- お役立ち記事
- Manufacturing Process of Automatic Tea Bag Dispensers and Improvement in Dispensing Mechanism
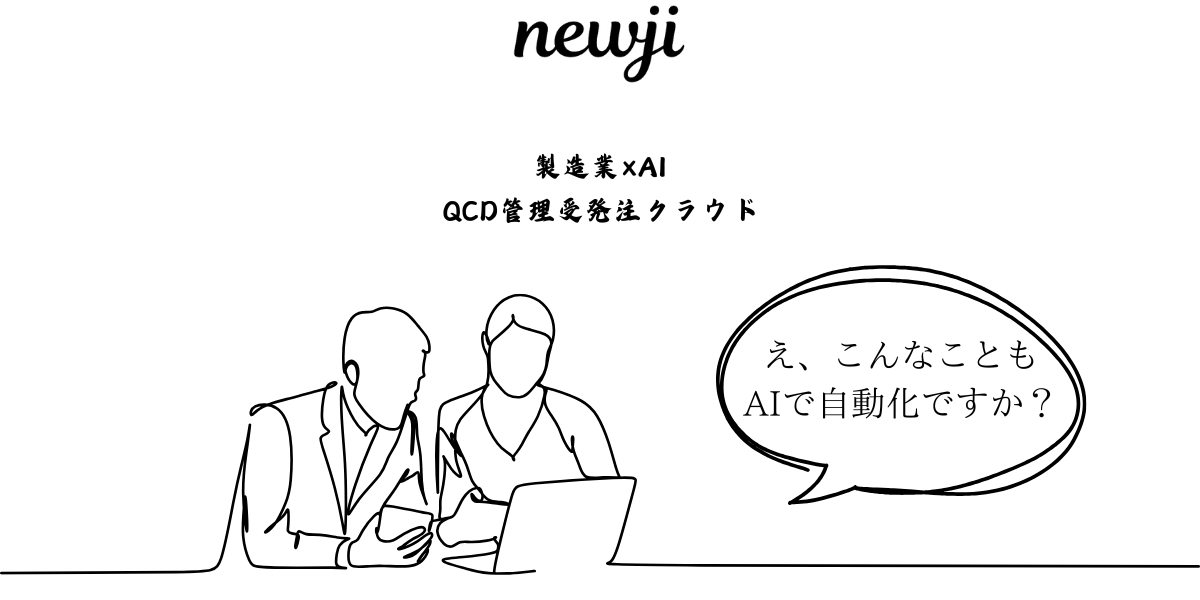
Manufacturing Process of Automatic Tea Bag Dispensers and Improvement in Dispensing Mechanism
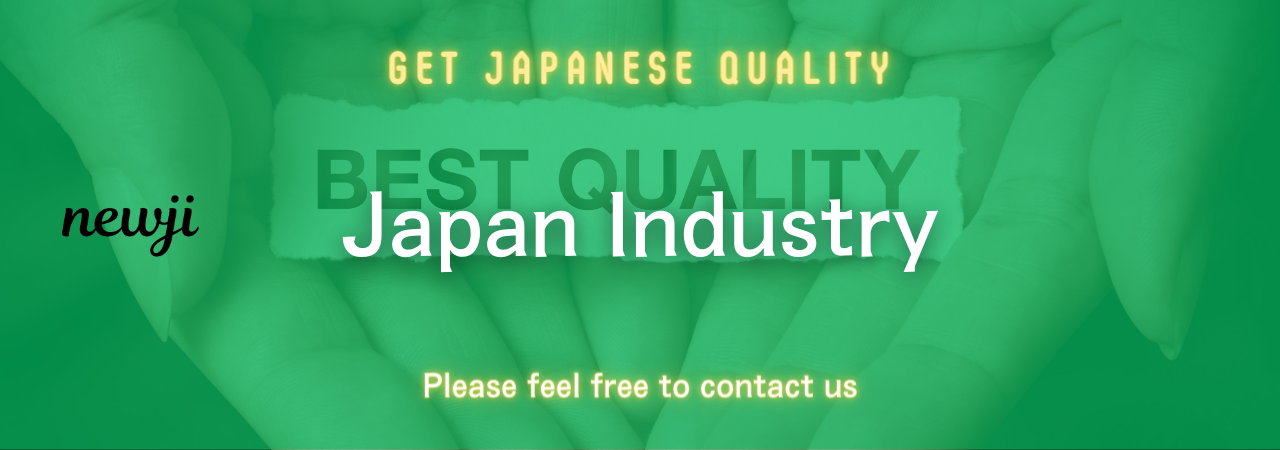
Automatic tea bag dispensers have become increasingly popular, offering convenience and efficiency in homes and commercial settings alike.
These devices not only save time but also ensure consistency in the brewing process.
To appreciate the value these machines bring, it’s essential to understand how they are manufactured and how their dispensing mechanisms have been improved over time.
目次
The Initial Stages of Manufacturing
The production of automatic tea bag dispensers begins with careful planning and design.
Engineers and designers work together to create a blueprint that balances functionality, aesthetics, and user-friendliness.
This stage involves selecting materials that are durable and safe for contact with food items.
Once the design is finalized, the next step involves prototyping.
In this phase, a physical model of the dispenser is created.
This prototype is rigorously tested to identify any potential issues or areas for improvement.
Feedback from this stage is crucial for refining the design before mass production begins.
Material Selection
When it comes to automatic tea bag dispensers, the choice of materials plays a significant role in determining the product’s quality and durability.
