- お役立ち記事
- Manufacturing Process of Digital Writing Pads and Enhancing Response Speed
Manufacturing Process of Digital Writing Pads and Enhancing Response Speed
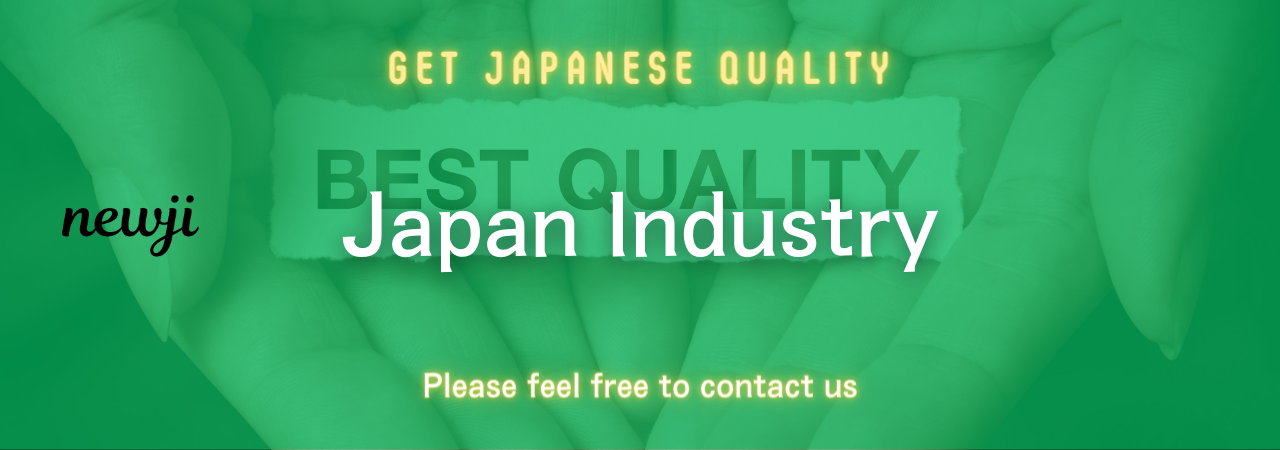
Digital writing pads, commonly known as digital notepads or e-writers, have become an essential tool in modern education, business, and personal organization.
They make it easy to take notes, create sketches, or annotate documents seamlessly.
Manufacturing these devices involves intricate processes to ensure high performance and reliable functionality.
In this article, we will explore the manufacturing process of digital writing pads and discuss ways to enhance their response speed.
目次
Design and Planning
The manufacturing process begins with comprehensive design and planning.
Engineers and designers work together to conceptualize the digital writing pad, keeping user experience, functionality, and cost in mind.
They draft the initial sketches and blueprints, focusing on the layout of the screen, buttons, and internal components.
Material Selection
Choosing the right materials is crucial for the durability and performance of the digital writing pad.
Common materials include plastic, glass, and various metals.
The screen is often made of LCD or e-paper, depending on the intended use of the device.
The selection of materials also affects the weight, thickness, and overall feel of the digital writing pad.
Prototype Development
Once the design is finalized, a prototype is created.
This prototype allows engineers to assess the feasibility of the design and make necessary adjustments.
It includes all critical components such as the screen, battery, processor, and stylus.
Testing the prototype helps identify potential issues and areas for improvement.
Electronic Components Assembly
After the prototype is approved, the next step involves the assembly of electronic components.
Screen Production
The screen is one of the most vital parts of a digital writing pad.
For LCD screens, the manufacturing process includes creating liquid crystal cells, assembling backlight units, and sealing the cells appropriately.
E-paper screens, on the other hand, involve the arrangement of tiny capsules filled with black and white particles that respond to electric fields.
Processor and Battery Installation
At this stage, the processor and battery are installed on the main circuit board.
The processor is responsible for interpreting the input from the stylus and converting it into digital signals, while the battery ensures long-lasting power for the device.
High-capacity lithium-ion batteries are commonly used due to their efficiency and lightweight nature.
Final Assembly and Quality Control
Once all electronic components are in place, the final assembly of the digital writing pad begins.
