- お役立ち記事
- Manufacturing Process of Clutch Discs and Durability Reinforcement
Manufacturing Process of Clutch Discs and Durability Reinforcement
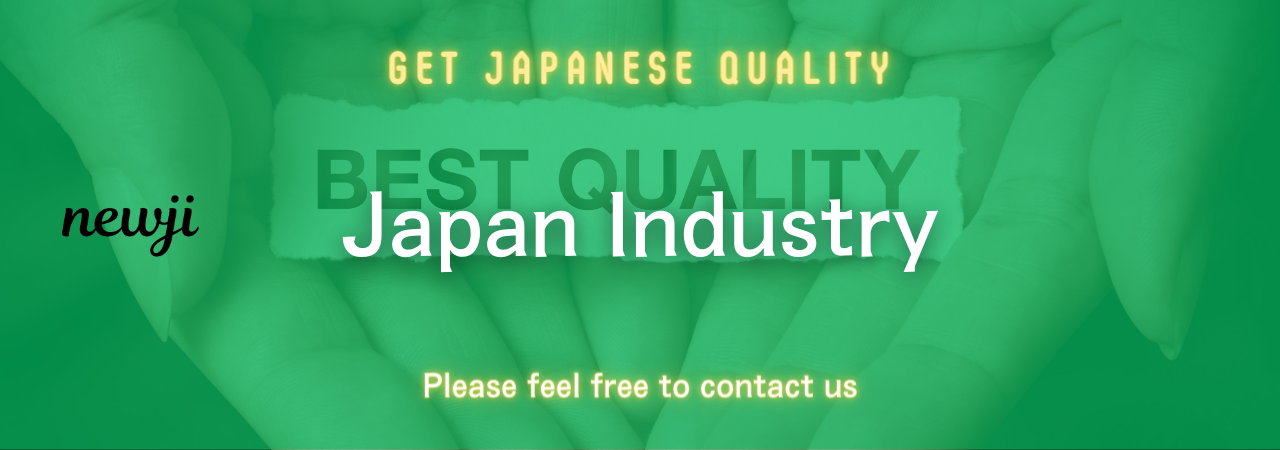
The process of creating clutch discs involves several crucial steps, each aimed at ensuring the final product is durable and functions effectively in vehicles.
Understanding the manufacturing process can highlight the importance of each phase, from raw material selection to the reinforcement techniques that enhance durability.
目次
Raw Material Selection
The first step in making clutch discs is choosing the right materials.
Manufacturers generally opt for high-strength steel, which provides the necessary durability and resilience.
These materials must withstand the friction and heat generated during clutch operation.
The selected steel undergoes rigorous testing to ensure it meets specific standards.
This initial quality control is crucial because any defect in the raw materials can compromise the entire manufacturing process.
Cutting and Shaping
Once the raw materials pass the quality checks, they are cut into the desired shapes using advanced cutting machines.
Precision is key in this step because even a minor deviation can affect the disc’s performance.
After cutting, the steel pieces are shaped into discs through a series of stamping and molding operations.
These shaped discs are then prepared for the next stage of manufacturing.
Heat Treatment
Heat treatment makes the clutch disc more robust and resistant to wear and tear.
During this phase, the discs are heated to high temperatures and then gradually cooled.
This process, known as tempering, strengthens the metal and enhances its durability.
Heat treatment not only improves the strength but also ensures the discs can cope with extreme conditions without deforming or breaking.
Friction Material Application
Friction materials are essential components of clutch discs because they enable the clutch to grip and release smoothly.
Manufacturers apply these materials using bonding techniques to ensure they adhere well to the metal discs.
These friction materials often consist of organic compounds, ceramics, or kevlar, each chosen for their high resistance to heat and wear.
This application process must be flawless to ensure the longevity and reliability of the clutch disc.
After the friction material is applied, the discs undergo another round of quality inspection to ensure there are no defects or inconsistencies.
Quality Assurance and Testing
Quality assurance is an ongoing process throughout the manufacturing of clutch discs.
However, a comprehensive final inspection is vital for guaranteeing the product’s performance.
Various tests are conducted, including stress tests, to measure the disc’s ability to handle real-world operating conditions.
Testing also includes checking for any potential flaws that may have surfaced during the manufacturing process.
These could range from micro-cracks to alignment issues.
Only after passing all these stringent tests are the clutch discs considered ready for the market.
Durability Reinforcement Techniques
To enhance the durability of clutch discs, manufacturers employ several reinforcement techniques.
Surface Coating
One common method is applying a protective surface coating.
This coating can be made from different materials, including nickel or chromium, which provide additional resistance against corrosion and wear.
This layer serves as the first line of defense against environmental factors that could degrade the clutch disc over time.
Strengthening Alloys
Another technique involves adding specific alloys to the base metal during the heat treatment phase.
These alloys, such as vanadium or titanium, work by forming a more robust molecular structure within the metal, thereby increasing its overall strength and longevity.
Advanced Bonding Techniques
Bonding the friction material securely to the disc is crucial for its long-term performance.
Manufacturers have developed advanced bonding methods, such as using high-pressure adhesives or advanced riveting techniques, to ensure a more secure attachment.
These advanced methods minimize the risk of the friction material detaching, which can lead to clutch failure.
Precision Engineering
Precision engineering plays a vital role in enhancing a clutch disc’s durability.
Using computer-aided design (CAD) and computer-aided manufacturing (CAM) technologies, manufacturers can create highly precise components that fit together perfectly.
This precision reduces unnecessary stress and wear on the clutch disc during operation.
Regular Feedback and Improvement
To continuously improve the durability of clutch discs, manufacturers often seek feedback from users and incorporate advancements in material science and engineering.
By staying abreast of the latest technological developments, they can refine their processes and materials, ensuring that they deliver the highest quality products.
In summary, the manufacturing process of clutch discs is meticulous and multi-faceted, with each step playing a pivotal role in determining the final product’s performance and durability.
From selecting the best raw materials to applying state-of-the-art reinforcement techniques, every phase is designed to produce clutch discs that can withstand the rigors of automotive use.
資料ダウンロード
QCD調達購買管理クラウド「newji」は、調達購買部門で必要なQCD管理全てを備えた、現場特化型兼クラウド型の今世紀最高の購買管理システムとなります。
ユーザー登録
調達購買業務の効率化だけでなく、システムを導入することで、コスト削減や製品・資材のステータス可視化のほか、属人化していた購買情報の共有化による内部不正防止や統制にも役立ちます。
NEWJI DX
製造業に特化したデジタルトランスフォーメーション(DX)の実現を目指す請負開発型のコンサルティングサービスです。AI、iPaaS、および先端の技術を駆使して、製造プロセスの効率化、業務効率化、チームワーク強化、コスト削減、品質向上を実現します。このサービスは、製造業の課題を深く理解し、それに対する最適なデジタルソリューションを提供することで、企業が持続的な成長とイノベーションを達成できるようサポートします。
オンライン講座
製造業、主に購買・調達部門にお勤めの方々に向けた情報を配信しております。
新任の方やベテランの方、管理職を対象とした幅広いコンテンツをご用意しております。
お問い合わせ
コストダウンが利益に直結する術だと理解していても、なかなか前に進めることができない状況。そんな時は、newjiのコストダウン自動化機能で大きく利益貢献しよう!
(Β版非公開)