- お役立ち記事
- Manufacturing Process of Condenser Units and Power Efficiency Improvement
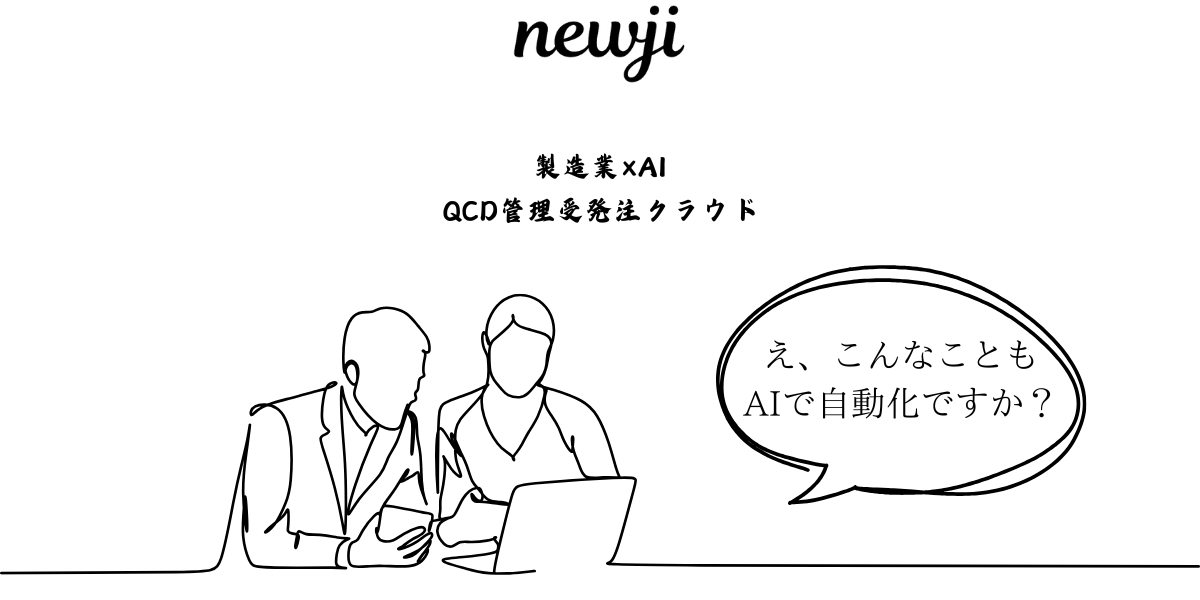
Manufacturing Process of Condenser Units and Power Efficiency Improvement
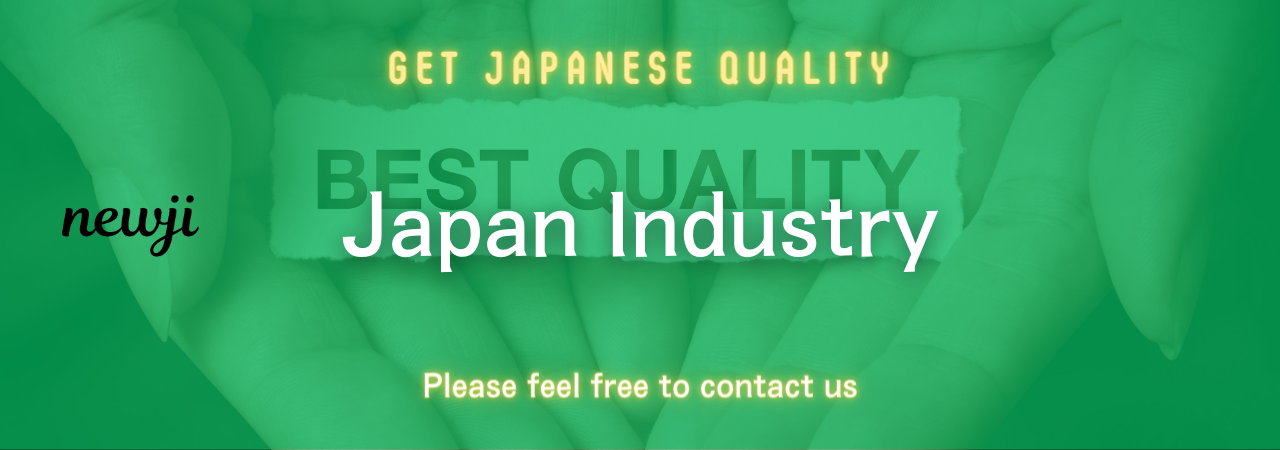
## Introduction
Condenser units play a critical role in various industries, particularly in HVAC (Heating, Ventilation, and Air Conditioning) systems.
They are essential in cooling applications and ensure systems run efficiently.
When it comes to enhancing power efficiency, understanding the manufacturing process of condenser units is crucial.
This article delves into the steps involved in manufacturing these units and how improvements in this process can lead to better power efficiency.
## Raw Material Selection
### Importance of Quality Materials
The first step in manufacturing condenser units is selecting high-quality raw materials.
The materials used significantly influence the durability, performance, and power efficiency of the final product.
Common materials include copper, aluminum, and various alloys that possess excellent thermal conductivity and resistance to corrosion.
### Sourcing and Inspection
Manufacturers source these materials from reliable suppliers to ensure consistency and quality.
Upon arrival, these materials undergo rigorous inspections to meet industry standards.
