- お役立ち記事
- Manufacturing Process of Electric Screwdrivers and Enhancing Torque Adjustment Functionality
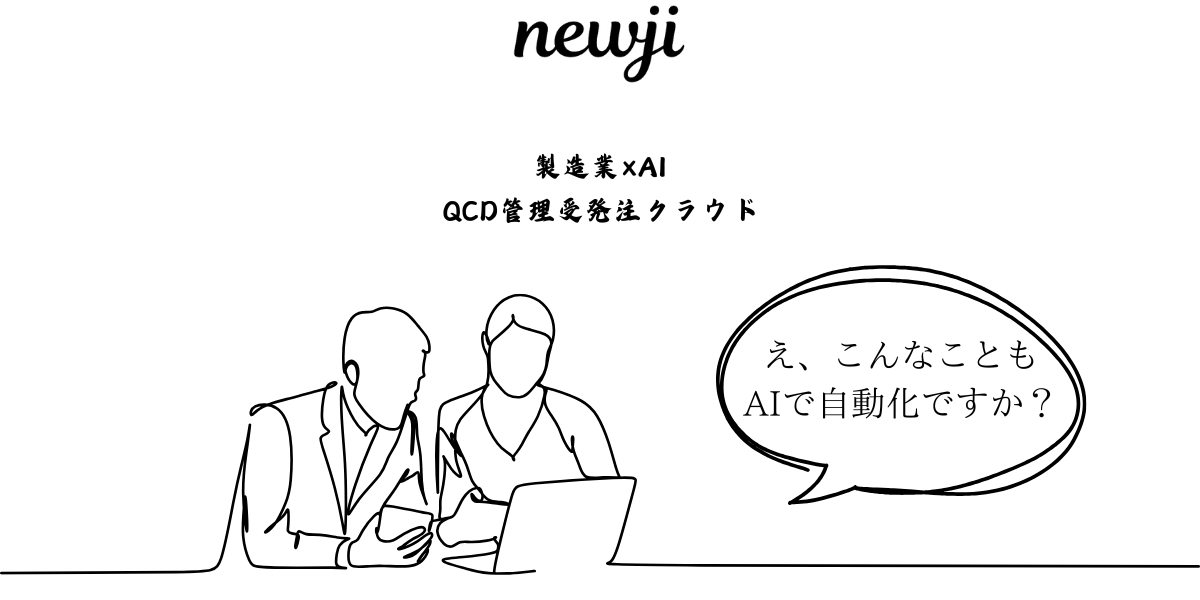
Manufacturing Process of Electric Screwdrivers and Enhancing Torque Adjustment Functionality
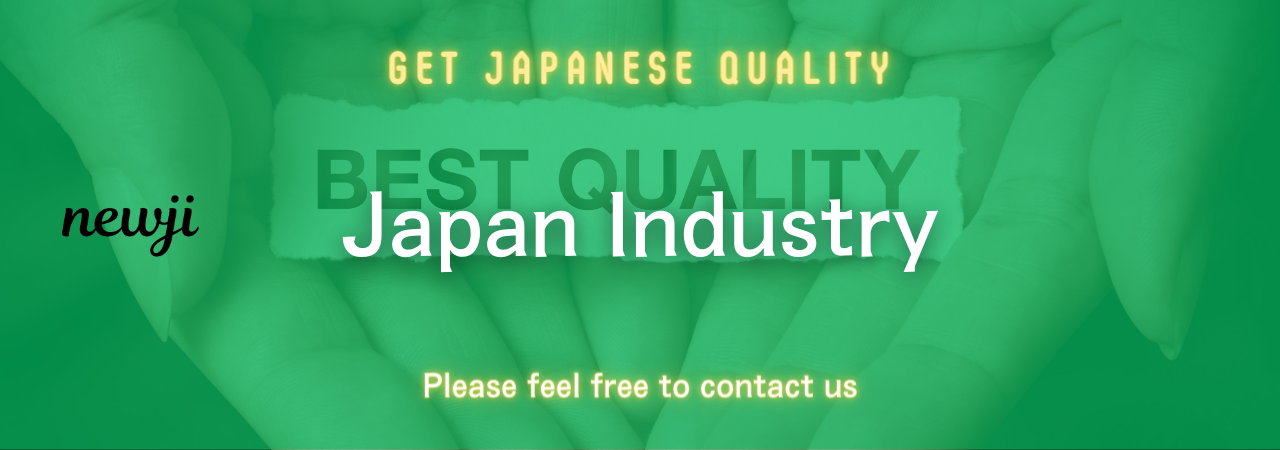
Electric screwdrivers are indispensable tools in various industries and household tasks.
Their ease of use and efficiency make them a preferred choice for many.
This article delves into the manufacturing process of electric screwdrivers and explores how torque adjustment functionality is enhanced.
目次
Materials and Initial Design
The manufacturing process of electric screwdrivers begins with selecting the appropriate materials.
High-quality metals like stainless steel and durable plastics form the core components.
The initial design phase is crucial as it lays the foundation for the tool’s efficiency and durability.
Metals and Plastics
Stainless steel is often used for the screwdriver bit due to its strength and resistance to wear.
For the casing, manufacturers opt for high-impact plastic, which combines light weight with durability.
Other components like springs and gears are typically made from steel, ensuring longevity and reliability.
Design Prototyping
Once materials are chosen, the design team creates prototypes using computer-aided design (CAD) software.
