- お役立ち記事
- Manufacturing Process of Cup Holders for Cars and Improvement in Stability
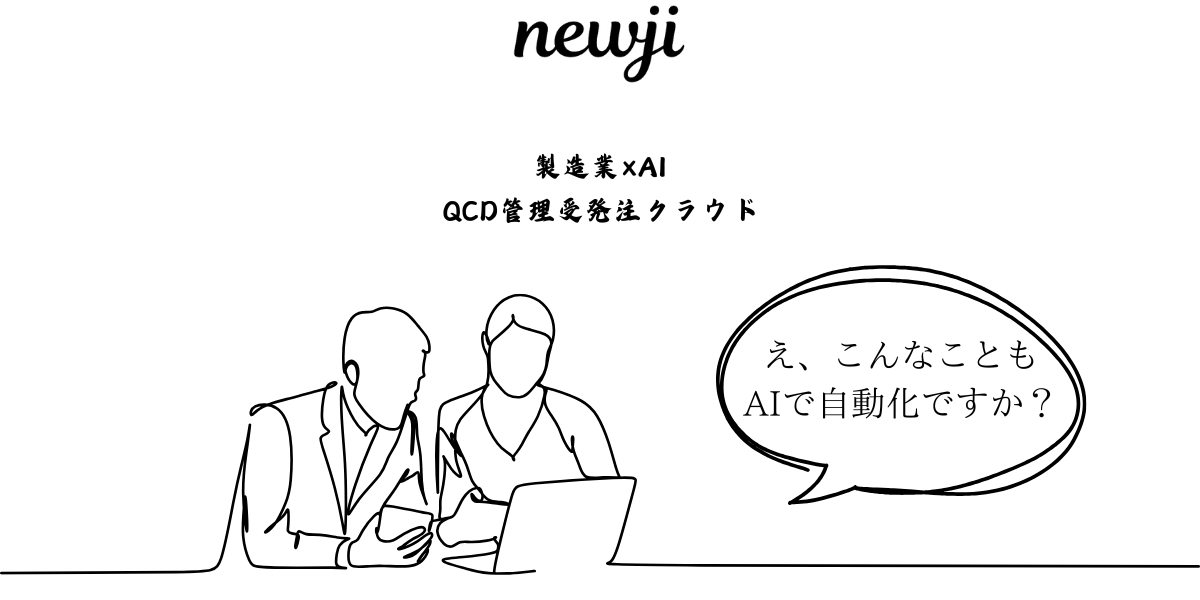
Manufacturing Process of Cup Holders for Cars and Improvement in Stability
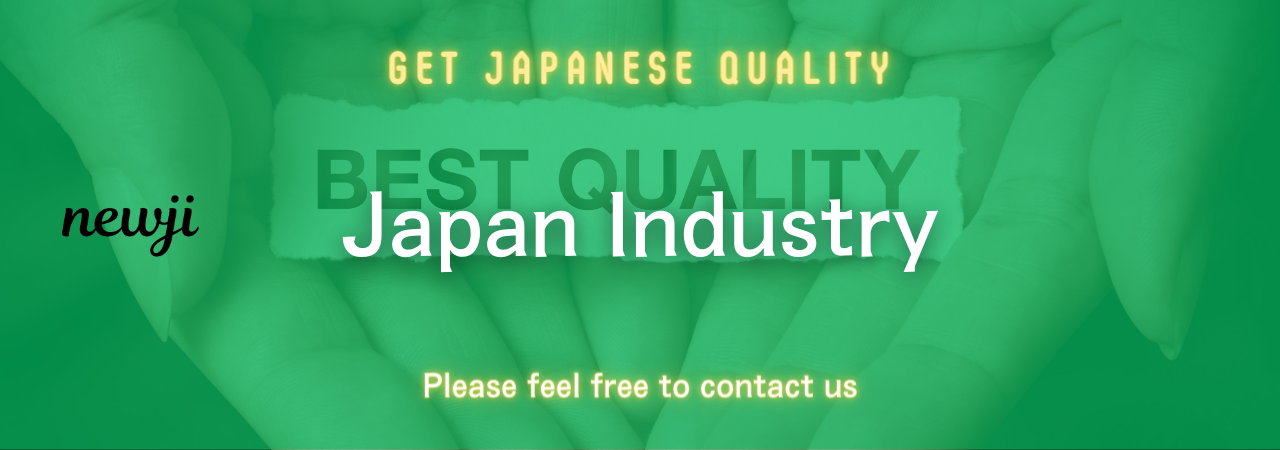
Cup holders in cars might seem like a small component, but they play a significant role in enhancing the driving experience.
Stability and convenience are crucial for these often-overlooked accessories.
This article delves into the manufacturing process of car cup holders and the advances made to improve their stability.
目次
Material Selection
The first step in the manufacturing of car cup holders is selecting the right material.
Car manufacturers usually opt for durable and lightweight materials such as plastic, silicone, or metal.
