- お役立ち記事
- Manufacturing Process of Electric Kettles and Assembly Procedures
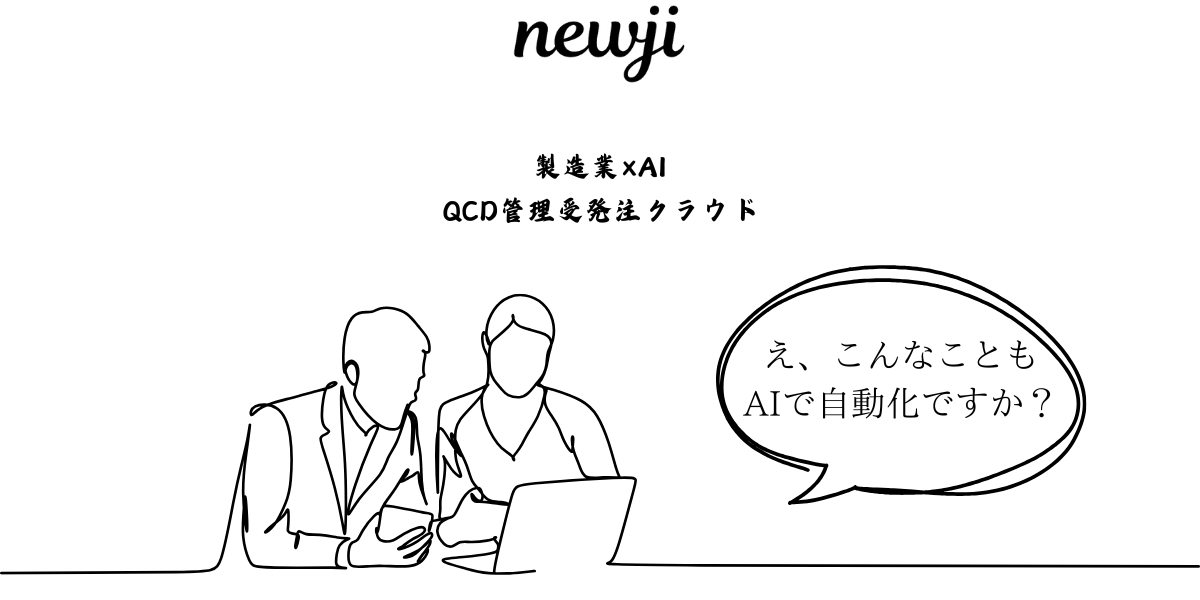
Manufacturing Process of Electric Kettles and Assembly Procedures
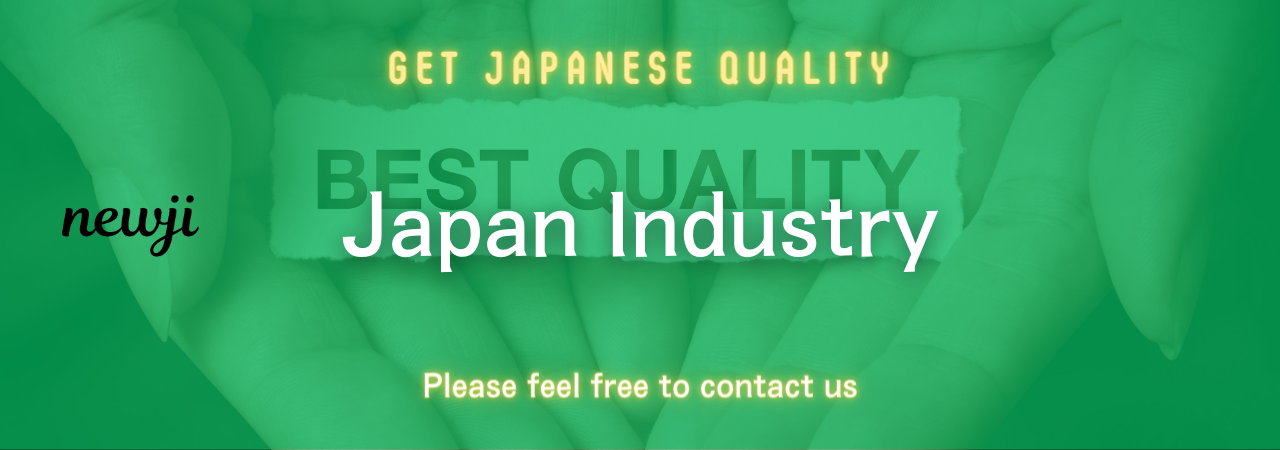
Electric kettles have become essential appliances in many households, providing the convenience of boiling water quickly and efficiently.
Understanding how these handy gadgets are manufactured and assembled can give you insight into the intricate processes involved.
Let’s take a closer look at each stage in the manufacturing and assembly of electric kettles.
目次
Materials and Components
Before diving into the manufacturing process, it’s important to understand the key materials and components required to build an electric kettle.