This step is vital to avoid defects that can compromise the efficiency of condenser units.
## Design and Engineering
### Custom Design
Design and engineering play a pivotal role in the functionality and efficiency of condenser units.
Engineers use advanced software tools to design units that optimize airflow and heat exchange.
Each design is tailored to meet specific requirements, whether for residential, commercial, or industrial applications.
### Prototyping
Before mass production, prototypes are developed to test the design’s feasibility.
These prototypes undergo a series of lab tests to evaluate performance, durability, and efficiency.
The feedback from these tests directs any necessary design adjustments.
## Production Process
### Sheet Metal Fabrication
Sheet metal fabrication marks the beginning of the production process.
Machinery cuts and shapes metal sheets into the required dimensions for various components of the condenser unit.
Precision cutting is crucial to ensure proper fit and performance.
### Coil Manufacturing
The coils are the heart of the condenser units, responsible for heat exchange.
Copper or aluminum tubes are shaped into coils and finned to increase the surface area for better heat dissipation.
These coils undergo several processes such as bending, finning, and brazing.
Proper alignment and spacing are essential to maintain optimal airflow and heat transfer.
### Assembly Line
The assembly line integrates all the manufactured components.
Technicians assemble parts like the coils, fans, and housing structure with meticulous care.
Fasteners, adhesives, and welding techniques ensure components are securely attached for durability.
Automated systems are often employed for tasks requiring high precision.
### Quality Control
At each stage of the production process, quality control checks are imperative.
From visual inspections to functional tests, quality control ensures that every unit meets the specified standards.
Advanced diagnostic tools help identify subpar components that need improvement or replacement.
## Finishing and Coating
### Rust and Corrosion Protection
Post-assembly, the units undergo finishing processes to protect against rust and corrosion.
Special coatings are applied to metal surfaces, adding a layer of protection against environmental elements.
These coatings also enhance the aesthetic appeal of the final product.
### Painting
Additional painting may be done for cosmetic purposes or to denote specific service lines.
Environmental considerations are taken into account when selecting paints and coatings, ensuring they are eco-friendly and durable.
## Testing and Certification
### Performance Testing
Before packaging, each condenser unit undergoes rigorous testing to ensure it meets regulatory standards and performance criteria.
Testing includes evaluating cooling efficiency, power consumption, noise levels, and overall functionality.
Units are tested under various conditions to simulate real-world scenarios.
### Certification
Once a unit passes all performance tests, it is certified for use.
Certifications from recognized bodies assure customers of the product’s quality and efficiency.
This step is crucial for compliance with industry regulations and boosting consumer trust.
## Packaging and Distribution
### Secure Packaging
Proper packaging is essential to protect units during transportation.
Packaging materials are selected to prevent physical damage and contamination.
Securing parts with shock-absorbent materials helps maintain the integrity of the product during transit.
### Efficient Distribution
Distribution logistics are planned meticulously to ensure timely delivery to customers and retailers.
Efficient distribution channels minimize lead times and reduce the carbon footprint associated with transportation.
## Power Efficiency Improvements
### Innovative Technologies
To improve power efficiency, manufacturers continually invest in innovative technologies.
Advancements in materials science, aerodynamics, and electronics contribute to the enhanced efficiency of condenser units.
For example, using variable speed motors allows the unit to adjust its performance based on load requirements, conserving energy.
### Maintenance and Upgrades
Regular maintenance and timely upgrades play a vital role in maintaining the efficiency of condenser units.
Manufacturers provide guidelines and support for users to ensure their units perform optimally.
Offering upgrade kits can also help older units meet new efficiency standards.
### Research and Development
Ongoing research and development efforts identify new ways to enhance the performance and efficiency of condenser units.
Collaborations with research institutions and universities often lead to breakthrough innovations that set industry benchmarks.
## Conclusion
The manufacturing process of condenser units is intricate but essential for ensuring high performance and power efficiency.
From raw material selection and design to production, testing, and distribution, each stage plays a significant role in the final product’s efficiency.
By understanding and continuously improving these processes, manufacturers can produce condenser units that not only perform well but also contribute to energy conservation and sustainability.
資料ダウンロード
QCD調達購買管理クラウド「newji」は、調達購買部門で必要なQCD管理全てを備えた、現場特化型兼クラウド型の今世紀最高の購買管理システムとなります。
ユーザー登録
調達購買業務の効率化だけでなく、システムを導入することで、コスト削減や製品・資材のステータス可視化のほか、属人化していた購買情報の共有化による内部不正防止や統制にも役立ちます。
NEWJI DX
製造業に特化したデジタルトランスフォーメーション(DX)の実現を目指す請負開発型のコンサルティングサービスです。AI、iPaaS、および先端の技術を駆使して、製造プロセスの効率化、業務効率化、チームワーク強化、コスト削減、品質向上を実現します。このサービスは、製造業の課題を深く理解し、それに対する最適なデジタルソリューションを提供することで、企業が持続的な成長とイノベーションを達成できるようサポートします。
オンライン講座
製造業、主に購買・調達部門にお勤めの方々に向けた情報を配信しております。
新任の方やベテランの方、管理職を対象とした幅広いコンテンツをご用意しております。
お問い合わせ
コストダウンが利益に直結する術だと理解していても、なかなか前に進めることができない状況。そんな時は、newjiのコストダウン自動化機能で大きく利益貢献しよう!
(Β版非公開)