- お役立ち記事
- Manufacturing Process of Electric Scalers and Improving Vibration Control Technology
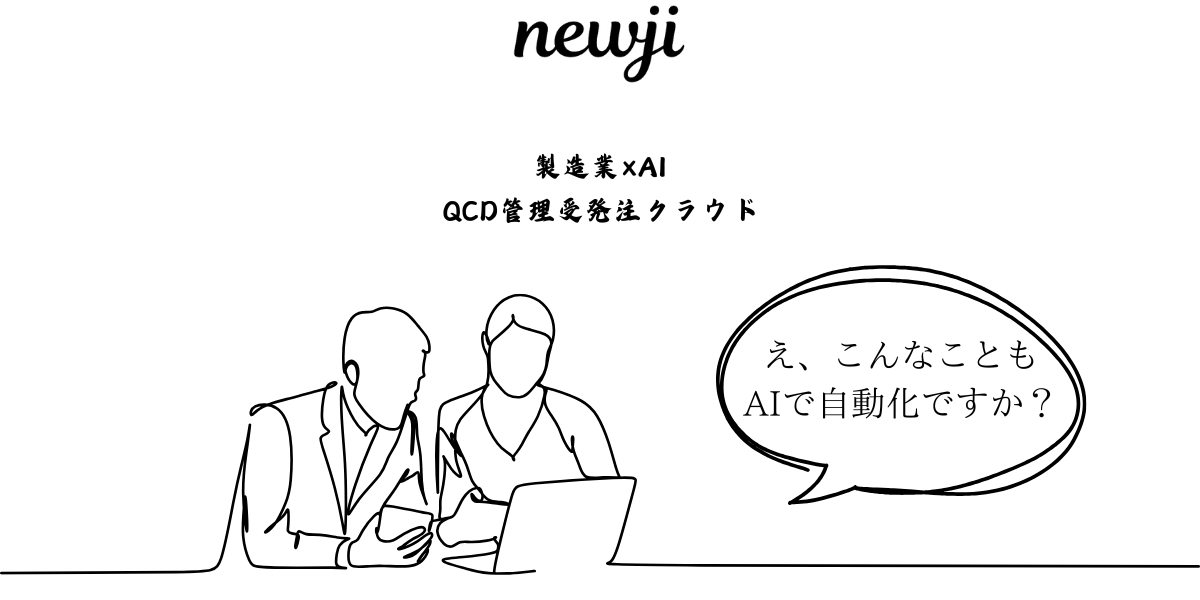
Manufacturing Process of Electric Scalers and Improving Vibration Control Technology
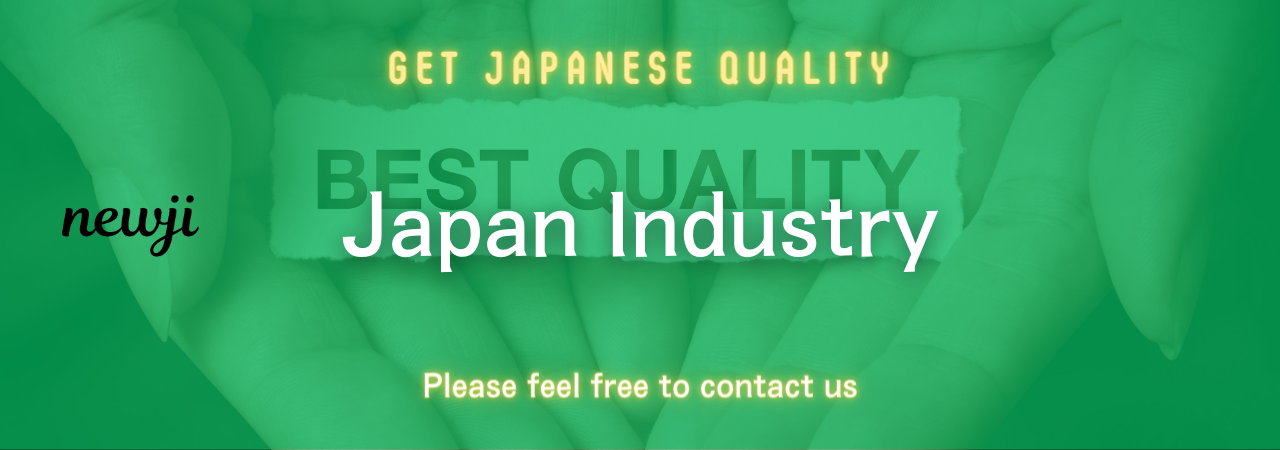
Understanding the intricate workings and sophisticated processes behind the manufacturing of electric scalers can be quite intriguing.
These delicate instruments are widely used in dental hygiene for the removal of tartar and plaque.
Every component is meticulously crafted to ensure the device can perform efficiently and reliably.
Moreover, modern advancements focus on improving vibration control technology to make these tools more comfortable and effective.
Let’s take a closer look at the manufacturing process and the innovations in vibration control.
The Basics of Electric Scalers
Electric scalers are specialized tools designed to aid dental professionals in removing stubborn deposits from teeth, which manual tools might struggle to remove effectively.
These devices operate using a high-frequency vibration mechanism that allows for the efficient cleaning of teeth surfaces.
