- お役立ち記事
- Manufacturing Process of Backflow Preventers and Anti-reverse Flow Function Enhancement
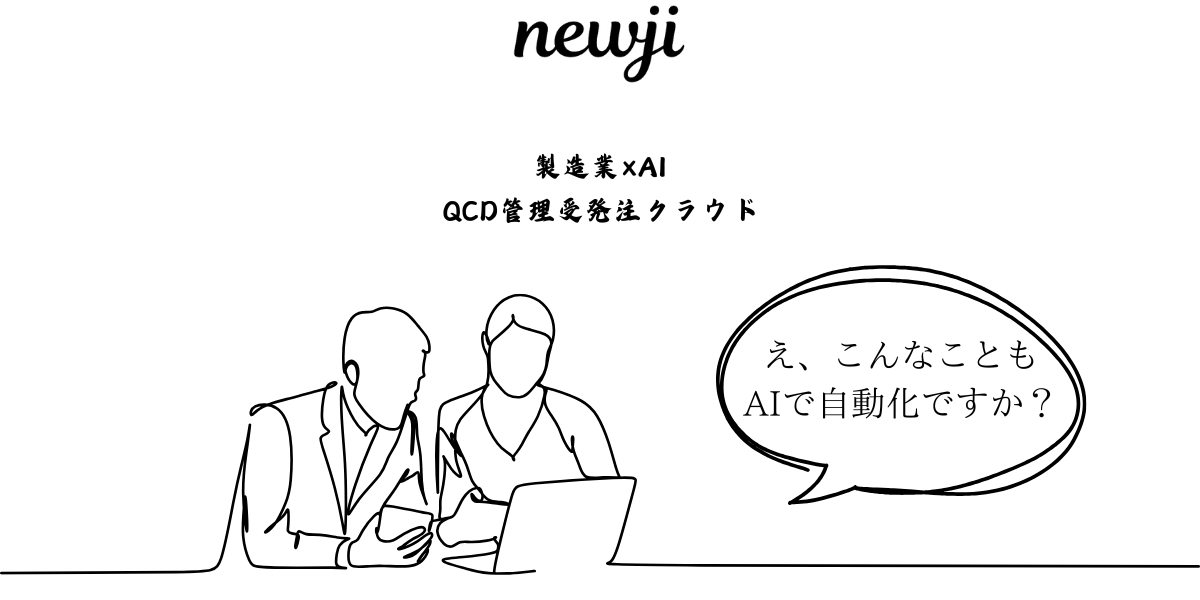
Manufacturing Process of Backflow Preventers and Anti-reverse Flow Function Enhancement
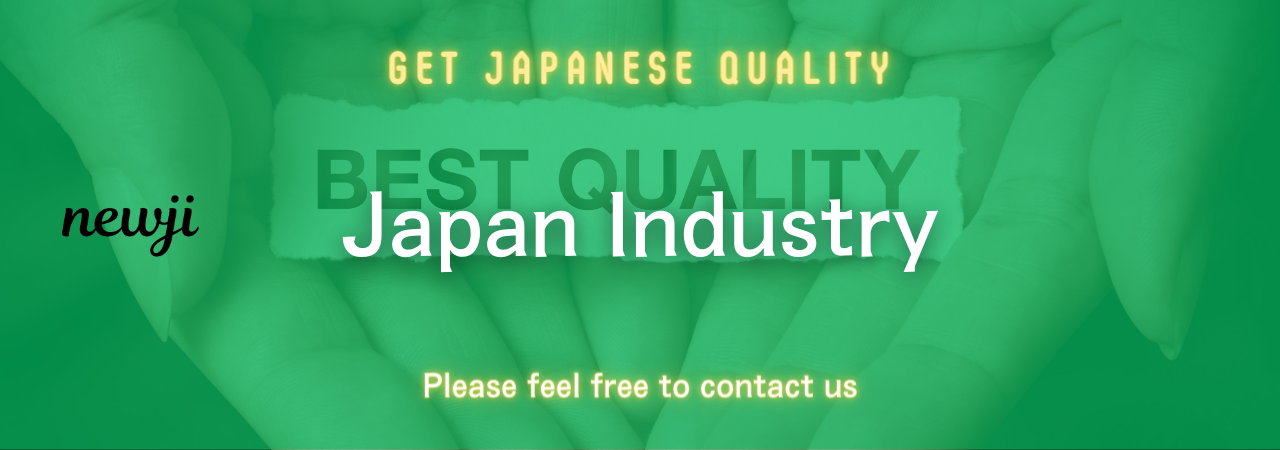
Backflow preventers are essential components in plumbing systems, ensuring that water flows in a single direction and safeguarding against contamination.
Their manufacturing process involves multiple steps and adherence to strict quality standards.
This article delves into the intricacies of how these devices are made and highlights advances in their anti-reverse flow function.
目次
The Importance of Backflow Preventers
Backflow preventers play a crucial role in protecting public health.
They prevent contaminated water from reversing direction and entering the clean water supply.
