- お役立ち記事
- Manufacturing Process of Bicycle Helmets and Innovations in Impact-Absorbing Materials
月間76,176名の
製造業ご担当者様が閲覧しています*
*2025年3月31日現在のGoogle Analyticsのデータより
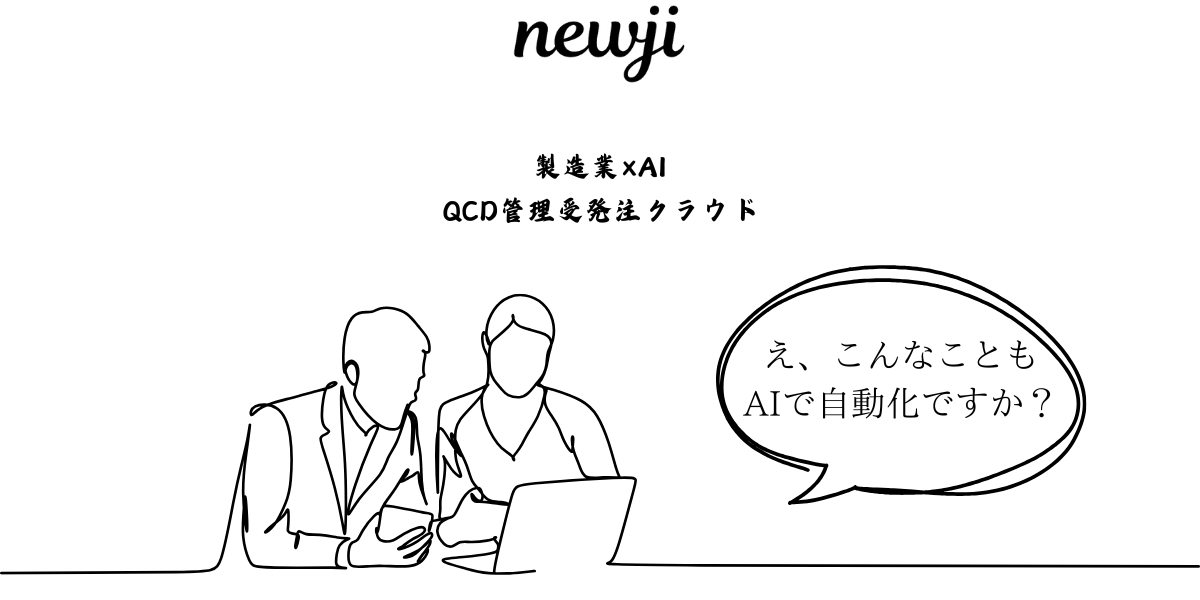
Manufacturing Process of Bicycle Helmets and Innovations in Impact-Absorbing Materials
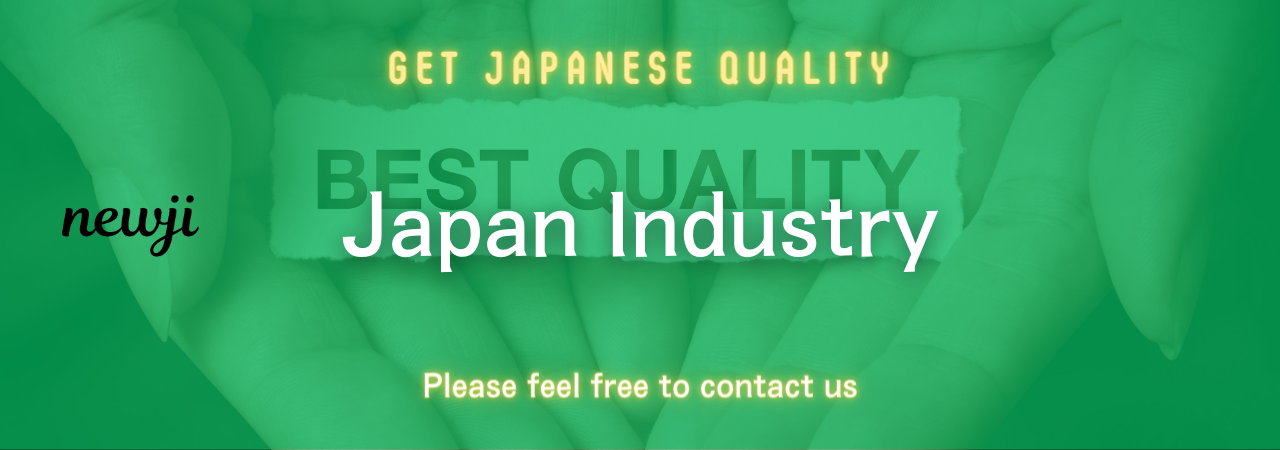
Bicycle helmets are essential for keeping cyclists safe.
The manufacturing process of these helmets is intricate and involves multiple steps to ensure reliability and effectiveness.
In recent years, innovations in impact-absorbing materials have significantly improved the protective quality of bicycle helmets.
Let’s delve into how bicycle helmets are made and examine some of the latest advancements in impact-absorbing materials.
目次
Basic Components of Bicycle Helmets
Before we discuss the manufacturing process, it’s essential to understand the basic components of a bicycle helmet.
A typical bicycle helmet consists of an outer shell, foam liner, padding, retention system, and ventilation.
Outer Shell
The outer shell is usually made from polycarbonate or similar plastic materials.
