- お役立ち記事
- Manufacturing Process of Automatic Shower Heads and Improvement in Water Flow Control Functions
月間76,176名の
製造業ご担当者様が閲覧しています*
*2025年3月31日現在のGoogle Analyticsのデータより
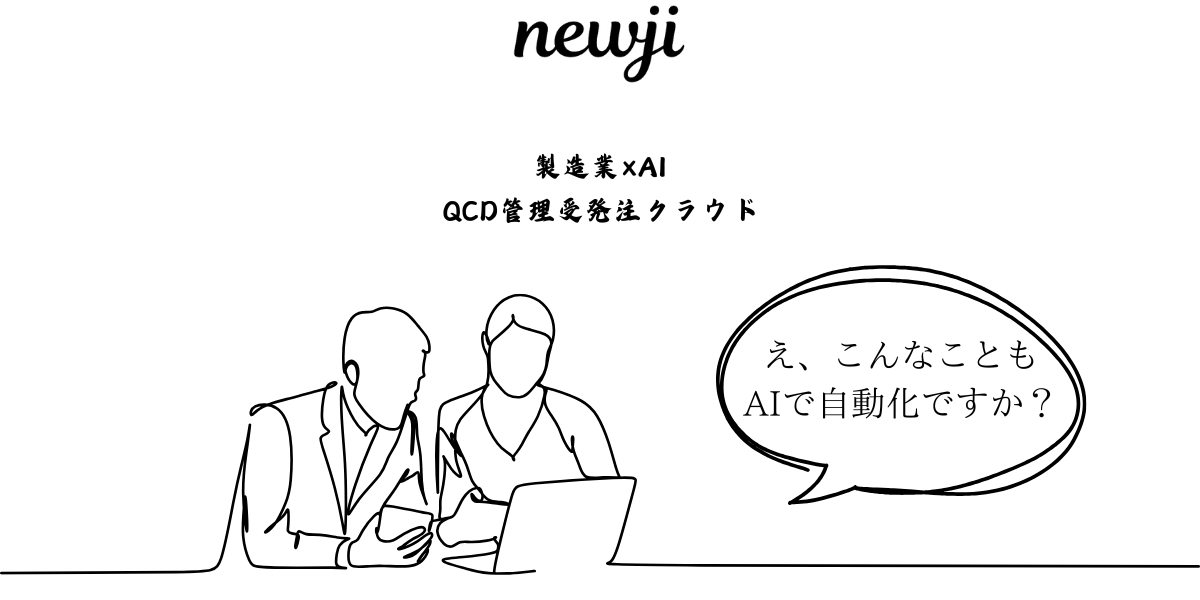
Manufacturing Process of Automatic Shower Heads and Improvement in Water Flow Control Functions
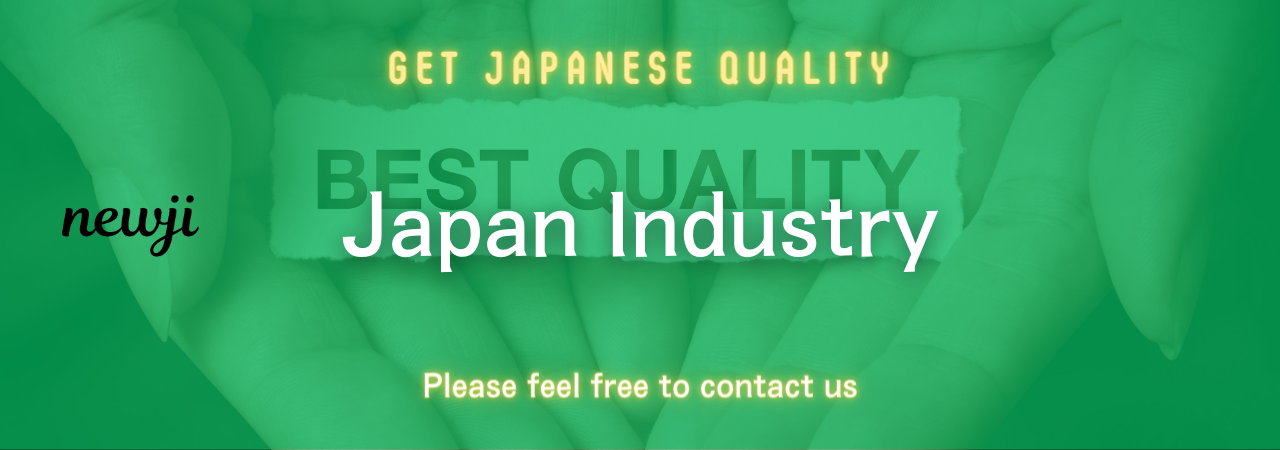
目次
Introduction to Automatic Shower Heads
Automatic shower heads are ingenious devices that bring both convenience and efficiency to your showering experience.
These shower heads are designed to automatically adjust water flow and temperature, providing a comfortable and consistent shower.
With growing concerns about water conservation and energy efficiency, automatic shower heads are becoming increasingly popular in modern households.
In this article, we will explore the manufacturing process of automatic shower heads and discuss how their water flow control functions have improved over time.
Materials Used in Manufacturing
The manufacturing of automatic shower heads begins with the selection of high-quality materials.
Durability and corrosion resistance are paramount since the shower head will be exposed to water daily.
Common materials include stainless steel, brass, and high-grade plastics.
Stainless steel is favored for its rust-resistant properties, while brass offers durability and a classic look.
High-grade plastics are lightweight and cost-effective, making them a popular choice as well.
Stainless Steel
Stainless steel is a widely recognized material in the industry.
Its corrosion-resistant properties make it an ideal choice for areas with high humidity.
