- お役立ち記事
- Manufacturing Process of Electric Brushes and Rotational Mechanism Design
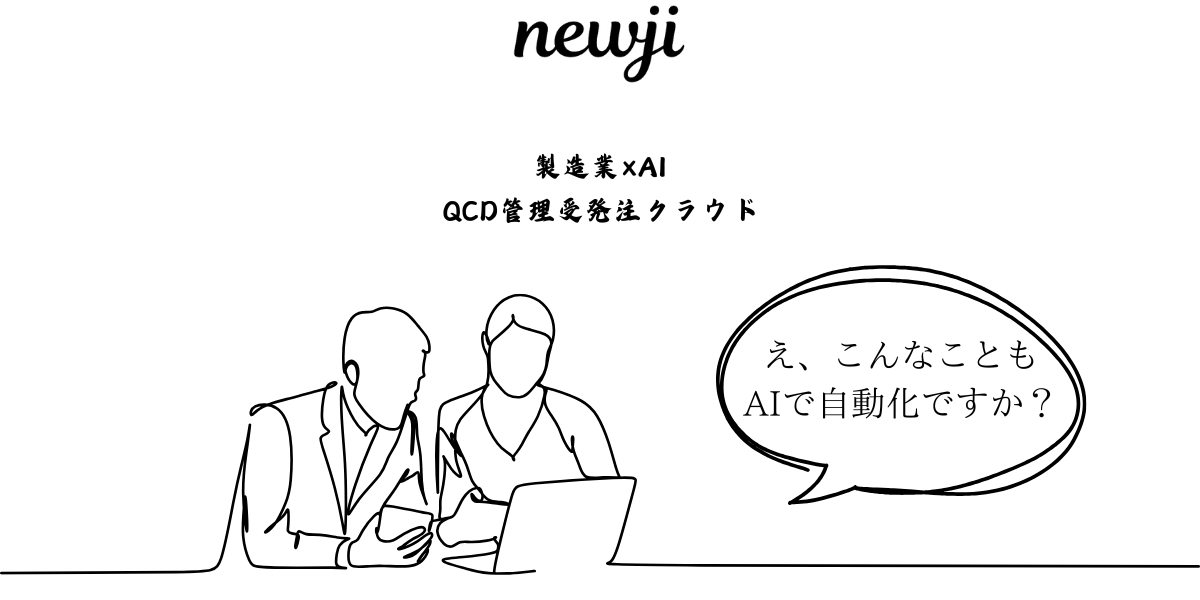
Manufacturing Process of Electric Brushes and Rotational Mechanism Design
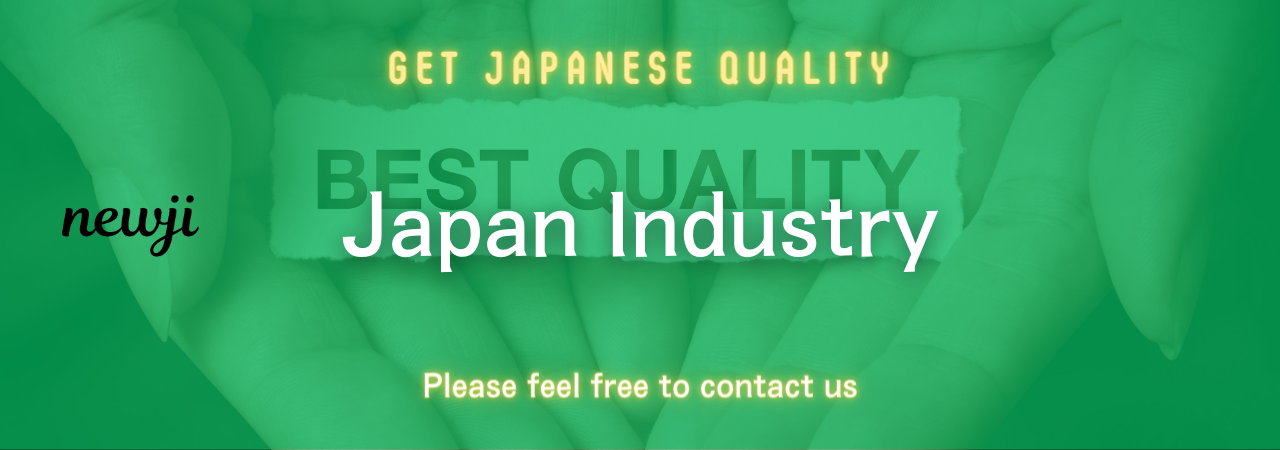
Electric brushes and rotational mechanisms are crucial components in many electrical devices and machines.
Their efficiency and reliability are essential for the performance of these devices.
Understanding the manufacturing process and design of these components is key to producing high-quality products.
In this article, we’ll explore the intricacies of making electric brushes and the principles behind designing an effective rotational mechanism.
目次
What Are Electric Brushes?
Electric brushes, commonly known as carbon brushes, are small devices that conduct electrical current between stationary wires and moving parts in a motor.
They play a critical role in ensuring the proper function of electric motors and generators.
These components are typically made from carbon, graphite, or a combination of both, which are chosen for their conductive properties and durability.
Types of Electric Brushes
There are several types of electric brushes, each designed for specific applications.
