- お役立ち記事
- Manufacturing Process of Combustion Control Boards and Improving Control Precision
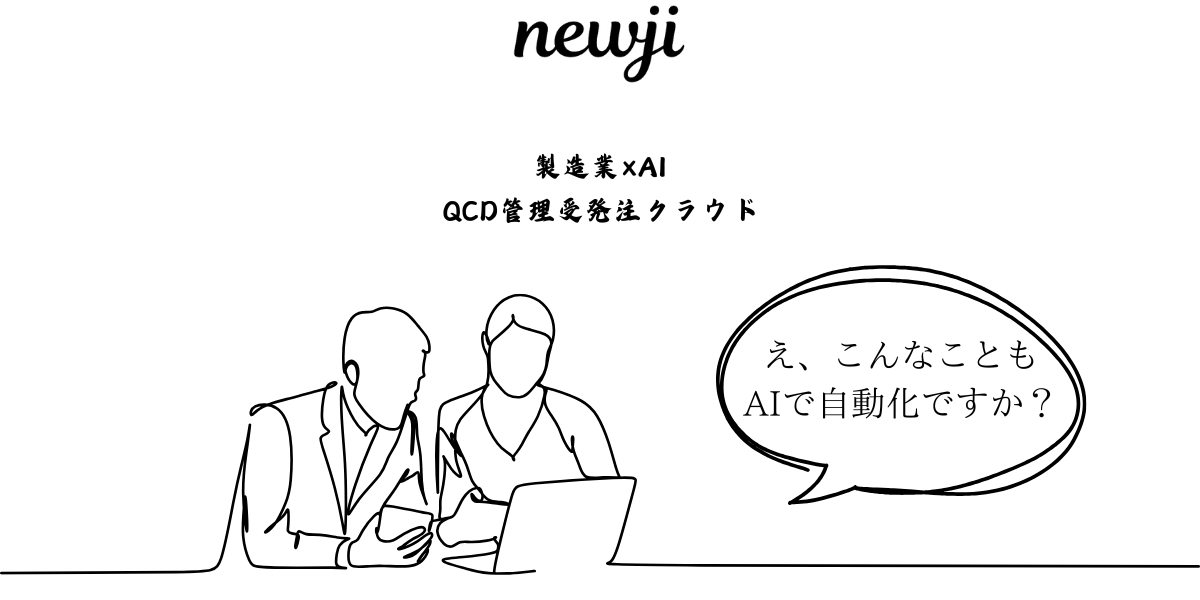
Manufacturing Process of Combustion Control Boards and Improving Control Precision
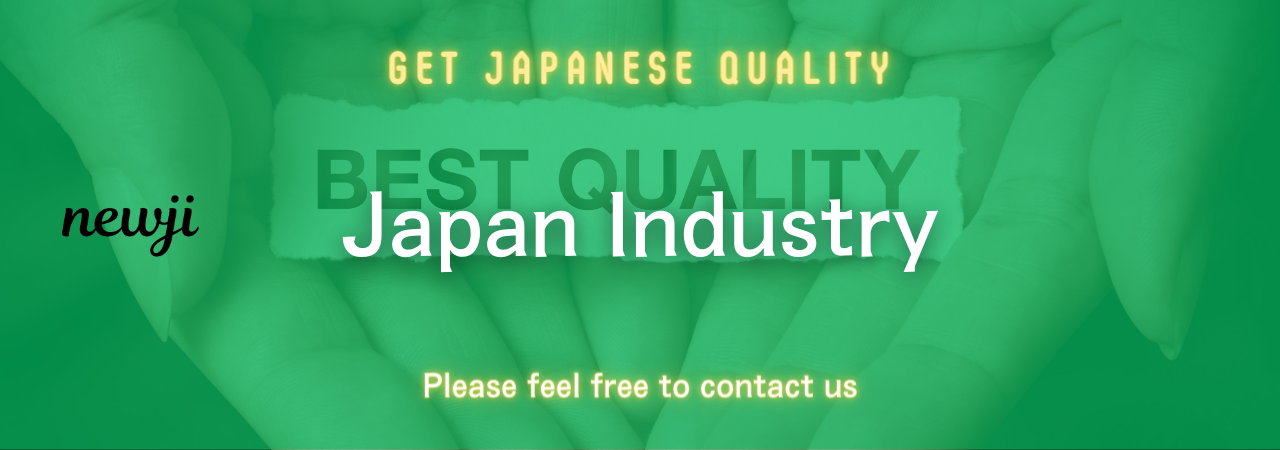
目次
The Importance of Combustion Control Boards
Combustion control boards play a critical role in various industries by managing the combustion process in devices like boilers, furnaces, and engines.
These boards ensure that the burning of fuel occurs efficiently, thereby optimizing energy use and reducing emissions.
In arenas such as power generation and industrial manufacturing, precise control is essential to maintain safety, performance, and environmental standards.
