- お役立ち記事
- Manufacturing Process of Bottles and Thermal Insulation Enhancement
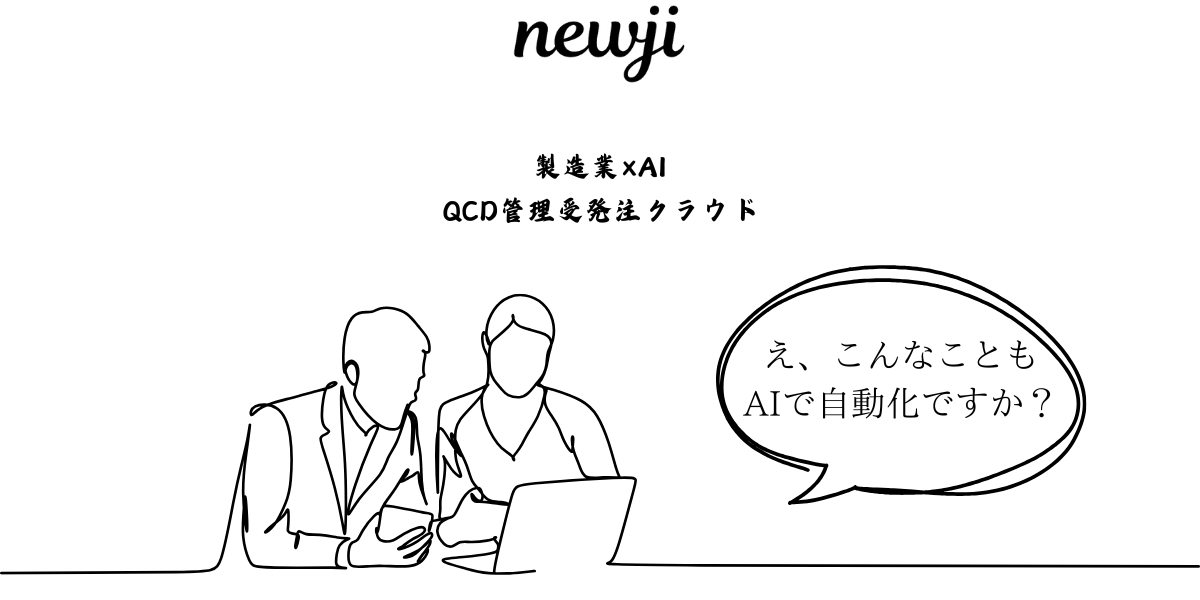
Manufacturing Process of Bottles and Thermal Insulation Enhancement
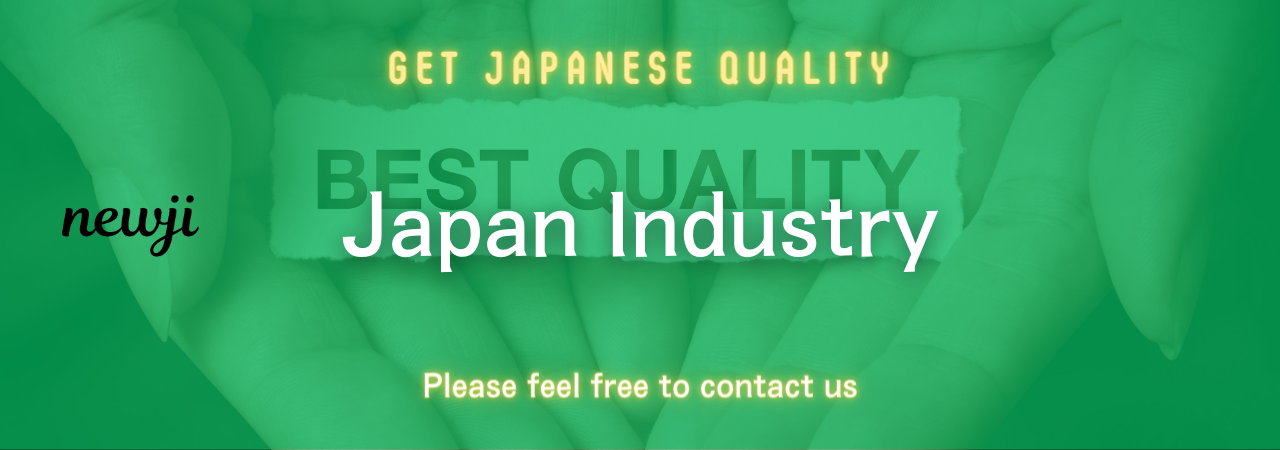
目次
Introduction to Bottle Manufacturing
The production of bottles is an intricate process that involves several steps, from designing to molding the final product.
Understanding the manufacturing process is essential for improving the thermal insulation efficiency of bottles, making them more competent in maintaining temperature.
In this article, we will delve into the stages of bottle production and discuss how to enhance thermal insulation.
Raw Material Selection
The choice of raw material is the initial step in bottle manufacturing.
Commonly used materials include glass, plastic, and metal.
Each of these materials has its own set of thermal properties that impact the bottle’s insulation capability.
Glass is a popular choice due to its inert nature and excellent heat resistance.
Plastic materials like PET (Polyethylene Terephthalate) are widely used for their durability and lightweight characteristics.
Metal, particularly stainless steel, offers superior insulation and is often selected for high-end insulated bottles.
Designing the Bottle
Design plays a crucial role in both functionality and aesthetics.
