- お役立ち記事
- Manufacturing Process of Combustion Control Boards and Control Precision Improvement
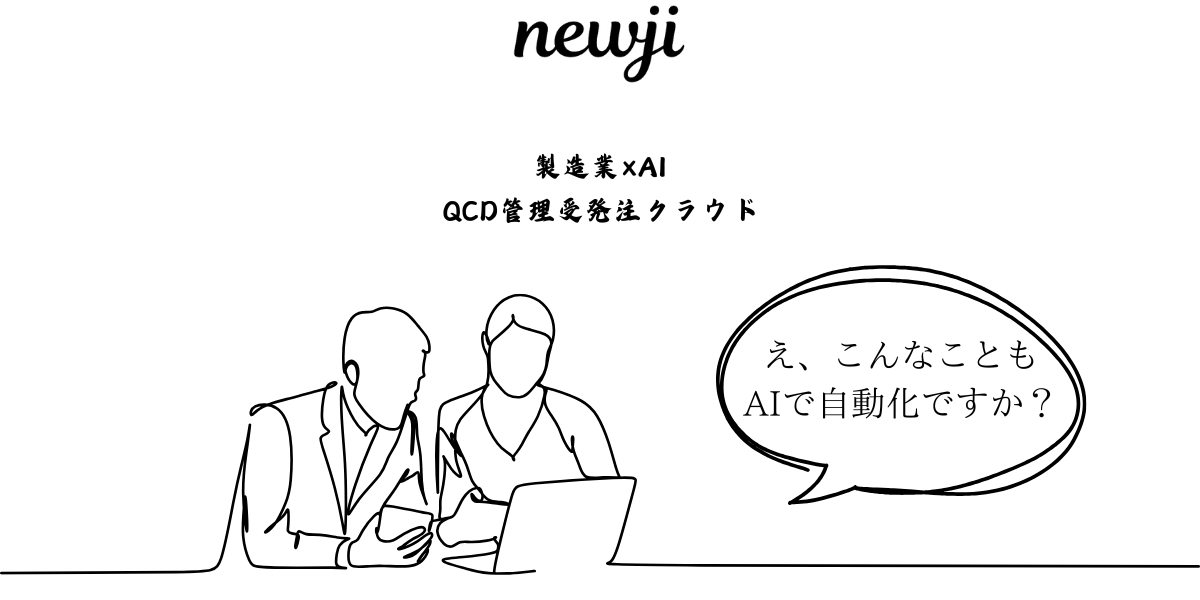
Manufacturing Process of Combustion Control Boards and Control Precision Improvement
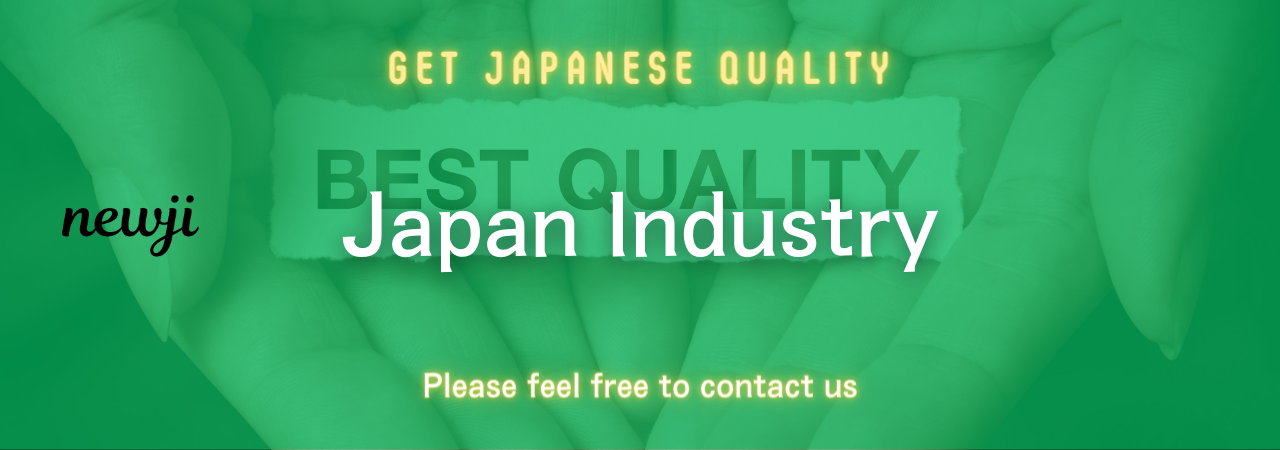
The manufacturing process of combustion control boards is a fascinating and intricate sequence of steps that ensures precision and reliability. These boards are critical in managing the combustion process within various systems, such as furnaces, boilers, and engines, to maintain safety and efficiency. Here, we’ll delve into the various stages involved, and explore how improvements in control precision are made.
目次
Understanding Combustion Control Boards
Combustion control boards are electronic circuits designed to control and monitor the combustion process. They play a pivotal role in regulating fuel and air mixture, overseeing temperature, and ensuring that the combustion is stable and efficient. These boards help enhance fuel efficiency, reduce emissions, and maintain the desired operational parameters.
Manufacturing Process Overview
The manufacturing process of combustion control boards involves several key stages, starting from the design phase and culminating in rigorous testing and quality assurance.
1. Design and Prototyping
The first step in the manufacturing process is the design phase.
Engineers and designers work closely to create a blueprint of the combustion control board.