Materials Used in Combustion Control Boards
Before delving into the manufacturing process, it is essential to understand the materials involved.
Combustion control boards are typically made up of multiple layers of specialized materials.
The primary materials include:
Printed Circuit Board (PCB)
The backbone of any combustion control board is the printed circuit board (PCB).
PCBs are usually made from fiberglass composites or other insulating materials and are crucial for housing the various electronic components.
Electronic Components
Various electronic components such as sensors, microprocessors, transistors, and resistors are mounted onto the PCB.
These components are often fabricated from materials like silicon, gold, and copper.
The Manufacturing Process of Combustion Control Boards
Design and Prototyping
The first step in the manufacturing process is the design phase.
Engineers use specialized software to create detailed schematics and layouts of the control board.
This stage also involves simulations to test the functionality and efficiency of the design.
Once the design is validated, a prototype is created.
The prototype serves as a proof of concept and helps in identifying any design flaws.
Material Procurement
After the design and prototyping phase, the next step is to procure the materials.
High-quality PCBs and electronic components are sourced from reliable suppliers to ensure the durability and efficiency of the control boards.
PCB Fabrication
The next step involves the fabrication of the PCB.
This process includes:
– *Layer Preparation:* The initial layers of the PCB are prepared, usually consisting of copper and insulating materials.
– *Etching:* Using chemical solutions, unwanted copper is removed to create the circuit pathways.
– *Lamination:* Multiple layers are fused using heat and pressure, producing a solid multilayer PCB.
– *Drilling:* Holes are drilled to accommodate the electronic components and connections.
Component Mounting
Once the PCB is fabricated, electronic components are mounted onto it using techniques like Surface Mount Technology (SMT) and Through-Hole Technology (THT).
In SMT, components are placed directly onto the surface of the PCB, while in THT, leads are inserted through the holes and soldered in place.
Soldering
Soldering is a critical step that ensures electrical connection between components.
Two techniques are commonly used:
– *Reflow Soldering:* Used primarily for SMT, where solder paste is applied, and the board is heated to melt the solder.
– *Wave Soldering:* Used for THT, where the board is passed over a wave of molten solder.
Quality Control and Testing
Quality control measures are implemented to ensure the board meets all specifications.
Various tests like Automated Optical Inspection (AOI), X-Ray Inspection, and functional tests are conducted.
These tests help in identifying any defects or inconsistencies.
Improving Control Precision in Combustion Control Boards
Advanced Algorithm Implementation
One of the most effective ways to improve control precision is via advanced algorithms.
Sophisticated algorithms can predict and adjust the combustion parameters in real-time, ensuring optimal performance.
Enhanced Sensors
The use of high-precision sensors can offer more accurate data, which in turn leads to better control.
Innovations in sensor technology have led to the development of sensors that can withstand extreme conditions and provide precise measurements.
Real-time Monitoring
Real-time monitoring allows for adjustments to be made instantly.
Integration with IoT (Internet of Things) devices can provide real-time data to a central monitoring system, thus offering better control and efficiency.
Machine Learning and AI
The implementation of machine learning and artificial intelligence can further improve the precision of combustion control boards.
These technologies can learn from past data and make predictions to optimize performance continually.
The Future of Combustion Control Boards
As technology continues to advance, we can expect combustion control boards to become even more efficient and precise.
Future improvements could potentially include further miniaturization, increased use of renewable materials, and even self-healing capabilities that can repair minor damages automatically.
Conclusively, the manufacturing process of combustion control boards is intricate and requires meticulous attention to detail.
With innovations in technology, the precision and capabilities of these control boards will continue to improve, playing a significant role in enhancing the efficiency of various combustion systems worldwide.
資料ダウンロード
QCD調達購買管理クラウド「newji」は、調達購買部門で必要なQCD管理全てを備えた、現場特化型兼クラウド型の今世紀最高の購買管理システムとなります。
ユーザー登録
調達購買業務の効率化だけでなく、システムを導入することで、コスト削減や製品・資材のステータス可視化のほか、属人化していた購買情報の共有化による内部不正防止や統制にも役立ちます。
NEWJI DX
製造業に特化したデジタルトランスフォーメーション(DX)の実現を目指す請負開発型のコンサルティングサービスです。AI、iPaaS、および先端の技術を駆使して、製造プロセスの効率化、業務効率化、チームワーク強化、コスト削減、品質向上を実現します。このサービスは、製造業の課題を深く理解し、それに対する最適なデジタルソリューションを提供することで、企業が持続的な成長とイノベーションを達成できるようサポートします。
オンライン講座
製造業、主に購買・調達部門にお勤めの方々に向けた情報を配信しております。
新任の方やベテランの方、管理職を対象とした幅広いコンテンツをご用意しております。
お問い合わせ
コストダウンが利益に直結する術だと理解していても、なかなか前に進めることができない状況。そんな時は、newjiのコストダウン自動化機能で大きく利益貢献しよう!
(Β版非公開)