- お役立ち記事
- Manufacturing Process of Electric Griddles and Heat Distribution Adjustment
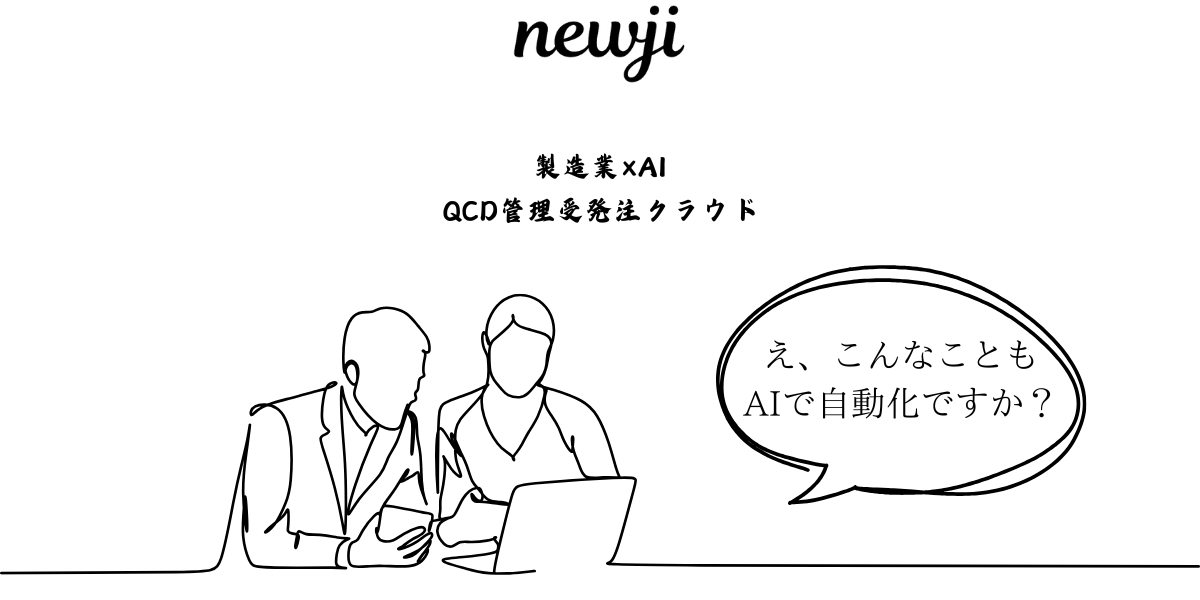
Manufacturing Process of Electric Griddles and Heat Distribution Adjustment
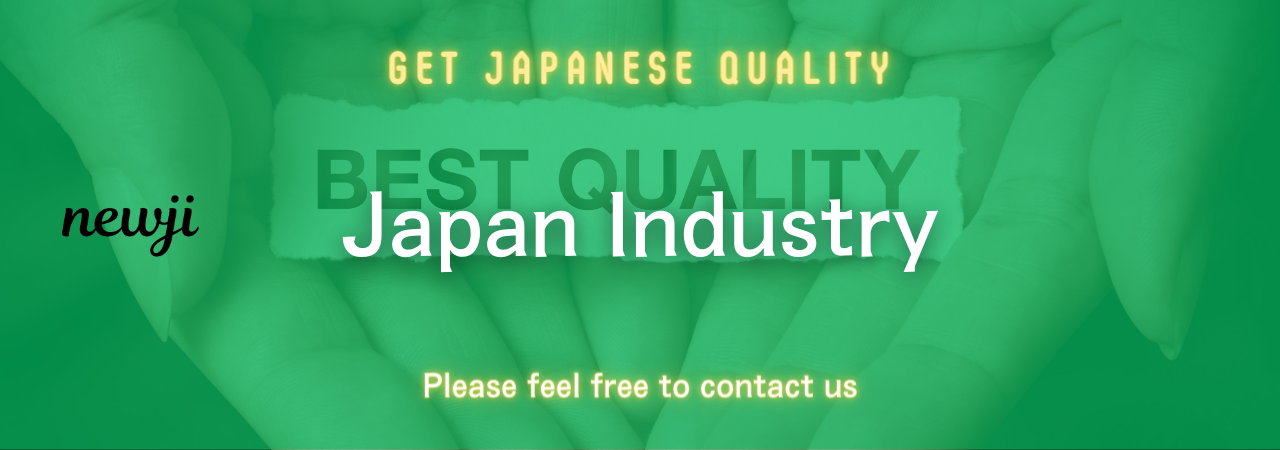
Electric griddles are increasingly popular kitchen appliances, known for their versatility in cooking a variety of foods.
Understanding the manufacturing process of electric griddles and how heat distribution is adjusted is crucial to appreciate the technology behind these useful devices.
Here’s a detailed look into how electric griddles are made and how manufacturers ensure even heat distribution for perfect cooking results.
目次
Design and Planning
The manufacturing process of electric griddles begins with careful design and planning.
Engineers and designers work together to create a blueprint that outlines every aspect of the griddle, from dimensions to materials used.
The design phase ensures that the final product will be efficient, safe, and easy to use.
Material Selection
Choosing the right materials is a crucial step in the design phase.
