- お役立ち記事
- Manufacturing Process of Car Batteries and Energy Efficiency Improvement
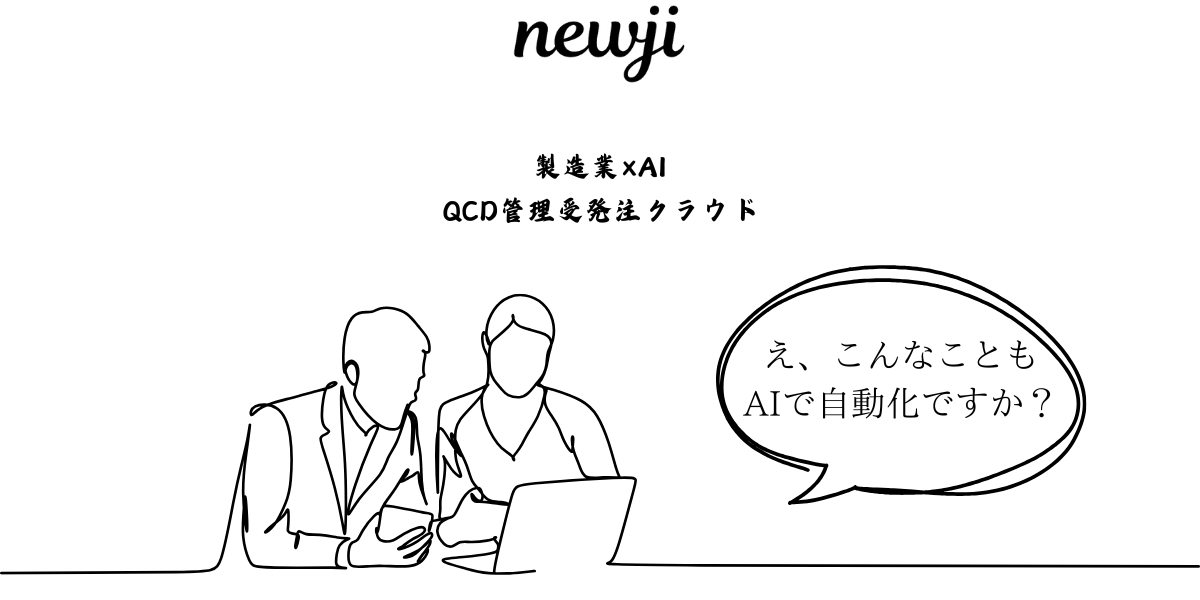
Manufacturing Process of Car Batteries and Energy Efficiency Improvement
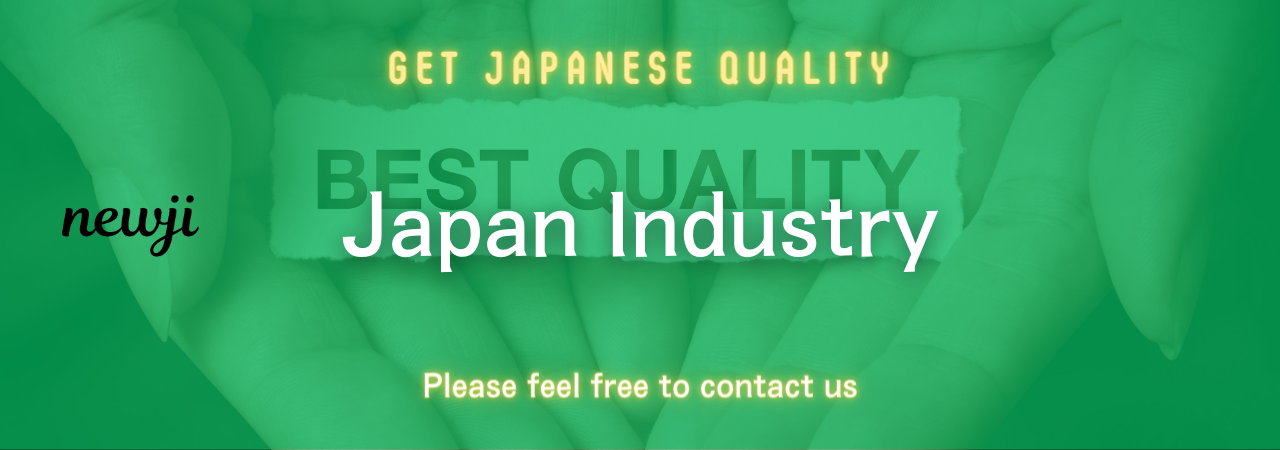
Car batteries play a crucial role in powering vehicles, ensuring they run smoothly and efficiently. Understanding the manufacturing process of car batteries and how to improve energy efficiency during their production can help us move towards a more sustainable future.
目次
Understanding Car Battery Manufacturing
The journey of a car battery starts with the extraction of raw materials. These materials include lead, sulfuric acid, plastic, and other essential components. Once extracted, the raw materials undergo several stages to transform into the car batteries that power our vehicles.
Materials Sourcing
Lead is a primary component in most car batteries. It is mined from lead ore, which is then processed to extract pure lead. Sulfuric acid is produced from sulfur, which can be obtained from natural gas, refining processes, or even fossil fuels. Plastic components, such as the battery case, are manufactured using petroleum-based products.