The primary components of an electric scaler include the handle, the internal power mechanism, the scaling tip, and the adjustable intensity settings.
Components and Materials
In the initial stages of manufacturing, selecting the right materials is crucial.
The handle is often made from lightweight, durable plastic to ensure ease of use and long-lasting performance.
The scaling tip requires a different approach, typically made of high-grade stainless steel to withstand the rigorous demands of dental procedures.
The internal power mechanism, which includes an oscillating motor or piezoelectric crystals, is encased within the handle.
Design and Prototyping
The design phase is critical in determining the overall efficiency and ergonomic efficiency of the scaler.
Modern 3D modeling software allows engineers to design every aspect of the scaler, from the shape and size to the internal components and how they will fit together.
Prototyping follows, during which a physical model is created based on the digital design.
This phase is essential for testing and refining the device.
Assembly and Quality Control
The assembly stage is where all individual components come together.
Precision Manufacturing
Each part of the electric scaler is manufactured with precision.
Automated machines and robotics are often used to ensure each component is crafted to exact specifications.
The manufacturing process involves creating the housing of the scaler and fitting the internal mechanisms, like the motor and battery.
The scaling tip is then attached, followed by thorough testing to ensure it meets the required performance standards.
Quality Assurance
Quality control is a critical step in ensuring that each scaler performs reliably.
Every device undergoes rigorous testing that includes checking the vibration frequency, battery life, and overall performance.
Scalers that fail to meet these benchmarks are rejected or sent back for rework.
Additionally, stress tests are conducted to simulate real-world usage and ensure durability under various conditions.
Improving Vibration Control Technology
A significant area of focus in recent years has been improving vibration control technology to reduce discomfort for both dental professionals and patients.
Enhanced vibration control not only makes the scaler more effective but also minimizes hand fatigue for the user, leading to better precision during dental procedures.
Piezoelectric Technology
One of the most noteworthy advancements is the use of piezoelectric technology.
This technology utilizes piezo crystals that expand and contract with electric current to generate precise, high-frequency vibrations.
Unlike traditional motor-driven scalers, piezoelectric scalers offer a higher degree of accuracy and smoother operation.
This leads to a more comfortable experience for patients and less strain for the operator.
Active Vibration Control
Active vibration control systems have also been introduced to dampen unwanted vibrations.
These systems actively counteract vibrations by adjusting the frequency and amplitude to maintain a steady, controlled motion.
This not only improves the comfort level but also enhances the overall efficiency of the scaling process.
Ergonomic Improvements
Advanced materials and designs have made modern electric scalers significantly more ergonomic.
Lightweight and well-balanced handles allow for better control and reduced fatigue during long procedures.
Materials such as advanced polymers and composites provide necessary strength while keeping the device light.
Future Trends in Electric Scaler Technology
As technology continues to evolve, so too will electric scalers and their capabilities.
Integration with Digital Health
Future scalers may integrate with digital health records, collecting and transmitting data to enhance patient care.
These devices could provide real-time feedback and diagnostic information, offering unprecedented precision and aid in dental hygiene.
Enhanced AI Capabilities
Artificial intelligence continues to make significant strides and may soon play a role in enhancing the functionality of electric scalers.
AI could potentially adapt the vibration settings based on real-time data, specifications of the patient’s dental condition, and user preferences, providing a highly personalized experience.
Eco-Friendly Innovations
Sustainability is another area where advancements can be expected.
Future designs may focus on the development of scalers made from biodegradable or recyclable materials.
Energy efficiency improvements and longer-lasting components will also contribute to more environmentally friendly dental tools.
To summarize, the manufacturing process of electric scalers is a meticulous operation requiring precision and quality control at every level.
Recent innovations, particularly in vibration control technology, have significantly enhanced the effectiveness and user comfort of these devices.
With emerging technologies and continuous improvements, the future of electric scalers looks promising, offering advanced features that further aid dental professionals and enhance patient care.
資料ダウンロード
QCD調達購買管理クラウド「newji」は、調達購買部門で必要なQCD管理全てを備えた、現場特化型兼クラウド型の今世紀最高の購買管理システムとなります。
ユーザー登録
調達購買業務の効率化だけでなく、システムを導入することで、コスト削減や製品・資材のステータス可視化のほか、属人化していた購買情報の共有化による内部不正防止や統制にも役立ちます。
NEWJI DX
製造業に特化したデジタルトランスフォーメーション(DX)の実現を目指す請負開発型のコンサルティングサービスです。AI、iPaaS、および先端の技術を駆使して、製造プロセスの効率化、業務効率化、チームワーク強化、コスト削減、品質向上を実現します。このサービスは、製造業の課題を深く理解し、それに対する最適なデジタルソリューションを提供することで、企業が持続的な成長とイノベーションを達成できるようサポートします。
オンライン講座
製造業、主に購買・調達部門にお勤めの方々に向けた情報を配信しております。
新任の方やベテランの方、管理職を対象とした幅広いコンテンツをご用意しております。
お問い合わせ
コストダウンが利益に直結する術だと理解していても、なかなか前に進めることができない状況。そんな時は、newjiのコストダウン自動化機能で大きく利益貢献しよう!
(Β版非公開)