- お役立ち記事
- Manufacturing Process of Electric Scissors and Blade Sharpness Adjustment Technology
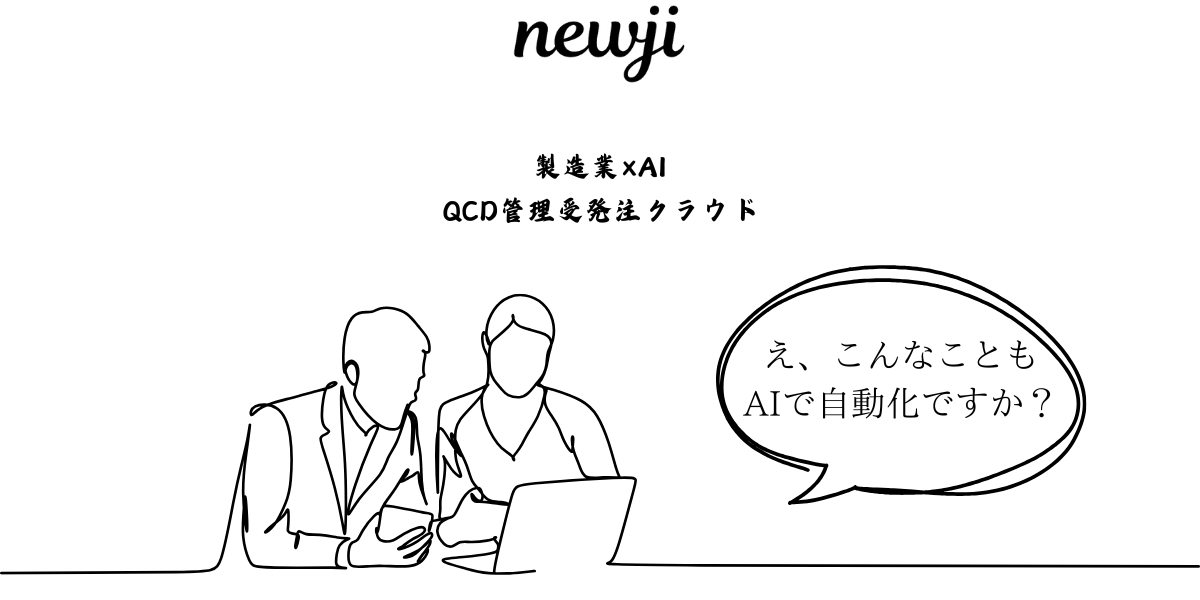
Manufacturing Process of Electric Scissors and Blade Sharpness Adjustment Technology
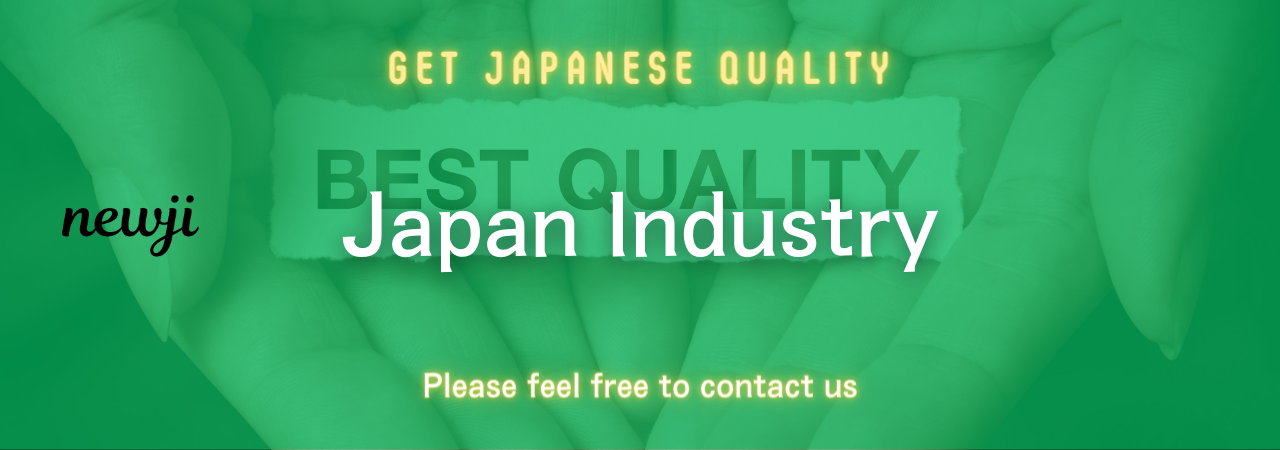
Electric scissors have revolutionized the way we cut materials, from fabric to paper and beyond. These handy tools offer precision, speed, and ease of use, making them invaluable in both domestic and industrial settings. But how are these modern marvels made? And what technology ensures their blade sharpness remains optimal? Let’s dive into the manufacturing process of electric scissors and explore the blade sharpness adjustment technology.
目次
Understanding the Basic Components of Electric Scissors
Before delving into the manufacturing process, it’s crucial to understand the primary components of electric scissors. These components work together to deliver the desired cutting performance.
Motor
The motor is the heart of electric scissors. It powers the blades, enabling them to move swiftly and efficiently. Typically, an electric motor converts electrical energy into mechanical energy, driving the blades’ movement.
