- お役立ち記事
- Manufacturing Process of Brake Pads and Friction Performance Improvement
月間76,176名の
製造業ご担当者様が閲覧しています*
*2025年3月31日現在のGoogle Analyticsのデータより
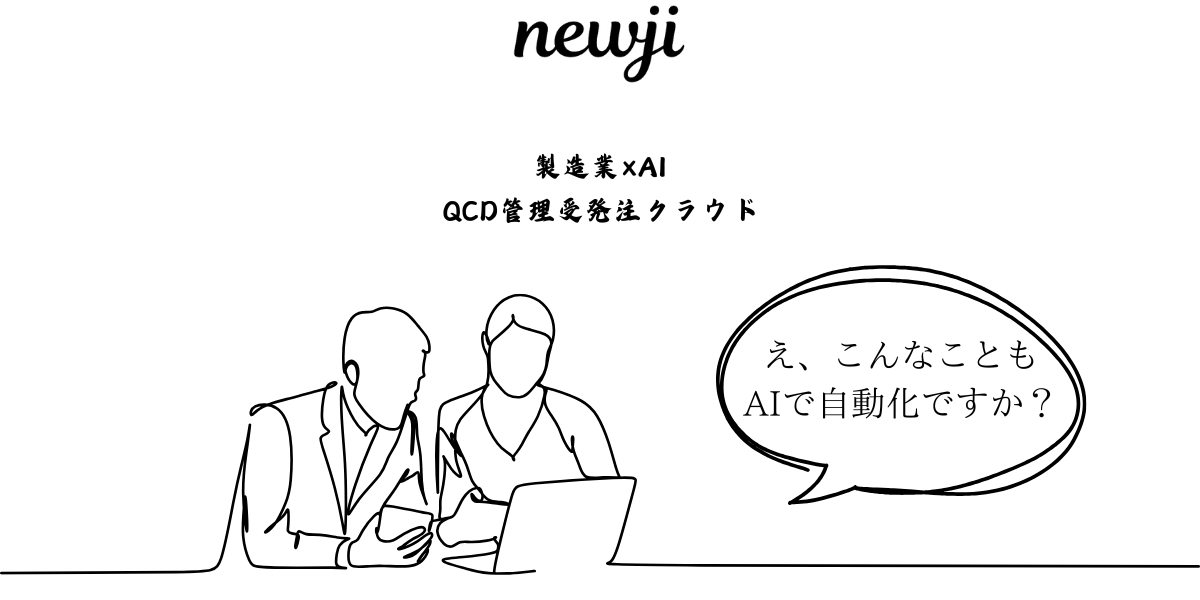
Manufacturing Process of Brake Pads and Friction Performance Improvement
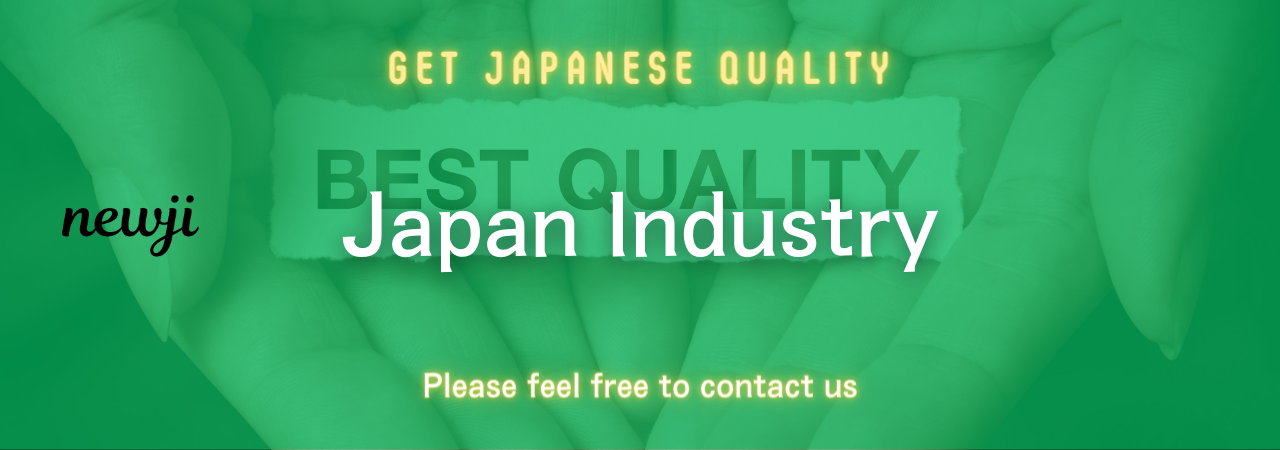
Brake pads are vital components in all sorts of vehicles, ensuring safety by allowing efficient braking.