Without them, there is a risk of pollutants, chemicals, and harmful agents infiltrating potable water sources.
Materials Used in Manufacturing
Backflow preventers are made from durable and high-quality materials to ensure longevity and reliability.
Common materials include:
– Brass: Known for its corrosion resistance and strength.
– Stainless Steel: Offers durability and resistance to rust.
– PVC: Lightweight and resistant to chemicals.
The choice of material depends on the specific application and environmental conditions.
Manufacturing Steps
Design and Engineering
The first step in manufacturing backflow preventers is designing the device.
Engineers use computer-aided design (CAD) software to create detailed blueprints.
These designs must comply with industry standards and regulations to ensure they function properly.
Material Selection and Procurement
Once the design is finalized, manufacturers select appropriate materials.
They source high-quality brass, stainless steel, or PVC from reputable suppliers.
This step is critical to ensure the preventer’s durability and effectiveness.
Component Fabrication
With materials in hand, manufacturers proceed to fabricate the individual components.
This process involves cutting, shaping, and forming the raw materials into the desired shapes and sizes.
Precision machining tools like lathes and milling machines are often used to achieve accurate dimensions.
Assembly
After fabrication, the individual parts are assembled.
Skilled technicians put together the components, ensuring a precise fit.
Assembly may involve welding, threading, or snap-fit connections, depending on the material and design.
Quality Control and Testing
Quality control is a critical aspect of the manufacturing process.
Each backflow preventer undergoes rigorous testing to ensure it meets performance standards.
Tests include:
– Leak Testing: Ensuring there are no leaks when the device is pressurized.
– Flow Testing: Verifying that water flows correctly through the preventer.
– Durability Testing: Subjecting the device to conditions it will encounter during its lifespan.
Any defects or issues are addressed before the product is approved for distribution.
Enhancing Anti-reverse Flow Function
Manufacturers continually strive to improve the anti-reverse flow function of backflow preventers.
Several advancements contribute to this enhancement:
Advanced Valve Mechanisms
One significant improvement is the development of advanced valve mechanisms.
These modern valves are designed for quick response and robust sealing.
They ensure that any backflow pressure triggers an immediate closure, preventing contamination.
Smart Technology Integration
Another leap forward is the integration of smart technology.
Some backflow preventers now feature sensors and IoT connectivity.
These smart devices can monitor water pressure and flow in real-time.
If an anomaly is detected, the system can alert maintenance personnel or automatically shut off the water supply.
Improved Sealing Materials
The sealing materials used in backflow preventers have also seen advancements.
New synthetic rubber compounds and advanced polymers provide better resistance to wear and chemical exposure.
These materials ensure a consistent and long-lasting seal, enhancing the device’s reliability.
Modular Designs
Modular designs allow for easier maintenance and replacement of parts.
Instead of replacing the entire unit, only the affected component needs to be swapped out.
This approach not only extends the lifespan of the device but also reduces maintenance costs.
Environmental Considerations
In addition to functional improvements, there is a growing emphasis on environmental considerations in the manufacturing process.
Efforts include:
– Reducing Waste: Implementing practices to minimize material waste during fabrication.
– Recycling: Using recyclable materials and promoting end-of-life recycling of backflow preventers.
– Energy Efficiency: Adopting energy-efficient processes and equipment to reduce the carbon footprint.
Conclusion
The manufacturing process of backflow preventers is a meticulous and multi-faceted one, ensuring the devices are reliable and effective.
From material selection to final assembly, each step is critical to produce a high-quality product.
Continuous advancements in technology and materials further enhance their anti-reverse flow function, offering better protection for water supplies.
As manufacturers adopt more sustainable practices, the future of backflow preventers looks promising, ensuring safety and reliability for years to come.
資料ダウンロード
QCD調達購買管理クラウド「newji」は、調達購買部門で必要なQCD管理全てを備えた、現場特化型兼クラウド型の今世紀最高の購買管理システムとなります。
ユーザー登録
調達購買業務の効率化だけでなく、システムを導入することで、コスト削減や製品・資材のステータス可視化のほか、属人化していた購買情報の共有化による内部不正防止や統制にも役立ちます。
NEWJI DX
製造業に特化したデジタルトランスフォーメーション(DX)の実現を目指す請負開発型のコンサルティングサービスです。AI、iPaaS、および先端の技術を駆使して、製造プロセスの効率化、業務効率化、チームワーク強化、コスト削減、品質向上を実現します。このサービスは、製造業の課題を深く理解し、それに対する最適なデジタルソリューションを提供することで、企業が持続的な成長とイノベーションを達成できるようサポートします。
オンライン講座
製造業、主に購買・調達部門にお勤めの方々に向けた情報を配信しております。
新任の方やベテランの方、管理職を対象とした幅広いコンテンツをご用意しております。
お問い合わせ
コストダウンが利益に直結する術だと理解していても、なかなか前に進めることができない状況。そんな時は、newjiのコストダウン自動化機能で大きく利益貢献しよう!
(Β版非公開)