Blades
Blades are the cutting components of electric scissors. They are usually made of high-quality stainless steel to ensure durability and resistance to corrosion. The sharpness and alignment of the blades are critical for optimal performance.
Battery
Many electric scissors are cordless and rely on rechargeable batteries. The battery life and charging time can vary depending on the model, but most offer a convenient and extended cutting experience.
Housing
The housing encloses all components, protecting them from external damage. It also provides a comfortable grip for users, ensuring ease of handling.
Manufacturing Process of Electric Scissors
The manufacturing process of electric scissors involves several steps, each crucial to the final product’s quality and performance. Let’s explore these steps in detail.
Design and Prototyping
The first step in manufacturing electric scissors is designing the product. Engineers create detailed blueprints and 3D models to visualize the final product. Prototyping follows the design phase, allowing engineers to test the product’s functionality and make necessary adjustments.
Material Selection
Once the design is finalized, the next step is selecting appropriate materials. High-quality stainless steel is typically chosen for the blades due to its strength and corrosion resistance. The housing is often made from durable plastic or metal to ensure longevity.
Blade Forging and Sharpening
The blades are forged from stainless steel sheets. They are then heat-treated to enhance their hardness and durability. After forging, the blades undergo a precise sharpening process to achieve the desired cutting edge. Advanced machines and skilled technicians ensure the blades are sharpened to perfection.
Motor Assembly
The motor is a crucial component that requires meticulous assembly. It involves winding the coils, assembling the rotor and stator, and integrating the motor with the other components. The motor is then tested to ensure it meets performance standards.
Battery Integration
The battery is another vital component that needs careful integration. It is connected to the motor and other electrical components, ensuring smooth power delivery. The battery is also tested for performance, safety, and longevity.
Final Assembly
In the final assembly stage, all components are brought together. The blades, motor, battery, and housing are assembled according to the design specifications. Quality control checks are performed at each stage to ensure the product meets the highest standards.
Testing and Quality Control
Before the electric scissors are released to the market, they undergo rigorous testing. This includes performance tests, safety checks, and durability assessments. Only products that pass all tests and quality control checks are approved for sale.
Blade Sharpness Adjustment Technology
Maintaining blade sharpness is crucial for the optimal performance of electric scissors. Various technologies ensure that the blades remain sharp and effective throughout their lifespan.
Automatic Sharpening Systems
Some advanced models of electric scissors come equipped with automatic sharpening systems. These systems use built-in mechanisms to sharpen the blades after a certain period or usage threshold. This ensures that the blades remain sharp without requiring manual intervention.
Adjustable Blade Tension
Adjustable blade tension is another innovative feature that helps maintain sharpness. Users can adjust the tension of the blades to ensure they are cutting at the optimal angle. This feature is particularly useful for cutting through different materials, requiring different levels of sharpness and pressure.
Interchangeable Blades
Some electric scissors are designed with interchangeable blades. Users can replace the blades once they become dull, ensuring continuous sharpness and performance. This feature extends the product’s lifespan and makes maintenance easier.
Sharpening Tools and Accessories
Manufacturers often provide specialized sharpening tools and accessories. These tools are designed to maintain the blades’ sharpness through regular maintenance. Users can easily sharpen the blades themselves, ensuring the scissors remain effective.
Conclusion
The manufacturing process of electric scissors is a complex and meticulous one, involving several steps to ensure high-quality and reliable products. From design and prototyping to final assembly and quality control, each stage is crucial to the overall performance and longevity of the product.
Equally important is the blade sharpness adjustment technology that ensures the scissors remain effective throughout their lifespan. With innovative features like automatic sharpening systems, adjustable blade tension, interchangeable blades, and specialized sharpening tools, manufacturers are providing users with reliable and efficient cutting solutions.
Electric scissors are an essential tool for various applications, offering precision, speed, and ease of use. Understanding their manufacturing process and the technology behind blade sharpness adjustment can help users appreciate the value and utility these modern tools bring.
資料ダウンロード
QCD調達購買管理クラウド「newji」は、調達購買部門で必要なQCD管理全てを備えた、現場特化型兼クラウド型の今世紀最高の購買管理システムとなります。
ユーザー登録
調達購買業務の効率化だけでなく、システムを導入することで、コスト削減や製品・資材のステータス可視化のほか、属人化していた購買情報の共有化による内部不正防止や統制にも役立ちます。
NEWJI DX
製造業に特化したデジタルトランスフォーメーション(DX)の実現を目指す請負開発型のコンサルティングサービスです。AI、iPaaS、および先端の技術を駆使して、製造プロセスの効率化、業務効率化、チームワーク強化、コスト削減、品質向上を実現します。このサービスは、製造業の課題を深く理解し、それに対する最適なデジタルソリューションを提供することで、企業が持続的な成長とイノベーションを達成できるようサポートします。
オンライン講座
製造業、主に購買・調達部門にお勤めの方々に向けた情報を配信しております。
新任の方やベテランの方、管理職を対象とした幅広いコンテンツをご用意しております。
お問い合わせ
コストダウンが利益に直結する術だと理解していても、なかなか前に進めることができない状況。そんな時は、newjiのコストダウン自動化機能で大きく利益貢献しよう!
(Β版非公開)