The most common types include:
– **Carbon Brushes:** Made from pure carbon, these are known for their excellent conductivity and longevity.
– **Graphite Brushes:** These are made from graphite and have good lubricating properties, reducing wear and tear on the commutator.
– **Metal Graphite Brushes:** A combination of graphite and metal, often copper, providing enhanced conductivity and mechanical strength.
– **Electrographite Brushes:** These are carbon brushes that have been heat-treated to improve their properties, like hardness and temperature resistance.
Manufacturing Process of Electric Brushes
The manufacturing process of electric brushes involves several steps, each crucial for producing a high-quality product.
Material Selection and Mixing
The first step is selecting the appropriate materials for the brush.
This can include pure carbon, graphite, or metal graphite, depending on the desired properties of the final product.
These materials are then mixed thoroughly to ensure a uniform composition.
This step is vital as it influences the performance and durability of the brush.
Molding and Forming
Once the materials are mixed, they are shaped into the desired form.
This is usually done through a process called molding, where the material is compressed into a mold under high pressure.
The shape and size of the mold depend on the specific requirements of the brush.
This step ensures that the brush has the correct dimensions and structure.
Heat Treatment
After molding, the brushes undergo a heat treatment process to improve their physical properties.
This involves heating the brushes to a high temperature to enhance their hardness and temperature resistance.
Heat treatment makes the brushes more durable and capable of withstanding the rigors of their operational environment.
Final Processing
The final step in the manufacturing process is finishing.
This involves grinding and polishing the brushes to achieve the desired surface finish.
Proper finishing ensures that the brushes have a smooth surface, which is essential for reducing friction and wear on the commutator.
Additionally, the brushes may be impregnated with lubricants to further enhance their performance.
Designing Rotational Mechanisms
A rotational mechanism is a system that converts electrical energy into mechanical rotation, typically used in electric motors and generators.
The efficiency and performance of these mechanisms are directly influenced by the design.
Here are the key considerations in designing an effective rotational mechanism.
Understanding the Basics
Before delving into the specifics, it’s important to understand the basic principles of rotational mechanisms.
These mechanisms consist of several components, including a rotor, stator, bearings, and brushes.
The rotor is the moving part, while the stator is stationary.
Bearings support the rotor, allowing it to spin smoothly, and brushes maintain electrical contact with the rotating shaft.
Material Selection
Choosing the right materials for the components is crucial for the performance of the rotational mechanism.
For instance, the rotor and stator require materials with high magnetic permeability to ensure efficient energy conversion.
Common materials include silicon steel and laminated cores.
Bearings are typically made from materials like steel or ceramic to provide durability and reduce friction.
Precision Engineering
Precision engineering is essential for designing a successful rotational mechanism.
This involves accurately machining the components to tight tolerances to ensure proper fit and function.
For example, the gap between the rotor and stator needs to be minimized to reduce energy losses and improve efficiency.
Additionally, the alignment of the bearings is critical for smooth operation and minimizing wear.
Cooling and Lubrication
Heat generated during operation can affect the performance and lifespan of the rotational mechanism.
Efficient cooling systems are necessary to dissipate this heat and maintain optimal operating temperatures.
This can include fans, cooling fins, or liquid cooling systems.
Lubrication is also vital for reducing friction and wear on moving parts.
Proper lubrication ensures the longevity of the bearings and other components.
Testing and Quality Control
Once the rotational mechanism is designed and assembled, rigorous testing and quality control measures are necessary to ensure its performance and reliability.
This includes running the mechanism under different operating conditions to assess its efficiency, temperature rise, and mechanical stability.
Any defects or performance issues identified during testing need to be addressed through design modifications or material improvements.
Conclusion
The manufacturing process of electric brushes and the design of rotational mechanisms are intricate and require careful attention to detail.
Understanding the materials, processes, and principles involved is essential for producing high-quality components that ensure the efficient and reliable operation of electrical devices and machines.
By focusing on precision, material selection, and rigorous testing, manufacturers can create products that meet the demands of various applications, from small household appliances to large industrial machinery.
資料ダウンロード
QCD調達購買管理クラウド「newji」は、調達購買部門で必要なQCD管理全てを備えた、現場特化型兼クラウド型の今世紀最高の購買管理システムとなります。
ユーザー登録
調達購買業務の効率化だけでなく、システムを導入することで、コスト削減や製品・資材のステータス可視化のほか、属人化していた購買情報の共有化による内部不正防止や統制にも役立ちます。
NEWJI DX
製造業に特化したデジタルトランスフォーメーション(DX)の実現を目指す請負開発型のコンサルティングサービスです。AI、iPaaS、および先端の技術を駆使して、製造プロセスの効率化、業務効率化、チームワーク強化、コスト削減、品質向上を実現します。このサービスは、製造業の課題を深く理解し、それに対する最適なデジタルソリューションを提供することで、企業が持続的な成長とイノベーションを達成できるようサポートします。
オンライン講座
製造業、主に購買・調達部門にお勤めの方々に向けた情報を配信しております。
新任の方やベテランの方、管理職を対象とした幅広いコンテンツをご用意しております。
お問い合わせ
コストダウンが利益に直結する術だと理解していても、なかなか前に進めることができない状況。そんな時は、newjiのコストダウン自動化機能で大きく利益貢献しよう!
(Β版非公開)