- お役立ち記事
- Manufacturing Process of Automatic Water Dispensers and Improvement in Water Volume Control Functions
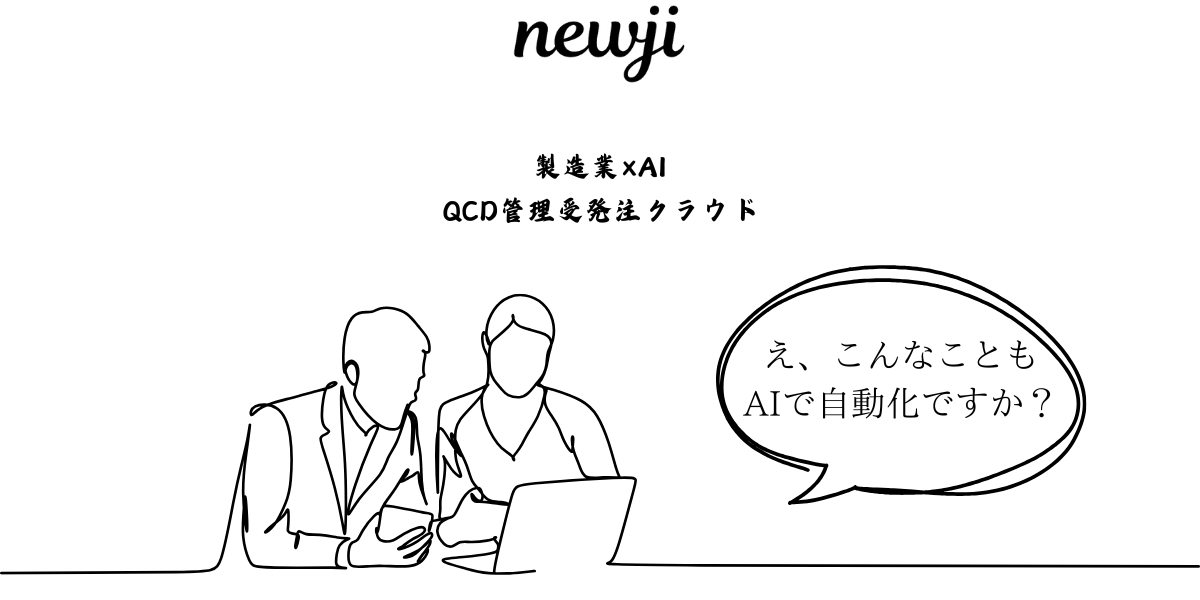
Manufacturing Process of Automatic Water Dispensers and Improvement in Water Volume Control Functions
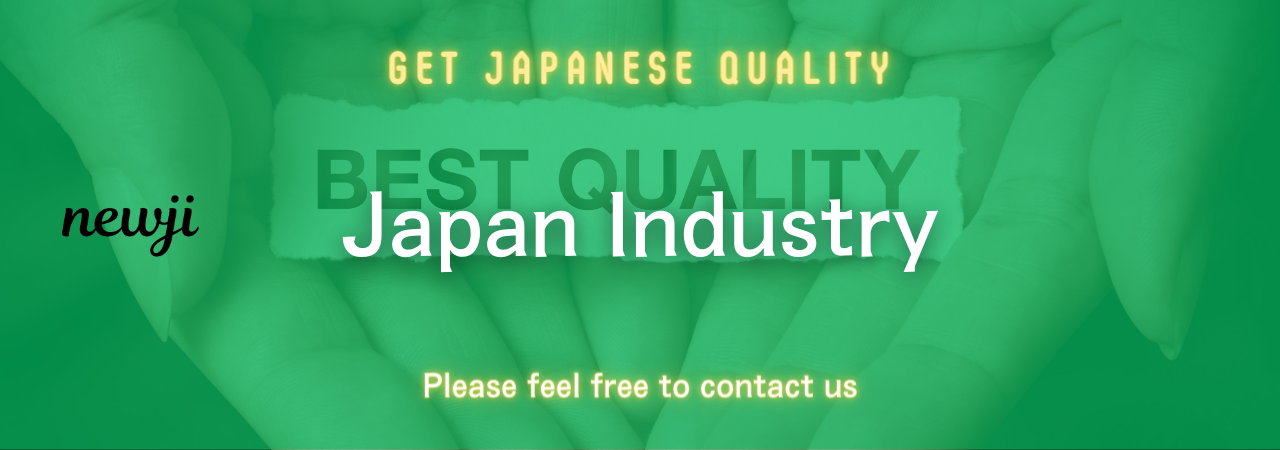
Automatic water dispensers have become an essential feature in various settings such as offices, homes, and public places. They provide a convenient way to access clean water, ensuring hydration with minimal effort. Let’s dive into the manufacturing process of these innovative appliances and explore how advancements in water volume control functions have enhanced their efficiency.
目次
Understanding the Basics of Automatic Water Dispensers
Before we delve into the manufacturing process, it’s crucial to understand what automatic water dispensers are and how they function. An automatic water dispenser typically consists of a reservoir for water storage, sensors to detect the cup placement, and a dispensing mechanism that releases water based on user input.
Types of Automatic Water Dispensers
There are several types of automatic water dispensers available in the market. Each type serves a specific purpose and caters to different user needs.
1. **Bottleless Water Dispensers**: These dispensers are connected directly to a water source and are equipped with advanced filtration systems to ensure the water is clean and safe for consumption.
2. **Bottled Water Dispensers**: These rely on pre-filled water bottles and are often used in regions where tap water might not be safe to drink.
3. **Touchless Water Dispensers**: Designed with hygiene in mind, these dispensers use infrared sensors to detect hand or cup presence, making them ideal for public places.