Its primary function is to distribute the force of an impact over a larger area, preventing punctures and maintaining structural integrity.
Foam Liner
The foam liner, typically made from Expanded Polystyrene (EPS) foam, is responsible for absorbing the shock during a collision.
This compressible material breaks down upon impact, dissipating energy that would otherwise reach the rider’s head.
Padding
Padding inside the helmet provides comfort and a better fit.
Although it does contribute to some degree of impact absorption, its primary purpose is to improve the wearability of the helmet.
Retention System
The retention system, including the straps and buckles, holds the helmet securely on the rider’s head.
A proper fit is crucial for ensuring that the helmet functions correctly in the event of a crash.
Ventilation
Ventilation holes help manage heat and moisture, making the helmet more comfortable to wear, especially during long rides.
Steps in the Manufacturing Process
Step 1: Designing
The design phase involves conceptualizing the helmet’s shape, features, and safety standards.
Computer-aided design (CAD) software is often used to create detailed models and simulations.
Step 2: Creating the Molds
Once the design is finalized, molds are created to form the various parts of the helmet.
These molds will be used to shape the outer shell and the foam liner.
Step 3: Forming the Outer Shell
The material for the outer shell is heated and vacuum-formed over the mold.
This process ensures the shell adopts the desired shape and provides a strong foundation for the helmet.
Step 4: Manufacturing the Foam Liner
EPS beads are introduced into the liner mold and subjected to heat, causing them to expand and fuse together.
This forms a sturdy yet lightweight foam liner that fits perfectly within the outer shell.
Step 5: Assembly
The foam liner is bonded to the outer shell using adhesive.
Straps, padding, and other components are then assembled to complete the helmet.
Step 6: Quality Control
Each helmet undergoes rigorous testing to ensure it meets safety standards.
This includes impact testing, penetration tests, and strap strength tests.
Innovations in Impact-Absorbing Materials
Traditional EPS foam has been the standard in helmet manufacturing for years.
However, recent innovations have introduced new materials and technologies that further enhance impact absorption and overall safety.
Multi-Directional Impact Protection System (MIPS)
One of the most significant advancements is the Multi-Directional Impact Protection System (MIPS).
MIPS technology involves a low-friction layer inside the helmet that allows it to slide relative to the head upon impact.
This reduces rotational forces, which are a common cause of brain injuries during a crash.
Expanded Polypropylene (EPP) Foam
Unlike EPS, Expanded Polypropylene (EPP) foam is more resilient.
It can withstand multiple impacts without losing its protective properties, making it ideal for helmets designed for high-risk activities.
Koroyd Technology
Koroyd technology utilizes a unique cylindrical structure made from thermoplastic.
This structure crumples upon impact, absorbing and dissipating energy more efficiently than traditional foams.
Composite Materials
New composite materials combine different types of fibers and resins to create a stronger, lighter helmet.
These helmets offer better protection and are more comfortable to wear for extended periods.
Environmental Considerations
As awareness of environmental issues grows, helmet manufacturers are exploring sustainable materials and processes.
Biodegradable foams and recyclable components are being developed to reduce the environmental impact of helmet production.
Recyclable EPS
Some companies are working on creating recyclable EPS foam.
This innovation allows the material to be reused in new products, minimizing waste.
Organic Foams
Researchers are also investigating the use of organic materials, such as mushroom mycelium and plant-based foams, for making helmet liners.
These materials offer similar protective qualities while being more environmentally friendly.
Future Trends
The future of bicycle helmet manufacturing looks promising, with continuous advancements in materials and technology.
Smart helmets equipped with sensors, communication systems, and advanced safety features are on the horizon.
These innovations aim to provide not only protection but also enhanced riding experiences.
In summary, the manufacturing process of bicycle helmets is a complex and meticulously controlled procedure that aims to provide maximum safety for cyclists.
Innovations in impact-absorbing materials, such as MIPS and Koroyd, have significantly enhanced the effectiveness of helmets.
As sustainability becomes a priority, future developments will likely focus on environmentally friendly materials and production methods.
By staying informed about these advancements, cyclists can make better choices and stay safer on the road.
資料ダウンロード
QCD管理受発注クラウド「newji」は、受発注部門で必要なQCD管理全てを備えた、現場特化型兼クラウド型の今世紀最高の受発注管理システムとなります。
ユーザー登録
受発注業務の効率化だけでなく、システムを導入することで、コスト削減や製品・資材のステータス可視化のほか、属人化していた受発注情報の共有化による内部不正防止や統制にも役立ちます。
NEWJI DX
製造業に特化したデジタルトランスフォーメーション(DX)の実現を目指す請負開発型のコンサルティングサービスです。AI、iPaaS、および先端の技術を駆使して、製造プロセスの効率化、業務効率化、チームワーク強化、コスト削減、品質向上を実現します。このサービスは、製造業の課題を深く理解し、それに対する最適なデジタルソリューションを提供することで、企業が持続的な成長とイノベーションを達成できるようサポートします。
製造業ニュース解説
製造業、主に購買・調達部門にお勤めの方々に向けた情報を配信しております。
新任の方やベテランの方、管理職を対象とした幅広いコンテンツをご用意しております。
お問い合わせ
コストダウンが利益に直結する術だと理解していても、なかなか前に進めることができない状況。そんな時は、newjiのコストダウン自動化機能で大きく利益貢献しよう!
(β版非公開)