- お役立ち記事
- Manufacturing Process of Electric Scissors and Blade Rotational Speed Adjustment Technology
Manufacturing Process of Electric Scissors and Blade Rotational Speed Adjustment Technology
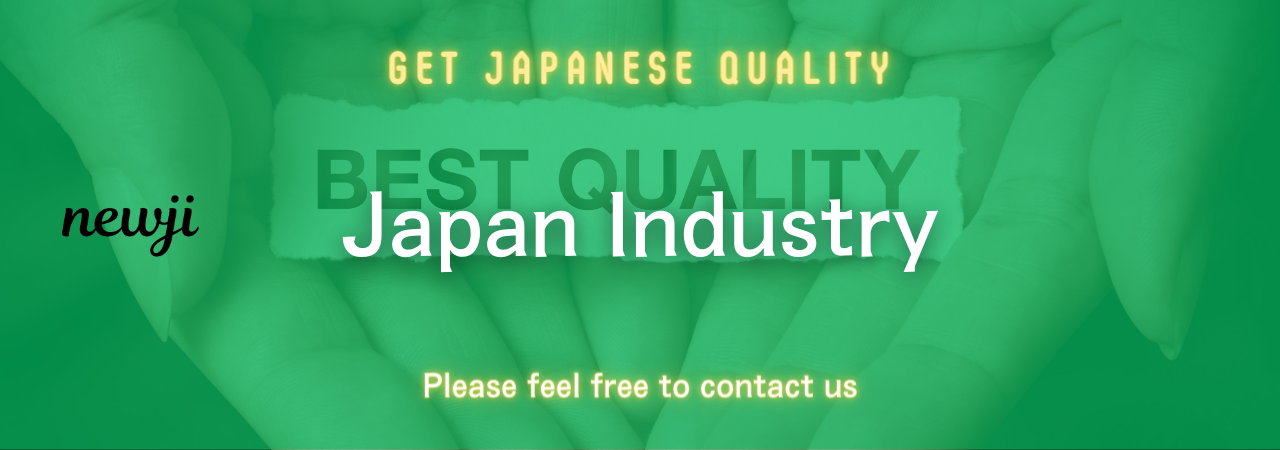
Electric scissors are an essential tool in various industries, from crafting to professional tailoring. This article explores the manufacturing process of electric scissors and the technology behind adjusting blade rotational speed. By understanding how these tools are made and how they function, we can appreciate their complexity and the innovation that goes into their development.
目次
Materials and Components
The manufacturing process starts with selecting the right materials. Electric scissors consist of several key components: blades, motor, housing, and electronic circuitry. The blades are typically made of high-carbon steel or stainless steel, which ensures durability and sharpness.
The housing, often crafted from durable plastic or alloy, protects the internal components and provides a comfortable grip. The motor, usually a small, efficient electric motor, powers the cutting mechanism. Finally, the electronic circuitry controls the motor and other functionalities like speed adjustment.
Blade Manufacturing
Blades are the heart of electric scissors. The manufacturing process involves several steps to ensure they are sharp and durable. It begins with selecting high-quality steel, which is then cut into the desired blade shape using precision tools.
Once the blades are cut, they undergo heat treatment to improve hardness and durability. After heat treatment, the blades are ground and sharpened to achieve the required sharpness. This process involves using grinding wheels and honing stones to achieve a razor-sharp edge.
Motor Assembly
The motor is another crucial component of electric scissors. The manufacturing process involves winding copper wire around a core to create electromagnets. This process is called coil winding. The wound coils are then assembled into the motor housing, along with a rotor and stator.
The rotor, which is the rotating part of the motor, interacts with the stator, the stationary part, to create rotational motion. This motion is transmitted to the blades, causing them to cut through materials.
Electronic Circuitry
Electronic circuitry is essential for controlling the functions of electric scissors. This includes the power supply, speed control, and safety features. The manufacturing process of electronic circuitry involves designing a circuit board with the necessary components like resistors, capacitors, and transistors.
