- お役立ち記事
- Manufacturing Process of Electric Chainsaws and Designing Safety Mechanisms
月間76,176名の
製造業ご担当者様が閲覧しています*
*2025年3月31日現在のGoogle Analyticsのデータより
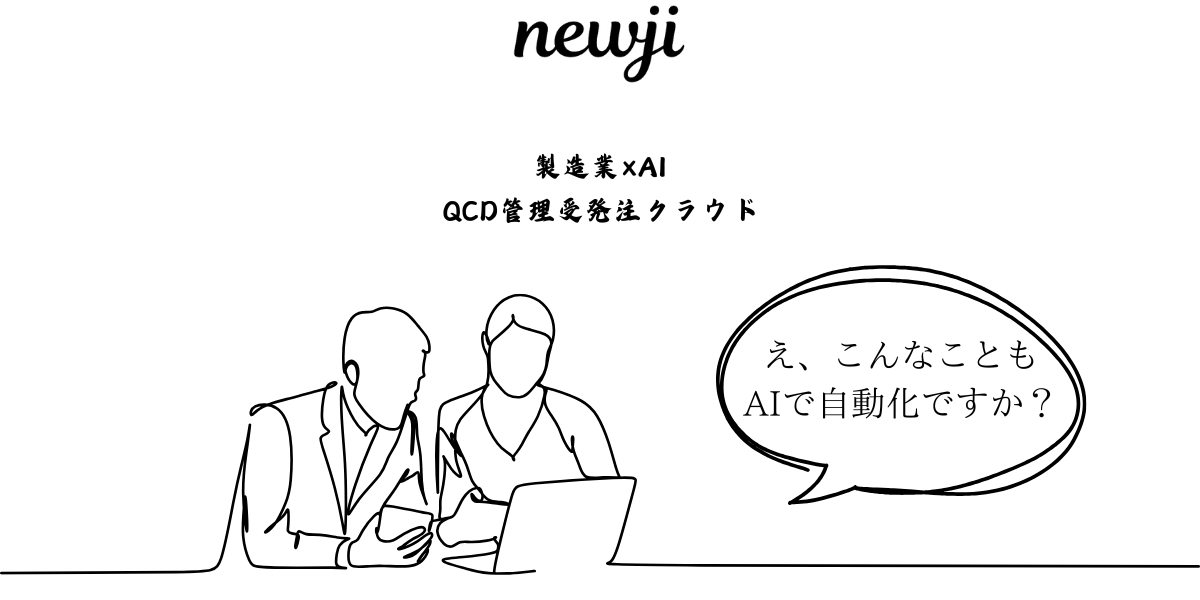
Manufacturing Process of Electric Chainsaws and Designing Safety Mechanisms
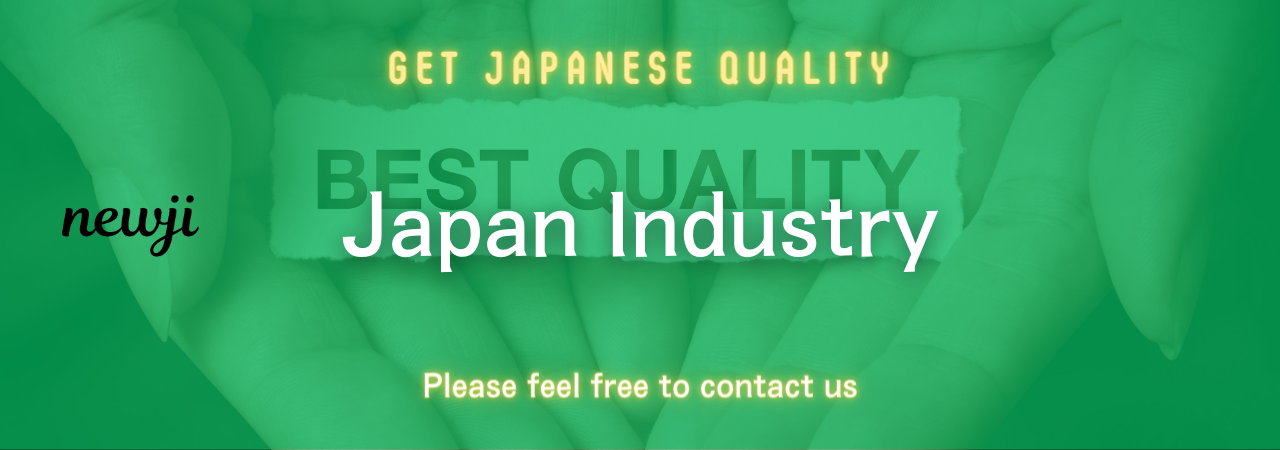
Electric chainsaws have become an essential tool for many industrial and domestic applications.
Their efficiency and ease of use make them a preferred choice over traditional gasoline-powered saws.
Understanding the manufacturing process and safety design of electric chainsaws can offer valuable insights into their functionality and reliability.
目次
Materials and Components Used
Electric chainsaws are composed of several key materials and components, each contributing to their performance and durability.
The primary materials include high-quality plastics, metals, rubber, and specialized alloys.
The casing of the chainsaw is typically made from durable plastic to reduce weight while maintaining structural integrity.
Metals like steel and aluminum are utilized for critical components such as the chain, bar, and internal mechanisms.
Rubber is often used for handles and grips to ensure comfort and reduce vibrations during operation.
The Motor
The motor is the heart of an electric chainsaw.
