- お役立ち記事
- Manufacturing Process of Car Seats and Comfort Improvement
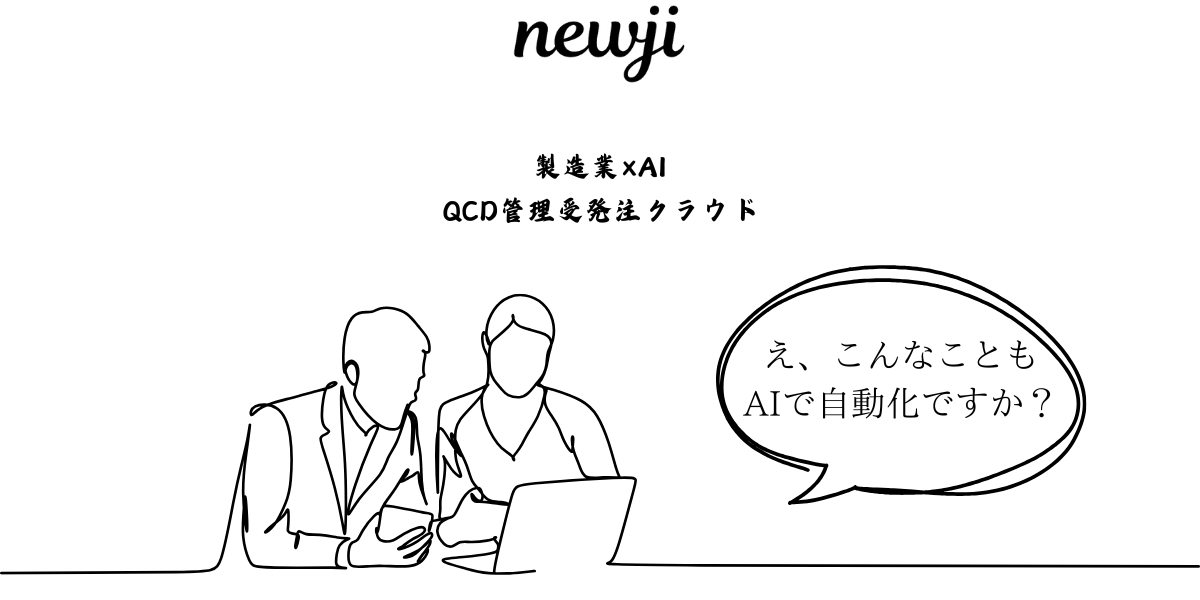
Manufacturing Process of Car Seats and Comfort Improvement
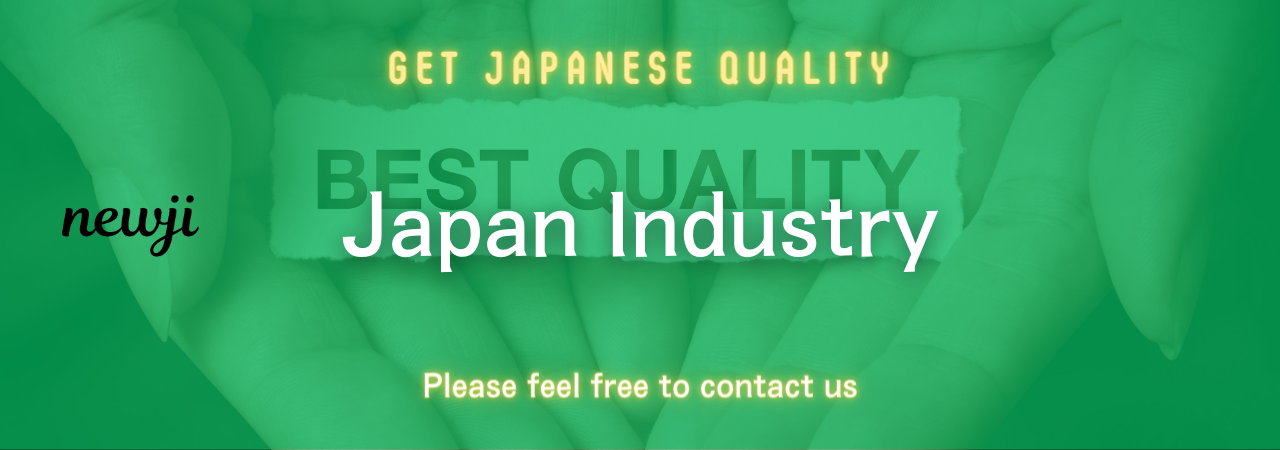
目次
Introduction to Car Seat Manufacturing
Car seats play a crucial role in the driving experience. They provide comfort during long journeys and ensure safety by supporting the driver’s and passengers’ bodies. The process of manufacturing car seats involves several steps, each designed to guarantee durability, comfort, and style. Let’s explore these steps and understand how car seats are made and how their comfort is improved.
Design and Planning
Before any material is cut or sewn, the first step in the manufacturing process is the design phase. Engineers and designers work together to create a seat that meets safety standards and customer preferences.
Initial Concept
Designers create the initial concept sketches of the seat. These sketches are based on research, trends, and ergonomics. They consider factors such as seat shape, padding, and adjustability.
Computer-Aided Design (CAD)
Once the initial concept is approved, the design is transferred to a computer-aided design (CAD) program. CAD allows designers to create precise models and make any necessary adjustments. This digital model will serve as a blueprint for the manufacturing process.
