- お役立ち記事
- Manufacturing Process of Automatic Vegetable Cutters and Improving Blade Precision
Manufacturing Process of Automatic Vegetable Cutters and Improving Blade Precision
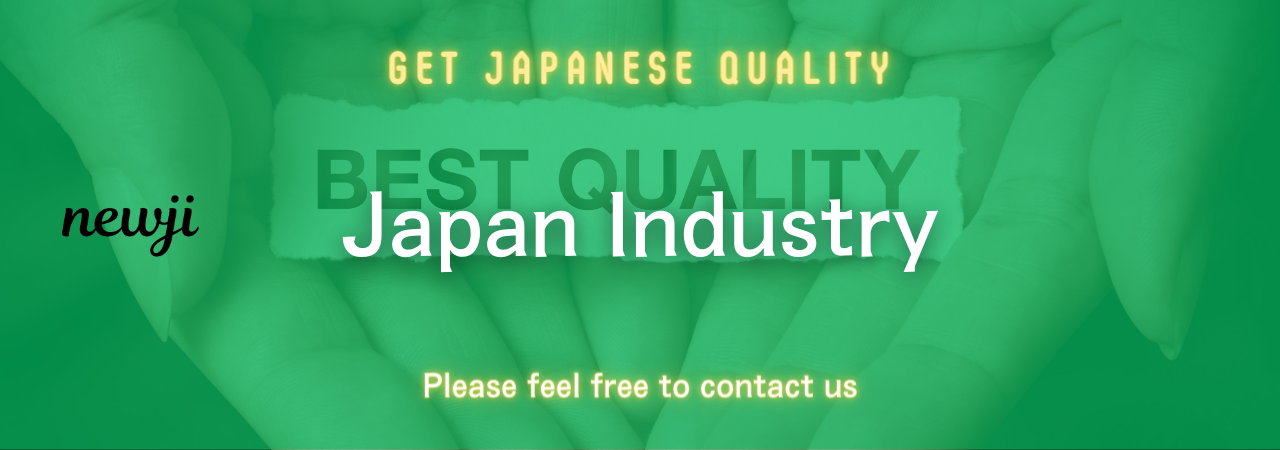
Automatic vegetable cutters have become essential tools in commercial kitchens and food processing facilities.
They significantly reduce labor and improve efficiency, allowing chefs and food workers to concentrate on other important tasks.
This article will delve into the manufacturing process of these machines and explore how blade precision can be enhanced for better performance.
目次
Materials Selection for Manufacturing
The foundation of any durable and efficient automatic vegetable cutter lies in the materials chosen for its construction.
Manufacturers typically opt for stainless steel and high-quality plastic for their durability and resistance to corrosion.
Stainless steel is often used for the blades due to its sharpness and longevity, while food-grade plastic is preferred for parts that come into direct contact with food to ensure hygiene and safety.
Stainless Steel for Blades
Stainless steel is favored for its excellent cutting performance and resistance to wear and tear.
Additionally, it is less likely to harbor bacteria, making it an ideal choice for food preparation equipment.
The selection of stainless steel grade greatly affects the blade’s performance—High-Carbon Stainless Steel (HCSS) is particularly popular for its hardness and ability to maintain a sharp edge.
Food-Grade Plastics
Food-grade plastics, such as polypropylene and polyethylene, are used for parts like the housing and safety guards.
These materials are lightweight, durable, and easy to clean, contributing to the overall efficiency of the cutter.
Selecting food-grade plastics ensures that the machine meets safety and hygiene standards essential for food processing environments.
Design and Engineering
Design and engineering play critical roles in developing automatic vegetable cutters.
A well-designed cutter should be user-friendly, efficient, and easy to maintain.
Engineers employ advanced computer-aided design (CAD) software to prototype and test various designs before settling on the most efficient model.
Ergonomics
One of the primary considerations in the design phase is ergonomics.
The machine should be intuitive to operate and comfortable to use.
Designers focus on creating interfaces and controls that reduce user fatigue and increase productivity.
Handles, buttons, and levers are positioned for easy access, minimizing repetitive stress injuries among users.
Safety Mechanisms
Safety is paramount when designing automatic vegetable cutters.
Foolproof safety mechanisms are integrated to protect users from accidental injuries.