Factors like cost, durability, and ease of production are considered when choosing the material.
Plastic
Plastic is the most commonly used material for car cup holders.
It is cost-effective, lightweight, and can be easily molded into various shapes.
Manufacturers often use ABS (acrylonitrile butadiene styrene) plastic for its strength and resistance to heat.
Silicone
Silicone is another popular material due to its flexibility and non-slip properties.
Silicone cup holders are designed to grip the cup securely, reducing the chances of spills.
They are also heat-resistant, making them ideal for holding hot beverages.
Metal
Metal cup holders, though less common, are used in premium car models.
They offer superior durability and add a touch of elegance to the car’s interior.
Aluminum and stainless steel are the preferred metals due to their resistance to rust and corrosion.
Design and Prototyping
Once the material is selected, the next step is designing the cup holder.
The design process involves creating 3D models and prototypes to ensure the cup holder fits perfectly within the car’s interior.
3D Modeling
3D modeling software is used to create detailed designs of the cup holder.
This allows designers to visualize the final product and make necessary adjustments before production.
The design must accommodate various cup sizes and integrate seamlessly with the car’s design.
Prototyping
Prototyping involves creating a physical model of the cup holder using 3D printing technology.
This step is crucial for testing the fit and stability of the cup holder.
Any issues identified during prototyping are addressed before moving on to mass production.
Manufacturing
With the design finalized, the next step is the manufacturing process.
This involves molding, assembly, and quality control to ensure the cup holders meet the required standards.
Injection Molding
Injection molding is the most common method used for manufacturing plastic cup holders.
The plastic material is melted and injected into a mold to form the cup holder’s shape.
Once cooled, the cup holders are removed from the mold and trimmed to remove any excess material.
Silicone Molding
For silicone cup holders, the material is poured into a mold and left to set.
Silicone molds are often created using a two-part process to ensure the final product has a smooth finish.
The cup holders are then removed and inspected for any defects.
Metal Fabrication
Metal cup holders are fabricated using techniques such as stamping and welding.
The metal sheets are stamped into the desired shape and then welded together.
The cup holders are polished and coated to prevent rust and enhance their appearance.
Quality Control
Quality control is a critical step in the manufacturing process.
Each cup holder undergoes rigorous testing to ensure it meets the required standards for durability and stability.
Load Testing
Load testing involves placing different weights in the cup holder to ensure it can hold various cup sizes without breaking.
This test helps identify any weaknesses in the design or material.
Heat Resistance
Heat resistance testing ensures the cup holder can withstand high temperatures without deforming or melting.
This is particularly important for cup holders that will hold hot beverages.
Fit and Finish
The final inspection involves checking the fit and finish of the cup holder.
This includes ensuring there are no sharp edges and the cup holder fits perfectly within the designated space in the car.
Improving Stability
Enhancing the stability of car cup holders is essential to prevent spills and improve the driving experience.
Several innovations have been made to achieve this.
Adjustable Holders
Adjustable cup holders can accommodate different cup sizes by expanding or contracting.
This feature ensures a snug fit, reducing the chances of the cup tipping over.
Non-Slip Materials
Using non-slip materials like silicone in the cup holder design helps grip the cup securely.
This reduces movement and minimizes the risk of spills.
Weighted Bases
Adding a weighted base to the cup holder improves stability by lowering the center of gravity.
This makes it less likely for the cup to tip over, especially during sudden stops or sharp turns.
Conclusion
The manufacturing process of car cup holders involves meticulous planning, material selection, and rigorous testing.
Advancements in design and materials have significantly improved their stability and functionality.
As car manufacturers continue to innovate, we can expect even more convenient and stable cup holders in future car models.
資料ダウンロード
QCD調達購買管理クラウド「newji」は、調達購買部門で必要なQCD管理全てを備えた、現場特化型兼クラウド型の今世紀最高の購買管理システムとなります。
ユーザー登録
調達購買業務の効率化だけでなく、システムを導入することで、コスト削減や製品・資材のステータス可視化のほか、属人化していた購買情報の共有化による内部不正防止や統制にも役立ちます。
NEWJI DX
製造業に特化したデジタルトランスフォーメーション(DX)の実現を目指す請負開発型のコンサルティングサービスです。AI、iPaaS、および先端の技術を駆使して、製造プロセスの効率化、業務効率化、チームワーク強化、コスト削減、品質向上を実現します。このサービスは、製造業の課題を深く理解し、それに対する最適なデジタルソリューションを提供することで、企業が持続的な成長とイノベーションを達成できるようサポートします。
オンライン講座
製造業、主に購買・調達部門にお勤めの方々に向けた情報を配信しております。
新任の方やベテランの方、管理職を対象とした幅広いコンテンツをご用意しております。
お問い合わせ
コストダウンが利益に直結する術だと理解していても、なかなか前に進めることができない状況。そんな時は、newjiのコストダウン自動化機能で大きく利益貢献しよう!
(Β版非公開)