Generally, electric kettles consist of the following primary components: the heating element, the body or shell, the power base, the thermostat, and various smaller parts like handles and lids.
Heating Element
The heating element is typically made from a coil of metallic material that has high electrical resistance such as nichrome.
When electricity passes through the coil, it heats up and transfers heat to the water.
Body or Shell
The body of the kettle is usually made from materials like plastic, stainless steel, or glass.
Each material has its advantages such as durability, heat resistance, and aesthetic appeal.
Power Base and Thermostat
The power base supplies electricity to the heating element and houses the thermostat.
The thermostat controls the temperature and ensures the kettle switches off automatically when the water reaches the desired boiling point.
Manufacturing Process
The manufacturing process of electric kettles typically involves several stages: designing, molding, assembly, and quality control.
Designing
Every electric kettle starts with a design phase.
Engineers and designers collaborate to create a functional and aesthetically pleasing model.
They use computer-aided design (CAD) software to sketch the initial design and perform simulations to predict how it will function.
The design includes specifications for the size, shape, materials, and electrical components.
Molding
Once the design is approved, the next step is to create molds for the various kettle components.
Molds are made using precise measurements to ensure each part fits together perfectly.
For plastic and stainless steel bodies, injection molding is the most common method.
Molten plastic or metal is injected into the molds and allowed to cool and harden.
Production of Heating Elements
The heating element is manufactured by winding nichrome wire into coils.
These coils are then covered with an insulating material to ensure they are safe to use.
The ends of the coils are connected to terminals that will later be attached to the power base.
Assembly
With all components ready, the assembly process can begin.
This stage involves several key steps:
1. **Attaching the Heating Element**:
The heating element is installed into the base of the kettle body.
It must be secured firmly to ensure good heat transfer and electrical connectivity.
2. **Installing the Thermostat and Controls**:
The thermostat and other control circuits are placed into the power base.
These components are wired to the heating element terminals.
3. **Assembling the Body**:
The body of the kettle, including the handle and lid, is securely assembled.
Manufacturers often use screws or ultrasonic welding to attach these parts.
4. **Combining Sub-Assemblies**:
The power base and kettle body are combined into one complete unit.
Any additional features like water level indicators or LED lights are also installed at this stage.
Quality Control
Quality control is crucial to ensure that each kettle meets safety and performance standards.
Manufacturers typically conduct a series of tests during and after assembly.
Electrical Testing
Every kettle undergoes electrical testing to ensure that the heating element functions correctly.
Engineers test the kettle’s ability to heat water to the boiling point and verify that the thermostat switches off the power as intended.
Safety Checks
Safety checks are performed to ensure there are no electrical hazards.
This includes checking the insulation on wires and verifying that no parts are exposed to the risk of shocks or short circuits.
Durability Testing
Durability tests help to confirm that the kettle can withstand repeated use.
This includes testing the handle’s strength, the lid’s fit, and the overall structural integrity of the kettle.
Packing and Shipping
Once the electric kettles pass all quality control checks, they are ready for packing.
Each unit is packaged securely, often with protective foam or cardboard to prevent damage during transportation.
The kettle is then boxed along with user manuals, warranty cards, and other necessary documents.
Finally, the packaged kettles are shipped to retailers or directly to consumers.
Final Thoughts
Understanding the manufacturing process of electric kettles reveals the complexity and precision involved in producing these useful appliances.
From designing and molding to assembly and quality control, each stage ensures that the final product is both functional and safe to use.
So, next time you enjoy a hot cup of tea or coffee, you’ll have a better appreciation for the intricate work that brought your electric kettle to life.
資料ダウンロード
QCD調達購買管理クラウド「newji」は、調達購買部門で必要なQCD管理全てを備えた、現場特化型兼クラウド型の今世紀最高の購買管理システムとなります。
ユーザー登録
調達購買業務の効率化だけでなく、システムを導入することで、コスト削減や製品・資材のステータス可視化のほか、属人化していた購買情報の共有化による内部不正防止や統制にも役立ちます。
NEWJI DX
製造業に特化したデジタルトランスフォーメーション(DX)の実現を目指す請負開発型のコンサルティングサービスです。AI、iPaaS、および先端の技術を駆使して、製造プロセスの効率化、業務効率化、チームワーク強化、コスト削減、品質向上を実現します。このサービスは、製造業の課題を深く理解し、それに対する最適なデジタルソリューションを提供することで、企業が持続的な成長とイノベーションを達成できるようサポートします。
オンライン講座
製造業、主に購買・調達部門にお勤めの方々に向けた情報を配信しております。
新任の方やベテランの方、管理職を対象とした幅広いコンテンツをご用意しております。
お問い合わせ
コストダウンが利益に直結する術だと理解していても、なかなか前に進めることができない状況。そんな時は、newjiのコストダウン自動化機能で大きく利益貢献しよう!
(Β版非公開)