- お役立ち記事
- Manufacturing Process of Clutch Discs and Durability Enhancement
月間76,176名の
製造業ご担当者様が閲覧しています*
*2025年3月31日現在のGoogle Analyticsのデータより
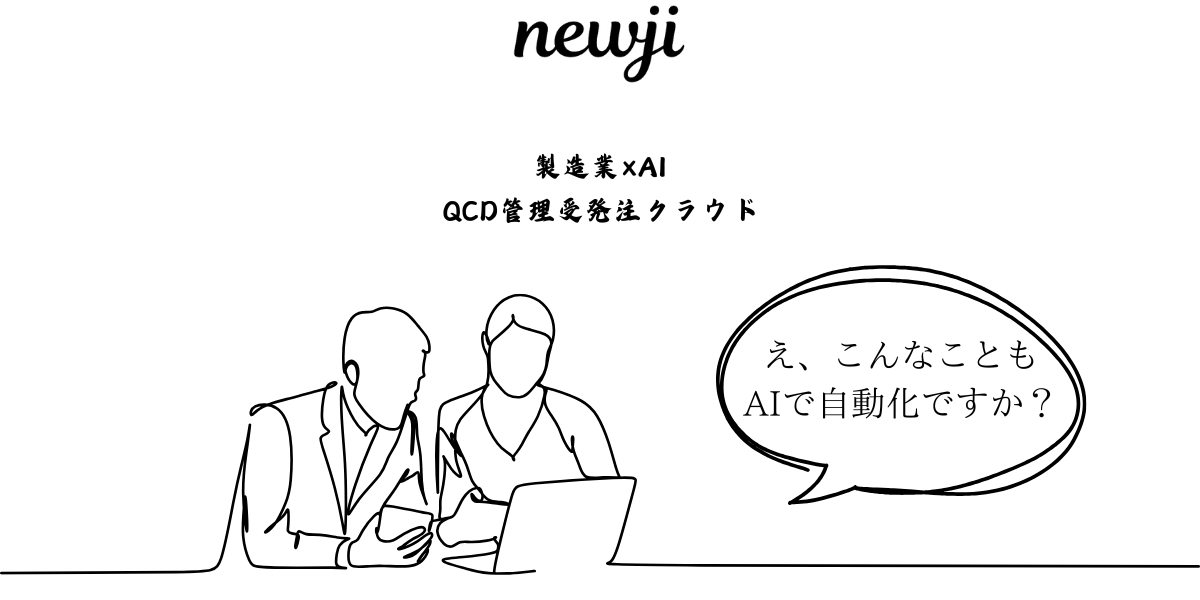
Manufacturing Process of Clutch Discs and Durability Enhancement
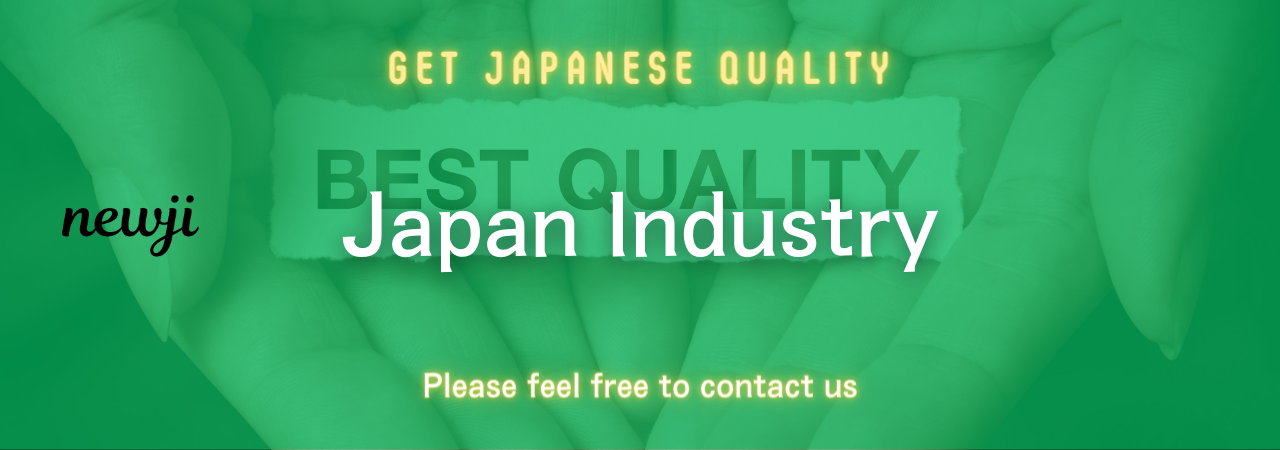
Clutch discs are an essential part of any vehicle’s transmission system.
These discs are responsible for engaging and disengaging the engine from the transmission, allowing for smooth gear shifts.
Understanding the manufacturing process of clutch discs and how to enhance their durability is crucial for ensuring reliable vehicle performance.
In this article, we will explore the steps involved in making clutch discs and the methods used to improve their longevity.
目次
Gathering Raw Materials
The first step in manufacturing clutch discs is the selection of high-quality raw materials.
Typically, clutch discs are made from a combination of metals and friction materials.
Steel is commonly used for the core structure because of its strength and durability.
Friction materials, such as organic compounds or ceramics, are applied to the disc’s surface to provide the necessary grip.
These materials must be carefully chosen and tested to ensure they meet the required standards for performance and durability.
Metal Selection
Manufacturers typically select specific metals based on the strength and wear resistance required for the clutch disc.
