド「newji」は、調達購買部門で必要なQCD管理全てを備えた、現場特化型兼クラウド型の今世紀最高の購買管理システムとなります。
ユーザー登録
調達購買業務の効率化だけでなく、システムを導入することで、コスト削減や製品・資材のステータス可視化のほか、属人化していた購買情報の共有化による内部不正防止や統制にも役立ちます。
NEWJI DX
製造業に特化したデジタルトランスフォーメーション(DX)の実現を目指す請負開発型のコンサルティングサービスです。AI、iPaaS、および先端の技術を駆使して、製造プロセスの効率化、業務効率化、チームワーク強化、コスト削減、品質向上を実現します。このサービスは、製造業の課題を深く理解し、それに対する最適なデジタルソリューションを提供することで、企業が持続的な成長とイノベーションを達成できるようサポートします。
オンライン講座
製造業、主に購買・調達部門にお勤めの方々に向けた情報を配信しております。
新任の方やベテランの方、管理職を対象とした幅広いコンテンツをご用意しております。
お問い合わせ
コストダウンが利益に直結する術だと理解していても、なかなか前に進めることができない状況。そんな時は、newjiのコストダウン自動化機能で大きく利益貢献しよう!
(Β版非公開)