Lead Processing
Once the raw lead is extracted, it is purified through a process called smelting. During smelting, the lead ore is heated to high temperatures to separate the pure lead from impurities. This pure lead is then cooled and cast into large blocks called ingots, which will later be transformed into various parts of the battery.
Battery Paste Preparation
The purified lead ingots are then converted into lead oxide powder. This powder is mixed with water, sulfuric acid, and other additives to form a thick paste. The paste is then applied to battery grids, which are made from lead or lead alloys. These grids provide the structural framework for the battery’s active material.
Grid Pasting and Curing
The paste-covered grids are placed in a curing chamber, where they are exposed to controlled heat and humidity. This process hardens the paste and ensures it adheres to the grids properly. Once cured, the paste-coated grids are ready to be assembled into battery cells.
Assembly of Battery Cells
In the assembly stage, positive and negative plates are arranged alternately, separated by insulating materials. This forms individual battery cells. Each cell is then filled with an electrolyte solution, usually sulfuric acid, which enables the flow of electric charge between the plates.
Formation and Charging
After assembly, the battery cells undergo an initial charge, known as the formation process. During formation, the battery is charged using a controlled electrical current, which helps form the active materials on the plates. This initial charge is crucial for ensuring the battery’s long-term performance and efficiency.
Sealing and Quality Control
Once the formation process is complete, the battery cells are sealed within a plastic or metal case to prevent leakage. The sealed battery then undergoes rigorous quality control tests to ensure it meets specific performance and safety standards. Any faulty units are discarded or recycled to maintain high-quality production.
Improving Energy Efficiency in Production
Manufacturing car batteries efficiently is essential for reducing energy consumption and minimizing environmental impact. Here are several strategies to enhance energy efficiency during the battery production process.
Optimizing Raw Material Use
Improving the yield of raw materials, such as lead and sulfur, reduces waste and excess energy consumption. Implementing efficient mining and extraction techniques can help achieve this. Recycling used batteries to recover lead and other valuable components also minimizes the need for new raw materials.
Enhancing Smelting Efficiency
Advanced smelting technologies, such as electric arc furnaces or oxygen-enriched air, can significantly improve energy efficiency. These methods allow for quicker and more efficient extraction of pure lead from ore, reducing overall energy consumption and emissions.
Energy-Efficient Manufacturing Processes
Automating key stages of the battery manufacturing process, such as paste preparation and grid pasting, can help reduce energy use. Automation ensures consistent application of materials, minimizing waste and improving overall process efficiency.
Utilizing renewable energy sources, like solar or wind power, to power the manufacturing facilities further enhances sustainability.
Optimizing the Curing and Formation Stages
The curing and formation stages are energy-intensive. Optimizing these processes through precise control of temperature, humidity, and electrical current can lead to significant energy savings. Investing in advanced monitoring and control systems ensures that energy use is minimized without compromising product quality.
Recycling and Reusing Materials
Encouraging the recycling and reuse of old batteries helps conserve resources and reduce energy consumption. Recycling facilities can recover valuable materials, such as lead, which can then be reused in new battery production. This circular economy approach minimizes waste and reduces the need for new raw material extraction.
Implementing Energy Management Systems
Adopting comprehensive energy management systems (EMS) in battery manufacturing plants can identify and monitor areas of high energy consumption. Implementing energy-saving measures, optimizing equipment performance, and reducing downtime contribute to overall energy efficiency. Regular audits and continuous improvement initiatives ensure ongoing energy management and sustainability.
Investing in Research and Development
Ongoing research and development (R&D) efforts are essential for discovering new methods to improve energy efficiency. Investing in R&D enables the development of advanced battery technologies, alternative materials, and more efficient manufacturing processes. Collaborative partnerships between industry, academia, and government institutions can accelerate innovation and promote sustainable practices.
Conclusion
Manufacturing car batteries is a complex process that requires careful consideration of raw materials, production techniques, and energy efficiency. By understanding the various stages of battery production and implementing strategies to improve energy efficiency, we can move towards more sustainable manufacturing practices.
Continued investment in research, recycling, and the adoption of new technologies will ensure that car battery production becomes increasingly environmentally friendly, ultimately benefiting both the industry and the planet.
資料ダウンロード
QCD調達購買管理クラウド「newji」は、調達購買部門で必要なQCD管理全てを備えた、現場特化型兼クラウド型の今世紀最高の購買管理システムとなります。
ユーザー登録
調達購買業務の効率化だけでなく、システムを導入することで、コスト削減や製品・資材のステータス可視化のほか、属人化していた購買情報の共有化による内部不正防止や統制にも役立ちます。
NEWJI DX
製造業に特化したデジタルトランスフォーメーション(DX)の実現を目指す請負開発型のコンサルティングサービスです。AI、iPaaS、および先端の技術を駆使して、製造プロセスの効率化、業務効率化、チームワーク強化、コスト削減、品質向上を実現します。このサービスは、製造業の課題を深く理解し、それに対する最適なデジタルソリューションを提供することで、企業が持続的な成長とイノベーションを達成できるようサポートします。
オンライン講座
製造業、主に購買・調達部門にお勤めの方々に向けた情報を配信しております。
新任の方やベテランの方、管理職を対象とした幅広いコンテンツをご用意しております。
お問い合わせ
コストダウンが利益に直結する術だと理解していても、なかなか前に進めることができない状況。そんな時は、newjiのコストダウン自動化機能で大きく利益貢献しよう!
(Β版非公開)