- お役立ち記事
- Manufacturing Process of Climbing Backpacks and Enhancing Durability
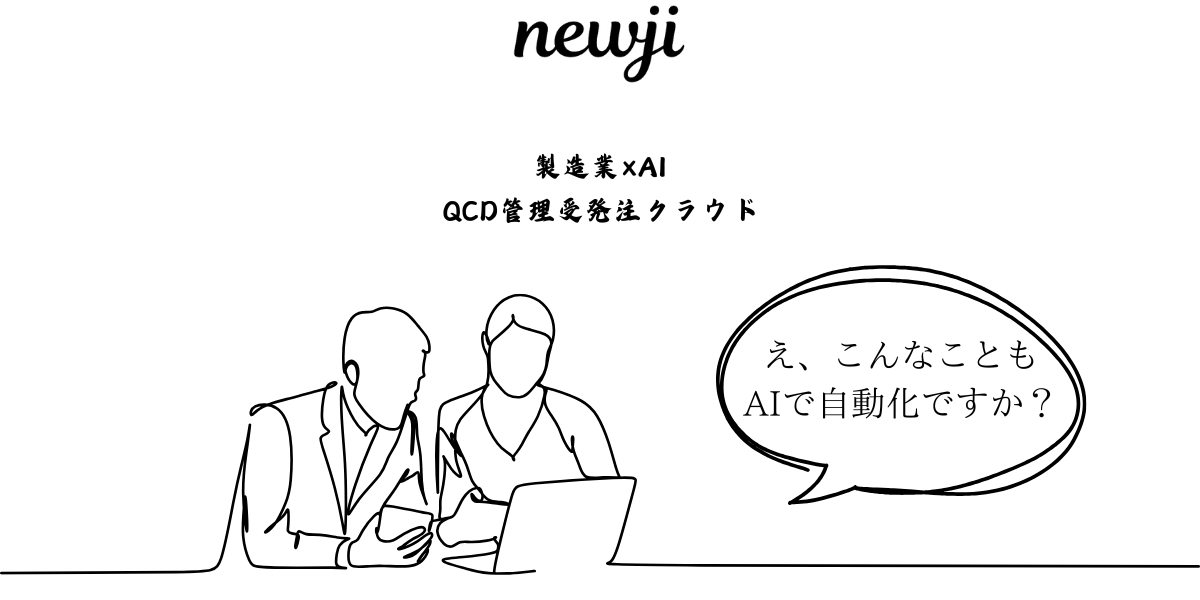
Manufacturing Process of Climbing Backpacks and Enhancing Durability
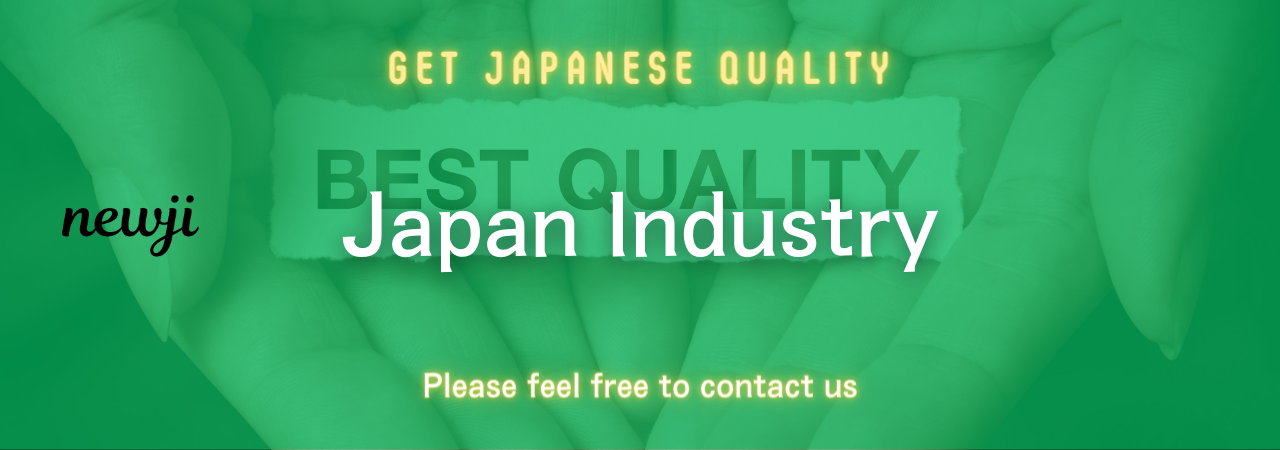
Climbing backpacks are essential for mountain enthusiasts who need durable and reliable gear to aid them in their adventures.
Understanding how these backpacks are made and what makes them durable can help consumers make informed choices when selecting their gear.
Let’s dive into the manufacturing process of climbing backpacks and explore the elements that contribute to their enhanced durability.
目次
Material Selection
Choosing the right materials is crucial in the manufacturing of climbing backpacks.
Manufacturers typically opt for high-quality, durable fabrics such as ripstop nylon or Cordura, which offer excellent resistance to wear and tear.