The Manufacturing Process: Step-by-Step
Creating an automatic water dispenser involves several stages, from designing the components to assembling and testing the final product. Here’s a breakdown of the key steps involved in the manufacturing process:
1. Designing the Components
The first step in manufacturing an automatic water dispenser is designing the components. Engineers and designers work together to create the blueprint of the dispenser, ensuring that it meets all safety and functionality standards.
– **Reservoir Design**: The water reservoir must be designed to hold an adequate amount of water while maintaining a compact form factor.
– **Sensor Placement**: Sensors must be strategically placed to accurately detect cup placement and user interactions.
– **Dispensing Mechanism**: The mechanism that releases water needs to be efficient and reliable, preventing leaks and ensuring consistent water flow.
2. Selecting Materials
Choosing the right materials is crucial for ensuring the durability and safety of the water dispenser. Common materials used include:
– **Food-Grade Plastics**: Often used for the reservoir and exterior parts to ensure the water remains safe to drink.
– **Stainless Steel**: Used for internal components and the dispensing nozzle to prevent corrosion and maintain cleanliness.
– **Electronic Components**: Sensors, microcontrollers, and other electronic parts are selected based on their performance and compatibility with the dispenser design.
3. Fabricating the Parts
Once the design is finalized and materials are selected, the next step is to fabricate the individual parts. This process involves:
– **Injection Molding**: Used to create plastic parts like the reservoir and outer casing.
– **Metal Fabrication**: Techniques such as stamping and cutting are used to create metal components.
– **Circuit Board Assembly**: Assembling the electronic components onto printed circuit boards (PCBs) that will control the dispenser’s functions.
4. Assembling the Dispenser
The assembly process involves putting together all the fabricated parts. This includes:
– **Mounting the Reservoir**: Securing the reservoir in its designated place within the dispenser casing.
– **Installing Sensors**: Placing the sensors at strategic locations to ensure proper functionality.
– **Connecting Electronics**: Integrating the electronic components and wiring them to the main control unit.
5. Quality Control and Testing
Quality control is a critical step to ensure that every dispenser meets the required standards. This involves:
– **Functionality Testing**: Checking the dispenser to ensure it releases water correctly when sensors detect user input.
– **Durability Testing**: Assessing the durability of components under various conditions to ensure longevity.
– **Safety Checks**: Ensuring that all materials and components meet safety regulations and standards.
Advancements in Water Volume Control Functions
One of the significant improvements in modern automatic water dispensers is the advancement in water volume control functions. This feature allows users to control the amount of water dispensed accurately, making these devices more efficient and convenient.
Importance of Accurate Water Volume Control
Accurate water volume control is essential for several reasons:
– **Preventing Spillage**: Ensuring the right amount of water is dispensed can prevent overflows and spills, maintaining cleanliness and reducing waste.
– **Customizable Portions**: Users can select specific water amounts, catering to their needs, whether it’s filling a cup, bottle, or cooking pot.
– **Energy Efficiency**: Reducing unnecessary water flow conserves energy, making the dispenser more environmentally friendly.
Technologies Enhancing Water Volume Control
Innovations in technology have significantly enhanced water volume control functions in automatic water dispensers. Some of these technologies include:
– **Precision Sensors**: Advanced sensors can detect the exact amount of water required, ensuring precise control over water flow.
– **Programmable Settings**: Users can program specific water amounts based on their preferences, offering a personalized experience.
– **Smart Controls**: Integration with smart home systems allows users to control the dispenser remotely through mobile apps or voice commands.
Benefits of Improved Water Volume Control
The advancements in water volume control functions bring several benefits to users and manufacturers alike:
– **User Satisfaction**: Enhanced control over water dispensing improves user satisfaction, providing a more convenient and tailored experience.
– **Reduced Waste**: Accurate water dispensing minimizes water waste, contributing to conservation efforts.
– **Brand Competitiveness**: Manufacturers that incorporate advanced water control features can stand out in the competitive market, attracting more customers.
In conclusion, the manufacturing process of automatic water dispensers is a complex yet fascinating journey that combines design, materials selection, fabrication, assembly, and rigorous testing. Improvements in water volume control functions play a vital role in enhancing the efficiency, convenience, and user satisfaction of these devices. As technology continues to evolve, we can expect even more innovations in the realm of automatic water dispensers, making them indispensable in our daily lives.
資料ダウンロード
QCD調達購買管理クラウド「newji」は、調達購買部門で必要なQCD管理全てを備えた、現場特化型兼クラウド型の今世紀最高の購買管理システムとなります。
ユーザー登録
調達購買業務の効率化だけでなく、システムを導入することで、コスト削減や製品・資材のステータス可視化のほか、属人化していた購買情報の共有化による内部不正防止や統制にも役立ちます。
NEWJI DX
製造業に特化したデジタルトランスフォーメーション(DX)の実現を目指す請負開発型のコンサルティングサービスです。AI、iPaaS、および先端の技術を駆使して、製造プロセスの効率化、業務効率化、チームワーク強化、コスト削減、品質向上を実現します。このサービスは、製造業の課題を深く理解し、それに対する最適なデジタルソリューションを提供することで、企業が持続的な成長とイノベーションを達成できるようサポートします。
オンライン講座
製造業、主に購買・調達部門にお勤めの方々に向けた情報を配信しております。
新任の方やベテランの方、管理職を対象とした幅広いコンテンツをご用意しております。
お問い合わせ
コストダウンが利益に直結する術だと理解していても、なかなか前に進めることができない状況。そんな時は、newjiのコストダウン自動化機能で大きく利益貢献しよう!
(Β版非公開)