It is usually an efficient, high-torque motor designed for powerful cutting action.
Manufacturers select motors based on their ability to deliver consistent performance while maintaining energy efficiency.
Brushless motors are increasingly popular due to their longer lifespan, lower maintenance requirements, and reduced heat generation.
The Chain and Bar
The cutting chain is crafted from hardened steel to withstand rigorous use and maintain sharpness over time.
The guide bar, which supports the chain, is made from either steel or composite materials.
The bar’s length can vary depending on the intended use of the chainsaw, with longer bars suitable for larger trees and trunks while shorter bars are better for pruning and smaller cuts.
The Power Source
Electric chainsaws can be corded or cordless.
Corded chainsaws draw power directly from an electrical outlet, providing consistent power output without the need for battery recharge.
Cordless chainsaws rely on rechargeable lithium-ion batteries, offering greater mobility and ease of use, albeit with limited operational time per charge.
Manufacturing Process
The production of electric chainsaws involves several meticulous steps to ensure quality and reliability.
Design and Prototyping
The initial phase involves designing the chainsaw and creating prototypes.
Engineers use computer-aided design (CAD) software to create detailed blueprints and simulate performance.
Prototypes are produced to test ergonomics, safety features, and overall functionality.
These prototypes undergo rigorous testing to identify and rectify potential issues.
Component Manufacturing
Once the design is finalized, the components are manufactured.
Plastic components like the casing are produced using injection molding, while metal parts such as the chain and bar are fabricated using precision machining and heat treatment processes.
Motors are assembled from stators, rotors, and windings, with quality control measures ensuring each motor meets stringent performance criteria.
Assembly
The assembly process combines all the manufactured components into a complete chainsaw.
Workers or automated systems assemble the motor, chain, bar, and casing, integrating electronic components and wiring as needed.
Attention to detail during assembly is paramount, as improper assembly can lead to mechanical failures or safety hazards.
Quality Control
Quality control is an integral part of the manufacturing process.
Each chainsaw undergoes a series of tests to ensure it meets performance and safety standards.
These tests include functional checks, endurance tests, and safety assessments.
Chainsaws that pass quality control are packaged and prepared for distribution.
Designing Safety Mechanisms
Safety is a critical consideration in the design of electric chainsaws.
Several safety mechanisms are incorporated to protect users from potential hazards.
Chain Brake
A chain brake is one of the most important safety features in an electric chainsaw.
It stops the chain almost instantly in the event of a kickback, potentially preventing serious injury.
The chain brake is typically activated by a lever in front of the handguard, which the user’s hand naturally pushes forward in case of a sudden motion.
Safety Switch
Electric chainsaws are equipped with a safety switch or a two-step trigger system to prevent accidental activation.
The user must press the safety switch or engage the two-step trigger mechanism before the motor can be powered on.
This design minimizes the risk of unintentional operation when handling or transporting the chainsaw.
Chain Catcher
The chain catcher is a metal or plastic guard located near the base of the bar.
Its purpose is to catch the chain if it derails or breaks, preventing it from causing harm to the user.
This feature enhances user safety by containing the chain within the chainsaw’s body.
Anti-Vibration System
Prolonged use of a chainsaw can lead to hand and arm fatigue due to vibrations.
Modern electric chainsaws are designed with anti-vibration systems that use rubber mounts or springs to absorb vibrations.
This system not only improves user comfort but also minimizes the risk of long-term repetitive strain injuries.
Noise Reduction
Electric chainsaws are generally quieter than their gasoline counterparts.
Manufacturers incorporate noise reduction technologies, such as sound insulation and mufflers, to further reduce noise levels.
Lower noise output contributes to a safer working environment by allowing users to maintain awareness of their surroundings.
Conclusion
The manufacturing process and design of electric chainsaws are intricate and deliberate, focusing on performance, durability, and safety.
From material selection to component manufacturing and assembly, each step is optimized to produce reliable and efficient tools.
Safety mechanisms like chain brakes, safety switches, chain catchers, anti-vibration systems, and noise reduction features are critical to user safety and comfort.
Understanding these aspects underscores the importance of precision and quality in producing electric chainsaws that users can trust and rely upon for various cutting tasks.
資料ダウンロード
QCD管理受発注クラウド「newji」は、受発注部門で必要なQCD管理全てを備えた、現場特化型兼クラウド型の今世紀最高の受発注管理システムとなります。
ユーザー登録
受発注業務の効率化だけでなく、システムを導入することで、コスト削減や製品・資材のステータス可視化のほか、属人化していた受発注情報の共有化による内部不正防止や統制にも役立ちます。
NEWJI DX
製造業に特化したデジタルトランスフォーメーション(DX)の実現を目指す請負開発型のコンサルティングサービスです。AI、iPaaS、および先端の技術を駆使して、製造プロセスの効率化、業務効率化、チームワーク強化、コスト削減、品質向上を実現します。このサービスは、製造業の課題を深く理解し、それに対する最適なデジタルソリューションを提供することで、企業が持続的な成長とイノベーションを達成できるようサポートします。
製造業ニュース解説
製造業、主に購買・調達部門にお勤めの方々に向けた情報を配信しております。
新任の方やベテランの方、管理職を対象とした幅広いコンテンツをご用意しております。
お問い合わせ
コストダウンが利益に直結する術だと理解していても、なかなか前に進めることができない状況。そんな時は、newjiのコストダウン自動化機能で大きく利益貢献しよう!
(β版非公開)