Reinforced stitching and seam sealing are also essential to ensure the backpack can withstand the rugged conditions of mountain climbing.
Materials are selected not just for their strength, but also for their weight, flexibility, and waterproof characteristics.
Design and Prototyping
Once materials are chosen, the design phase begins.
Designers focus on creating ergonomic and efficient models that distribute weight evenly and provide maximum comfort.
Various designs are prototyped and rigorously tested for functionality and comfort.
Focus groups and professional climbers often test these prototypes in real-world conditions.
Feedback from these tests is crucial for making any necessary adjustments before finalizing the design.
Cutting and Preparation
After the design is approved, the manufacturing process moves to cutting and preparation.
Large sheets of the chosen fabric are precisely cut into the various components needed for the backpack.
This is often done using automated cutting machines to ensure accuracy and consistency.
Smaller components like zippers, buckles, and straps are also prepared and gathered for assembly.
Assembly
The assembly process involves sewing the cut pieces of fabric together, adding zippers, buckles, and other hardware.
Specialized sewing machines are used to handle the heavy-duty stitching required for climbing backpacks.
Seams are often double-stitched or reinforced with binding tape to prevent them from coming apart under stress.
Many high-end climbing backpacks feature bar-tack stitching, a method that provides additional strength to areas of high stress.
Adding Special Features
During assembly, manufacturers incorporate special features tailored to enhance the backpack’s functionality.
These may include multiple compartments, hydration bladder sleeves, gear loops, and tool holders.
Some climbing backpacks have built-in rain covers or attachment points for carrying ropes and helmets.
The addition of these features is meticulously planned and executed to ensure they do not compromise the backpack’s structural integrity or user comfort.
Quality Control
Quality control is a critical step in the manufacturing process.
Each finished backpack undergoes rigorous inspection to ensure it meets the manufacturer’s quality standards.
This includes checking the stitching, seams, zippers, and hardware for any defects.
Some manufacturers also conduct field tests to confirm the backpack’s performance under real climbing conditions.
This thorough inspection process helps prevent faulty products from reaching consumers.
Enhancing Durability
Several methods are employed to enhance the durability of climbing backpacks.
One common technique is using reinforced fabric in high-wear areas, such as the base of the backpack.
Waterproof coatings and seam sealants are applied to improve water resistance without adding significant weight.
Manufacturers may also use advanced materials such as Dyneema, which is known for its high strength-to-weight ratio.
Additionally, adjustable back systems and padded shoulder straps help distribute weight evenly, reducing stress on the backpack and enhancing user comfort.
Eco-Friendly Manufacturing
As consumers become more environmentally conscious, many manufacturers are adopting eco-friendly practices.
This includes using recycled materials and environmentally friendly dyes.
Some companies have started implementing sustainable manufacturing processes to reduce their carbon footprint.
These efforts not only appeal to eco-conscious consumers but also contribute to the overall sustainability of the environment.
Packaging and Distribution
Once the backpacks have passed quality control, they are packaged for distribution.
Packaging is designed to protect the backpack during transit and often includes information about the product’s features and care instructions.
From the manufacturing facility, backpacks are distributed to retailers, both physical and online, and made available to consumers.
Conclusion
The manufacturing process of climbing backpacks involves careful material selection, precise design, and rigorous testing to ensure durability and functionality.
By understanding this process, consumers can appreciate the craftsmanship involved and make informed decisions when purchasing their climbing gear.
Durability enhancements and eco-friendly practices are becoming standard in the industry, ensuring that climbers have reliable equipment while also contributing to a more sustainable environment.
Whether you’re a seasoned climber or a beginner, investing in a high-quality climbing backpack is essential for a safe and enjoyable adventure.
資料ダウンロード
QCD調達購買管理クラウド「newji」は、調達購買部門で必要なQCD管理全てを備えた、現場特化型兼クラウド型の今世紀最高の購買管理システムとなります。
ユーザー登録
調達購買業務の効率化だけでなく、システムを導入することで、コスト削減や製品・資材のステータス可視化のほか、属人化していた購買情報の共有化による内部不正防止や統制にも役立ちます。
NEWJI DX
製造業に特化したデジタルトランスフォーメーション(DX)の実現を目指す請負開発型のコンサルティングサービスです。AI、iPaaS、および先端の技術を駆使して、製造プロセスの効率化、業務効率化、チームワーク強化、コスト削減、品質向上を実現します。このサービスは、製造業の課題を深く理解し、それに対する最適なデジタルソリューションを提供することで、企業が持続的な成長とイノベーションを達成できるようサポートします。
オンライン講座
製造業、主に購買・調達部門にお勤めの方々に向けた情報を配信しております。
新任の方やベテランの方、管理職を対象とした幅広いコンテンツをご用意しております。
お問い合わせ
コストダウンが利益に直結する術だと理解していても、なかなか前に進めることができない状況。そんな時は、newjiのコストダウン自動化機能で大きく利益貢献しよう!
(Β版非公開)