Once the circuit design is finalized, the components are soldered onto the circuit board. Quality control tests ensure that the electronic circuitry functions correctly before it is assembled with the other components.
Assembling the Electric Scissors
With all the components ready, the final assembly process begins. This involves fitting the motor and electronic circuitry into the housing. The blades are attached to the motor’s output shaft, ensuring they are aligned correctly.
Screws and fasteners secure all components in place. Once assembled, the electric scissors undergo testing to ensure they are functioning correctly. This includes checking the blade’s sharpness, motor’s power, and electronic circuitry’s responsiveness.
Blade Rotational Speed Adjustment Technology
An important feature of modern electric scissors is the ability to adjust the blade’s rotational speed. This allows the user to control the cutting speed based on the material being cut. The technology behind this feature involves using electronic speed controllers (ESC).
Understanding Electronic Speed Controllers (ESC)
Electronic speed controllers are devices that regulate the speed of an electric motor. They work by varying the voltage and current supplied to the motor. In electric scissors, the ESC interprets signals from the user, typically through a speed adjustment dial or switch, and adjusts the motor’s speed accordingly.
Closed-Loop Control Systems
Advanced electric scissors use closed-loop control systems for precise speed adjustment. A closed-loop control system includes a feedback mechanism that monitors the motor’s speed and adjusts it in real-time.
When the user selects a speed setting, the controller sets the motor to that speed. Sensors monitor the actual speed and send data back to the controller. If there is any discrepancy between the desired speed and the actual speed, the controller makes adjustments to correct it.
Pulse Width Modulation (PWM)
Pulse Width Modulation (PWM) is a common technique used in speed controllers for electric motors. PWM involves switching the motor’s power supply on and off at high frequencies.
By varying the width of the on-time pulses, the average power supplied to the motor is controlled, thereby adjusting its speed. This method is efficient and provides fine control over the motor’s speed, which is crucial for the precise operation of electric scissors.
Quality Control and Testing
Quality control is a vital part of the manufacturing process. Each pair of electric scissors undergoes rigorous testing to ensure it meets the required standards. This includes testing the sharpness of the blades, the power and efficiency of the motor, and the functionality of the electronic circuitry, including the speed adjustment feature.
The testing process involves cutting various materials to ensure the scissors perform well under different conditions. Any defects or issues identified during testing are rectified before the product is shipped to the market.
Conclusion
The manufacturing process of electric scissors combines precision engineering with advanced technology. From selecting high-quality materials to employing sophisticated blade rotational speed adjustment technology, each step is crucial in producing a reliable and efficient tool.
Understanding the intricacies of this process not only highlights the innovation involved but also helps users appreciate the craftsmanship behind their everyday tools. Whether for professional use or personal projects, electric scissors are a testament to the advances in modern manufacturing and electronic control systems.
資料ダウンロード
QCD調達購買管理クラウド「newji」は、調達購買部門で必要なQCD管理全てを備えた、現場特化型兼クラウド型の今世紀最高の購買管理システムとなります。
ユーザー登録
調達購買業務の効率化だけでなく、システムを導入することで、コスト削減や製品・資材のステータス可視化のほか、属人化していた購買情報の共有化による内部不正防止や統制にも役立ちます。
NEWJI DX
製造業に特化したデジタルトランスフォーメーション(DX)の実現を目指す請負開発型のコンサルティングサービスです。AI、iPaaS、および先端の技術を駆使して、製造プロセスの効率化、業務効率化、チームワーク強化、コスト削減、品質向上を実現します。このサービスは、製造業の課題を深く理解し、それに対する最適なデジタルソリューションを提供することで、企業が持続的な成長とイノベーションを達成できるようサポートします。
オンライン講座
製造業、主に購買・調達部門にお勤めの方々に向けた情報を配信しております。
新任の方やベテランの方、管理職を対象とした幅広いコンテンツをご用意しております。
お問い合わせ
コストダウンが利益に直結する術だと理解していても、なかなか前に進めることができない状況。そんな時は、newjiのコストダウン自動化機能で大きく利益貢献しよう!
(Β版非公開)