Furthermore, stainless steel offers a sleek and modern appearance, enhancing the aesthetic appeal of the bathroom.
Brass
Brass is an alloy composed mainly of copper and zinc.
It is known for its robustness and longevity.
Shower heads made from brass are often considered premium products due to their durability and resistance to wear and tear.
High-Grade Plastics
High-grade plastics such as ABS (Acrylonitrile Butadiene Styrene) are lightweight yet strong.
They are also more affordable, making them accessible to a wider range of consumers.
Additionally, plastics can be easily molded into various designs, offering more flexibility in terms of aesthetics.
Design and Prototyping
Once the materials are selected, the next step is the design and prototyping phase.
Engineers and designers work together to create a functional and aesthetically pleasing shower head.
3D modeling software and CAD (Computer-Aided Design) tools are commonly used for this purpose.
During this phase, various parameters such as water pressure, spray patterns, and temperature control mechanisms are taken into consideration.
Prototypes are created to test these functionalities rigorously before mass production begins.
3D Modeling
3D modeling allows designers to visualize the shower head from all angles.
This helps in identifying potential issues and making necessary adjustments in the design.
The use of 3D modeling accelerates the development process and ensures precision.
Prototype Testing
Prototypes are manufactured and tested extensively.
Engineers evaluate water flow, temperature regulation, and durability.
User feedback is also considered to ensure that the final product meets consumer expectations.
This meticulous testing phase ensures that any flaws are identified and rectified before moving to full-scale production.
Manufacturing Process
The manufacturing process of automatic shower heads involves several stages, including molding, assembly, and quality control.
Each stage is crucial to ensuring the final product is both functional and reliable.
Molding
Molding is the first step in the manufacturing process.
For plastic components, injection molding is commonly used.
Molten plastic is injected into a mold cavity, which is then cooled and solidified to form the desired shape.
For metal components, die casting or forging may be employed.
Assembly
Once all the individual components are molded, they are assembled to form the complete shower head.
This involves attaching the nozzle, temperature control unit, and other moving parts.
Automated machines are often used for assembly to ensure precision and speed.
Quality Control
Quality control is an integral part of the manufacturing process.
Each shower head undergoes rigorous testing to ensure it meets specified standards.
Water flow rate, temperature control efficacy, and durability are among the key parameters tested.
Defective units are discarded, ensuring only high-quality products reach the market.
Improvement in Water Flow Control Functions
Technological advancements have significantly improved the water flow control functions of automatic shower heads.
Modern shower heads come equipped with features such as adjustable spray patterns, pressure control, and temperature regulation.
Adjustable Spray Patterns
Early shower heads offered a single spray pattern.
However, modern designs allow users to switch between various spray modes, such as mist, rain, and massage.
This customization enhances the showering experience, allowing users to choose the most comfortable setting.
Pressure Control
Pressure control mechanisms have also seen substantial improvements.
Advanced shower heads can automatically adjust water pressure to provide a consistent flow, even in areas with low water pressure.
This ensures a steady stream of water, making the shower more enjoyable.
Temperature Regulation
Automatic temperature control is a game-changer.
Modern shower heads come equipped with sensors that monitor and adjust water temperature in real-time.
This prevents sudden temperature fluctuations, ensuring a safe and comfortable shower.
Energy Efficiency and Water Conservation
One of the primary motivations behind the development of automatic shower heads is energy efficiency and water conservation.
Modern designs use advanced technology to reduce water consumption without sacrificing performance.
Low-Flow Shower Heads
Low-flow shower heads are designed to use less water while providing adequate pressure and coverage.
They achieve this by mixing air with water to produce a steady stream, reducing water usage by up to 60%.
Smart Sensors
Smart sensors detect the presence of a person and adjust water flow accordingly.
When the shower is not in use, the water flow is reduced or stopped, minimizing wastage.
This not only conserves water but also reduces energy consumption.
Conclusion
The manufacturing process of automatic shower heads involves meticulous planning and execution.
From selecting high-quality materials to rigorous testing, each step ensures the production of reliable and efficient products.
Technological advancements have significantly improved water flow control functions, making modern shower heads more efficient and user-friendly.
As we continue to prioritize energy efficiency and water conservation, automatic shower heads will play a crucial role in achieving these goals.
Investing in a high-quality automatic shower head is not only a wise choice for personal comfort but also a step towards a more sustainable future.
資料ダウンロード
QCD管理受発注クラウド「newji」は、受発注部門で必要なQCD管理全てを備えた、現場特化型兼クラウド型の今世紀最高の受発注管理システムとなります。
ユーザー登録
受発注業務の効率化だけでなく、システムを導入することで、コスト削減や製品・資材のステータス可視化のほか、属人化していた受発注情報の共有化による内部不正防止や統制にも役立ちます。
NEWJI DX
製造業に特化したデジタルトランスフォーメーション(DX)の実現を目指す請負開発型のコンサルティングサービスです。AI、iPaaS、および先端の技術を駆使して、製造プロセスの効率化、業務効率化、チームワーク強化、コスト削減、品質向上を実現します。このサービスは、製造業の課題を深く理解し、それに対する最適なデジタルソリューションを提供することで、企業が持続的な成長とイノベーションを達成できるようサポートします。
製造業ニュース解説
製造業、主に購買・調達部門にお勤めの方々に向けた情報を配信しております。
新任の方やベテランの方、管理職を対象とした幅広いコンテンツをご用意しております。
お問い合わせ
コストダウンが利益に直結する術だと理解していても、なかなか前に進めることができない状況。そんな時は、newjiのコストダウン自動化機能で大きく利益貢献しよう!
(β版非公開)