- お役立ち記事
- Manufacturing Process of Electric Lifts and Enhancing Safety
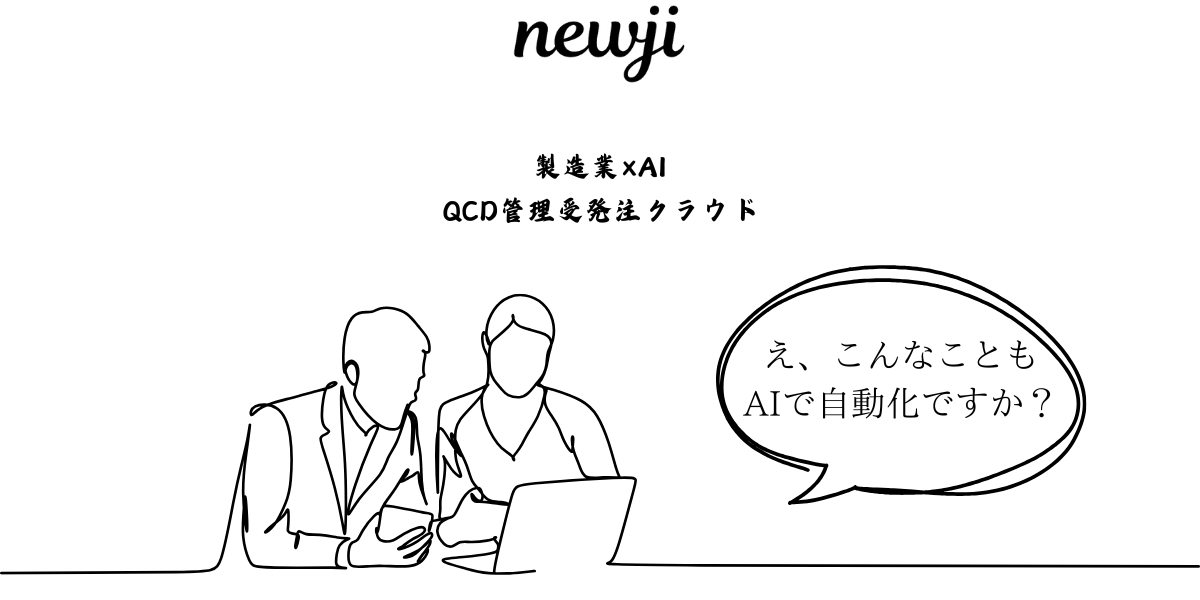
Manufacturing Process of Electric Lifts and Enhancing Safety
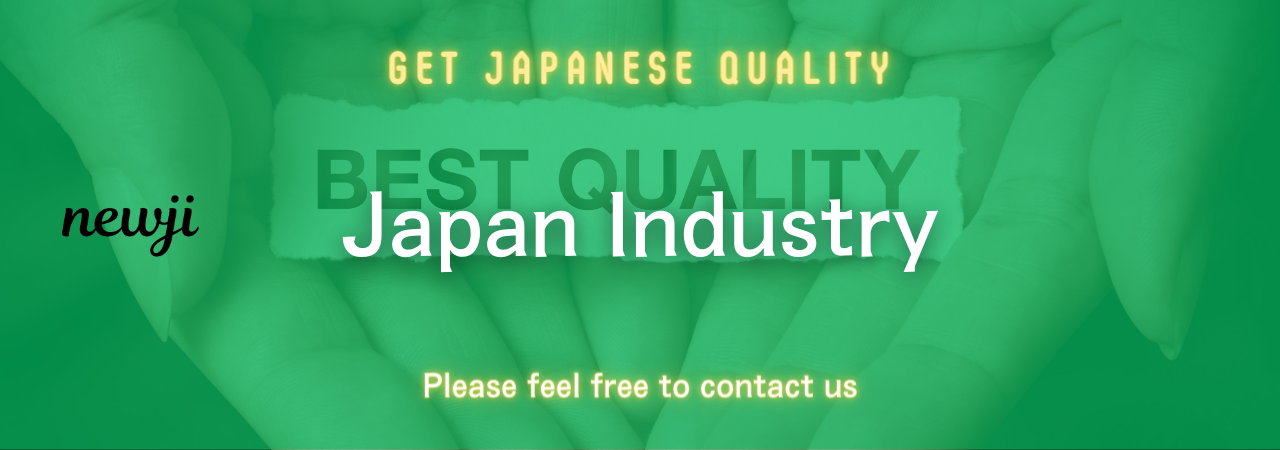
Electric lifts, often referred to as elevators, are essential components in modern buildings, providing ease of movement between floors. Understanding their manufacturing process and ensuring their safety is critical. This comprehensive guide will highlight the step-by-step manufacturing process and the importance of safety measures.
