- お役立ち記事
- Manufacturing Process of Automatic Whisk and Motor Performance Improvement
Manufacturing Process of Automatic Whisk and Motor Performance Improvement
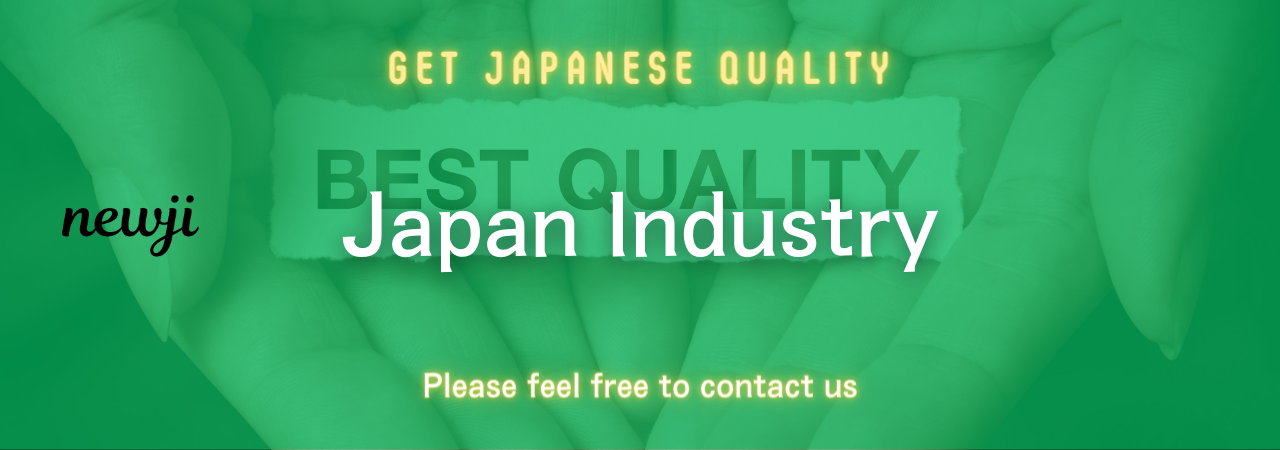
The manufacturing process of an automatic whisk involves several stages that require precision and quality control. By understanding these stages, we can appreciate how the performance of the motor used in an automatic whisk can be improved to enhance its efficiency and durability.
目次
Material Selection
Choosing the right materials is the first step in manufacturing an automatic whisk. The body of the whisk is typically made of high-quality plastic or stainless steel. The handles need to be ergonomically designed for comfort and durability.
Plastic parts are usually made from polyethylene or polypropylene, known for their strength and resistance to wear and tear. Stainless steel parts need to be corrosion-resistant, making them suitable for frequent use in kitchen environments.
Motor Components
The motor is the heart of the automatic whisk. It is essential to select components that can handle the demands of continuous use. Small DC motors are commonly used due to their efficiency and reliability.
These motors comprise several key parts:
1. **Stator**: The stationary part of the motor that generates a magnetic field.
2. **Rotor**: The rotating part that converts the magnetic field into mechanical movement.
3. **Commutator**: Conducts electricity between the stationary and rotating parts.
4. **Brushes**: Ensure electrical contact with the commutator.
**Bearings** and **gears** must also be selected with care, ensuring they can withstand the mechanical stresses of operation.
Design and Prototyping
Before mass production, manufacturers create prototypes to test the design’s functionality and performance. Modern technology allows for computer-aided design (CAD) software to create digital models.
Prototyping involves creating a physical model using 3D printing or traditional machining. This model is then tested under various conditions to ensure it can withstand the rigors of actual use.
Testing focuses on:
1. Durability
2. Efficiency
3. Safety
Any issues identified during prototyping are addressed before moving to the production stage.
Performance Testing of the Motor
During the prototyping stage, the motor’s performance is vigorously tested. Factors such as torque, speed, and electrical efficiency are evaluated. This helps ensure the motor can handle the whisk’s required workload without overheating or failing prematurely.