Prototyping allows manufacturers to identify potential issues with the design and make necessary adjustments.
This step ensures that the final product is both functional and user-friendly.
Manufacturing Components
The next phase involves the actual production of the individual components.
Each part of the electric screwdriver, from the motor to the casing, undergoes a rigorous manufacturing process.
Motor Production
The electric motor is the heart of the screwdriver.
Manufacturing begins with winding copper wires around a metal core to create the electromagnet.
This is followed by assembling the motor components, which include the commutator, brushes, and bearings.
Quality control measures ensure that each motor meets performance standards.
Screwdriver Bit Fabrication
The screwdriver bit is forged from stainless steel.
This process involves heating the metal to a high temperature and then molding it into the desired shape.
The bits are then heat-treated to enhance their hardness, followed by coating them to prevent corrosion.
Casing and Handle
The handle and casing are typically injection-molded from high-impact plastic.
A mold shaped like the intended design is filled with molten plastic, which is then allowed to cool and harden.
Once solidified, the casings are trimmed and polished to remove any imperfections.
Assembly Process
Upon completion of the separate components, the assembly phase begins.
The motor, gearbox, electronic circuit boards, and external casings are brought together to form the final product.
Integrating Motor and Gearbox
The motor is installed into the gearbox, which translates the motor’s rotational power into the appropriate torque required for driving screws.
Precision alignment is crucial at this stage to ensure the tool operates smoothly and efficiently.
Sealed bearings are often used to reduce friction and increase the lifespan of the device.
Installing Electronic Components
Modern electric screwdrivers come equipped with various electronic features, such as adjustable speed and torque control.
Circuit boards and wiring harnesses are carefully positioned within the casing.
Safety features, including overload protection and thermal cutoffs, are also incorporated during this stage.
Final Assembly
The screwdriver bit, motor-gearbox assembly, and electronic controls are housed within the plastic casing.
Screws and clips secure the components, ensuring they remain fixed during use.
Rubber grips are often added to the handle to enhance comfort and control.
Improving Torque Adjustment Functionality
Torque adjustment is a critical feature in electric screwdrivers as it allows for precision and prevents damage to materials and fasteners.
Enhancing this functionality involves several key considerations and technologies.
Innovative Clutch Systems
One common method to enhance torque adjustment is through the use of advanced clutch systems.
A mechanical clutch disengages the drive when the preset torque level is reached.
This mechanism ensures consistent and accurate torque levels, preventing over-tightening.
Electronic Controls
Integration of electronic controls has revolutionized torque adjustment.
Microprocessors within the screwdriver monitor the torque and adjust the power supply accordingly.
This allows for more precise control and adaptability across different tasks.
Some models even feature digital displays for easy monitoring and adjustment.
Torque Calibration and Testing
Before leaving the factory, electric screwdrivers undergo rigorous torque calibration and testing.
This ensures that the torque settings are accurate and reliable.
Automatic calibration systems have been developed to standardize this process, reducing human error and increasing consistency.
Quality Assurance and Final Inspection
The final stage in the manufacturing process is quality assurance and inspection.
Each electric screwdriver is tested to ensure it meets performance and safety standards.
Performance Testing
Tests simulate real-world usage scenarios to verify the tool’s functionality.
This includes running the motor at various speeds, checking the torque settings, and ensuring that all electronic components operate correctly.
Any failure to meet the required standards results in the product being sent back for rework or adjustments.
Safety Inspection
Safety is paramount in power tools.
Each unit undergoes thorough safety inspections, checking for electrical integrity, insulation, and mechanical durability.
Certifications from regulatory bodies are often required, ensuring the tool is safe for consumer use.
Packaging and Distribution
After passing all tests, the electric screwdrivers are cleaned, polished, and packaged.
Packaging protects the tool during transit and provides critical information to the consumer.
Distribution networks then deliver the final product to retailers and end-users.
Understanding the intricate steps involved in manufacturing electric screwdrivers and improving their torque adjustment capabilities highlights the balance of engineering and innovation.
These steps ensure that the final product is efficient, reliable, and user-friendly, upholding the high standards expected by consumers.
資料ダウンロード
QCD調達購買管理クラウド「newji」は、調達購買部門で必要なQCD管理全てを備えた、現場特化型兼クラウド型の今世紀最高の購買管理システムとなります。
ユーザー登録
調達購買業務の効率化だけでなく、システムを導入することで、コスト削減や製品・資材のステータス可視化のほか、属人化していた購買情報の共有化による内部不正防止や統制にも役立ちます。
NEWJI DX
製造業に特化したデジタルトランスフォーメーション(DX)の実現を目指す請負開発型のコンサルティングサービスです。AI、iPaaS、および先端の技術を駆使して、製造プロセスの効率化、業務効率化、チームワーク強化、コスト削減、品質向上を実現します。このサービスは、製造業の課題を深く理解し、それに対する最適なデジタルソリューションを提供することで、企業が持続的な成長とイノベーションを達成できるようサポートします。
オンライン講座
製造業、主に購買・調達部門にお勤めの方々に向けた情報を配信しております。
新任の方やベテランの方、管理職を対象とした幅広いコンテンツをご用意しております。
お問い合わせ
コストダウンが利益に直結する術だと理解していても、なかなか前に進めることができない状況。そんな時は、newjiのコストダウン自動化機能で大きく利益貢献しよう!
(Β版非公開)