Understanding the manufacturing process of brake pads offers insight into how they work and ways to improve their friction performance.
目次
Introduction to Brake Pad Manufacturing
The manufacturing of brake pads revolves around several key steps that transform raw materials into highly functional braking elements.
Each step is crucial in ensuring the final product meets the necessary performance standards.
Material Selection
The first step in the process involves selecting the right materials.
Brake pads typically include materials such as steel, rubber, resin, and various fibers.
These materials are chosen based on their stress-bearing capabilities and efficiency in generating friction.
Mixing and Compacting
Once the materials are chosen, they are mixed together to create a homogeneous blend.
This blend forms the basis of the friction material, which is crucial for the pad’s performance.
The mixed material is then compacted into a specific shape using a hydraulic press.
Compacting not only gives the brake pad its shape but also ensures it has the required density and strength.
Preforming and Heat Treatment
In this step, the compacted material, now in preform shape, undergoes heat treatment.
This process involves applying heat at controlled temperatures to harden the material.
It helps in binding the components together, giving the brake pad its durability and structural integrity.
Improving Friction Performance
Enhancing the friction performance of brake pads involves modifying both the manufacturing process and material composition.
Advanced Material Technology
Innovations in material technology significantly impact the friction performance of brake pads.
For example, using ceramic and carbon fibers can enhance heat resistance and reduce wear and tear.
These advanced materials help maintain consistent braking performance, especially under high-stress conditions.
Surface Treatments
Applying specialized surface treatments to brake pads can improve their friction characteristics.
Coatings like molybdenum disulfide reduce wear and improve heat distribution across the pad surface.
Such treatments help in maintaining the efficiency of the braking system over extended periods.
Optimizing the Manufacturing Process
Refinements in the manufacturing process, such as improved compacting techniques and precise heat treatment control, can also enhance friction performance.
Automation and computer-aided manufacturing (CAM) ensure consistent quality and precision in production, resulting in more reliable brake pads.
Testing and Quality Control
Before brake pads reach the market, they undergo rigorous testing and quality control processes to ensure they meet safety standards and performance benchmarks.
Performance Testing
Brake pads undergo various performance tests, including friction tests, wear tests, and thermal resistance tests.
These tests measure the efficiency, durability, and heat handling capabilities of the pads, ensuring they perform well under real-world conditions.
Quality Assurance
Quality assurance involves inspecting the brake pads for any defects or inconsistencies.
This step is crucial in maintaining the reliability and safety of the product.
Manufacturers often use automated systems and advanced imaging techniques to detect even the smallest flaws.
Environmental Considerations
Modern brake pad manufacturing also takes into account environmental impacts.
Efforts are made to use eco-friendly materials and manufacturing processes to reduce the carbon footprint and ensure sustainable production.
Recycling and Waste Management
Recycling plays a significant role in minimizing waste in brake pad manufacturing.
Many components of brake pads, such as steel fibers, can be recycled and reused in new products.
Effective waste management practices help in conserving resources and reducing environmental pollution.
Eco-Friendly Materials
Manufacturers are increasingly turning to eco-friendly materials, such as organic fibers and resins, which are biodegradable and less harmful to the environment.
These materials not only offer superior performance but also align with global sustainability goals.
Understanding the intricacies of brake pad manufacturing and methods to improve friction performance allows for the creation of safer and more efficient braking systems.
Continuous advancements in material technology and manufacturing processes play a pivotal role in shaping the future of automotive safety.
資料ダウンロード
QCD管理受発注クラウド「newji」は、受発注部門で必要なQCD管理全てを備えた、現場特化型兼クラウド型の今世紀最高の受発注管理システムとなります。
ユーザー登録
受発注業務の効率化だけでなく、システムを導入することで、コスト削減や製品・資材のステータス可視化のほか、属人化していた受発注情報の共有化による内部不正防止や統制にも役立ちます。
NEWJI DX
製造業に特化したデジタルトランスフォーメーション(DX)の実現を目指す請負開発型のコンサルティングサービスです。AI、iPaaS、および先端の技術を駆使して、製造プロセスの効率化、業務効率化、チームワーク強化、コスト削減、品質向上を実現します。このサービスは、製造業の課題を深く理解し、それに対する最適なデジタルソリューションを提供することで、企業が持続的な成長とイノベーションを達成できるようサポートします。
製造業ニュース解説
製造業、主に購買・調達部門にお勤めの方々に向けた情報を配信しております。
新任の方やベテランの方、管理職を対象とした幅広いコンテンツをご用意しております。
お問い合わせ
コストダウンが利益に直結する術だと理解していても、なかなか前に進めることができない状況。そんな時は、newjiのコストダウン自動化機能で大きく利益貢献しよう!
(β版非公開)