Improvements to motor performance may involve:
1. Using more efficient **brushless motors** to reduce wear and tear.
2. Optimizing the **gear mechanism** to improve torque without compromising speed.
3. Enhancing the **cooling system** to prevent overheating during prolonged use.
Manufacturing and Assembly
Once the design passes all tests, the manufacturing process begins. The parts are usually produced in specialized factories. Plastic parts are fabricated through injection molding, while metal parts are machined or stamped.
The assembly process is often automated to ensure consistency and precision. The steps typically include:
1. **Mounting the motor** into the whisk body.
2. **Connecting electrical components** like the switch and power cord.
3. **Securing the whisk attachments** to the motor shaft.
During assembly, quality control checks are performed at each step to detect any defects or issues. Techniques like **vision systems** can automatically verify the correct assembly of components.
Final Quality Control
Before the automatic whisks are packaged and shipped, they undergo rigorous final quality control checks. This may involve:
1. Electrical tests to ensure the motor operates correctly.
2. Mechanical tests to confirm the whisk moves smoothly and without unusual noise.
3. Safety tests to verify compliance with international standards.
Any product that fails these checks is either reworked or scrapped to maintain high-quality standards.
Packaging and Shipping
Once quality control is complete, the automatic whisks are packaged for shipping. Packaging needs to protect the product during transit and be easy for consumers to open. Manufacturers often use recyclable materials to minimize environmental impact.
The packaged products are then transported to distribution centers before being delivered to retailers or directly to consumers.
Improving Motor Performance
Enhancing the motor performance of an automatic whisk can involve several strategies. By focusing on the motor’s design, materials, and cooling mechanisms, manufacturers can create more efficient and durable products.
Enhanced Motor Design
One approach is to optimize the motor’s design. This can include:
1. **Reducing friction** by using high-quality bearings and lubricants.
2. **Minimizing weight** to make the whisk lighter and more comfortable to use.
3. **Improving balance** to reduce vibrations and noise during operation.
Using advanced design software, engineers can simulate various configurations to find the optimal motor design.
Using Superior Materials
Selecting superior materials for the motor components can significantly enhance performance. Using high-grade steel or ceramic for bearings can reduce wear and extend the motor’s lifespan.
The choice of magnets in the motor can also impact performance. Rare-earth magnets like neodymium can provide stronger magnetic fields, improving efficiency and power output.
Advanced Cooling Systems
Overheating is a common issue in small motors used in appliances like automatic whisks. Implementing advanced cooling systems can help manage heat better. Techniques can include:
1. **Using heat sinks** to dissipate heat effectively.
2. **Integrating thermal sensors** that can shut down the motor if it overheats.
3. **Improving airflow** within the motor housing to facilitate cooling.
These strategies can prevent damage caused by overheating, making the whisk more reliable.
Conclusion
The manufacturing process of an automatic whisk involves multiple stages, from material selection to final quality control, each crucial in ensuring a durable and efficient product. By focusing on improving motor performance through better design, superior materials, and advanced cooling systems, manufacturers can create automatic whisks that meet the needs of consumers and stand out in the market.
資料ダウンロード
QCD調達購買管理クラウド「newji」は、調達購買部門で必要なQCD管理全てを備えた、現場特化型兼クラウド型の今世紀最高の購買管理システムとなります。
ユーザー登録
調達購買業務の効率化だけでなく、システムを導入することで、コスト削減や製品・資材のステータス可視化のほか、属人化していた購買情報の共有化による内部不正防止や統制にも役立ちます。
NEWJI DX
製造業に特化したデジタルトランスフォーメーション(DX)の実現を目指す請負開発型のコンサルティングサービスです。AI、iPaaS、および先端の技術を駆使して、製造プロセスの効率化、業務効率化、チームワーク強化、コスト削減、品質向上を実現します。このサービスは、製造業の課題を深く理解し、それに対する最適なデジタルソリューションを提供することで、企業が持続的な成長とイノベーションを達成できるようサポートします。
オンライン講座
製造業、主に購買・調達部門にお勤めの方々に向けた情報を配信しております。
新任の方やベテランの方、管理職を対象とした幅広いコンテンツをご用意しております。
お問い合わせ
コストダウンが利益に直結する術だと理解していても、なかなか前に進めることができない状況。そんな時は、newjiのコストダウン自動化機能で大きく利益貢献しよう!
(Β版非公開)