Steel alloys with high carbon content are often preferred for their ability to withstand high stress and thermal conditions.
Friction Material Selection
The selection of friction materials depends on the type of vehicle and the intended use of the clutch.
Organic friction materials, made from resins and fibers, are commonly used for everyday vehicles because of their smooth engagement properties.
Ceramic-based materials are preferred for high-performance applications as they offer higher heat resistance and durability.
Stamping and Shaping the Core
Once the raw materials are selected, the steel cores must be stamped and shaped into the desired form.
This process involves using large presses to cut and shape the steel into the appropriate size and profile for the clutch disc.
Precision is key during this stage to ensure that the disc will fit correctly and function properly within the transmission system.
Computer-aided design (CAD) software is often used to create detailed blueprints that guide the stamping process.
Precision Cutting
Computer-controlled machines are employed to cut the steel with high accuracy, minimizing waste and ensuring that each disc meets exact specifications.
Shaping the Core
Specialized presses apply high pressure to shape the cut steel into the final form of the clutch disc core.
This step may also involve adding features such as slots or holes, which aid in heat dissipation and material engagement.
Applying Friction Materials
With the core shaped, the next step is to apply the friction materials to the disc’s surface.
This process typically involves bonding the selected friction materials to the steel core using adhesives or mechanical fasteners.
A high level of precision is essential to ensure even application and consistent performance.
Adhesive Bonding
Adhesive bonding involves applying a special glue to attach the friction material firmly to the core.
The adhesive must be heat resistant and able to withstand the rigors of the clutch’s operating environment.
Mechanical Fastening
In some cases, friction materials are mechanically fastened to the core using rivets or bolts.
This method provides extra security and ensures that the materials remain firmly attached over the clutch disc’s lifespan.
Heat Treatment
To further enhance the strength and durability of the clutch disc, a heat treatment process is applied.
This involves heating the entire disc to high temperatures and then cooling it rapidly.
Heat treatment helps to improve the steel’s hardness and resistance to wear and tear.
Annealing
Annealing is a specific type of heat treatment that involves heating the clutch disc to a specific temperature and then allowing it to cool slowly in a controlled environment.
This process relieves internal stresses within the steel and enhances its overall toughness.
Quenching
Quenching is another heat treatment method where the disc is heated to a high temperature and then rapidly cooled in water or oil.
This process increases the steel’s hardness and improves its resistance to deformation under load.
Finishing and Quality Control
After the heat treatment, the clutch disc undergoes finishing processes to ensure it meets all specifications and is free from defects.
These processes may include grinding, polishing, and balancing.
Grinding
Grinding involves removing any excess material from the disc’s surface to achieve a smooth, even finish.
This step is crucial for ensuring that the clutch engages smoothly and operates without vibration.
Polishing
Polishing enhances the surface finish of the clutch disc, further improving its performance and resistance to wear.
A polished surface reduces friction and allows for smoother engagement.
Balancing
Balancing is essential to ensure that the clutch disc operates smoothly at high speeds.
Unbalanced discs can cause vibrations and reduce the overall lifespan of the transmission system.
Special machines are used to detect and correct any imbalances in the disc.
Durability Enhancement Techniques
Enhancing the durability of clutch discs is vital for ensuring long-term performance and reliability.
Several techniques can be employed to achieve this goal.
Surface Coating
Applying a specialized coating to the surface of the clutch disc can significantly improve its resistance to wear and corrosion.
Coatings such as anti-wear or anti-corrosion treatments are commonly used to extend the disc’s lifespan.
Material Upgrades
Using advanced materials, such as composite or hybrid materials, can enhance the durability of clutch discs.
These materials offer better resistance to high temperatures and stress compared to traditional materials.
Regular Maintenance
Regular maintenance and inspection of the clutch system can help detect any signs of wear or damage early on.
Routine maintenance ensures that the clutch disc remains in optimal condition and performs reliably over time.
Understanding the manufacturing process of clutch discs and implementing durability enhancement techniques are essential for ensuring the longevity and performance of a vehicle’s transmission system.
By selecting high-quality materials, employing precise manufacturing methods, and applying advanced durability enhancements, manufacturers can produce clutch discs that meet the demands of modern vehicles.
資料ダウンロード
QCD管理受発注クラウド「newji」は、受発注部門で必要なQCD管理全てを備えた、現場特化型兼クラウド型の今世紀最高の受発注管理システムとなります。
ユーザー登録
受発注業務の効率化だけでなく、システムを導入することで、コスト削減や製品・資材のステータス可視化のほか、属人化していた受発注情報の共有化による内部不正防止や統制にも役立ちます。
NEWJI DX
製造業に特化したデジタルトランスフォーメーション(DX)の実現を目指す請負開発型のコンサルティングサービスです。AI、iPaaS、および先端の技術を駆使して、製造プロセスの効率化、業務効率化、チームワーク強化、コスト削減、品質向上を実現します。このサービスは、製造業の課題を深く理解し、それに対する最適なデジタルソリューションを提供することで、企業が持続的な成長とイノベーションを達成できるようサポートします。
製造業ニュース解説
製造業、主に購買・調達部門にお勤めの方々に向けた情報を配信しております。
新任の方やベテランの方、管理職を対象とした幅広いコンテンツをご用意しております。
お問い合わせ
コストダウンが利益に直結する術だと理解していても、なかなか前に進めることができない状況。そんな時は、newjiのコストダウン自動化機能で大きく利益貢献しよう!
(β版非公開)