目次
Introduction to Electric Lifts
Electric lifts are complex machines designed to move people and goods vertically within buildings. The primary components include the cabin, hoistway, motor, and control system. Electric lifts can be found in residential buildings, commercial establishments, and industrial settings, showcasing their versatility and efficiency.
Materials and Components
Cabin
The cabin is the enclosed space where passengers or goods are transported. Typically, cabins are made from sturdy materials like stainless steel, aluminium, or reinforced glass to ensure durability and safety.
Hoistway
The hoistway is the vertical shaft in which the elevator moves. It is constructed from reinforced concrete or steel and must be precisely measured and aligned to ensure smooth operation.
Motor and Drive System
The motor is the heart of the electric lift, usually powered by electricity. There are different types of motors, including geared, gearless, and hydraulic motors, each with its own advantages.
Control System
The control system ensures the elevator operates smoothly and safely. It manages the lift’s speed, stops, and door operations. It also includes sensors and switches to monitor and respond to various conditions.
Manufacturing Process of Electric Lifts
Design and Planning
The first step in manufacturing an electric lift is designing the system. Engineers and architects collaborate to create detailed blueprints and specifications based on the building’s requirements. This stage involves selecting materials and components that will meet safety and efficiency standards.
Component Manufacturing
Once the design and planning phase is complete, individual components are manufactured. This process often involves advanced machinery and precise engineering to ensure all parts meet specified tolerances. Key components like motors, cables, and control systems are produced in specialized factories.
Assembly
After manufacturing the components, the next step is assembly.
Technicians carefully assemble each part of the lift according to the design specifications. This involves installing the cabin, motor, drive system, and control units. Every connection and fixture is checked multiple times to guarantee reliability.
Installation in the Building
With the lift assembled, it is transported to the building site for installation. This process includes building the hoistway, securing the lift components, and integrating the control system. Installation must be done by skilled professionals to ensure the safety and efficiency of the lift.
Testing and Commissioning
Before the electric lift can be put into service, it undergoes rigorous testing and commissioning. Engineers and safety inspectors evaluate the operational parameters, ensure compliance with safety regulations, and perform load tests. Any issues identified during this phase are corrected to ensure optimal functionality.
Ensuring Safety
Regulatory Compliance
Electric lifts must adhere to strict safety regulations and standards. These guidelines are established by regulatory authorities and cover aspects such as structural integrity, emergency systems, and electrical safety. Compliance ensures that the lift operates safely under various conditions.
Regular Maintenance
Regular maintenance is essential to keep electric lifts functioning safely and efficiently. Scheduled inspections by certified technicians help identify and address potential issues before they become serious. Maintenance activities include checking the motor, cables, control systems, and safety devices.
Safety Features
Modern electric lifts come equipped with multiple safety features designed to protect passengers and property. These include emergency brakes, alarm systems, intercoms, and fire-resistant materials. Additionally, sensors and automated controls help detect malfunctions and initiate corrective actions.
Emergency Preparedness
Incorporating emergency preparedness plans is crucial for enhancing the safety of electric lifts. This involves training building personnel on the correct procedures during emergencies, installing emergency lighting and communication systems, and conducting regular drills.
Conclusion
Understanding the manufacturing process and the safety measures for electric lifts is vital for ensuring their reliable operation. By adhering to rigorous design, manufacturing, installation, and maintenance standards, manufacturers and building owners can provide safe and efficient vertical transportation.
Regular inspections and updates to safety features also play a significant role in maintaining the integrity of electric lifts. Ensuring safety is a continuous process that requires diligence and adherence to best practices.
With advancements in technology, the future of electric lifts promises even more innovative features and enhanced safety, making them an indispensable part of modern infrastructure.
資料ダウンロード
QCD調達購買管理クラウド「newji」は、調達購買部門で必要なQCD管理全てを備えた、現場特化型兼クラウド型の今世紀最高の購買管理システムとなります。
ユーザー登録
調達購買業務の効率化だけでなく、システムを導入することで、コスト削減や製品・資材のステータス可視化のほか、属人化していた購買情報の共有化による内部不正防止や統制にも役立ちます。
NEWJI DX
製造業に特化したデジタルトランスフォーメーション(DX)の実現を目指す請負開発型のコンサルティングサービスです。AI、iPaaS、および先端の技術を駆使して、製造プロセスの効率化、業務効率化、チームワーク強化、コスト削減、品質向上を実現します。このサービスは、製造業の課題を深く理解し、それに対する最適なデジタルソリューションを提供することで、企業が持続的な成長とイノベーションを達成できるようサポートします。
オンライン講座
製造業、主に購買・調達部門にお勤めの方々に向けた情報を配信しております。
新任の方やベテランの方、管理職を対象とした幅広いコンテンツをご用意しております。
お問い合わせ
コストダウンが利益に直結する術だと理解していても、なかなか前に進めることができない状況。そんな時は、newjiのコストダウン自動化機能で大きく利益貢献しよう!
(Β版非公開)