Material Selection
Choosing the right materials is vital for the seat’s durability and comfort. Different materials are selected for various parts of the seat, including the frame, padding, and fabric.
Frame Materials
The seat frame is typically made from high-strength steel or aluminum. These materials provide a sturdy base while keeping the seat relatively lightweight.
Padding Materials
Foam padding is used to make the seat comfortable. Manufacturers often use polyurethane foam due to its durability, flexibility, and support. Depending on the design, memory foam may also be used for added comfort.
Fabric and Leather
The outer covering of the seat can be made from various fabrics or leather. Fabric coverings are breathable and available in many colors and patterns. Leather offers a luxurious feel and is easy to clean. Some manufacturers opt for synthetic leather, which provides a similar look and feel at a reduced cost.
Manufacturing the Seat Frame
The seat frame is the first part to be manufactured. This process involves several steps, including cutting, welding, and assembling.
Cutting the Metal
Metal sheets or tubes are cut into the required shapes and sizes using lasers or computer-controlled cutting machines. This ensures precision and consistency.
Welding and Assembly
The cut pieces are then welded together to form the seat frame. After welding, the frame undergoes several quality checks to ensure there are no weak spots or defects. The frame is then painted or coated to prevent rust and enhance its appearance.
Adding Foam Padding
Once the frame is complete, foam padding is added to provide comfort.
Cutting the Foam
The foam is cut into shapes that fit perfectly on the frame using computer-controlled machines. This ensures uniformity and accuracy.
Gluing the Foam
The foam pieces are then glued onto the frame. Manufacturers use special adhesives that provide a strong bond without affecting the foam’s flexibility. The foam is pressed onto the frame using machines to ensure it adheres properly.
Covering the Seat
The final step in the manufacturing process is covering the seat with fabric or leather.
Cutting the Cover Material
Similar to the foam, the cover material is cut into pieces that will fit the seat perfectly. Cutting machines equipped with computer systems are used to ensure accuracy.
Sewing and Assembly
The cut pieces of fabric or leather are sewn together to form the seat cover. Skilled workers or automated sewing machines perform this task. The cover is then stretched and fitted over the foam padding and frame. This step requires precision to avoid wrinkles and ensure a smooth finish.
Quality Control and Testing
Quality control is a vital part of the manufacturing process. Each seat undergoes several tests to ensure it meets safety and comfort standards.
Comfort Testing
Seats are tested for comfort by simulating various driving conditions. This ensures that the seat remains comfortable over long periods. Manufacturers may use pressure sensors to measure the distribution of weight and identify any areas that need adjustment.
Durability Testing
Durability tests involve applying repeated stress to the seat to simulate years of use. This helps identify any potential weak points and ensures the seat will last over time.
Safety Testing
The seat is also subjected to safety tests, such as crash simulations, to ensure it provides adequate protection in the event of an accident. This includes testing the seatbelt anchor points and the seat’s overall structure.
Comfort Improvement Techniques
Improving the comfort of car seats is an ongoing process. Manufacturers employ several techniques to enhance the driving experience.
Ergonomic Design
Seats are designed to follow the natural curves of the human body. This helps reduce fatigue and provides better support for the back, neck, and legs.
Adjustability
Modern car seats offer various adjustment options, including height, tilt, lumbar support, and headrest positions. This allows drivers and passengers to customize the seat to their individual preferences.
Advanced Materials
Manufacturers are continuously researching and developing new materials that offer better comfort and durability. For example, advanced memory foams and gel inserts can provide additional support and reduce pressure points.
Conclusion
The manufacturing process of car seats is intricate and involves several steps to ensure safety, durability, and comfort. From the initial design and material selection to assembly and testing, each phase is crucial. Continuous improvements in ergonomics, adjustability, and materials help enhance the comfort of car seats, providing a better driving experience for everyone. Understanding this process gives us greater appreciation for the craftsmanship involved in something we use daily without much thought.
資料ダウンロード
QCD調達購買管理クラウド「newji」は、調達購買部門で必要なQCD管理全てを備えた、現場特化型兼クラウド型の今世紀最高の購買管理システムとなります。
ユーザー登録
調達購買業務の効率化だけでなく、システムを導入することで、コスト削減や製品・資材のステータス可視化のほか、属人化していた購買情報の共有化による内部不正防止や統制にも役立ちます。
NEWJI DX
製造業に特化したデジタルトランスフォーメーション(DX)の実現を目指す請負開発型のコンサルティングサービスです。AI、iPaaS、および先端の技術を駆使して、製造プロセスの効率化、業務効率化、チームワーク強化、コスト削減、品質向上を実現します。このサービスは、製造業の課題を深く理解し、それに対する最適なデジタルソリューションを提供することで、企業が持続的な成長とイノベーションを達成できるようサポートします。
オンライン講座
製造業、主に購買・調達部門にお勤めの方々に向けた情報を配信しております。
新任の方やベテランの方、管理職を対象とした幅広いコンテンツをご用意しております。
お問い合わせ
コストダウンが利益に直結する術だと理解していても、なかなか前に進めることができない状況。そんな時は、newjiのコストダウン自動化機能で大きく利益貢献しよう!
(Β版非公開)