Interlocks, emergency stop buttons, and blade guards are just a few of the features incorporated to enhance user safety.
Engineers run rigorous tests to ensure these safety features function reliably under all conditions.
Manufacturing Process
The manufacturing process of automatic vegetable cutters involves several intricate steps, including fabrication, assembly, testing, and quality assurance.
Fabrication
Fabrication is the initial stage where raw materials are transformed into usable components.
CNC machining and laser cutting are commonly employed to create precise parts from stainless steel and plastic sheets. This stage is critical as it lays the groundwork for the cutter’s overall quality and durability.
Assembly
Once all components are fabricated, they are transferred to the assembly line.
Skilled workers and robotic arms work in tandem to piece together the cutter.
Special care is taken to ensure that all moving parts are correctly aligned and lubricated.
Manufacturers often follow a strict protocol to ensure that assembly meets predefined standards.
Testing
Testing is an essential phase that ensures each cutter functions as intended.
Various tests are conducted to evaluate the machine’s performance, safety features, and durability.
Sample vegetables are run through the cutter to check if it slices, dices, or chops as per specifications.
Any irregularities are corrected before the unit proceeds to the next stage.
Quality Assurance
Quality assurance is the final step before the cutter reaches the market.
Units that pass the testing phase undergo a final inspection to ensure that they meet all quality standards.
This step often includes a thorough visual examination and additional functional tests.
Only those units that pass all inspections are deemed ready for shipping.
Improving Blade Precision
The precision of the blade is crucial for the performance of automatic vegetable cutters.
A sharp, accurate blade ensures clean cuts, reducing food waste and improving presentation.
Blade Material and Geometry
Blade precision largely depends on the material and geometry.
High-carbon stainless steel is renowned for retaining sharpness.
The geometry of the blade—its thickness, angle, and edge—are meticulously designed for optimal cutting performance.
Engineers often employ finite element analysis (FEA) to simulate blade performance under various conditions.
Sharpening Techniques
Regular sharpening is vital for maintaining blade precision.
Automated sharpening machines use grindstones and honing rods to refine the blade’s edge.
Manufacturers sometimes apply a special coating to enhance the blade’s sharpness and durability.
Periodic re-sharpening ensures the blade remains effective over its lifetime.
Alignment and Calibration
Proper alignment and calibration of the blade with the machine are critical.
Misalignment can cause uneven cuts and wear out the blade prematurely.
Manufacturers use precise calibration tools and techniques to ensure the blade is correctly installed.
Routine maintenance includes checking alignment and re-calibration, if necessary.
Automatic vegetable cutters are invaluable tools in any large-scale food operation.
The manufacturing process involves careful material selection, innovative design, and meticulous engineering.
Understanding how to improve blade precision further enhances the machine’s performance, making it a worthwhile investment.
With continuous advancements, these cutters will only become more efficient, user-friendly, and indispensable in commercial kitchens and food processing facilities.
資料ダウンロード
QCD調達購買管理クラウド「newji」は、調達購買部門で必要なQCD管理全てを備えた、現場特化型兼クラウド型の今世紀最高の購買管理システムとなります。
ユーザー登録
調達購買業務の効率化だけでなく、システムを導入することで、コスト削減や製品・資材のステータス可視化のほか、属人化していた購買情報の共有化による内部不正防止や統制にも役立ちます。
NEWJI DX
製造業に特化したデジタルトランスフォーメーション(DX)の実現を目指す請負開発型のコンサルティングサービスです。AI、iPaaS、および先端の技術を駆使して、製造プロセスの効率化、業務効率化、チームワーク強化、コスト削減、品質向上を実現します。このサービスは、製造業の課題を深く理解し、それに対する最適なデジタルソリューションを提供することで、企業が持続的な成長とイノベーションを達成できるようサポートします。
オンライン講座
製造業、主に購買・調達部門にお勤めの方々に向けた情報を配信しております。
新任の方やベテランの方、管理職を対象とした幅広いコンテンツをご用意しております。
お問い合わせ
コストダウンが利益に直結する術だと理解していても、なかなか前に進めることができない状況。そんな時は、newjiのコストダウン自動化機能で大きく利益貢献しよう!
(Β版非公開)