This includes schematic diagrams, layout plans, and specifications for components.
Once the design is complete, a prototype is developed.
The prototype undergoes initial testing to ensure it meets the desired performance standards.
2. Component Selection and Sourcing
Selecting the right components is crucial for the functionality and durability of the control board.
Components such as resistors, capacitors, microcontrollers, and sensors are chosen based on the design specifications.
Vendors and suppliers are sourced for high-quality materials to ensure reliability.
The availability and cost-effectiveness of these components are also considered during this phase.
3. PCB Fabrication
Printed Circuit Board (PCB) fabrication is a vital step in the manufacturing process.
The designed schematic is transferred onto a PCB, which serves as the framework for the control board.
PCB material, typically made from fiberglass-reinforced epoxy, is chosen for its durability and conductivity.
The board undergoes drilling, layering, and etching processes to form the circuit patterns.
4. Component Placement and Soldering
Once the PCB is ready, the next step is component placement.
Automated machines place the components on the board with precise accuracy.
These machines ensure that each component is positioned correctly as per the design.
After placement, the components are soldered onto the board.
Soldering can be done using various methods, including reflow soldering and wave soldering, to secure the components in place.
5. Assembly and Integration
In this phase, the combustion control board is assembled and integrated into a larger system if necessary.
Connectors, wires, and external interfaces are attached to the board.
This step ensures that the board can communicate and interact with other parts of the system.
Assembly also includes securing the board within its housing or casing.
6. Testing and Calibration
Testing and calibration are crucial to ensure the control board functions accurately.
Automated and manual tests are conducted to check for any defects or inconsistencies.
Calibration involves adjusting the board’s settings to meet precise operational standards.
These tests verify the board’s ability to control combustion parameters effectively and reliably.
7. Quality Assurance and Inspection
Quality assurance (QA) is an essential step to confirm the reliability and performance of the control board.
QA processes involve visual inspections, functional tests, and stress tests.
These inspections ensure that the board meets industry standards and regulatory requirements.
8. Packaging and Distribution
Once the combustion control board passes all tests and inspections, it is ready for packaging.
The packaging process involves securing the board in protective materials to prevent damage during transport.
Proper labeling and documentation are also prepared.
Finally, the control boards are distributed to customers or integrated into larger systems.
Improving Control Precision
Improving control precision is a continuous goal in manufacturing combustion control boards.
Here are some key strategies employed to enhance precision:
1. Advanced Sensor Integration
Integrating advanced sensors into combustion control boards allows for more accurate monitoring and control.
Sensors such as infrared, gas, and pressure sensors provide real-time data on combustion parameters.
This data enables the board to make precise adjustments to fuel and air mixtures.
2. Enhanced Algorithms
Developing sophisticated algorithms improves the control board’s decision-making capabilities.
These algorithms analyze data from sensors and make real-time adjustments to maintain optimal combustion.
Improvements in software programming also contribute to more accurate control.
3. Real-Time Feedback Systems
Incorporating real-time feedback systems allows the combustion control board to respond quickly to changes in combustion conditions.
Feedback loops help maintain stability and efficiency by continuously adjusting parameters based on real-time data.
This dynamic adjustment enhances control precision.
4. High-Quality Components
Using high-quality components in the manufacturing process ensures that the control board performs reliably.
Components with tight tolerances and superior materials enhance the overall precision of the control board.
Investing in reputable suppliers and conducting rigorous component testing contribute to improved precision.
5. Rigorous Testing and Calibration
Continuous testing and calibration processes are essential for maintaining control precision.
Regular updates to testing procedures and calibration techniques help identify and rectify any deviations.
Implementing automated testing systems further enhances the accuracy and efficiency of the testing process.
Conclusion
The manufacturing process of combustion control boards is a meticulous and detail-oriented sequence of steps.
From design and prototyping to testing and quality assurance, each stage plays a crucial role in ensuring the functionality and reliability of the control board.
Moreover, continuous improvements in control precision through advanced sensors, algorithms, feedback systems, high-quality components, and rigorous testing contribute to the development of highly efficient combustion control boards.
These advancements not only enhance the performance of combustion systems but also contribute to energy efficiency and environmental sustainability.
資料ダウンロード
QCD調達購買管理クラウド「newji」は、調達購買部門で必要なQCD管理全てを備えた、現場特化型兼クラウド型の今世紀最高の購買管理システムとなります。
ユーザー登録
調達購買業務の効率化だけでなく、システムを導入することで、コスト削減や製品・資材のステータス可視化のほか、属人化していた購買情報の共有化による内部不正防止や統制にも役立ちます。
NEWJI DX
製造業に特化したデジタルトランスフォーメーション(DX)の実現を目指す請負開発型のコンサルティングサービスです。AI、iPaaS、および先端の技術を駆使して、製造プロセスの効率化、業務効率化、チームワーク強化、コスト削減、品質向上を実現します。このサービスは、製造業の課題を深く理解し、それに対する最適なデジタルソリューションを提供することで、企業が持続的な成長とイノベーションを達成できるようサポートします。
オンライン講座
製造業、主に購買・調達部門にお勤めの方々に向けた情報を配信しております。
新任の方やベテランの方、管理職を対象とした幅広いコンテンツをご用意しております。
お問い合わせ
コストダウンが利益に直結する術だと理解していても、なかなか前に進めることができない状況。そんな時は、newjiのコストダウン自動化機能で大きく利益貢献しよう!
(Β版非公開)