In this stage, engineers and designers work together to create a bottle that meets consumer needs while optimizing thermal insulation.
Special attention is given to the bottle’s shape and thickness.
An efficient design minimizes heat transfer, whether the content inside is hot or cold.
Advanced computer-aided design (CAD) software helps in visualizing and refining prototypes before moving on to production.
Importance of Bottle Closures
Bottle closures such as caps and lids are integral to thermal insulation.
Well-designed closures prevent air exchange between the bottle’s interior and exterior, maintaining the temperature of the contents for longer periods.
Silicone seals or double-walled caps are frequently used to enhance insulation properties.
They ensure that the bottle remains airtight, thereby preserving the temperature inside.
Production Process
Once the design is finalized, the next step is to manufacture the bottle itself.
This involves several stages, including preform molding, blowing, and final inspection.
Preform Molding
Preform molding is a preliminary step, especially in the production of plastic bottles.
Preforms are small, thick tubes that will later be expanded into full-sized bottles.
These preforms are created using injection molding machines, which heat the plastic resin before injecting it into molds.
Blow Molding
Blow molding is the process where preforms turn into the final bottle shape.
In stretch blow molding, the preform is reheated and placed into a blow mold.
Compressed air is then used to expand the preform into the mold cavities, creating the bottle’s shape.
For glass bottles, a similar technique is employed, often using high-temperature furnaces to soften the glass before blowing it into shape.
Quality Control and Inspection
Quality control is a critical phase that ensures each bottle meets industry standards and consumer expectations.
This stage involves multiple testing procedures to check for defects, structural integrity, and insulation properties.
Technological advancements have introduced automated systems for thorough inspection, making the process more reliable and efficient.
Non-destructive tests like ultrasound and infrared thermography help identify potential flaws without damaging the bottles.
Enhancing Thermal Insulation
Improving thermal insulation in bottles is a major focus for manufacturers aiming to offer better performance to consumers.
Choosing the Right Materials
Using double-walled construction, especially in metal bottles, significantly enhances insulation.
Double walls create a vacuum layer that minimizes heat transfer.
Another effective material is foam insulation, often used in plastic bottles to provide additional thermal barriers.
Coatings and Treatments
Insulating coatings play a vital role in enhancing thermal performance.
Reflective coatings can be applied to the exterior to reflect heat and light, thus maintaining the bottle’s temperature.
Additionally, interior coatings can prevent direct contact between the liquid and the bottle walls, enhancing overall insulation.
Advanced Manufacturing Techniques
Implementing advanced manufacturing techniques also helps in improving insulation.
For instance, vacuum insulation panels (VIPs) are increasingly incorporated in bottle designs.
VIPs consist of an inner core material surrounded by a vacuum, offering superior thermal resistance compared to traditional methods.
Innovative Cap Designs
Innovative designs in bottle caps significantly contribute to thermal insulation.
Caps fitted with specialized sealing mechanisms ensure minimal heat exchange.
Some designs even incorporate vacuum-sealed systems that offer near-perfect insulation.
Sustainability in Bottle Manufacturing
With the growing concern for environmental sustainability, manufacturers are now focusing on eco-friendly materials and processes.
Recycled materials are being used without compromising on insulation properties.
Moreover, research in biodegradable and compostable materials aims to minimize the environmental footprint of bottle production.
Energy-Efficient Processes
Modern manufacturing plants are employing energy-efficient processes to reduce the overall carbon footprint.
Energy recovery systems and optimization of heating and cooling cycles in furnaces ensure minimal energy wastage.
Consumer Education
Educating consumers about the proper use and maintenance of insulated bottles ensures they get the most out of their purchases.
Simple tips like pre-heating or pre-cooling the bottle before use can significantly enhance its thermal performance.
Conclusion
In conclusion, the manufacturing process of bottles is a complex yet fascinating journey from raw materials to the final product.
By focusing on design, material selection, and innovative manufacturing techniques, manufacturers can significantly improve the thermal insulation properties of bottles.
Such advancements not only boost consumer satisfaction but also contribute to sustainability efforts.
Understanding these processes provides valuable insights into how everyday items are optimized for better performance and environmental impact.
資料ダウンロード
QCD調達購買管理クラウド「newji」は、調達購買部門で必要なQCD管理全てを備えた、現場特化型兼クラウド型の今世紀最高の購買管理システムとなります。
ユーザー登録
調達購買業務の効率化だけでなく、システムを導入することで、コスト削減や製品・資材のステータス可視化のほか、属人化していた購買情報の共有化による内部不正防止や統制にも役立ちます。
NEWJI DX
製造業に特化したデジタルトランスフォーメーション(DX)の実現を目指す請負開発型のコンサルティングサービスです。AI、iPaaS、および先端の技術を駆使して、製造プロセスの効率化、業務効率化、チームワーク強化、コスト削減、品質向上を実現します。このサービスは、製造業の課題を深く理解し、それに対する最適なデジタルソリューションを提供することで、企業が持続的な成長とイノベーションを達成できるようサポートします。
オンライン講座
製造業、主に購買・調達部門にお勤めの方々に向けた情報を配信しております。
新任の方やベテランの方、管理職を対象とした幅広いコンテンツをご用意しております。
お問い合わせ
コストダウンが利益に直結する術だと理解していても、なかなか前に進めることができない状況。そんな時は、newjiのコストダウン自動化機能で大きく利益貢献しよう!
(Β版非公開)