Typically, these dispensers are made from a combination of plastics and metals.
Plastics like ABS (Acrylonitrile Butadiene Styrene) and polycarbonate are commonly used for their strength and resistance to heat.
Metals such as stainless steel might be employed for components that require additional sturdiness.
The Manufacturing Process
Once the design and materials have been finalized, the manufacturing process begins in earnest.
This involves several key steps, each contributing to the creation of a reliable and efficient automatic tea bag dispenser.
1. Injection Molding
Injection molding is a crucial step in manufacturing plastic components of tea bag dispensers.
In this process, molten plastic is injected into molds to create parts like the outer casing and internal mechanisms.
These molded parts are then cooled and ejected from the mold, ready for assembly.
2. Metal Fabrication
For metal components, different fabrication techniques such as stamping, cutting, and bending are employed.
These processes shape the metal into desired forms, ensuring they fit perfectly with the plastic parts.
Metal components often include the dispensing mechanism and any structural supports that enhance the durability of the dispenser.
3. Assembly
Once all the parts have been fabricated, the assembly process begins.
This is a critical stage where precision is paramount.
Assembly typically involves automated machinery and manual labor.
Components are carefully fit together, and electronic parts are integrated into the system.
During assembly, a series of quality checks are conducted to ensure that each dispenser meets the required standards.
This includes testing the dispensing mechanism to make sure it operates smoothly and consistently.
4. Calibration and Testing
After assembly, each tea bag dispenser undergoes calibration to ensure that it dispenses the correct number of tea bags with each use.
This is a meticulous process that involves fine-tuning the internal mechanism.
Following calibration, comprehensive testing is carried out to evaluate the dispenser’s performance.
Testing includes stress tests, operational tests, and user experience evaluations.
The goal is to identify any issues that might affect the performance or longevity of the dispenser.
Only those units that pass all tests are approved for distribution.
Improvements in Dispensing Mechanisms
The dispensing mechanism is the heart of any automatic tea bag dispenser.
Over the years, several advancements have been made to enhance the efficiency and reliability of these mechanisms.
1. Enhanced Motor Precision
In the past, inconsistencies in the motor’s operation could lead to uneven dispensing of tea bags.
Modern dispensers now use high-precision motors that ensure consistent performance.
These motors are often quieter and more energy-efficient, contributing to a better user experience.
2. Sensor Integration
Sensors have significantly improved the functionality of tea bag dispensers.
Modern devices often include sensors that detect the presence of a cup or mug, triggering the dispensing mechanism automatically.
This feature not only adds convenience but also reduces the chances of accidental releases.
3. Customizable Dispensing Options
Today’s tea bag dispensers offer customizable options to cater to different user preferences.
Users can adjust the number of tea bags dispensed or select different tea varieties if the dispenser has multiple compartments.
This level of customization enhances user satisfaction and makes the device more versatile.
4. Improved User Interface
The user interface plays a critical role in the overall functionality of the dispenser.
Recent developments have seen the inclusion of touch screen interfaces and mobile app controls.
These enhancements make the dispensers more intuitive and easier to use.
Users can program their devices remotely, add to the convenience of the whole process.
Environmental Considerations
In today’s eco-conscious world, manufacturers are paying more attention to the environmental impact of their products.
This trend is evident in the production of automatic tea bag dispensers as well.
1. Sustainable Materials
Many manufacturers are now opting for sustainable materials, such as recycled plastics and metals.
These materials help reduce the overall carbon footprint of the product without compromising on quality.
2. Energy Efficiency
Energy-efficient components, such as low-power motors and LED indicators, are becoming standard in modern dispensers.
These features not only save on electricity but also contribute to the device’s longevity.
3. Waste Reduction
Innovative designs aim to minimize waste by ensuring that all tea bags are dispensed accurately, leaving no residual bags in the dispenser.
Manufacturers are also incorporating recyclable packaging to make the entire product lifecycle more sustainable.
Automatic tea bag dispensers offer a convenient and efficient way to enjoy your favorite brew.
Understanding the intricate manufacturing process and the continuous improvements in dispensing mechanisms allows for a greater appreciation of these innovative machines.
As technology advances, we can expect even more user-friendly and environmentally sustainable designs in the future.
資料ダウンロード
QCD調達購買管理クラウド「newji」は、調達購買部門で必要なQCD管理全てを備えた、現場特化型兼クラウド型の今世紀最高の購買管理システムとなります。
ユーザー登録
調達購買業務の効率化だけでなく、システムを導入することで、コスト削減や製品・資材のステータス可視化のほか、属人化していた購買情報の共有化による内部不正防止や統制にも役立ちます。
NEWJI DX
製造業に特化したデジタルトランスフォーメーション(DX)の実現を目指す請負開発型のコンサルティングサービスです。AI、iPaaS、および先端の技術を駆使して、製造プロセスの効率化、業務効率化、チームワーク強化、コスト削減、品質向上を実現します。このサービスは、製造業の課題を深く理解し、それに対する最適なデジタルソリューションを提供することで、企業が持続的な成長とイノベーションを達成できるようサポートします。
オンライン講座
製造業、主に購買・調達部門にお勤めの方々に向けた情報を配信しております。
新任の方やベテランの方、管理職を対象とした幅広いコンテンツをご用意しております。
お問い合わせ
コストダウンが利益に直結する術だと理解していても、なかなか前に進めることができない状況。そんな時は、newjiのコストダウン自動化機能で大きく利益貢献しよう!
(Β版非公開)