- お役立ち記事
- Manufacturing Process of Bicycles and Improvement in Frame Rigidity
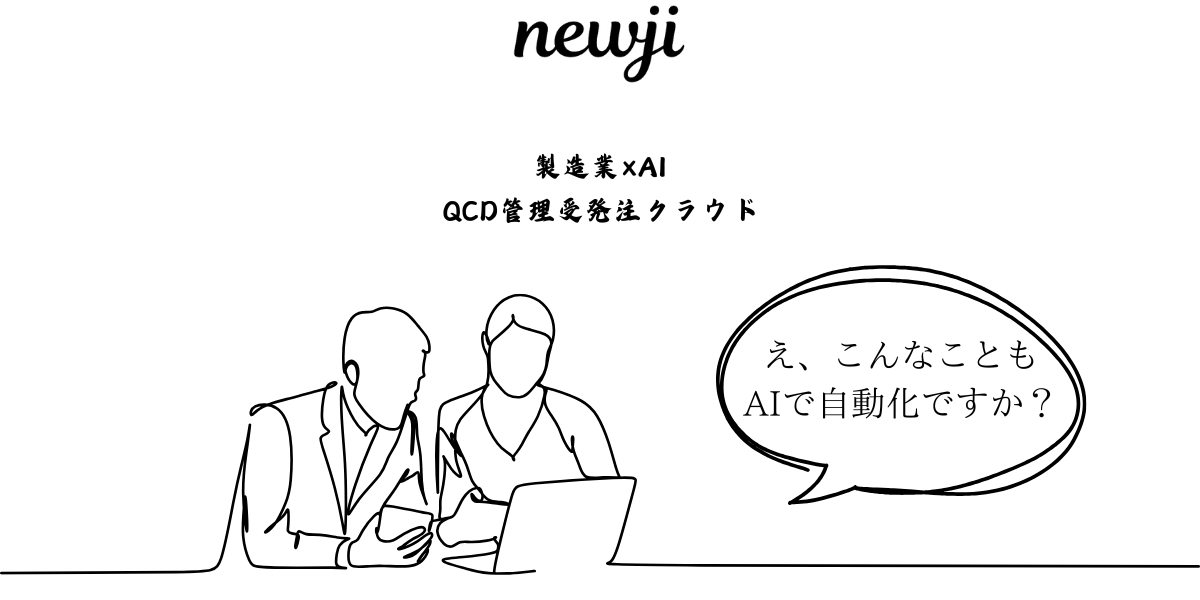
Manufacturing Process of Bicycles and Improvement in Frame Rigidity
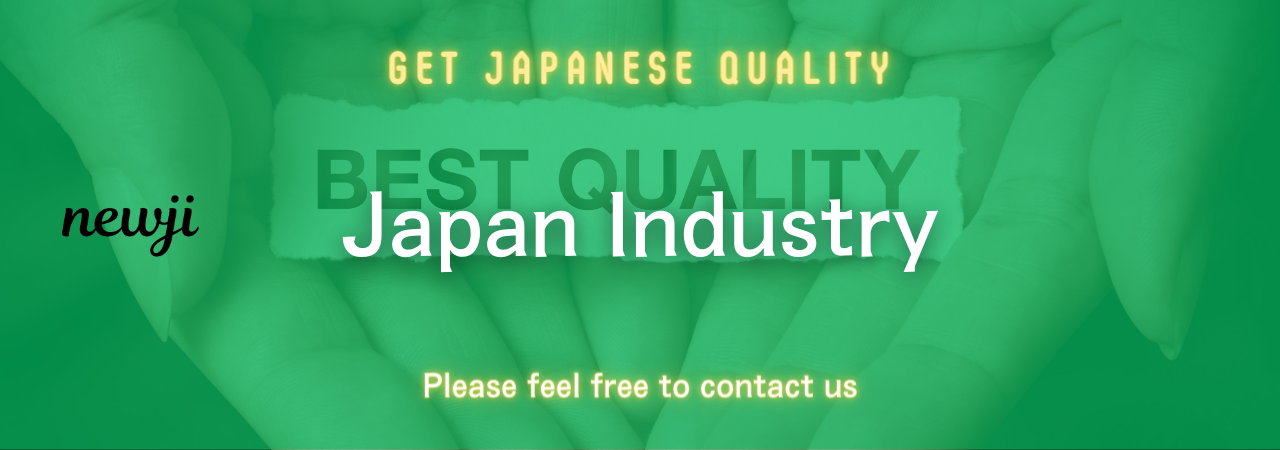
The bicycle is one of the most efficient forms of transportation, and its design has been meticulously refined over the years.
One of the key aspects that significantly affect the performance of a bicycle is the frame’s rigidity.
A rigid frame ensures better energy transfer, which translates to a more responsive and efficient ride.
In this article, we’ll explore the manufacturing process of bicycles and how improvements in frame rigidity have been achieved.
目次
The Manufacturing Process of Bicycles
The journey of a bicycle from a concept to a finished product involves several steps.
Design and Conceptualization
Before production begins, the bicycle design team creates detailed blueprints and 3D models.
These visual representations help in visualizing the final product and allow engineers to tweak and optimize the design for performance, weight, and aesthetics.
Advanced software is used to simulate stress tests and aerodynamics to ensure the bike meets high standards.
Material Selection
The choice of material is crucial in determining the frame’s rigidity and weight.