The griddle surface must be durable, heat-resistant, and non-stick. Common materials include stainless steel, cast iron, and non-stick coatings like Teflon.
The body of the griddle usually consists of heat-resistant plastic or metal.
Prototyping
Once the design and materials are selected, a prototype is created. This is a sample model of the electric griddle that will be tested for functionality and performance.
Any flaws or issues discovered during testing are addressed before moving forward with mass production.
Manufacturing Process
After the prototype has been perfected, the actual manufacturing of electric griddles begins.
This process involves several stages, each critical to ensuring the final product is of high quality.
Component Fabrication
The first step in manufacturing is fabricating individual components.
The griddle surface is created by cutting and shaping the selected material.
Metal parts are often stamped or pressed into the desired shapes, while non-stick coatings are applied using specialized equipment.
Plastic components are usually produced through injection molding, a process that involves injecting molten plastic into molds to form the required shapes.
Assembly
With all components fabricated, the next step is assembly.
Workers or automated machines assemble the griddles, attaching the heating elements to the griddle surface and securing the body and handles in place.
Electrical wiring is also installed to connect the heating elements to the controls.
Quality Control
Quality control is a vital part of the manufacturing process.
Each electric griddle is inspected for defects or imperfections.
Tests are conducted to ensure the griddle heats evenly and functions correctly. Out of specification products are either remanufactured or discarded.
Heat Distribution Adjustment
Ensuring even heat distribution is one of the most crucial aspects of electric griddle manufacturing.
Different techniques and technologies are employed to achieve this.
Heating Elements
The heating elements are the core components responsible for generating heat.
These elements can be made from various materials, including nichrome and other heat-conductive metals. They are strategically placed within the griddle to ensure even heat distribution.
Some high-end models use multiple heating elements to provide more uniform heating.
Thermostat and Temperature Control
Integrated thermostats help maintain consistent temperatures by monitoring the griddle’s surface temperature and adjusting the power supply to the heating elements accordingly.
Advanced models may feature digital temperature controls, allowing users to precisely set and maintain the desired cooking temperature.
Insulation
Proper insulation plays a significant role in heat distribution.
Insulating materials are used to prevent heat loss and ensure that the heat generated by the elements is evenly spread across the cooking surface.
High-quality insulation also enhances the safety and energy efficiency of the griddle.
Surface Design
The design of the griddle surface can also impact heat distribution.
Grooved or patterned surfaces help channel heat more evenly, while flat, smooth surfaces provide a consistent cooking area. The thickness of the griddle surface is also carefully calibrated to optimize heat retention and distribution.
Final Testing and Packaging
After manufacturing and assembling, final testing is performed to verify that the electric griddle meets all quality and safety standards.
Each unit undergoes thorough testing for performance, safety, and durability.
Performance Testing
Performance tests include checking the evenness of heat distribution, the accuracy of temperature controls, and the overall functionality of the griddle.
These tests ensure that the griddle performs as expected and can cook food evenly and efficiently.
Safety Testing
Safety tests are performed to ensure the product complies with industry safety standards.
This includes checking for electrical safety, ensuring there are no sharp edges, and verifying that the griddle does not overheat or pose other hazards.
Durability Testing
Durability tests simulate everyday use to ensure the griddle can withstand regular wear and tear.
This includes testing the non-stick surface for scratch resistance and ensuring that the handles and body are robust and reliable.
Packaging
Once the griddle passes all tests, it is cleaned, polished, and prepared for packaging.
Packaging not only protects the griddle during transportation but also provides essential information to the consumer, such as usage instructions, safety warnings, and warranty details.
Conclusion
The manufacturing process of electric griddles involves meticulous design, material selection, fabrication, assembly, and rigorous testing.
Attention to detail in every step ensures that the final product is safe, reliable, and efficient.
By understanding this process, consumers can appreciate the technology and craftsmanship that goes into making these versatile kitchen appliances.
With advancements in design and technology, modern electric griddles offer precise heat distribution and user-friendly controls, making them a valuable addition to any kitchen.
資料ダウンロード
QCD調達購買管理クラウド「newji」は、調達購買部門で必要なQCD管理全てを備えた、現場特化型兼クラウド型の今世紀最高の購買管理システムとなります。
ユーザー登録
調達購買業務の効率化だけでなく、システムを導入することで、コスト削減や製品・資材のステータス可視化のほか、属人化していた購買情報の共有化による内部不正防止や統制にも役立ちます。
NEWJI DX
製造業に特化したデジタルトランスフォーメーション(DX)の実現を目指す請負開発型のコンサルティングサービスです。AI、iPaaS、および先端の技術を駆使して、製造プロセスの効率化、業務効率化、チームワーク強化、コスト削減、品質向上を実現します。このサービスは、製造業の課題を深く理解し、それに対する最適なデジタルソリューションを提供することで、企業が持続的な成長とイノベーションを達成できるようサポートします。
オンライン講座
製造業、主に購買・調達部門にお勤めの方々に向けた情報を配信しております。
新任の方やベテランの方、管理職を対象とした幅広いコンテンツをご用意しております。
お問い合わせ
コストダウンが利益に直結する術だと理解していても、なかなか前に進めることができない状況。そんな時は、newjiのコストダウン自動化機能で大きく利益貢献しよう!
(Β版非公開)