This step ensures that all parts fit together seamlessly and function correctly.
Casing and Housing
The casing and housing of the digital writing pad are assembled around the internal components.
The outer shell is typically made of plastic or aluminum, offering protection and a sleek look.
The device is then sealed to safeguard against dust, moisture, and damage from external forces.
Software Integration
Software integration is another critical aspect of the manufacturing process.
The digital writing pad’s firmware and operating system are installed, enabling the device to perform tasks like recognizing handwriting, storing notes, and syncing with other devices.
Custom software may also be developed to enhance specific functionalities based on the target market.
Quality Control Testing
Quality control testing is essential to ensure that each digital writing pad meets industry standards.
Various tests, including functionality checks, durability tests, and battery life assessments, are conducted.
Devices that pass these tests are then packaged and prepared for distribution.
Enhancing Response Speed
Enhancing the response speed of digital writing pads is crucial for a smooth and efficient user experience.
Here are some strategies to achieve this goal.
Optimizing Processor Performance
One of the main factors that affect response speed is the processor’s performance.
Using a faster processor can significantly reduce lag and improve the device’s responsiveness.
Additionally, optimizing the software to leverage the processor’s capabilities can further enhance speed.
Improving Stylus Technology
The stylus plays a significant role in determining the response speed.
Advanced stylus technologies such as electro-magnetic resonance (EMR) or active capacitive styluses provide better accuracy and responsiveness.
Upgrading the stylus technology can result in a more natural and immediate writing experience.
Reducing Screen Latency
Screen latency is another critical aspect.
Reducing the time it takes for the screen to update or refresh can improve the overall response speed.
Manufacturers can achieve this by using screens with higher refresh rates or low-latency e-paper displays.
Efficient Software Algorithms
Optimized software algorithms can process input data more effectively and quickly.
Engineers often refine handwriting recognition and input processing algorithms to ensure minimal delay between the stylus movement and the digital output.
User Experience and Continuous Improvement
Lastly, focusing on user experience and continuous improvement are essential for the ongoing success of digital writing pads.
Manufacturers must gather user feedback and regularly update their devices to address any issues and incorporate new features.
User Feedback Collection
Collecting user feedback provides valuable insights into the performance and functionality of the digital writing pad.
Surveys, reviews, and direct customer support interactions can highlight areas for improvement and new features that users desire.
Regular Firmware Updates
Regular firmware updates ensure that the digital writing pad remains up-to-date with the latest technology and security standards.
These updates can also include performance enhancements and bug fixes that improve overall device responsiveness and functionality.
In conclusion, the manufacturing process of digital writing pads involves meticulous planning, advanced technology, and stringent quality control measures.
By continuously seeking ways to enhance response speed and user experience, manufacturers can produce reliable and high-performing devices that cater to the evolving needs of users.
資料ダウンロード
QCD調達購買管理クラウド「newji」は、調達購買部門で必要なQCD管理全てを備えた、現場特化型兼クラウド型の今世紀最高の購買管理システムとなります。
ユーザー登録
調達購買業務の効率化だけでなく、システムを導入することで、コスト削減や製品・資材のステータス可視化のほか、属人化していた購買情報の共有化による内部不正防止や統制にも役立ちます。
NEWJI DX
製造業に特化したデジタルトランスフォーメーション(DX)の実現を目指す請負開発型のコンサルティングサービスです。AI、iPaaS、および先端の技術を駆使して、製造プロセスの効率化、業務効率化、チームワーク強化、コスト削減、品質向上を実現します。このサービスは、製造業の課題を深く理解し、それに対する最適なデジタルソリューションを提供することで、企業が持続的な成長とイノベーションを達成できるようサポートします。
オンライン講座
製造業、主に購買・調達部門にお勤めの方々に向けた情報を配信しております。
新任の方やベテランの方、管理職を対象とした幅広いコンテンツをご用意しております。
お問い合わせ
コストダウンが利益に直結する術だと理解していても、なかなか前に進めることができない状況。そんな時は、newjiのコストダウン自動化機能で大きく利益貢献しよう!
(Β版非公開)