Common materials used in bicycle frames include steel, aluminum, titanium, and carbon fiber.
Each material has its unique properties:
– **Steel**: Durable but heavy, often used in traditional and touring bikes.
– **Aluminum**: Lightweight and resistant to corrosion, common in mid-range bicycles.
– **Titanium**: Combines strength and lightness but is more expensive.
– **Carbon Fiber**: Extremely light and stiff, used in high-performance racing bikes.
Cutting and Shaping
Once the material is chosen, it is cut into appropriate sizes.
For metal frames, tubes are cut using CNC (Computer Numerical Control) machines.
These machines ensure precision and consistency.
For carbon fiber frames, sheets are cut and laid into molds where they are shaped.
Welding and Joining
In metal frames, the cut tubes are joined using welding processes such as TIG (Tungsten Inert Gas) welding or brazing.
This stage requires skilled workers to ensure strong bonds.
For carbon fiber frames, the pre-shaped sheets are layered and bonded using high-pressure molding processes.
Heat Treatment and Cooling
After welding, metal frames undergo heat treatment to relieve stresses and increase strength.
The frames are heated in a furnace and then cooled at controlled rates.
This process helps in achieving the desired rigidity without making the metal brittle.
Painting and Coating
Once the frame is assembled, it goes through a finishing process where it is cleaned, primed, and painted.
Good quality paint not only enhances the aesthetic appeal but also protects the frame from corrosion.
Powder coating is another popular method for durable and long-lasting finishes.
Assembly
The final step in the manufacturing process is assembly.
Here, the frame is fitted with components such as forks, handlebars, brakes, gears, wheels, and tires.
Each part is meticulously checked and adjusted for proper alignment and function.
Improvement in Frame Rigidity
The rigidity of a bicycle frame is paramount for a stable ride and better energy efficiency.
Manufacturers have employed several strategies to enhance this crucial attribute.
Optimized Frame Geometry
The design of the frame plays a significant role in its rigidity.
Engineers use advanced CAD (Computer-Aided Design) tools to optimize the geometry for maximum stiffness.
A well-thought-out design ensures that the forces are well-distributed across the frame, minimizing flex.
Material Innovations
Innovations in materials have dramatically improved frame rigidity.
For example, carbon fiber composites have revolutionized the industry.
These materials can be layered in specific patterns to maximize stiffness while minimizing weight.
New alloys with higher strength-to-weight ratios have also contributed to more rigid and lighter frames.
Advanced Manufacturing Techniques
Cutting-edge manufacturing techniques like hydroforming and 3D printing allow for more complex and precise shapes.
Hydroforming involves using high-pressure fluid to shape metal into strong and lightweight forms.
3D printing enables custom geometries and internal structures that were previously impossible, allowing for enhanced rigidity.
Integration of Reinforcements
Reinforcements can be strategically placed in areas of high stress.
For example, engineers might integrate gussets or double-butted tubes where the frame experiences the most pressure.
These reinforcements add stiffness without significantly increasing weight.
Quality Control and Testing
Maintaining high standards of quality control ensures that the frames meet required rigidities.
Manufacturers employ rigorous testing procedures, including real-world testing and laboratory-based stress tests.
Frames are subjected to simulation of different riding conditions to ensure they can withstand various stresses.
The Impact of Rigidity on Performance
The improvements in frame rigidity have a direct impact on a bicycle’s performance.
A stiff frame allows for more efficient energy transfer from the rider’s pedaling to the wheels.
This reduces energy loss and improves acceleration and speed.
Additionally, a rigid frame provides better handling and stability, especially during high-speed descents and sharp turns.
Comfort vs. Performance
While a rigid frame offers numerous performance benefits, a balance must be struck between rigidity and ride comfort.
Excessive stiffness can lead to a harsh ride, which may be tiring over long distances.
Manufacturers often incorporate flexible materials or suspension systems in specific areas to absorb shocks and improve comfort without compromising overall rigidity.
Advancements in the manufacturing process and innovations in materials and design have significantly contributed to the improvement in frame rigidity.
Future developments will likely bring even more sophisticated techniques and materials, further enhancing the performance and riding experience for cyclists around the world.
資料ダウンロード
QCD調達購買管理クラウド「newji」は、調達購買部門で必要なQCD管理全てを備えた、現場特化型兼クラウド型の今世紀最高の購買管理システムとなります。
ユーザー登録
調達購買業務の効率化だけでなく、システムを導入することで、コスト削減や製品・資材のステータス可視化のほか、属人化していた購買情報の共有化による内部不正防止や統制にも役立ちます。
NEWJI DX
製造業に特化したデジタルトランスフォーメーション(DX)の実現を目指す請負開発型のコンサルティングサービスです。AI、iPaaS、および先端の技術を駆使して、製造プロセスの効率化、業務効率化、チームワーク強化、コスト削減、品質向上を実現します。このサービスは、製造業の課題を深く理解し、それに対する最適なデジタルソリューションを提供することで、企業が持続的な成長とイノベーションを達成できるようサポートします。
オンライン講座
製造業、主に購買・調達部門にお勤めの方々に向けた情報を配信しております。
新任の方やベテランの方、管理職を対象とした幅広いコンテンツをご用意しております。
お問い合わせ
コストダウンが利益に直結する術だと理解していても、なかなか前に進めることができない状況。そんな時は、newjiのコストダウン自動化機能で大きく利益貢献しよう!
(Β版非公開)